蜗轮是一种与蜗杆相啮合、齿形特殊的齿轮。蜗轮齿部的切削加工一般用滚齿机完成﹐主要有滚齿和飞刀切齿两种方法。最近有朋友询问滚刀加工蜗轮时的安装角如何调整以及需要注意的事项,今天咱们就聊一聊这个话题。
制造精密蜗轮时,可在滚齿或切齿后再进行剃齿﹑珩齿或研齿等精整加工。
滚齿
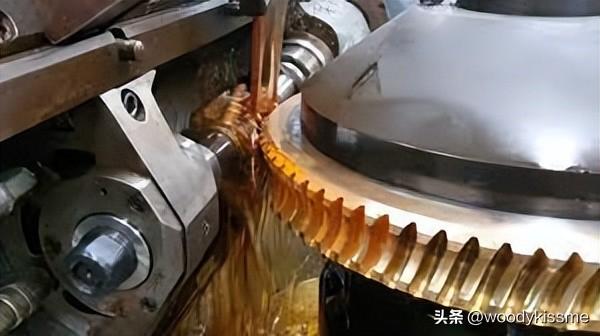
采用基本参数与工作蜗杆相同的蜗轮滚刀﹐按展成法原理切出齿形。如果采用径向进给法滚齿﹐则滚刀与工件按Z
2/Z 1的传动比(Z 1为工作蜗杆螺纹头数﹐Z
2为蜗轮齿数)对滚﹐两者逐渐靠近直到其中心距等于工作蜗杆与蜗轮啮合时的中心距为止。采用切向进给法滚齿时﹐机床除保证刀具旋转外﹐还要有轴向进给﹔同时机床的工作台也要增加相应的附加转动﹐才能实现展成运动﹐这就要使用差动链。因此﹐切向进给法的加工精度一般不如径向进给法﹐但齿面质量较好﹐且不会产生根切现象。滚切蜗轮的精度一般可达6~8级(JB162-60)。
精密蜗轮的滚齿需在高精度的分度蜗轮滚齿机上采用高精度的滚刀进行﹐也可在通用滚齿机上加装机械的或电子的传动链误差校正装置﹐以提高加工精度﹐最高加工精度可达3级。
飞刀切齿
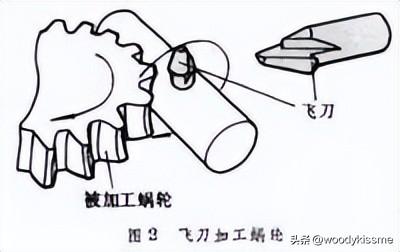
飞刀相当于蜗轮滚刀的一个刀齿。飞刀切齿只能采用切向进给法﹐在滚齿机上可使飞刀转一周蜗轮转Z 1个齿﹐再加上飞刀的切向进给与工作台的附加转动﹐也能按展成法原理切出正确的齿形﹐精度可达7~8级。飞刀制造简单﹐但切齿的生产率低﹐适于在单件生产和修配工作中采用。
