Редакторът ще организира много практически методи за знания и горещи новини за всеки, всеки трябва да обърне повече внимание и ще ви бъде представено по-добро съдържание.
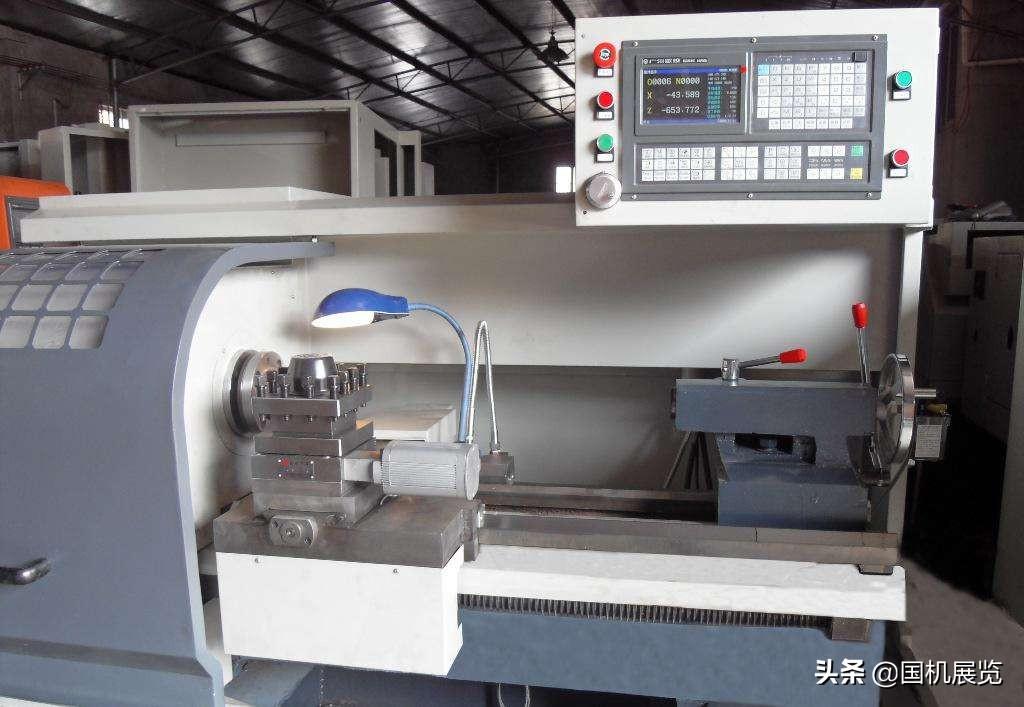
На струг с ЦПУ могат да се завъртят четири стандартни резби: метрично, инчово, модулно и радиално управление Независимо от вида на резбата, струговият шпиндел и инструментът трябва да поддържат строга връзка на движение: т.е. при всяко завъртане на шпиндела (т.е. при всяко завъртане на детайла), инструментът трябва да се движи равномерно разстояние на оловото на детайла. Чрез анализа на обикновените нишки, ние се стремим да подобрим разбирането си за обикновените нишки, за да ги обработим по-добре.
1,Размерен анализ на обикновените нишки
Стругът с ЦПУ изисква серия от размери за обработка на обикновени резби, а изчисляването и анализа на размерите, необходими за обработка на обикновени резби, включват главно следните два аспекта:
1. Диаметър на детайла преди обработка на резба
Като се има предвид разширяването на профила на резбата по време на обработката на резбата, диаметърът на детайла преди обработката на резбата е Обикновено, въз основа на малкия деформационен капацитет на материала, той се приема за 0,1 до 0,5 по-малък от основния диаметър на резбата.
2. Количество на подаването за обработка на резба
Количеството подаване на резбата може да се отнася до долния диаметър на резбата, който е крайната позиция на подаване на резеца.
Минималният диаметър на резбата е: основен диаметър -2 пъти височината на зъба; Височина на зъбите=0,54p (p е наклон)
Количеството подаване за обработка на резби трябва непрекъснато да се намалява и специфичното количество подаване трябва да бъде избрано въз основа на инструмента и работния материал.
2,Монтаж и подравняване на обикновени инструменти за рязане на резби
Ако инсталирането на инструмента за струговане е твърде високо или твърде ниско, когато инструментът за рязане достигне определена дълбочина, задната повърхност на рязане на инструмента за струговане притиска срещу детайла, увеличава триенето и дори огъва детайла, причинявайки явлението на ухапване на инструмента; Ако е твърде ниско, чиповете не се разреждат лесно, а радиалната сила на инструмента за струговане е към центъра на детайла. Освен това, разстоянието между хоризонталния винт и гайката е твърде голямо, което причинява автоматично задълбочаване на дълбочината на рязане, като по този начин повдига детайла и причинява рязане. В този момент височината на инструмента за струговане трябва да се регулира своевременно, за да се гарантира, че върхът му е на същата височина като оста на детайла (като се използва върха на задната част за подравняване на инструмента). По време на грубо и полупрецизно струговане позицията на върха на инструмента е около 1% по-висока от центъра на детайла (представлява диаметъра на обработвания детайл).
