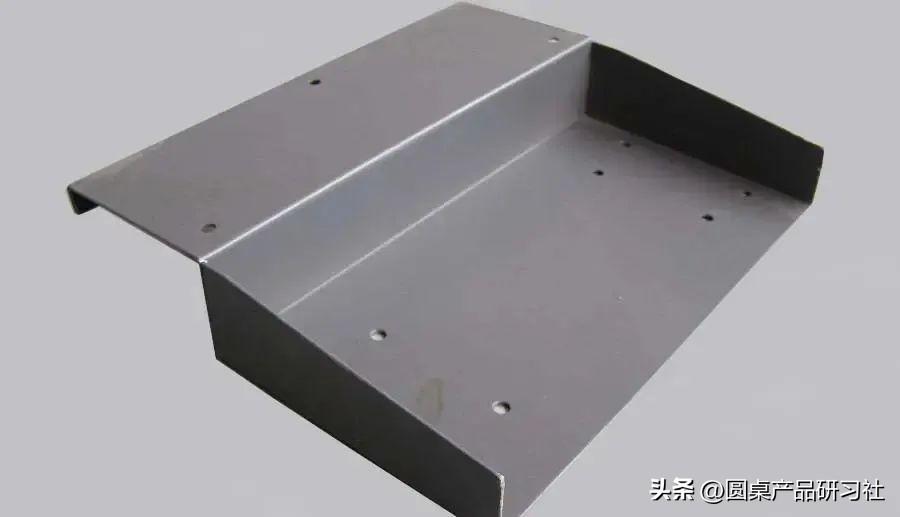
1,Сгъваемо легло съдържание за обработка: 1.Сгъваемото легло е разделено на 90 градуса сгъване и не 90 градуса сгъване според ъгъла.
Според обработката, тя може да бъде разделена на обща обработка (и специална обработка (L 1> Формата се избира въз основа на материала, дебелината на плочата и ъгъла на формиране. 2> Принципът на доверие 1) Въз основа на принципа на две правила за позициониране отзад и позициониране според формата на детайла. 2) Когато позиционирате задния габарит, обърнете внимание на отклонението и се уверете, че той е на същата централна линия като размера на огъването на детайла. 3) При огъване на малки гънки е по-добре да ги обработвате в обратна позиция. 4) По-добре е да зададете правилата към гърба и към средата. (Когато се облегнете на позицията, не е лесно задното регулиране да повдига) 5) По-добре е да сте близо до ръба на позицията и задното регулиране. 6) По-добре е да се облегнете на дългата страна. 7) Използвайте приспособления за подпомагане на позиционирането (неправилно наклонено позициониране на ръба). 3> Предпазни мерки 1. Трябва да се обърне внимание на метода на позициониране по време на обработката и стандартизирания режим на движение сред различните методи за обработка на позициониране. 2.Когато матрицата е сглобена, тя трябва да бъде огъната и издърпана назад, за да се предотврати деформация на детайла по време на огъване. 3.При огъване на големи детайли вътрешно, поради голямата форма на детайла и малката огъваща площ, е трудно инструментът за рязане и зоната на огъване да съвпадат, което води до затруднения при позиционирането на детайла или повреда на огъвания детайл. За да се избегне горната ситуация, може да се добави точка на позициониране в надлъжната посока на машинната обработка, така че машинната обработка да може да бъде позиционирана от две посоки, което прави позиционирането на машинната обработка удобно и подобрява безопасността на машинната обработка, избягва повреда на детайла и подобрява ефективността на производството. 2. Нфолд изисква различни методи на обработка в зависимост от формата. При огъване вътрешните размери на материала трябва да бъдат по-големи от 4мм, а размерът на размера Х е ограничен от формата на матрицата. Ако размерът вътре в материала е по-малък от 4ММ, трябва да се използват специални методи за обработка. 1> Изберете матрицата въз основа на дебелината на материала, размера, материала и ъгъла на огъване. 2> Принципът на доверие 1) Уверете се, че детайлът не пречи на инструмента 2) Уверете се, че ъгълът на позициониране е малко по-малък от 90 градуса. 3) Най-добре е да използвате две правила за позициониране отзад, освен при специални обстоятелства. 3> Предпазни мерки 1) След огъване ъгълът трябва да се поддържа на или малко по-малко от 90 градуса, за да се улесни машинната обработка и позиционирането. 2) По време на втория процес на сгъване е необходимо позицията да се подравни с обработващата повърхност като център. 3. Огъването, известно още като сегментна разлика, се отнася до огъването на един положителен и един отрицателен. Разликата в сегмента на наклонените ръбове и разликата в сегмента на прави ръбове се разделя според ъгъла. Минималният размер за обработка на огъване е ограничен от обработката на матрицата, докато максималният размер на обработка се определя от формата на обработващата машина. Като цяло, когато вътрешният размер на сгънатия материал е по-малък от 3,5 Т, се използва сегментирана обработка на матрици. Когато е по-голямо от 3,5 се използват нормални методи за обработка. 1> Принципът на доверие 1) Удобно позициониране и добра стабилност. 2) Като цяло позиционирането е същото като сгъването. 