За един миг работя със струг с ЦПУ в продължение на десет години и натрупах някои умения за обработка и опит в струговете с ЦПУ и бих искал да обменя идеи с колегите си. Благодарение на честата подмяна на обработени части и ограничените фабрични условия ние програмираме, проверяваме инструментите, отстраняваме грешки и завършваме машинната обработка на частите сами през последното десетилетие.В обобщение нашите оперативни умения могат да бъдат разделени на следните точки. (Автор/Ли Ненг)
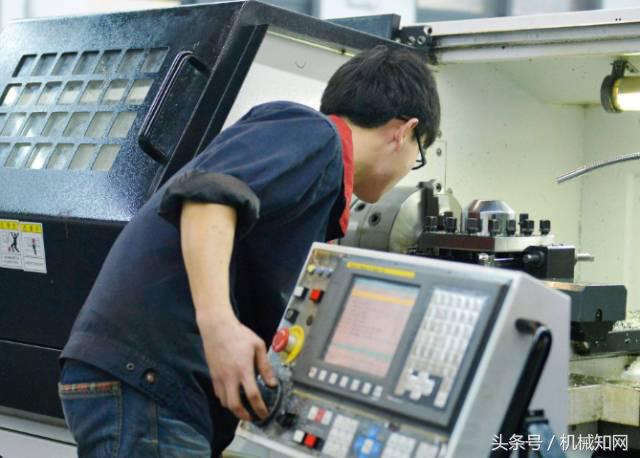
1, Умения за програмиране: Поради високите изисквания за прецизност на нашата фабрика за преработени продукти, следните фактори трябва да бъдат взети предвид при програмирането:
1. Последователност на обработка на частите:
Първо пробийте и след това сплеснете края (това е за да предотвратите свиване на материала по време на пробиване);
Първо груба кола, след това фина кола (това е, за да се гарантира точността на частите);
Първо обработете тези с по-големи отклонения, а след това обработете тези с по-малки отклонения (това гарантира, че повърхността на малкия размер на отклонението не е надраскана и предотвратява деформация на частите).
2.Изберете разумна скорост, скорост на подаване и дълбочина на рязане въз основа на твърдостта на материала:
1) Изберете материали от въглеродна стомана с висока скорост, висока скорост на подаване и голяма дълбочина на рязане. Например: 1изберете и дълбочина на рязане 2 мм;
2) Изберете ниска скорост, ниска скорост на подаване и малка дълбочина на рязане за твърди сплави. Например: изберете и дълбочина на рязане от 0,5 мм;
3) Титановата сплав трябва да бъде избрана с ниска скорост, висока скорост на подаване и малка дълбочина на рязане. Например за Ти6 изберете и дълбочина на рязане 0,3 мм. Като вземем пример обработката на определена част: материалът е много твърд материал, след многобройни тестове най-накрая е избран като и дълбочина на рязане 0,2, за да се получи квалифицирана част.
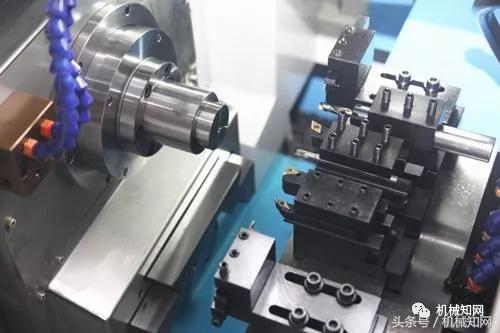
2,Техниката за подравняване на ножа е разделена на инструмент за подравняване на ножа и директно подравняване на ножа. Повечето стругове в нашата фабрика нямат устройство за подравняване на инструментите и изискват директно подравняване на инструментите Следните техники за подравняване на инструментите се отнасят до директно подравняване на инструментите.