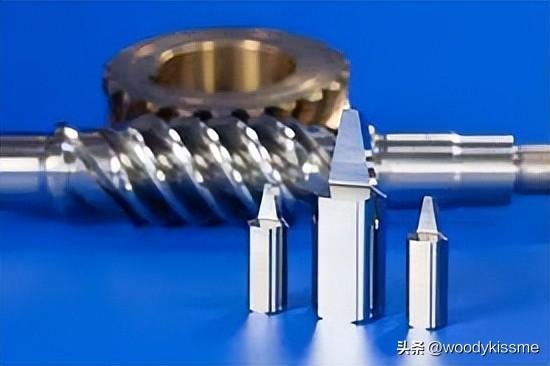
剃齿
蜗轮剃齿刀的基本参数与工作蜗杆相同。蜗轮剃齿一般用滚齿机﹐可以由剃齿刀带动蜗轮自由剃齿﹐也可在机床传动链控制下强迫剃齿﹐剃后齿面质量和精度有所提高。
珩齿和研齿
蜗轮滚齿或飞刀切齿后﹐为了提高齿面质量﹑改善蜗轮与蜗杆啮合时的接触情况﹐可在滚齿机上珩齿或研齿。珩齿工具是用磨料与塑料﹑树脂的混合物浇铸在基体上而制成的珩磨蜗杆﹔研齿时用铸铁制成的研磨蜗杆加研磨剂与蜗轮对研。
以上是蜗轮不同的加工方法,咱们今天的正题是:在滚切蜗轮时,蜗轮滚刀怎么安装,滚切的时候要注意哪些问题:
滚切蜗轮
1.普通型蜗轮滚刀
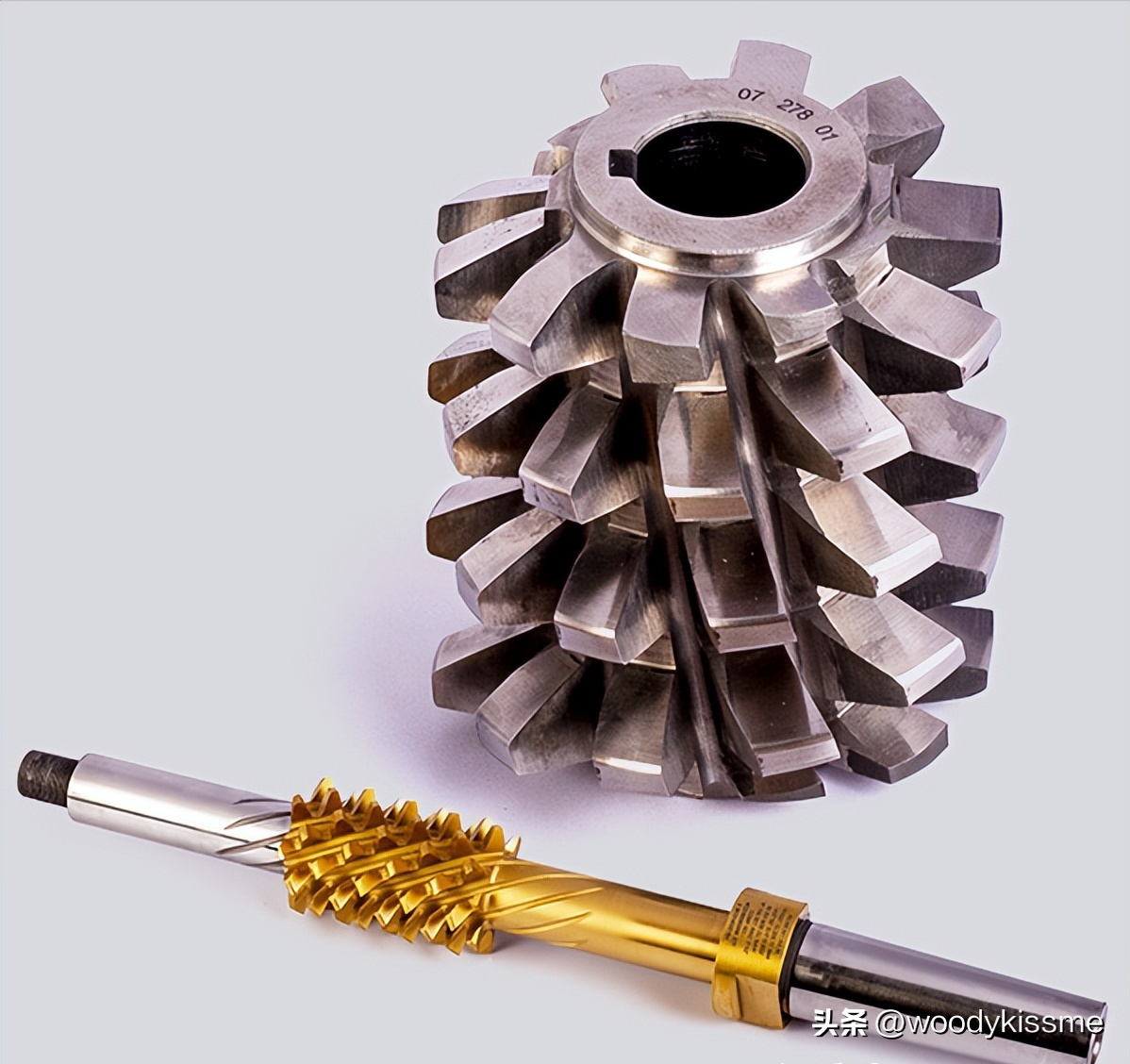
通常我们在加工蜗轮时,所用标准蜗轮滚刀(以下简称滚刀)的基本蜗杆符合被加工蜗轮相啮合的工作蜗杆,其主要参数如模数、压力角、分度圆直径、头数、螺旋方向和螺旋升角等,与相啮蜗杆一致,而且在加工蜗轮时,滚刀的加工中心距与工作中心距相同,这样加工出的蜗轮在理论上与蜗杆能够保证正确的啮合。
普通滚刀滚蜗轮时,滚刀处于工作蜗杆的工作位置,即刀具为水平状态,与蜗轮呈正交错空间啮合,慢慢地从径向往里切,切到工作中心距时,则滚齿结束,蜗轮滚切完毕。
2.增径蜗轮滚刀(大外径滚刀)
