①精度要求:
尺寸精度:CNC加工能够实现很高的尺寸精度,通常可以达到±0.01mm或更小的公差要求。
形状精度:除了尺寸精度外,CNC加工还需要保证零件的形状精度,确保零件的各个部分符合设计要求。
位置精度:位置精度是指零件上各点之间的相对位置关系是否符合要求,这也是CNC加工的一个重要技术指标。
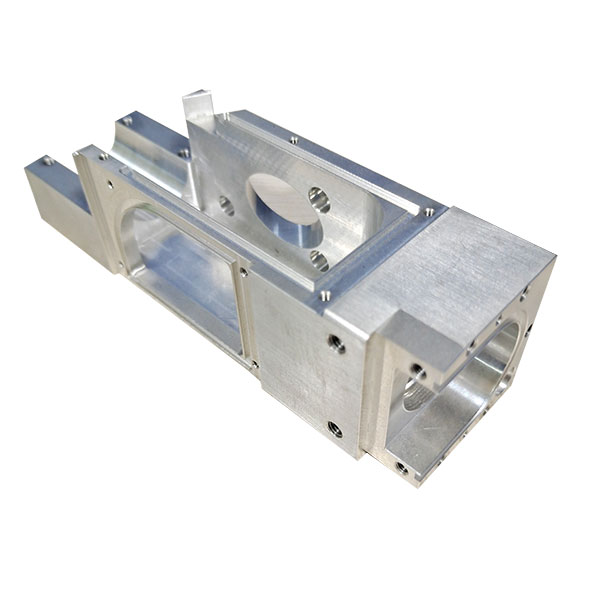
表面粗糙度:CNC加工应能够控制零件表面的粗糙度,以满足特定的要求。通常,表面粗糙度可以达到Ra 0.8μm或更小,有时甚至可以达到Ra 0.4μm以下,以确保零件表面的光洁度和质量。
表面光洁度:光洁度是零件表面的光滑程度,也是表面质量的一个重要指标。CNC加工可以通过选择合适的切削参数和冷却液来确保零件表面的光洁度。
③尺寸稳定性要求:
尺寸稳定性是零件长期使用的重要保障,它涉及到零件的热稳定性、机械稳定性等多个方面。CNC加工需要通过合理的工艺设计和加工过程控制来确保零件的尺寸稳定性。
熟练掌握数控机床的操作:
④操作人员需要熟练掌握数控机床的各项操作,包括开机、关机、手动操作、程序编辑、差错处理等,并了解CNC加工的基本原理和操作流程。
操作人员还需要掌握基本的数学知识,如三角函数、向量运算、坐标系等,以便进行相关数学计算和图像绘制。
⑤加工过程控制:
在CNC加工过程中,需要对加工过程进行严格的监控和控制,避免加工误差的产生。这包括选择合适的加工设备、刀具、切削参数等,以及对加工过程进行实时的监控和调整。
⑥数字化设计与编程:
CNC加工通常需要使用CAD(计算机辅助设计)软件进行工件的三维模型设计,并使用CAM(计算机辅助制造)软件进行加工路径规划和CNC程序编制。操作人员需要熟练掌握这些软件的使用,并能够根据设计要求编制出高质量的CNC程序。
⑦质量控制与检测:
在CNC加工过程中,需要对加工质量进行严格的控制和检测。这包括使用各种测量工具和设备对加工后的零件进行尺寸、形状、位置精度等方面的检测,以确保加工质量符合设计要求。