Първо, изберете центъра на дясната страна на края на частта като точка на подравняване на инструмента и го задайте като нулева точка След като машинният инструмент се върне към произхода, всеки инструмент, който трябва да се използва, се подравнява с центъра на дясната страна на края на частта като нулева точка; Когато инструментът влезе в контакт с дясната страна на края, въведете и кликнете върху бутона за измерване. Стойността на компенсацията на инструмента автоматично записва измерената стойност, което показва, че оста е подравнена правилно. Осата е за пробно рязане, а когато използвате инструмента за регулиране на външния кръг на частта, въведете за измерване стойността на външния кръг на частта, която се регулира (например Натиснете бутона за измерване и стойността на компенсацията автоматично записва измерената стойност. В този момент оста също е подравнена правилно; Този метод за подравняване на инструмента, дори ако машинният инструмент е изключен, няма да промени стойността на подравняване след включване и рестартиране.Подходящ е за мащабно и дългосрочно производство на една и съща част, по време на което стругът не трябва да се подравнява отново.
3,Умения за отстраняване на грешки: След програмиране и подравняване на инструмента, частите трябва да бъдат тествани и отстранявани грешки. За да се предотвратят грешки в програмата и подравняването на инструмента, които могат да причинят инциденти при сблъсък, първо трябва да извършим симулационна обработка на празен ход. В координатната система на машинния инструмент инструментът трябва да бъде преместен надясно с 2-3 пъти общата дължина на частта като цяло; След като завършите симулацията на машинната обработка, потвърдете, че програмата и подравняването на инструмента са правилни и след това започнете да обработвате частите. След като първата част от частта е обработена, проверете сами и потвърдете, че тя е квалифицирана и след това намерете специален инспектор, който да я инспектира. Само след като специализираният инспектор потвърди, че е квалифицирана, отстраняването на грешки може да бъде завършено.
4,След като първото парче пробно рязане е завършено, обработените части трябва да бъдат масово произведени. Въпреки това, квалификацията на първото парче не означава, че цялата партида от части ще бъде квалифицирана, защото по време на обработката различни обработващи материали ще причинят износване на инструмента. Меките обработващи материали имат по-малко износване на инструмента, докато твърдите обработващи материали имат по-бързо износване на инструмента. Следователно, по време на обработката е необходимо да се провеждат чести проверки и своевременно увеличаване или намаляване на стойността на компенсация на инструмента, за да се гарантира квалификацията на частите.
Като вземем определена част като пример, материалът за обработка е К414, с обща дължина на обработка 180Поради изключително твърдия материал износването на инструмента е много бързо по време на обработката. От началната точка до крайната точка ще се генерира леко отклонение от 10-20мм поради износването на инструмента, поради което трябва ръчно да добавим леко отклонение от 10-20мм в програмата, за да гарантираме квалификацията на частта.
Накратко, основният принцип на обработка е първо груба машина, отстраняване на излишния материал от детайла и след това прецизна машина; Вибрациите трябва да се избягват по време на обработката; Има много причини да се избегнат вибрации, причинени от термична деформация по време на обработката на детайла, което може да се дължи на прекомерно натоварване; Това може да бъде резонанс между машинния инструмент и детайла, или недостатъчна твърдост на машинния инструмент, или може да бъде причинена от пасивиране на инструмента.Можем да намалим вибрациите по следните методи:; Намалете страничната скорост на подаване и дълбочината на обработка, проверете дали затягането на детайла е сигурно, увеличете скоростта на инструмента, което може да намали резонанса чрез намаляване на скоростта и проверете дали е необходимо инструментът да бъде заменен с нов.
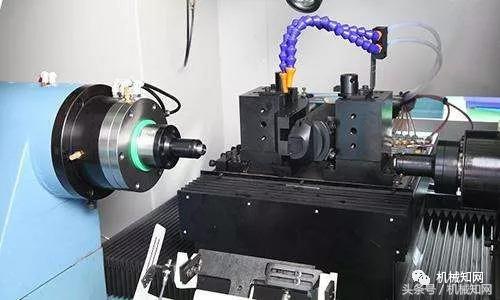
5,Опитът за предотвратяване на сблъсъци между машинни инструменти значително уврежда точността на машинни инструменти, а въздействието варира за различни видове машинни инструменти. Като цяло, тя има по-голямо въздействие върху машинни инструменти с слаба твърдост. Така че при високопрецизните стругове сблъсъците трябва да бъдат абсолютно елиминирани.Докато операторът е внимателен и овладее определени методи против сблъсък, сблъсъците могат да бъдат напълно предотвратени и избегнати.
