Zpracování plechu je komplexní proces obrábění za studena pro plechy (obvykle pod 6mm), včetně střihu, děrování, ohýbání, svařování, nýtování, tvarování forem a povrchové úpravy. Jeho výrazným rysem je, že tloušťka stejné části je konzistentní.
Metoda zpracování plechu: Nezpracování forem: Proces zpracování plechu prostřednictvím zařízení, jako je numerické děrování, laserové řezání, střihací stroje, ohýbací stroje, nýtovací stroje atd. Obvykle se používá pro výrobu vzorků nebo malých sérií, s vysokými náklady. Krátký cyklus zpracování a rychlá reakce. Zpracování forem: Používání pevných forem pro zpracování plechu jsou obecně řezné formy a tvářecí formy, které se používají hlavně pro hromadnou výrobu s nižšími náklady. Počáteční náklady na formu jsou vysoké a kvalita dílů je zaručena. Časný cyklus zpracování je dlouhý a náklady na formu jsou vysoké. Proces zpracování plechu: řezání: numerické děrování, laserové řezání, střihací stroj
Tváření ohýbání, protahování, děrování: ohýbací stroje, děrovací stroje atd
Ostatní zpracování: nýtování, závitování atd
Svařování: metoda připojení plechu
Povrchová úprava: práškové stříkání, galvanické pokovování, kreslení drátu, sítotisk atd
Technologie zpracování plechu Hlavní metody řezání plechu zahrnují numerické děrování, laserové řezání, střihací stroje a řezání forem. CNC je v současné době běžně používaná metoda a laserové řezání se používá většinou ve fázi vzorků (nebo může také zpracovat nerezové plechové díly), s vysokými náklady na zpracování. Řezání forem se používá většinou pro velké zpracování.
Níže představíme hlavně řezání plechů pomocí numerického děrování
