Казва се, че плесените са майката на индустрията, но какво точно е непрекъснат щамповане матрица?
Като цяло, т.нар. непрекъснато щамповане матрица е структурата на процеса на комбиниране на множество проекти в една и съща матрица, резба на материалния колан в матрицата и щампване една стъпка по една, за да се създаде пълен хардуер.
Формоване на щамповане: Сред различните видове формове за щамповане, формовете за непрекъснато щамповане са най-подходящи за масово производство поради високата им производствена ефективност.Освен това, формовете за непрекъснато щамповане имат широк спектър от приложения и могат да се използват за различни хардуерни части.

Основните предимства на непрекъснатите щамповани форми са:
1. Производството с бобинни материали води до по-ниско използване на материала и спестява недостатъка на непрекъснатото подаване.
2. Инженерното и структурното проектиране са по-гъвкави.
3.Един удар може да произведе множество ПЧС, с бърза скорост на производство и висока ефективност.
4. Същият набор от форми може да произвежда множество продукти едновременно.
5. Лесно за постигане на автоматизирано производство, спестяване на много работна ръка и материални ресурси.
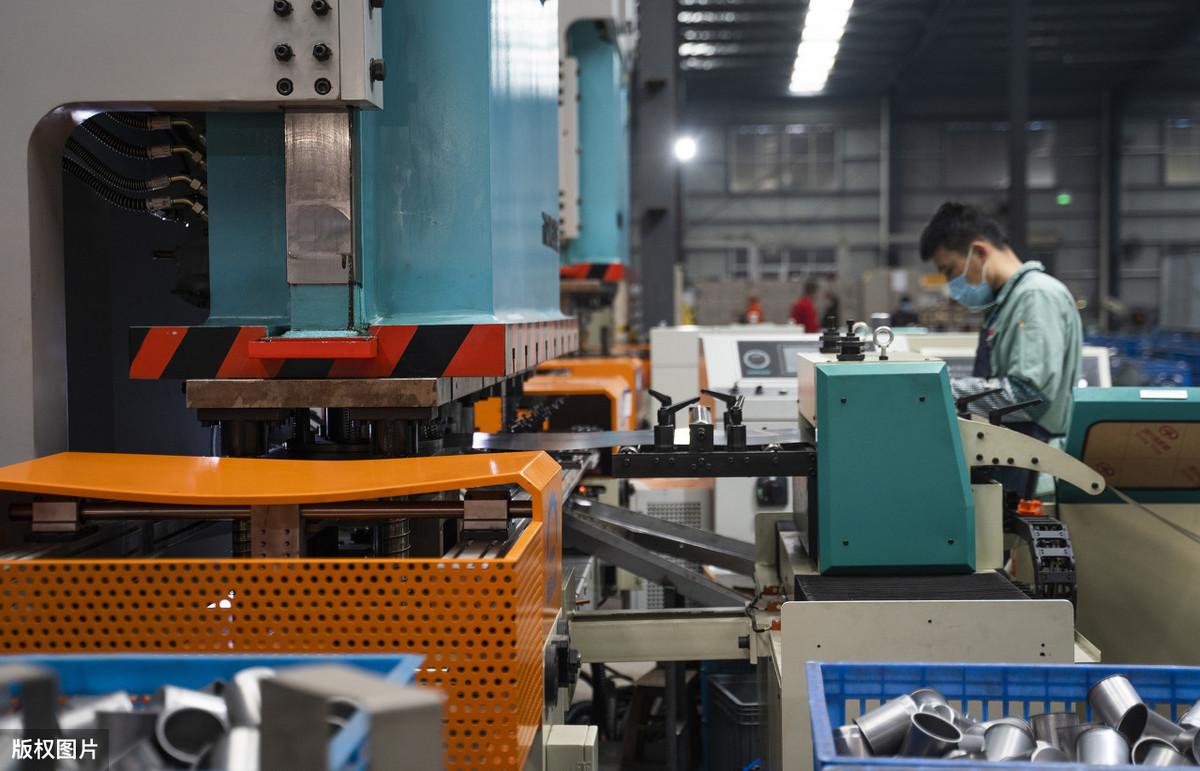
Елементи за потвърждение за преглед на чертежите на готовия продукт преди проектирането и отварянето на мухъл:
1. посока на ръба и валцуване, готов продукт материал и дебелина.
2. посоката на намотката на непрекъснатата лента (обърнете внимание на това дали се изисква галванизиране).
3. Анотациите трябва да са ясни, а чуждите езици трябва да бъдат преведени и анотирани.
4. Дали размерите и допустимите отклонения на чертежа на крайния продукт са напълно маркирани.
5. Какъв е методът на ъгъла за гледката, и са размерите, посочени в метрични или имперски.