但实际生产中发现传统滚刀加工的蜗轮啮合效果往往不理想,传动扭力也很难达到预期要求,增径蜗轮滚刀的发展和使用解决了这一难题。下面简要介绍一下增径蜗轮滚刀的特点、基本设计原理和正确使用方法。
增径蜗轮滚刀采用局部接触理论设计,滚刀的分度圆直径做得比工作蜗杆的分度圆略大些(非对偶),这样理论上不是局部接触,而是“点接触”了,但在加载使用时,由于弹性变形使得点接触成为小的局部面接触,接触面呈椭圆形,从而满足了啮合斑点集中在中间的要求。
这种点接触传动一方面克服了由于线接触蜗杆副瞬时接触线与相对速度方向接近,使其润滑性能变差的缺点,从而提高了轮系的传动效率;另一方面由于传动质量对蜗杆副制造和安装误差的敏感性降低,从而降低了对蜗杆副制造及安装精度的要求。还允许蜗轮滚刀具有更多的重磨次数,从而有效延长了滚刀的使用寿命。某些场合,蜗杆分度圆太小,导致滚刀制造困难、强度差,增大直径后可解决这一难题,使滚刀制造成为可能。
3.增径蜗轮滚刀设计原理
按螺旋齿轮啮合原理,使滚刀基本蜗杆的法向基节与工作蜗杆的法向基节相等。增径后滚刀基本蜗杆节圆处的法向压力角不变,与工作蜗杆相同,头数不变,二者的法向模数相同。
一般先选定分度圆的增加百分比,增径量的选择通常根据试验和经验。它的大小和所加工蜗轮的蜗杆类型及接触区域的大小都相关,一般来说,蜗杆单头时取大值,多头时取小值。当然也可以通过计算的,但计算过程相对复杂。
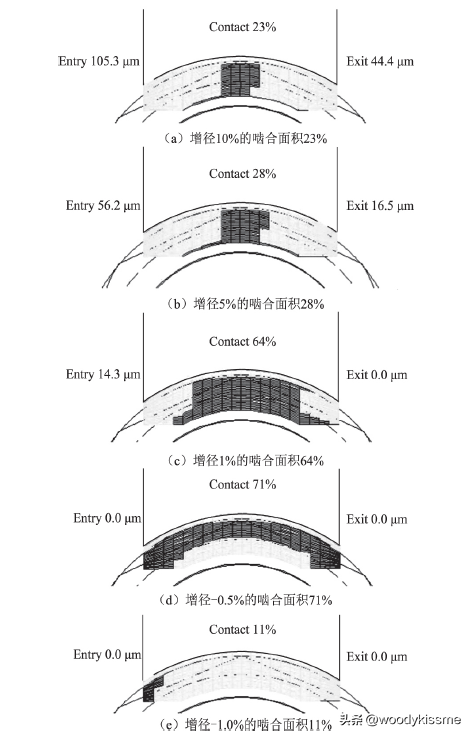
增径量和接触区域面积关系