Numerické děrování, také známé jako CNC děrovací stroj věže, lze použít pro řezání, děrování, protahování otvorů, válcovací žebra, děrovací rolety atd. Jeho přesnost obrábění může dosáhnout+/-0.1mm.
Tloušťka CNC obráběcího plechu je:
Plechy válcované za studena a za tepla 4,0mm
Hliníková deska 5.0mm
Nerezová ocelová deska 2.0mm
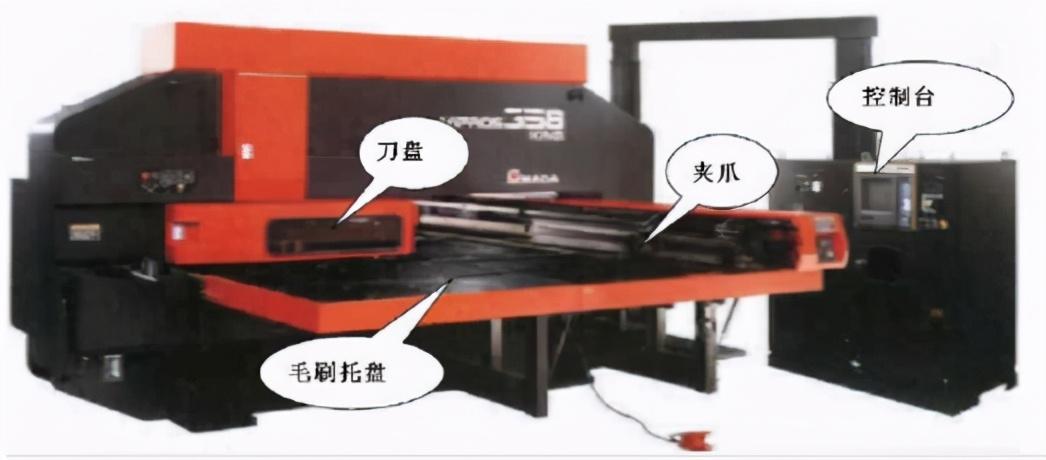
Pro děrování je požadavek na minimální velikost. Minimální velikost děrování souvisí s tvarem otvoru, mechanickými vlastnostmi materiálu a tloušťkou materiálu. (Jak je uvedeno na obrázku níže) 000 @ 000
2. Vzdálenost a vzdálenost hran děrovacích otvorů. Pokud minimální vzdálenost mezi děrovací hranou dílu a vnějším okrajem dílu není rovnoběžná s vnějším okrajem dílu, minimální vzdálenost by neměla být menší než tloušťka materiálu t; Pokud je paralelní, neměla by být menší než 1.5t. (Jak je uvedeno na obrázku níže)
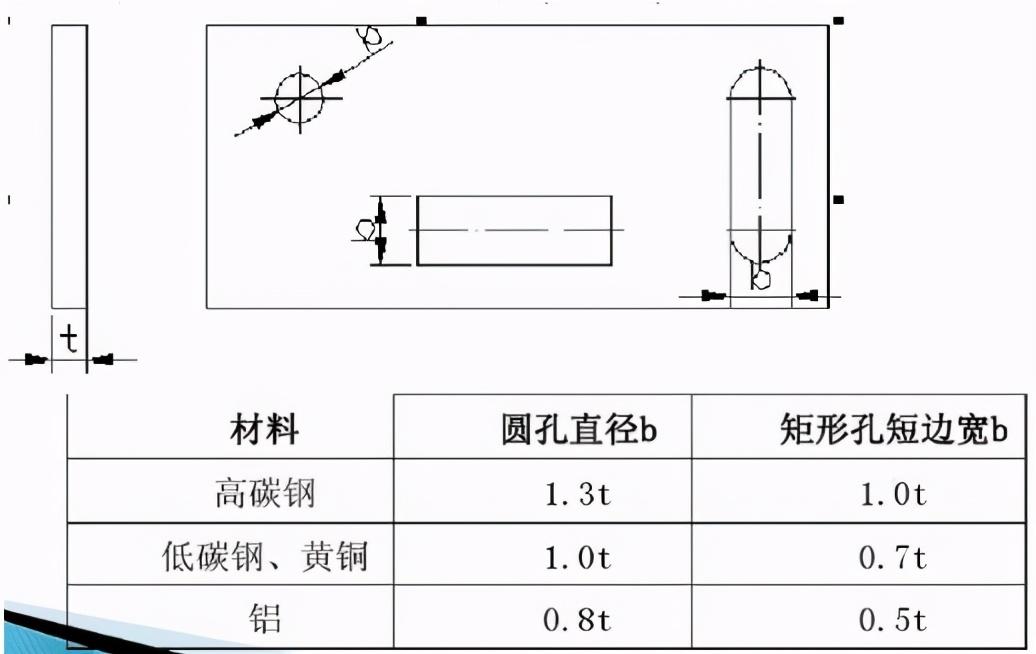
3. Při protahování otvorů je minimální vzdálenost mezi protahovacím otvorem a hranou 3T, minimální vzdálenost mezi dvěma protahovacími otvory je 6T a minimální bezpečná vzdálenost mezi protahovacím otvorem a ohýbací hranou (uvnitř) je 3T+R (T je tloušťka plechu, R je ohýbací filet)
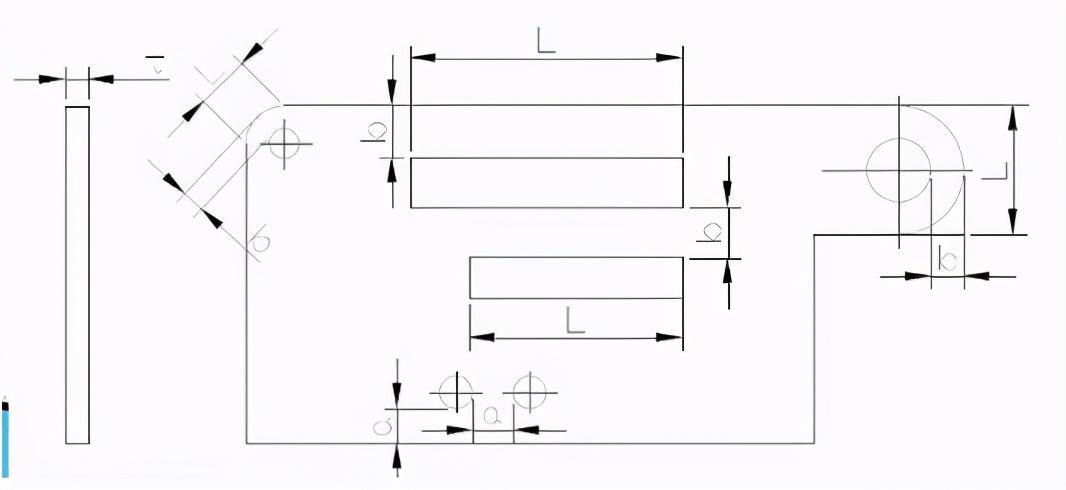
4. Při děrování otvorů v natažených a ohýbaných částech a hluboko tažených částech by měla být zachována určitá vzdálenost mezi stěnou otvoru a rovnou stěnou. (Jak je uvedeno na obrázku níže)
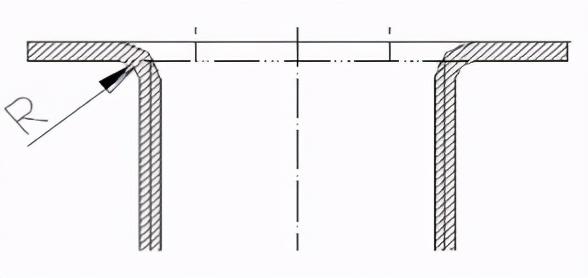
Technologie zpracování plechu: Tváření plechu zahrnuje hlavně ohýbání a natahování plechu.
1. Ohýbání plechu 1.1 Ohýbání plechu používá hlavně ohýbací stroje.
přesnost obrábění skládacího stroje;
Jeden záhyb:+/-0,1mm
