方法就这么简单,但是价值巨大,关键看你重视不重视!
这只是其中方法之一,还有更多方法,军哥后面给大家传授。
画出刀具路径图,是一种倒推方法,什么样的刀路就会决定后面怎么编写程序。
比如锯齿型螺纹刀路图如下,两侧的牙型角度数不一样。
比如下面TR螺纹的刀具路径图,左右借刀
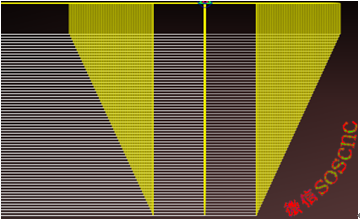
今天文章就和大家聊聊T型螺纹的宏程序编程
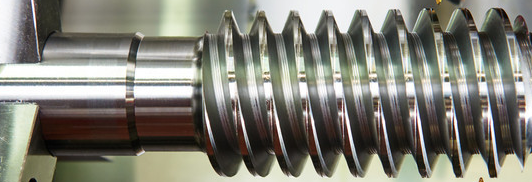
如上刀路图:分层车,每一层三刀,即先中间,再两边左右借刀方法
刀路图放大,如下图所示:
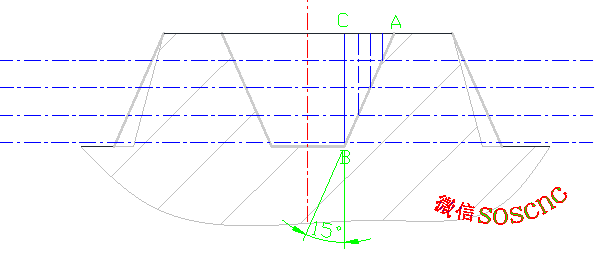
这样大家就可以直观看到:(如上图右侧的借刀)随着切深加深,刀具需要沿着AB线移动,这样借刀出来才是需要的螺纹牙型。
换句话说吃刀深度X 的尺寸和Z方向的尺寸有关系,这个关系满足勾股定律 ,即TAN15=AC/BC
那么可以推导出:AC=TAN15* BC
这个关系式太重要了,后面编程中随着切深BC 的变化,AC也就按照此关系式变化,从而加工出Tr型螺纹轮廓形状。
那么 Tr轮廓形状并不代表Tr螺纹就能合格加工出来。
因为加工时候还要考虑刀具。
因为具体到每一个Tr型螺纹是有具体牙型尺寸的。
比如选择的刀宽2mm (左右借刀,刀具宽需要小于牙底宽)
比如TR100*12外螺纹为例子,相关尺寸如下:
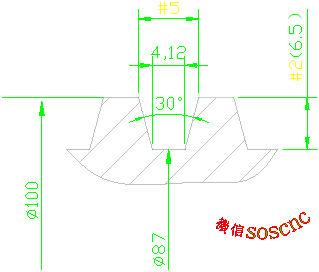
我任意设几个变量,如上图所示
#2代表牙高,也就是吃刀深度
#5代表牙总宽,也就是我们要加工出的螺纹牙型尺寸
#5= 4.12+2*TAN[15]*#2
因为刀具也有宽度,所以实际牙槽宽度应该是:
牙底宽+2 x斜坡宽-刀具宽。
所以最终#5= 4.12+2*TAN[15]*#2 -2 (需要把刀具宽度计算在内)
好了,分析到这儿里直接上程序
T0101
S300 M13
G0X100Z12. (快速移动到螺纹起始点)
#2=6.5(牙高的初始赋值)
WHILE[#2GT0]DO1 (如果牙高没车到0 ,说明还没到螺纹底径尺寸)
#2=#2-0.1 (吃刀量,每层车0.1,单边值)
IF[#2LE0] THEN#2=0
#3=87+2*#2 (既然#3的赋值为6.5,而且第一刀在螺纹大径处下刀,所以小径加上双边牙高才等于大径,当#2的值变化了,那就意味着大径也就变化了,从而实现分层切)
Z12. (Z12为定位基准,后面程序左右借刀的起点,都是以Z12为基准的)
G0X#3(X方向下刀)
G32Z-80.F12 (切螺纹)
G0X102 (退刀)
Z12. (退刀)
#5=4.12+2*TAN[15]*#2-2 (当前牙高所对应的牙宽,是后面两边借刀的依据)
#6=#5/2 (既然两边借刀#5除以2均分即可)
Z[12+#6] (先向右边借刀,由于要让刀具向右边移动,所以加上#6)
G0X#3
G32Z-80.F12
G0X102
Z12.
Z[12-#6] (先向左边借刀,由于要让刀具向左边移动,所以减上#6)
G0X#3
G32Z-80.F12
G0X102
Z12.
END1
G0X200.
Z200.
M30
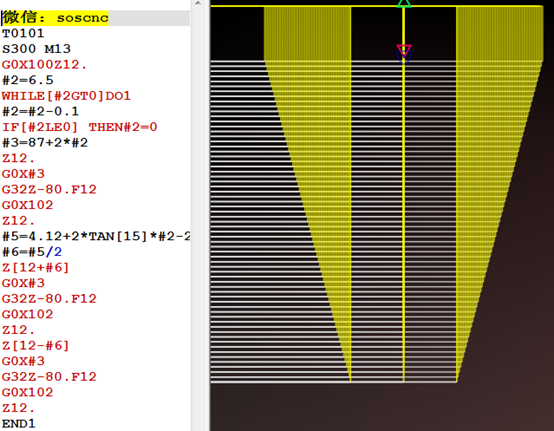