6. Позицията на режещия ръб влияе ли върху функционалността или монтажа на крайния продукт.
7.Дали двете страни на огъваната част в корена на крайния продукт са симетрични, асиметрията може да причини отклонение след огъване и трябва да бъде договорена с клиента.
8. Опитайте се да получите функции за използване на продукта и свързано съдържание от клиентите, доколкото е възможно.
Когато размерите или допустимите отклонения са неразумни, липсват или не са ясни, клиентът трябва да бъде уведомен писмено и да бъде поискан да предостави писмен отговор, който следва да бъде изцяло запазен за бъдеща справка.
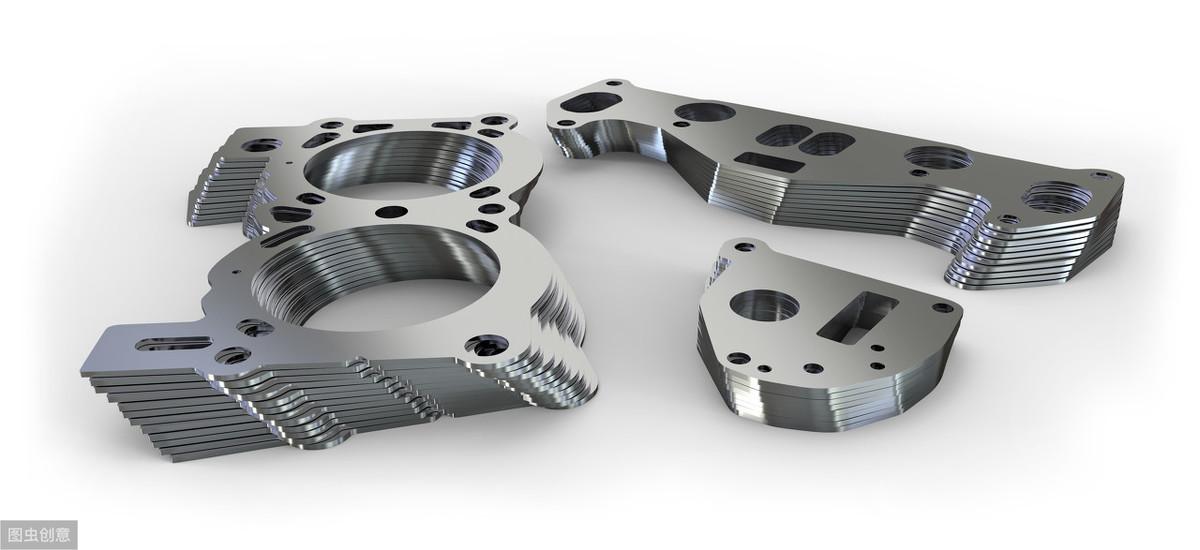
Предпазни мерки при разгъване на настройките:
Настройката на размера трябва да бъде логична, например височината на огъване на отвора и контакта трябва да бъдат зададени с горни граници.
2. долната граница трябва да бъде определена за разгънатия размер на извитата форма и размера на корена на сгънатия вътрешен диаметър.
3. Когато има изискване за стойност, обхватът на допустимото отклонение трябва да бъде умножен, когато е 1.33, и умножен, когато е 1.67
По-късно го нагласи.
4.Когато има изисквания за галванизиране, трябва да се вземат предвид промените в размерите преди и след галванизирането.
5. Материалът е относително мек и ще има разтягане, когато се огъне над 80 градуса
Трябва да се обърне внимание при разгъване на около 0,10-0,12.
6.При огъване и формиране в зигзагова форма, ще има разтягане и внимание трябва да се обърне при разгъване.