Poloviční složení:+/-0.2mm
Více než 20% sleva:+/-0,3mm
Základním principem sekvence zpracování ohýbání je ohýbání zevnitř naruby a z malého na velké. Speciální tvary by měly být nejprve ohýbány a předchozí proces by neměl ovlivňovat nebo zasahovat do následných procesů po tváření.
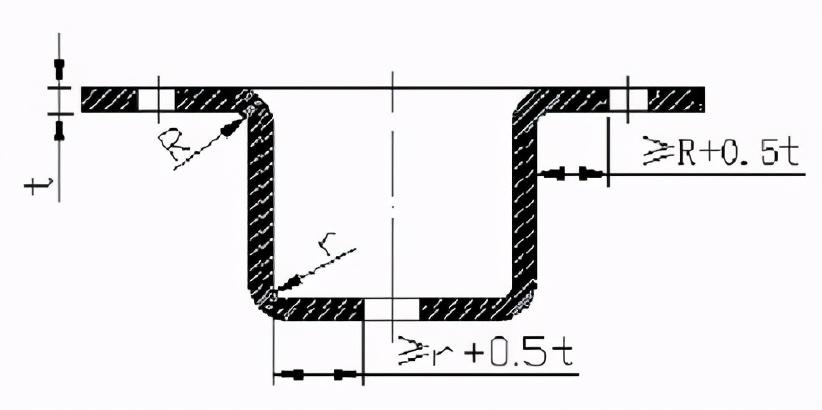
1.3 Běžné tvary ohýbacích nožů:
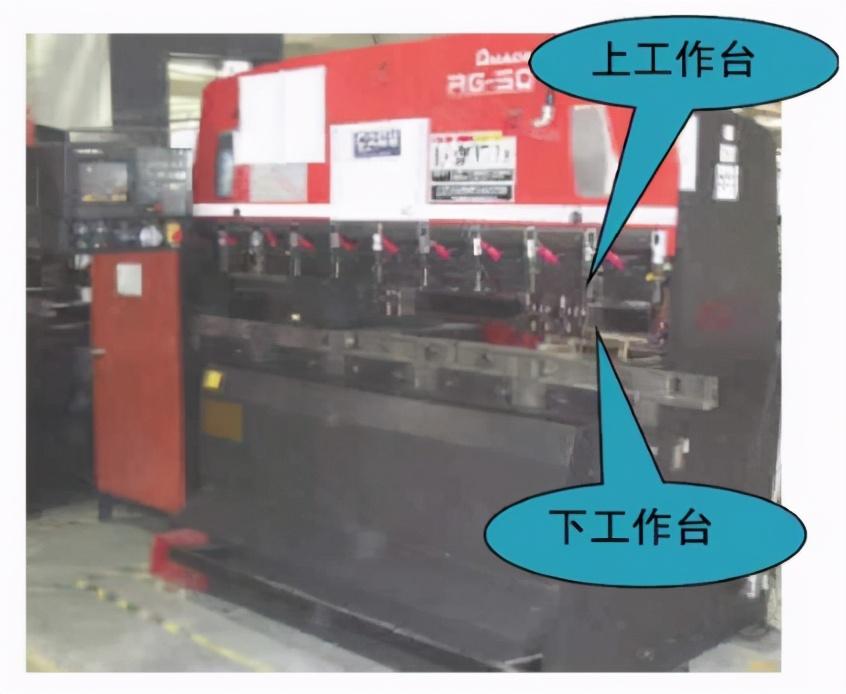
Běžné tvary V-drážky:
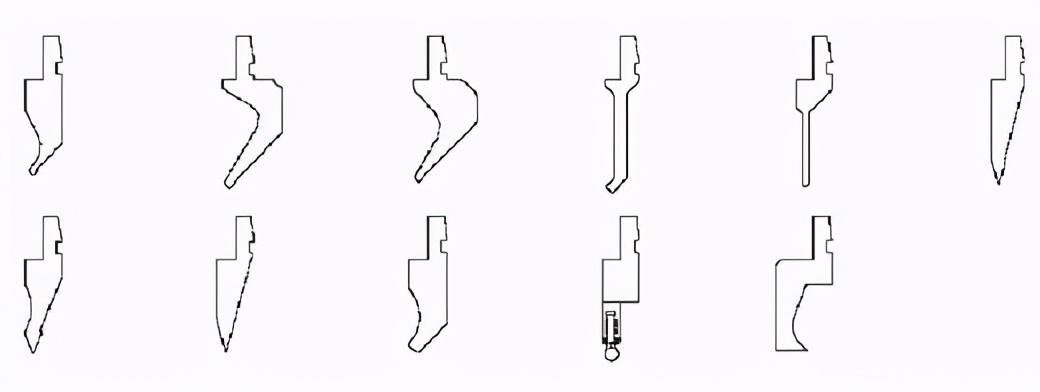
1.4 Minimální poloměr ohybu ohýbaných dílů:
Při ohýbání materiálu se vnější vrstva natahuje a vnitřní vrstva je stlačena v oblasti zaoblené. Pokud je tloušťka materiálu konstantní, čím menší je vnitřní r, tím silnější je napětí a stlačení materiálu; Když tahové napětí vnějšího zaobleného rohu překročí konečnou pevnost materiálu, dojde k trhlinám a zlomeninám. Konstrukční návrh ohýbaných dílů by proto měl zabránit příliš malým ohybovým zaobleným poloměrům rohu. Minimální poloměr ohybu běžně používaných materiálů ve společnosti je uveden v tabulce níže.
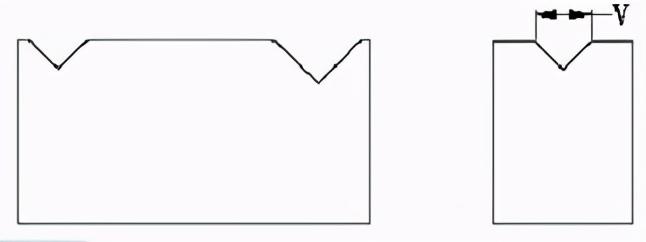
Tabulka minimálního poloměru ohybu ohýbaných dílů:
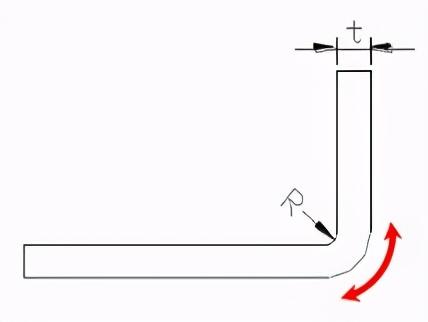
Poloměr ohybu odkazuje na vnitřní poloměr ohýbané části a t je tloušťka stěny materiálu.
Výška rovné hrany ohýbané části je 1,5:
Obecně platí, že minimální výška rovné hrany by neměla být příliš malá a minimální požadavek na výšku je: h>2t
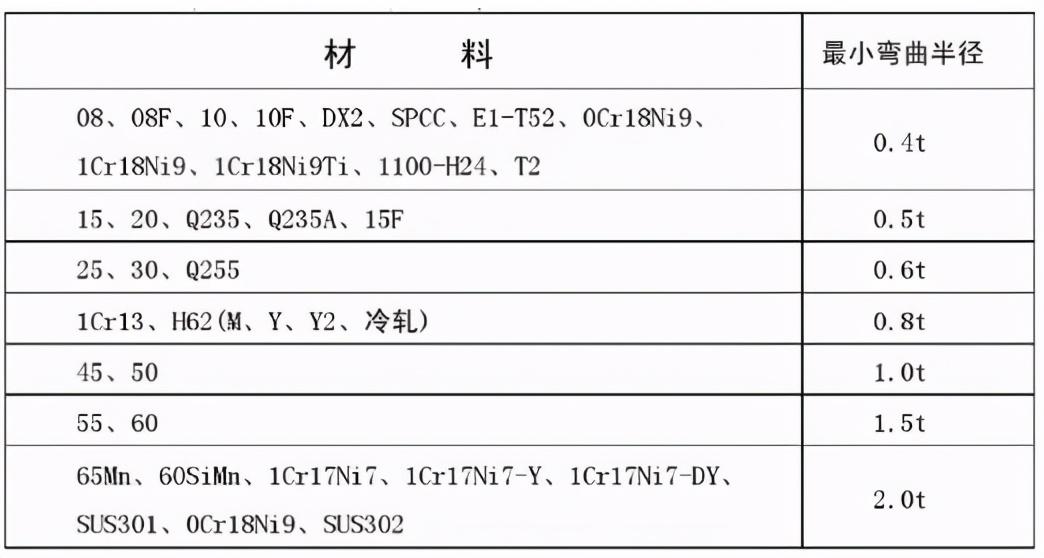
Pokud je požadována rovná výška hrany h2t ohýbané části, nejprve zvyšte výšku ohýbací hrany a poté ji zpracujte na požadovanou velikost po ohýbání; Nebo po zpracování mělkých drážek v oblasti deformace ohybu proveďte ohýbání.