3) Вторичното позициониране изисква обработеният детайл да бъде промит с долната матрица. 2> Предпазни мерки 1) Ъгълът на обработка на сгъвката трябва да бъде на място, обикновено се изисква да бъде между 89,5-90 градуса. 2) При изтегляне назад съгласно по-късните спецификации трябва да се обърне внимание на деформацията на детайла. 3) Редът на обработка трябва да е правилен. 4) За специална обработка могат да се използват следните методи: Метод на разделяне на централните линии (ексцентрична обработка) Обработка с малък V (изисква увеличаване на коефициента на огъване) Лесно формоване Смляне на долната плесен 4. Обратно сгъване и изравняване, известно също като компресия на ръба. Стъпките за обработка на мъртви ръбове са: 1. Огънете и поставете на дълбочина около 35 градуса първо. След това сплесквайте и оформете, докато стане плоска и плътно прикрепена. 1> Метод за избор на модел Изберете ширината на жлеба на долната матрица с дълбочина 30 градуса според 5-6 пъти дебелината на материала и изберете горната матрица според специфичната ситуация на обработка на мъртвите ръбове. 2> Предпазни мерки Трябва да се обърне внимание на паралелизма на двете страни на мъртвия ръб, когато размерът на обработка на мъртвия ръб е сравнително дълъг, сплесканият ръб може да бъде сгънат първо под повдигнат ъгъл и след това сплескан. За по-къси мъртви ръбове може да се използва обработка на подплънки. Хардуерът за пресоване използва сгъваемо легло за пресоване и уплътняване на хардуерни компоненти, обикновено използвайки спомагателни форми като вдлъбнати форми и приспособления за обработка. Като цяло има: гайки за компресия, болтове за компресия, винтове за компресия и други хардуерни компоненти. Предпазни мерки за обработка: 1.Когато формата на детайла трябва да се избягва по време на машинната обработка, трябва да се вземат мерки за избягване. 2.След обработката е необходимо да се провери дали въртящият момент и тягата отговарят на стандартите и дали хардуерът и детайлът са плоски и плътно прикрепени. 3.След огъване и натискане, когато натискате до машинния инструмент, обърнете внимание на избягването на машинната обработка и паралелизма на матрицата. 4.Ако е изпъкнал, също така е важно да се отбележи, че не трябва да има пукнатини по издутия ръб и издутият ръб не трябва да се изпъква над повърхността на детайла. 6. съдържанието на обработка на лесно формоване обикновено включва: малки разлики, куки, мостове, торби, пружини под налягане и някои неправилни форми. Принципът на проектиране на Лесен молд се отнася до "Принцип на проектиране на Лесен молд за лазерно рязане" Лесно за формоване обикновено използва пост позициониране или самопозициониране. Най-важното нещо при обработката на горното съдържание с лесна мухъл е, че неговата функция и изисквания за монтаж не са засегнати и външният вид е нормален. 2,Чести проблеми и решения при обработката на сгъваеми легла: 1.Анализ на причините за плъзгане по време на обработката: 1.При избора на огъване матрица обикновено се избира ширина на жлеба от (4-6) Т. Когато размерът на завоя е по-малък от половината широчина на избрания жлеб, ще възникне плъзгащо явление. 2. Избраният слот е твърде голям 3. Обработка на процесите Метод на разтвора 1. Метод на отклонение на централната линия (ексцентрична обработка). Ако вътрешните размери на огънатия материал са по-малки от (4-6) Т/2, компенсирайте разликата възможно най-много 2. Обработка на подложки. 3. Огънете с малък канал и нанесете натиск с голям канал. 