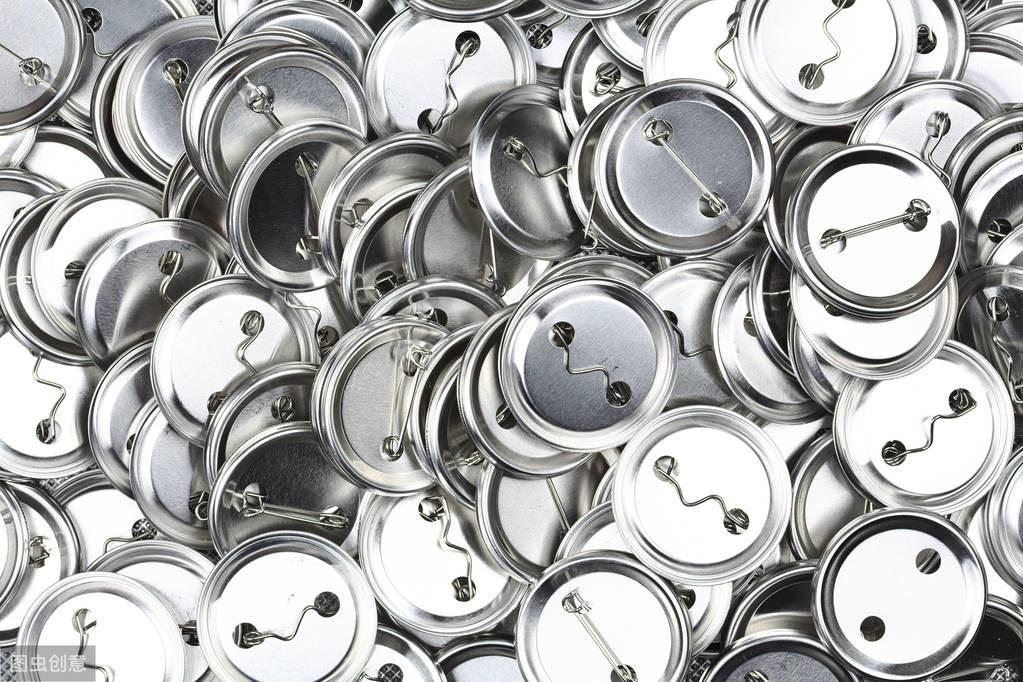
Процес на проектиране на матрицата за непрекъснато щамповане:
1. Стойностите за разгъване на готовия продукт и стойностите за огъване.
2. Задайте посоката на борбите на крайния продукт и посоката на търкаляне.
3. Задайте разгъната диаграма (три изгледа).
4. Настройте инженерната структура диаграма.
5. Дискусионна среща за нова конструкция на матрицата.
6. Разглобете части и рисувайте.
7. Корекция и рисуване.
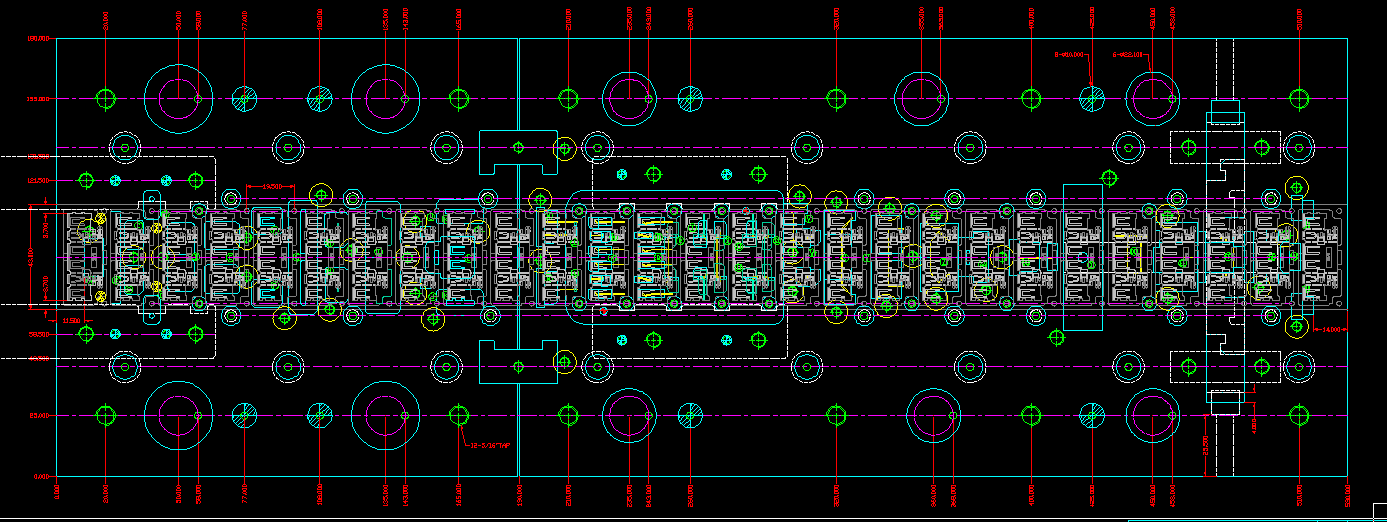
Задаване на празнини между различните материали:
1.Разстоянието на срязване на месинг (С680) е 4% (дебелина на материала 0,04 = размер на едностранната пролука).
Разстоянието на срязване на фосфорната мед (е 5% (дебелина на материала 0,05 = размер на едностранната пролука).
Разстоянието на срязването на западната бяла дъска (е 5% (дебелина на материала 0,05 = размер на едностранната пролука).
4.Разстоянието на срязване на е 4% (дебелина на материала 0,04 = размер на едностранната пролука).
Разстоянието на срязване от неръждаема стомана (дебелина на материала 0,04 = размер на едностранната пролука).
6.Разстоянието на срязване на алуминий е 2% (дебелина на материала 0,02 = размер на едностранната пролука).