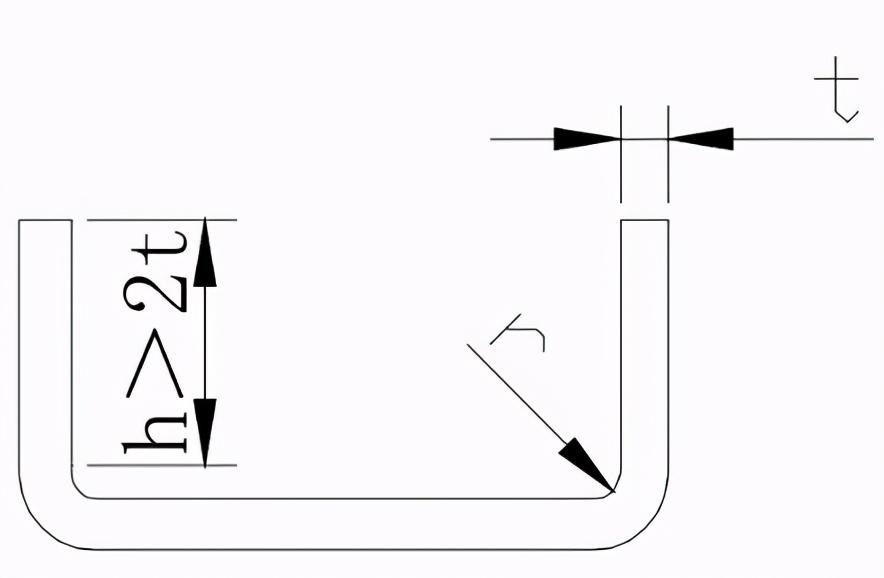
1.6 Minimální výška ohybu rovné hrany s šikmým úhlem na zakřivené hraně:
Při ohybu zakřivené části se šikmou hranou je minimální výška boku: h=(2-4) t> 3mm
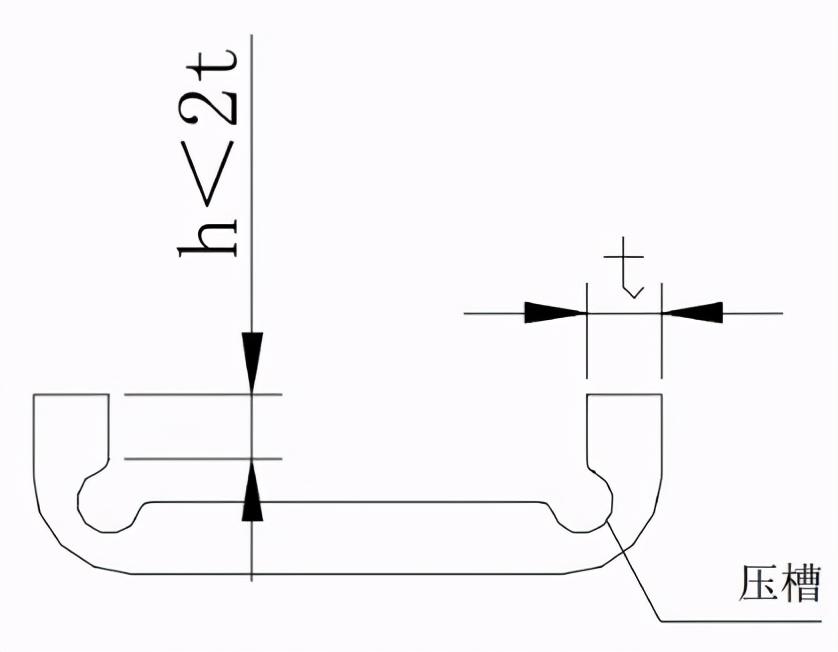
1.7 Okrajová vzdálenost otvorů na ohýbaných dílech:
Vzdálenost hrany otvoru: Nejprve dělejte otvor a poté ho ohýbejte.Poloha otvoru by měla být mimo deformační zónu ohýbání, aby se zabránilo deformaci otvoru během ohýbání. Vzdálenost od stěny otvoru k zakřivenému okraji je uvedena v tabulce níže.
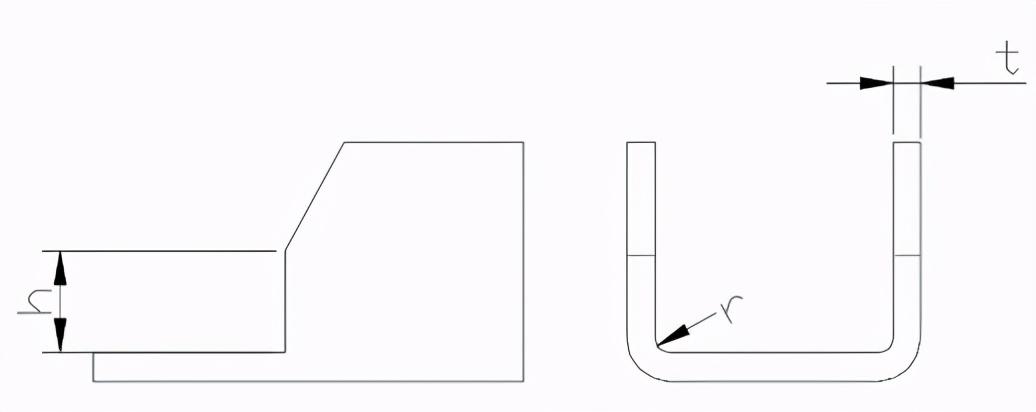
1.8 Procesní řez pro lokální ohýbání:
Ohýbací linka ohýbací části by se měla vyhnout náhlým změnám velikosti. Při ohýbání určitého segmentu hrany lokálně, aby se zabránilo koncentraci napětí a trhlinám v ostrých rozích, může být ohýbání křivky posunuta na určitou vzdálenost, aby zanechala náhlou změnu velikosti (obrázek a), nebo může být otevřena procesní drážka (obrázek b) nebo může být děrována procesní otvor (obrázek c). Věnujte pozornost požadavkům na velikost v diagramu: SR; šířka štěrbiny kt; Hloubka drážky Lt+R+k/2.