Основната причина за сблъсъци:
Единият е входната грешка на диаметъра и дължината на режещия инструмент;
На второ място, има грешки при въвеждането на размерите и други свързани геометрични размери на детайла, както и грешки в първоначалното позициониране на детайла;
Трето, координатната система на детайла на машинния инструмент е зададена неправилно или нулевата точка на машинния инструмент се нулира по време на процеса на обработка, което води до промени.Сблъсъците на машинния инструмент се случват предимно по време на бързото движение на машинния инструмент, а опасностите от такива сблъсъци също са най-големи, което трябва да се избягва абсолютно.
Така операторите трябва да обърнат специално внимание на началния етап на изпълнение на програмата и подмяна на инструмента.Ако програмата е редактирана неправилно или диаметърът и дължината на инструмента са въведени неправилно, вероятно е да възникнат сблъсъци. В крайна фаза на програмата, ако последователността на действието на изтегляне на оста ЦПУ е неправилна, могат да възникнат и сблъсъци.
За да се избегнат гореспоменатите сблъсъци, операторът трябва напълно да използва функциите на лицевите си черти при работа с машината, да наблюдава дали има някакви ненормални движения, искри, шум, ненормални звуци, вибрации или изгорени миризми. Ако се установи някаква необичайна ситуация, програмата трябва да бъде спряна незабавно, машинният инструмент може да продължи да работи само след като проблемът с леглото е решен.
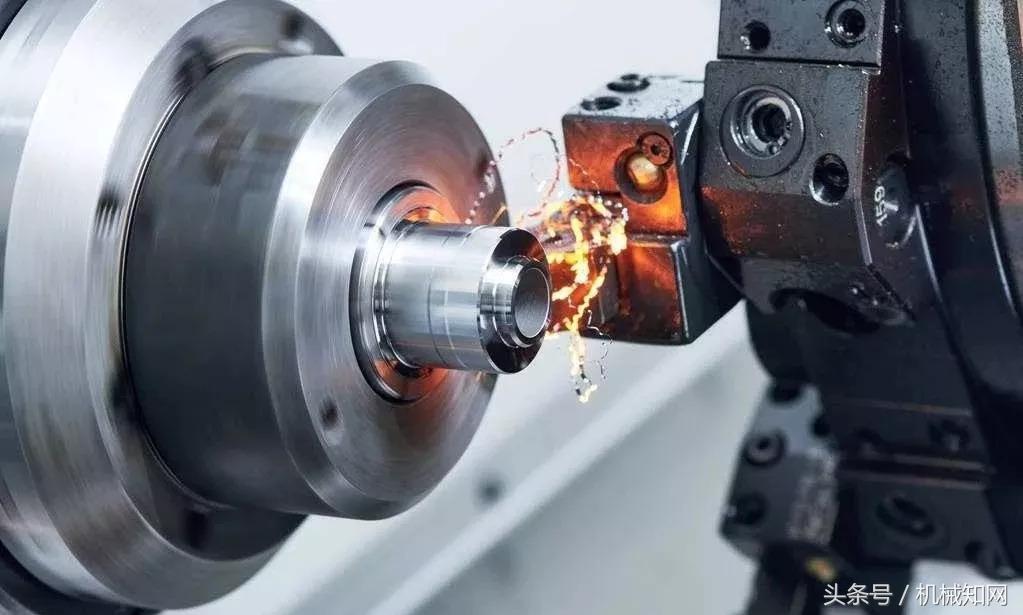
Накратко, овладяването на работните умения на машинните инструменти с ЦПУ е постепенен процес и не може да бъде постигнато за една нощ. Тя се основава на овладяване на основната работа на машинните инструменти, основни познания за механичната обработка и основни познания за програмиране. Оперативните умения на машинните инструменти с ЦПУ не са фиксирани, те изискват операторът да използва напълно въображението си и практическата си способност в органична комбинация, което е иновативен труд.