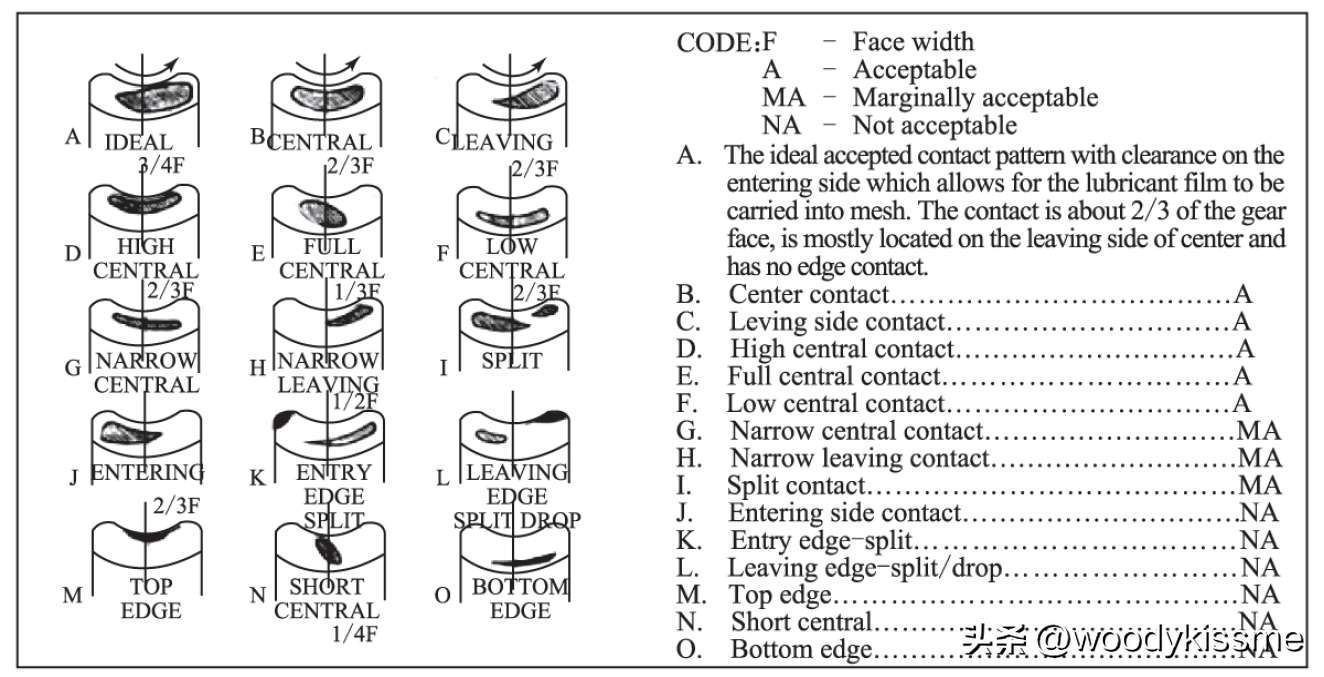
一般来说,增径量较大,按照经验可以做到20%增径甚至更大,根据这一要求计算出增径量。
已知:蜗杆mx、αx ( αn)、d(r)、λ、n(m为模数,α为压力角,d为分度圆直径,r为半径,λ为螺纹升角,n为头数)和蜗轮宽度b2。符号中下标凡含o者表示刀具,下标不含o者表示工作蜗杆;下标x表示轴向,n表示法向,2表示蜗轮。
蜗杆的螺旋角:β=90°-λ
设滚刀节圆半径的增量为Fr,增径后的滚刀节圆半径为ro,则:
ro=r+Fr
cosβo=rcos(β)/ro
mxo=mxsinβ/sinβo
相应的滚齿时的中心距增量为:
ΔA=Fr
滚齿的安装角: SA=β0-β
滚刀用盾重磨之后,由于滚刀外径减小,需要重新计算安装角。一般设计的滚刀都考虑了刃磨问题。所以在设计时会在之前的基础上增加一个附加值Δr(备磨量,一般为0.1M左右)这时:
ro'=ro+Δr
do'=2ro'
tanβo'=tan(βo)(ro+Δr)/ro
λo'=90°-βo'
ΔA'=Fr+Δr
此时,安装角应为:SA'=β-βo'
4.增径蜗轮滚刀和普通滚刀的主要差异
根据以上设计原理可知,增径滚刀的模数已不再等于原始蜗杆的模数了,而是略小于原始蜗杆的模数;螺纹升角也不同于原始值了。
增径蜗轮滚刀与传统蜗轮滚刀的结构差别
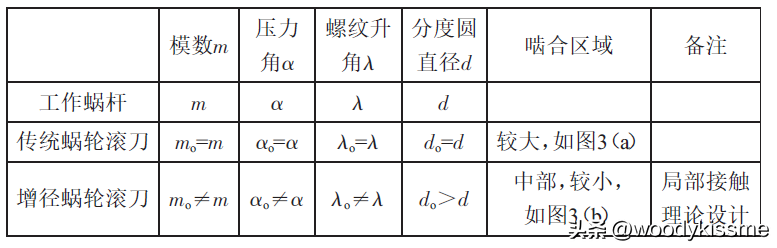