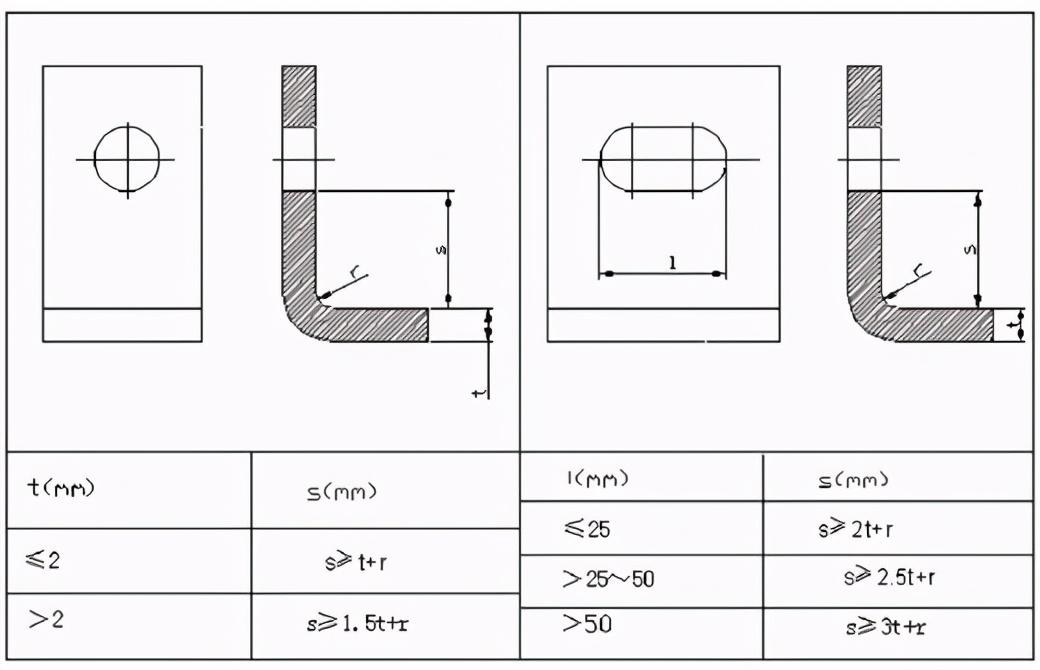
1.9 Ohybové hrany se zkosenými hranami by měly zabránit deformačním zónám:
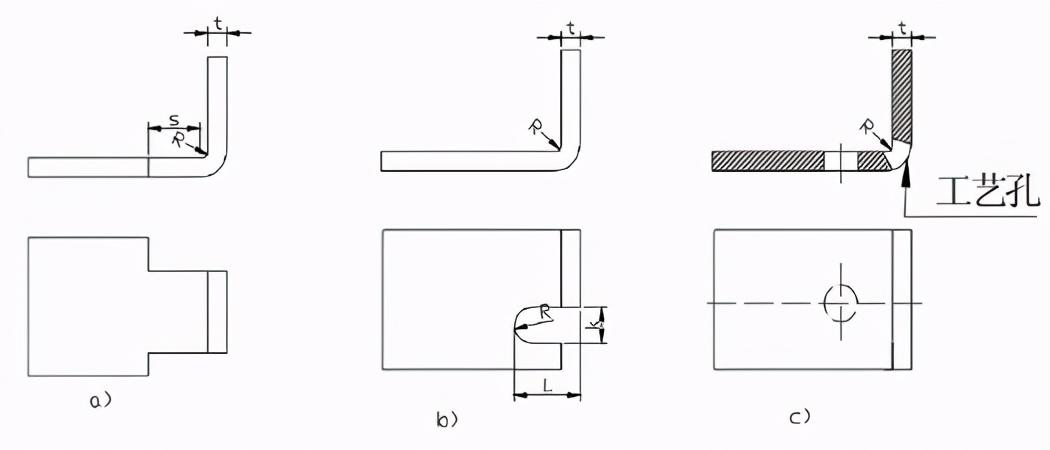
1.10 Návrhové požadavky na záhyby plechu (mrtvé hrany):
Délka mrtvého okraje záhybů plechu souvisí s tloušťkou materiálu. Jak je uvedeno na následujícím obrázku, minimální délka mrtvé hrany je obecně L3,5t+R.
Mezi nimi je t tloušťka stěny materiálu a R je minimální vnitřní poloměr ohybu předchozího procesu (jak je znázorněno vpravo na obrázku níže) před usmrcením hrany.
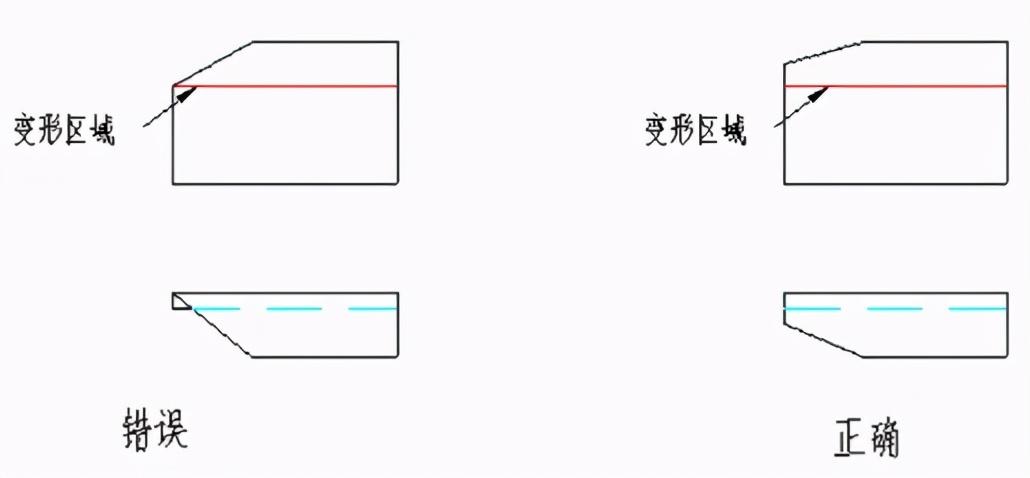
1.11 Přidány otvory pro polohování procesu:
Aby bylo zajištěno přesné umístění polohy polotovaru ve formě a zabránilo odchylce polotovaru během ohýbání, měly by být předem přidány otvory pro polohování procesu během návrhu, jak je znázorněno na následujícím obrázku. Zvláště u dílů, které byly několikrát ohýbané, musí být procesní otvory použity jako referenční polohovací reference, aby se snížilo kumulativní chyby a zajistilo kvalitu výrobku.