Детайлът не може да бъде здраво затегнат, а твърдостта на самия детайл не може да издържи на силата на рязане по време на струговане, което води до прекомерно отклонение и промяна на централната височина между инструмента за струговане и детайла (детайлът е повдигнат), което води до внезапно увеличаване на дълбочината на рязане и гризане на инструмента.По това време детайлът трябва да бъде здраво затегнат, а накрайниците на задните части могат да се използват за увеличаване на твърдостта на детайла.
Методите за подравняване на инструмента за обикновени резби включват метод за пробно рязане и инструмент за автоматично подравняване на инструмента, Инструментът може да се използва директно за пробно рязане, или нулевата точка на детайла може да бъде зададена с движение на детайла за подравняване на инструмента. Изискванията за подравняване на инструмента при обработка на резби не са много високи, особено няма строги ограничения за подравняване на инструмента в посока което може да се определи според изискванията за програмиране на машинната обработка.
3,Програмиране и обработка на обикновени резби
В сегашните стругове с ЦПУ обикновено има три метода на обработка за рязане на резба: метод на право рязане Поради различните методи на рязане и методи на програмиране, грешките в машинната обработка също варират. Трябва внимателно да анализираме работата и употребата и да се стремим да обработваме висококачествени детайли.
1. Методът на направо рязане поради едновременната работа на двата режещи ръба има висока сила на рязане и е труден за рязане, поради което по време на рязане и двата режещи ръба са склонни към износване. При рязане на резби с по-големи наклони, поради по-голямата дълбочина на рязане, износването на острието е по-бързо, което води до грешки в диаметъра на наклона на резбата; Въпреки това, точността на обработената форма на зъба е сравнително висока, така че обикновено се използва за обработка на малки нишки. Поради факта, че движението и рязането на инструмента са завършени чрез програмиране, машинната програма е сравнително дълга; Поради лесното износване на режещия ръб е необходимо често измерване по време на обработката.
2.Методът на направо рязане опростява програмирането и подобрява ефективността в сравнение с инструкцията.
3.Методът на наклонено рязане поради своята обработка с единичен ръб е склонен към повреда и износване на режещия ръб, което води до неравна резбована повърхност и промени в ъгъла на върха на инструмента, което води до лоша точност на формата на зъба. Въпреки това, поради работата си с един ръб, натоварването на инструмента е малко, отстраняването на чипове е лесно и дълбочината на рязане намалява. Ето защо този метод на обработка обикновено е подходящ за обработка на големи нишки. Благодарение на лесното отстраняване на чиповете и добрите условия на рязане, този метод на обработка е по-удобен, когато изискванията за точност на резбата не са високи. При обработката на високопрецизни резби може да се използва обработка на два инструмента, което включва грубо струговане, използвайки първо метода на обработка и след това прецизно струговане, използвайки метода на обработка. Но е важно да се гарантира, че началната точка на инструмента е точна, в противен случай е лесно да се закопчае случайно и да доведе до скрап на части.
4. След завършване на обработката на резбата качеството на резбата може да бъде оценено и мерките могат да бъдат взети своевременно, като се наблюдава профила на резбата. Когато горната част на резбата не е насочена, увеличаването на размера на рязане на инструмента действително ще увеличи основния диаметър на резбата, което зависи от пластичността на материала.
4,Изпитване на обикновени нишки
За общи стандартни резби за измерване се използват габарити за резба или щепсели. При измерване на външни нишки, ако резбата е" Over End; Габаретът на пръстена е прецизно завинтен, докато & квота; Краен стоп; Ако пръстеномерът не може да се завърти, това показва, че обработената резба отговаря на изискванията, в противен случай тя е неквалифицирана. Когато измервате вътрешни резби, използвайте габарит на щепсела на резбата и използвайте същия метод за измерване. За измерване могат да се използват и други измервателни инструменти. Диаметърът на резбата може да се измерва с микрометър на резбата, а дебелината на зъба може да се измерва с верниер за дебелина на зъба за диаметър на трапецовидната резба и диаметър на стъпката на червея. За измерване на диаметъра на резбата може да се използва измервателна игла с помощта на метода за измерване на трите игли.
15-тото международно изложение на машинни инструменти в Китай (ще се проведе от 18 до 22 май 2020 г. в новата сграда на Международния изложбен център в Китай (Ние ви приветстваме да дойдете и да ни напътствате.