4. Изберете по-малък слот. 2. Анализ на причините, поради които вътрешната ширина на огъване е по-тясна от стандартната ширина на мухъла: Поради минималната стандартна ширина на матрицата за сгъваемо легло е 10 мм, частта за обработка на огъване има ширина по-малка от 10 мм. Ако е 90 градусов завой, размерът на дължината му не трябва да бъде по-малък от 2 (L+V/2)+T. За този тип огъване матрицата трябва да бъде фиксирана върху седалката на матрицата (с изключение на неограничената свобода в посока нагоре), за да се избегне изместване на матрицата, което може да доведе до изстъргване на детайла или да причини аварии при безопасността. Решение: 1> Увеличете размера (да се координира с клиента), т.е. увеличете ширината на вътрешната гънка. 2> Лесна за формоване обработка 3> Инструменти за шлифоване (което води до увеличаване на разходите за обработка) 3. Дупката е твърде близо до линията на огъване и огъването ще доведе до дупката да издърпа материала. Анализ на причините за обръщане: Ако приемем, че разстоянието между отвора и огъващата линия е L, когато L<; При (4-6) дупката ще издърпа материала. Основно поради силата на разтягане по време на процеса на огъване, материалът претърпява деформация, което води до явлението дърпане и обръщане. Съгласно съществуващата стандартна ширина на жлеба на матрицата минималната стойност за различните дебелини на плочите е показана в следната таблица: Решение: 1> Увеличете размера и смилете сгънатите ръбове след оформяне. 2> Разширете отвора до огъващата линия (не трябва да има въздействие върху външния вид или функцията и клиентът се съгласява). 3> Обработка на режещите линии или обработка на тръбите за налягане 4> Ексцентрична обработка на мухъл 5> Промяна размера на отвора 4.Анализ на причините за деформация в точката на извличане след огъване поради малкото разстояние между екстракционния ръб и огъващата линия: Когато L<; При (4-6) поради контакта между чертежа и долната матрица възниква деформация по време на процеса на огъване поради силата, упражнена върху чертежа. Решение: 1> Прережи или натисни линията. 2> Промяна на размера на рисунката. 3> Използване на специални форми за обработка 4> Ексцентрична обработка на мухъл 5. Анализ на причините за изкривяване след сплескане на дългия мъртъв ръб: Поради дългия мъртъв ръб, той не може да се залепи плътно, когато е сплескан, което води до свиване на края след сплескане. Тази ситуация е тясно свързана с сплесканата позиция, така че трябва да се обърне внимание на сплесканата позиция при сплескане Решение: 1> Преди да сгънете мъртвия ръб, първо сгънете повдигнатия ъгъл (както е показано на диаграмата), а след това го сплеснете. 2> Разширяване на няколко стъпки: Натиснете първо края, за да огънете мъртвия ръб надолу. Справи корените. Внимание: Ефектът на сплескане е свързан с оперативните умения на оператора, така че моля обърнете внимание на действителната ситуация по време на сплескане. 6. анализ на причините за лесната фрактура на издърпване на моста с висока височина: 1> Поради високата височина на моста материалът е силно опънат, което води до фрактура. 2> Ъглите на матрицата не са полирани или не са достатъчно полирани. 3> Здравината на материала е твърде лоша или тялото на моста е твърде тясно. Решение: 1> Разтегнете дупката за процеса отстрани на фрактурата. 2> Увеличи ширината на моста. 3> Смачкайте ъгъла на матрицата и увеличете прехода на дъгата. 4> Добавете смазочно масло към смукателния мост. (Ето защо, този метод ще направи повърхността на детайла мръсна, така че не може да се използва за части и т.н.) 7. Анализ на причините за работа на размерите на машинната обработка при лесна обработка на матрицата: Поради силата на натискане напред върху детайла по време на процеса на обработка, детайлът се движи напред, което води до увеличаване на малкия ъгъл на гребло отпред. Решение: 1> Премахнете сенчестите зони на снимката. Обикновено разликата се компенсира възможно най-много. 