Při označování rozměrů ohýbaných dílů je třeba vzít v úvahu zpracovatelnost:
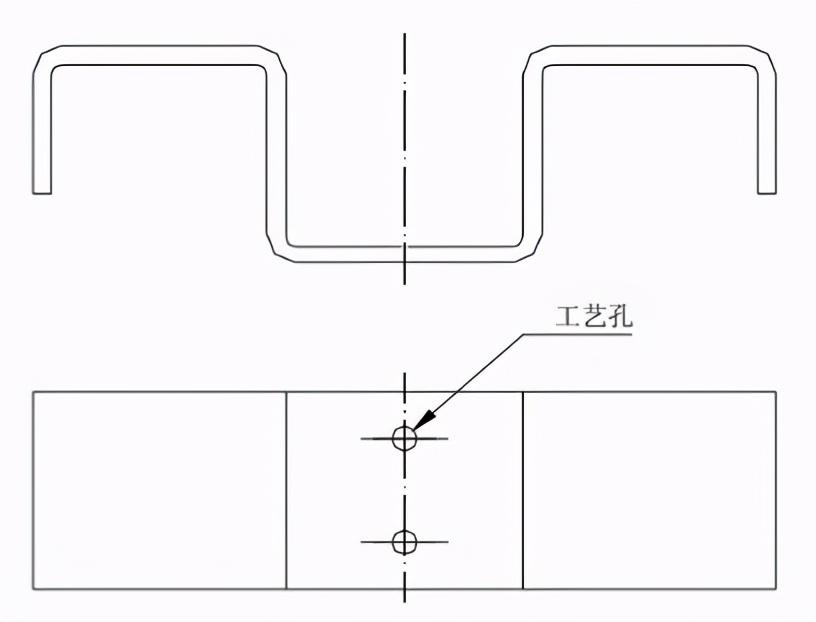
Jak je znázorněno na výše uvedeném obrázku, a) nejprve děrování a poté ohýbání, přesnost rozměrů L je snadno zajistitelná a zpracování je pohodlné. b) Pokud je požadavek na přesnost rozměru L vysoký, je nutné nejprve ohýbat a pak zpracovat otvor, který je obtížný zpracovat.
Existuje mnoho faktorů, které ovlivňují odpružení ohýbaných dílů, včetně mechanických vlastností materiálu, tloušťky stěny, poloměru ohybu a kladného tlaku během ohýbání. Čím větší je poměr vnitřního poloměru ohýbané části k tloušťce desky, tím větší je odraz. Metodě potlačení odrazu z pohledu návrhu, jako je odraz ohýbaných dílů, se v současné době především výrobci při návrhu forem vyhýbají přijetím určitých opatření. Zlepšení určitých konstrukcí v konstrukci může současně snížit úhel odpružení, jak je znázorněno na následujícím obrázku: lisování výztužných žeber v oblasti ohýbání může nejen zvýšit tuhost obrobku, ale také pomoci potlačit odpružení.
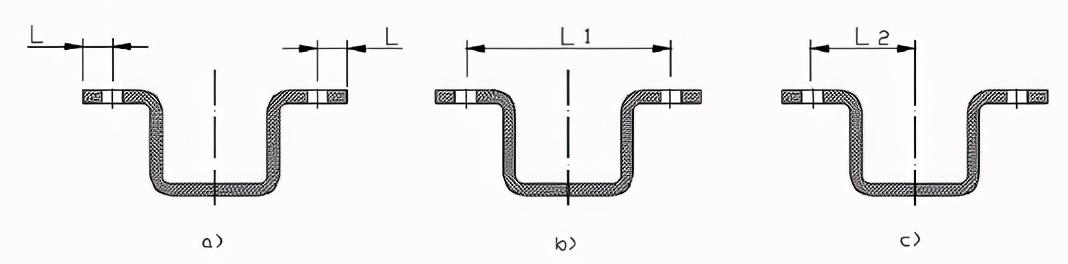
2. Protahování plechu je dokončeno hlavně CNC nebo konvenčním děrováním, které vyžaduje různé protahovací děrovací děrovací formy nebo formy.
Tvar natažené části by měl být co nejjednodušší a symetrický a měl by být co nejvíce tvořen v jednom úseku.
Části, které vyžadují více roztahů, by měly během procesu natahování umožnit možné povrchové značky.
Za předpokladu zajištění montážních požadavků by mělo být umožněno protahovat boční stěny s určitým sklonem.
2.1 Požadavky na poloměr filetu mezi spodní částí natažené části a rovnou stěnou:
Jak je uvedeno na obrázku níže, poloměr filetu mezi spodní částí natažené části a rovnou stěnou by měl být větší než tloušťka desky, tj. r1t. Aby byl proces natahování hladší, je obecně brán r1=(3-5) t a maximální poloměr filetu by měl být menší nebo rovný 8-krát tloušťky desky, což je r18t.
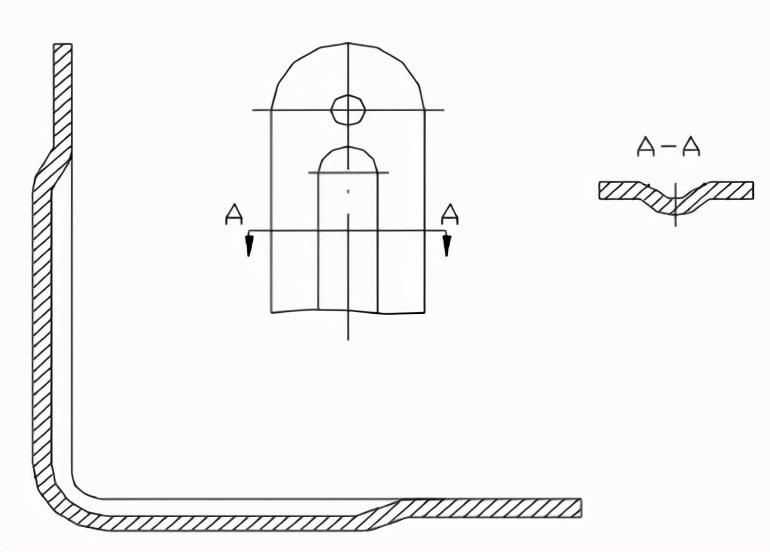
2.2 Poloměr zaoblení mezi přírubou a stěnou natažené části
Poloměr filetu mezi přírubou a stěnou natažené části by měl být větší než dvojnásobek tloušťky desky, tj. r22t. Aby byl proces natahování hladší, je obecně přijat r2=(5-10) t a maximální poloměr příruby by měl být menší nebo rovný 8-krát tloušťky desky, tj. r28t. (Viz výše uvedený obrázek)
2.3 Průměr vnitřní dutiny kruhových natažených částí
Vnitřní průměr kruhového protahovacího kusu by měl být brán jako D d+10t, takže tlaková deska je při protahování pevně stlačena bez vrásek. (Viz výše uvedený obrázek)
2.4 Zaoblený poloměr mezi sousedními stěnami obdélníkových natažených částí
Poloměr filetu mezi sousedními stěnami obdélníkového nataženého kusu by měl být brán jako r3 3t. Pro snížení počtu protažení je třeba brát r3 H/5 co nejvíce, aby bylo možné ji vytáhnout najednou.
