Тъй като повечето местни предприятия за производство на матрици за щамповане са малки и средни предприятия и подходяща част от тези предприятия все още са в традиционния етап на управление на производството в стил цех, те често пренебрегват стабилността на матриците, което води до дълги цикли на разработване на матрици и високи производствени разходи, които сериозно ограничават темпото на развитие на предприятието.
Както е добре известно, металните материали, използвани в печатни форми, включват много сортове, а изискванията и критериите за подбор на техните материали също са различни поради различните ефекти на различните части в матрицата. Ето защо, как да изберете материалите за мухъл разумно се превърна в една от много важните задачи в дизайна на мухъл.
При избора на материали за мухъл, в допълнение към изискването материалът да има висока якост, висока устойчивост на износване и подходяща якост, е необходимо също така напълно да се вземат предвид характеристиките и производствените изисквания на преработения продукт материал, за да се постигнат изискванията за стабилност на формоването на мухъл.
В практическата работа дизайнерите на мухъл са склонни да избират материали за мухъл въз основа на личен опит, което често води до нестабилно оформяне на мухъл поради неправилния избор на материали на мухъл части при щамповане. Струва си да се отбележи, че по време на процеса на щамповане всеки тип печатен лист има свой собствен химичен състав, механична функция и характерни стойности, тясно свързани с функцията на щамповане.Нестабилността на функцията на печатния материал, колебанията в дебелината на печатния материал и промените в печатния материал не само пряко засягат точността и качеството на обработката на щамповане, но също така могат да доведат до повреда на печатните форми.
За да се реши проблемът с стабилността на мухъла, е необходимо стриктно да се контролира от следните аспекти:
1. в етапа на планиране на процеса, чрез анализ на продукта, могат да се предвидят потенциални дефекти, които могат да възникнат по време на производството, и след това може да се разработи стабилен производствен процес план;
2. Прилагане на стандартизация на производствените процеси и производствените техники;
3. Създаване на база данни и непрекъснато обобщаване и оптимизиране; С помощта на софтуерната система за анализ се получи оптималният план за решение.
Тази статия е от ЕМАР Молд Ко ООД За повече информация, свързана с ЕМАР, моля, кликнете на За повече информация, свързана с ЕМАР,
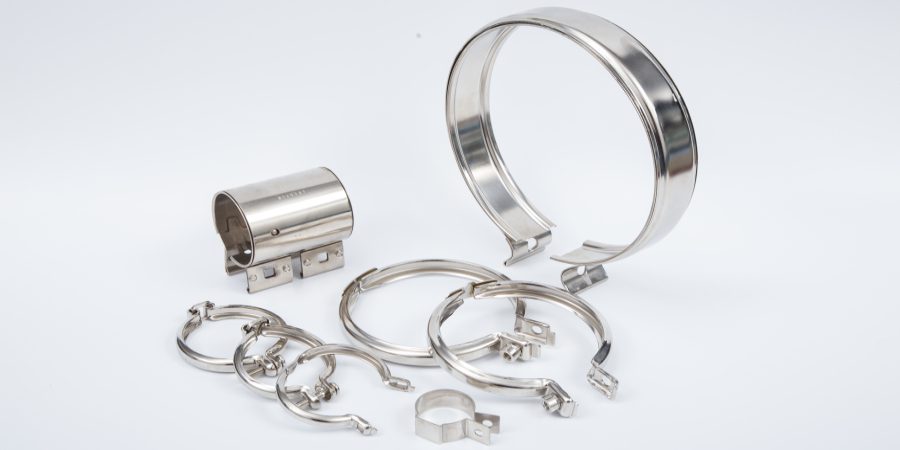