增径蜗轮滚刀与传统蜗轮滚刀的使用差别
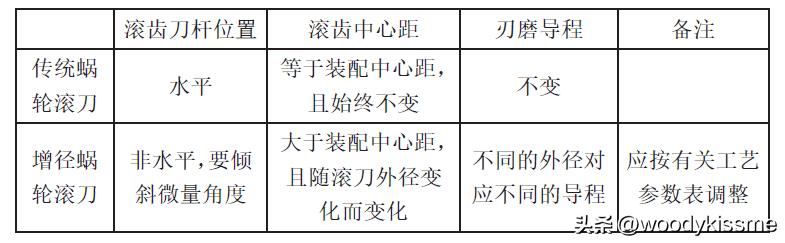
5.增径蜗轮滚刀使用方法
由于增径蜗轮滚刀的螺纹升角已不等于工作蜗杆的螺纹升角,故加工蜗轮时刀子也不再是水平了,而是要扳一个微量的安装角(注意方向)。滚齿中心距也不等于装配中心距,而是略大于装配中心距。刀子刃磨后因直径变小,参数有变,导致各次滚齿时的上述各项都要跟着变化,因此,在使用增径滚刀加工蜗轮时,必须对首件蜗轮进行接触斑点的检测,根据接触斑点的情况,再微调滚刀安装角度,确保蜗轮的接触斑点在蜗轮的中部,才能正式开始加工蜗轮,以达到预期效果。
为了保证增径滚刀加工的蜗轮螺旋角符合图纸的要求,在安装增径滚刀时,必须将滚刀刀架扳转一个角度。至于这些工艺参数如何变化,一般刀具供应厂家都会提供一份参数调整表。
注意事项:(1)刀具刃磨后需要重新测量滚刀的外径值。
(2)保证正确的安装角度和中心距。
(3)对啮合斑点观察,及时调整安装角。
如果这篇对您有所帮助,请帮忙点个赞,谢谢!
我是woodykissme,定期分享有关,机械传动及齿轮加工方面的内容,对这方面感兴趣的小伙伴,可以关注我。希望能够与大家讨论一下:
齿轮的设计及加工方法,加工齿轮所用的刀具设计、制造及使用方面的相关问题。
- 齿轮刀具设计计算方法,相关应用程序的开发,CAD二次开发自动绘图等的相关技术问题。
- 刀具应用方面,刀具的切削参数、涂层和使用寿命,加工中遇到的问题和解决办法等问题。