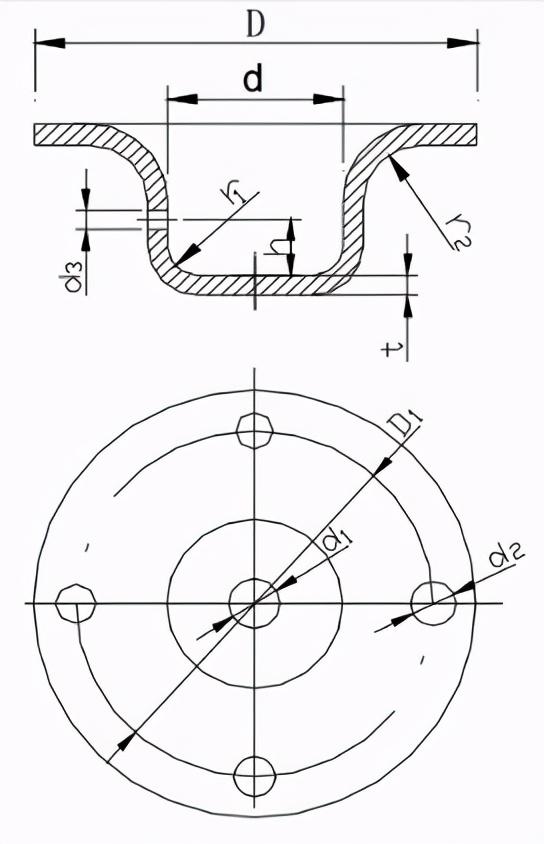
Požadavky na rozměrový vztah mezi výškou a průměrem 2,5 kulatého bezpřírubového natahovacího dílu při jednorázovém tváření
Při vytváření kruhové příruby bez natahovací části v jednom tahu by poměr výšky H k průměru d měl být menší nebo rovný 0,4, tj. H/d 0,4, jak je znázorněno na následujícím obrázku.
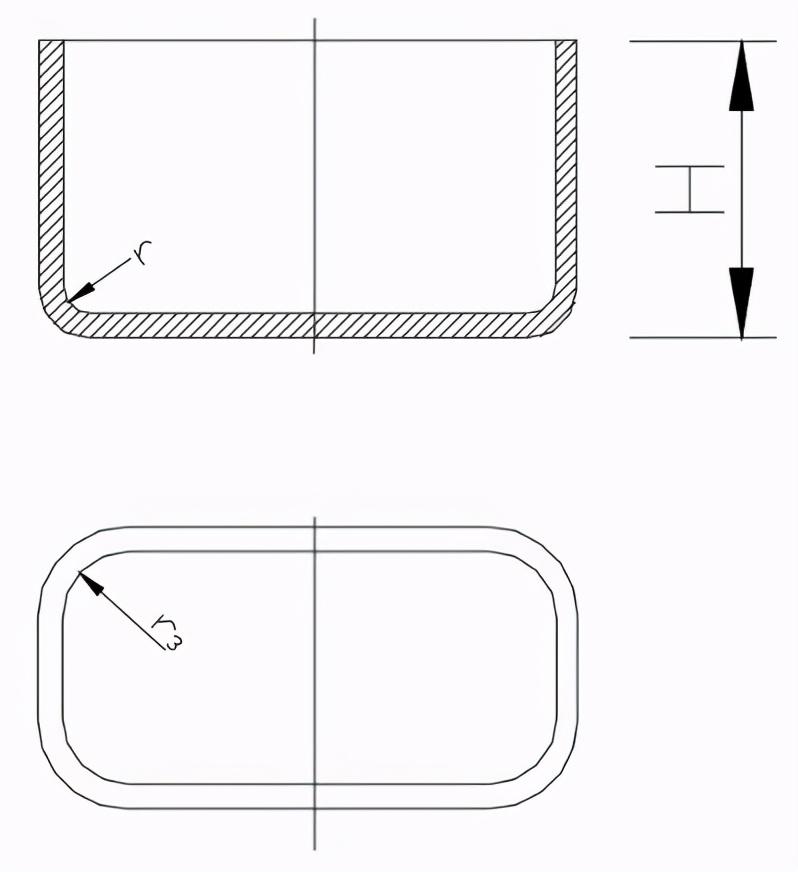
2.6 Variace tloušťky nataženého materiálu:
Tloušťka nataženého materiálu se mění v důsledku různých úrovní napětí působených na každou část. Obecně řečeno, původní tloušťka je zachována ve středu spodní části, materiál ve zaoblených rozích spodní části se stává tenčí, materiál v blízkosti příruby nahoře se stává silnější a materiál kolem zaoblených rohů obdélníkové natažené části se stává silnější.
2.7 Způsob značení rozměrů výrobku natažených dílů
Při navrhování strečových výrobků by měly být rozměry na výkresu výrobku jasně uvedeny, aby bylo zajištěno zaručení vnějších i vnitřních rozměrů a vnitřních a vnějších rozměrů nelze označit současně.
2.8 Metoda pro anotaci rozměrových tolerancí natažených částí
Vnitřní poloměr konkávního konvexního oblouku natažené části a tolerance výškových rozměrů válcové natažené části tvořené v jednom tahu jsou oboustranné symetrické odchylky, s hodnotou odchylky poloviny absolutní hodnoty přesnosti tolerance národní normy (GB) úrovně 16 a jsou číslovány.