2> Смачкайте всички самопозициониращи се части на матрицата и превключете на фиксирано позициониране. (Както е показано на фигурата по-долу) 8. Общият размер на материала (отнасящ се до разгъване) е твърде малък или твърде голям, което не съответства на кръглата повърхност. Анализ на причините: 1> Проектът беше стартиран неправилно. 2> Размерът на рязане е неправилен. Решение: Изчислява се разпределеното отклонение за всеки завой въз основа на общото отклонение в посоката на отклонението и броя на огъващите остриета. Ако изчисленото допустимо отклонение е в рамките на обхвата на допустимото отклонение, детайлът е приемлив. Ако размерът е твърде голям, за обработка може да се използва малък жлеб. Ако размерът е твърде малък, за обработка може да се използва голям жлеб. 9. Анализ на причините за деформация, причинена от разширение или хлабаво прилягане след пробиване на отвори и зацепване: 1> Подуването се дължи на това, че ъгълът на отвора е твърде малък или борбите на фланеца са твърде големи. 2> Разхлабеното прилягане се дължи на неадекватното разширяване на отвора. 3> Деформацията може да бъде причинена от неправилно подравняване на отвора или неправилен метод на чифтосване. Решение: 1> Изберете удар с голям ъгъл вместо това. Внимание: Бури около дупката по време на изтегляне на дупката и фланциране. 2> Увеличете налягането, увеличете и задълбочете дупката за салата и използвайте пунш с голям ъгъл вместо това. 3> Методът за изкопаване на причините за промяна на метода на чифтосване и неравномерност на отворите. 10. Анализ на причините за изкривяване или деформация на детайла след натискане на винт: 1> По време на обработката на продукта няма счупени плоски детайли. 2> Неравномерна сила или прекомерно налягане върху долната повърхност на детайла. Решение: 1> При натискане на винта детайлът трябва да бъде изравнен. 2> Направи опорна рамка. 3> Регулирай налягането отново. 4> Увеличете обхвата на силата върху долната повърхност и намалете обхвата на силата, приложена върху горната повърхност. 11. Анализ на причините за липсата на паралелизъм между двете страни след сегментната разлика: 1> Формата не е калибрирана. 2> Горните и долните уплътнения на мухъла не се регулират правилно. 3> Изборът на горни и долни повърхности на мухъл е различен. Решение: 1> Прекалибрирай формата. 2> Добавяне или премахване на подложки. (За конкретни методи за регулиране, моля, вижте "Технология за обработка на сегменти") 3> Плесента е ексцентрична. 4> Заменете повърхността, така че повърхностите на горните и долните форми да са еднакви. 12. Анализ на причините за дълбоките гънки по повърхността на продукта: 1> В-жлебът на долната матрица е малък 2> Ъгълът на жлеба в долната матрица е малък 3> Материалът е прекалено мек. Решение: 1> Използване на обработка на големи V-жлебове 2> Използване на матрица с голям ъгъл за обработка 3> , възглавница материал огъване (възглавница стоманен лист или лепило Юли) 13. Анализ на причините за деформация в близост до точката на огъване след огъване: Машината работи бързо по време на процеса на огъване, а скоростта на огъване нагоре на детайла по време на деформация е по-голяма от скоростта, с която операторът поддържа движението на детайла с ръцете си. Решение: 1> Намаляване на работната скорост на машината 2> Увеличете скоростта на опората на ръцете на оператора. 14. Анализ на причините за напукване в АЛ части по време на огъване: Благодарение на уникалната кристална структура на материала, той е склонен да се счупи, когато се огъне успоредно с посоката на зърното. Решение: 1> При рязане обмислете въртенето на материала перпендикулярно на посоката на огъване (дори ако посоката на огъване на материала е перпендикулярна на зърното). 2> Увеличете ъгъла на горната плесен.