3. Jiné tváření plechu: Výztužná žebra:Lisování žeber na plochých kovových dílech pomáhá zvýšit strukturální tuhost.
Žaluzie: Žaluzie se běžně používají na různých krytech nebo krytech pro zajištění ventilace a odvodu tepla.
Otvorová příruba (protahovací otvor používaný k obrábění závitů nebo zvýšení tuhosti otvoru.
3.1 Posílení:
Konstrukce výztuže a výběr velikosti
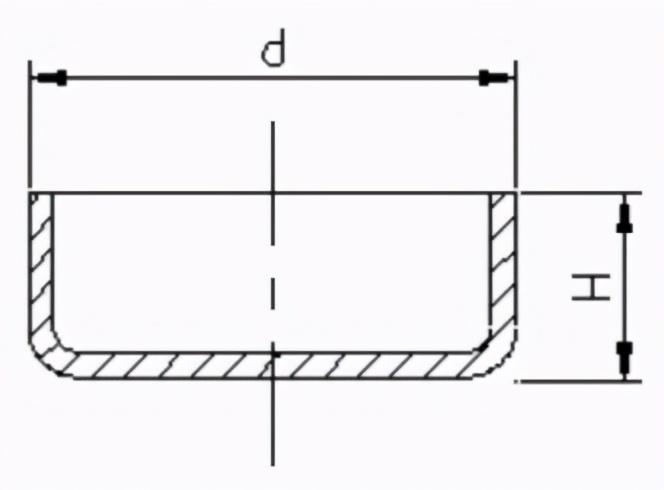
Maximální rozměry pro konvexní vzdálenost a vzdálenost konvexních hran jsou vybrány podle tabulky níže.
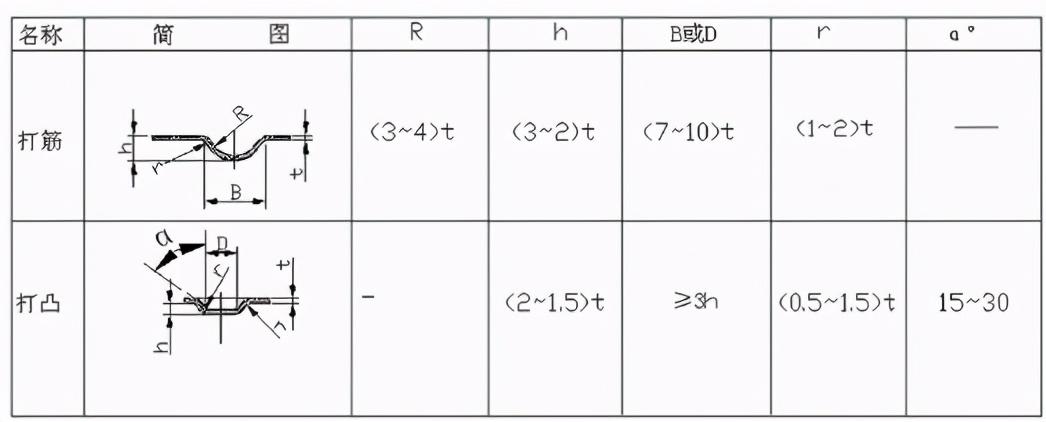
3.2 Žaluzie
Metoda tvarování žaluzie spočívá v otevření materiálu pomocí jedné hrany konvexní formy, zatímco zbývající části konvexní formy současně natahují a deformují materiál, vytvářejí zvlněný tvar s jedním bočním otvorem.
Typická struktura žaluzie je zobrazena na následujícím obrázku
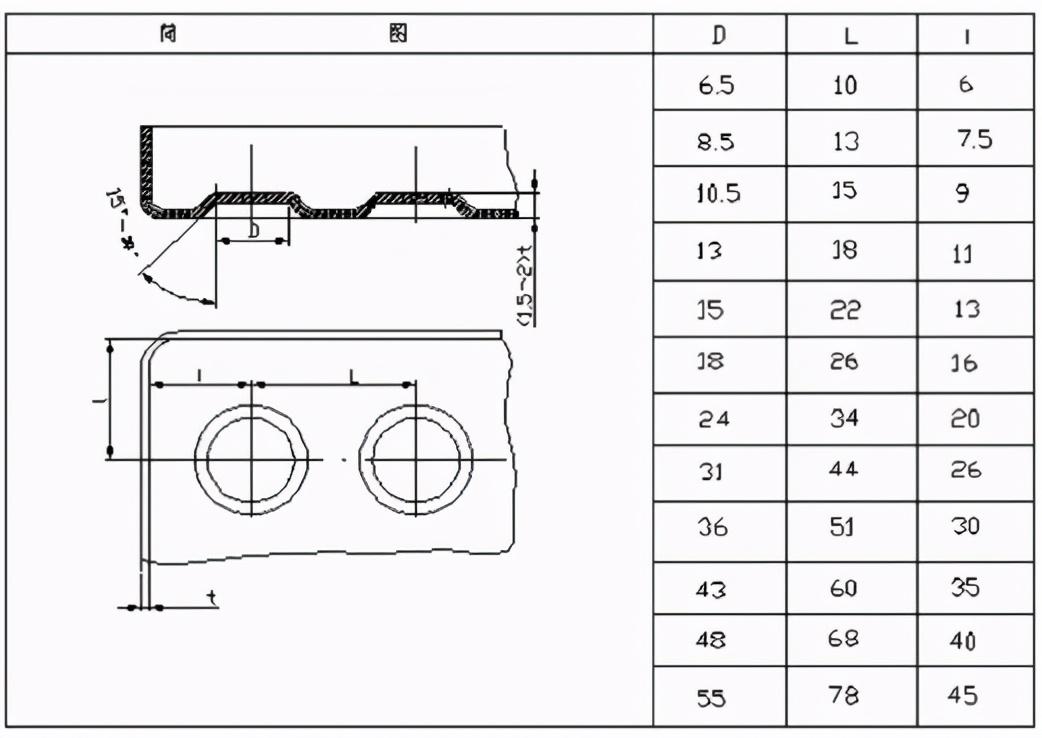
Požadavek na velikost žaluzie: a4t; b6t;h5t;L24t;r0.5t。
3.3 Příruby otvorů (protahovací otvory)
Existuje mnoho forem příruby otvorů a běžnou je obrábět přírubu vnitřního otvoru závitů.
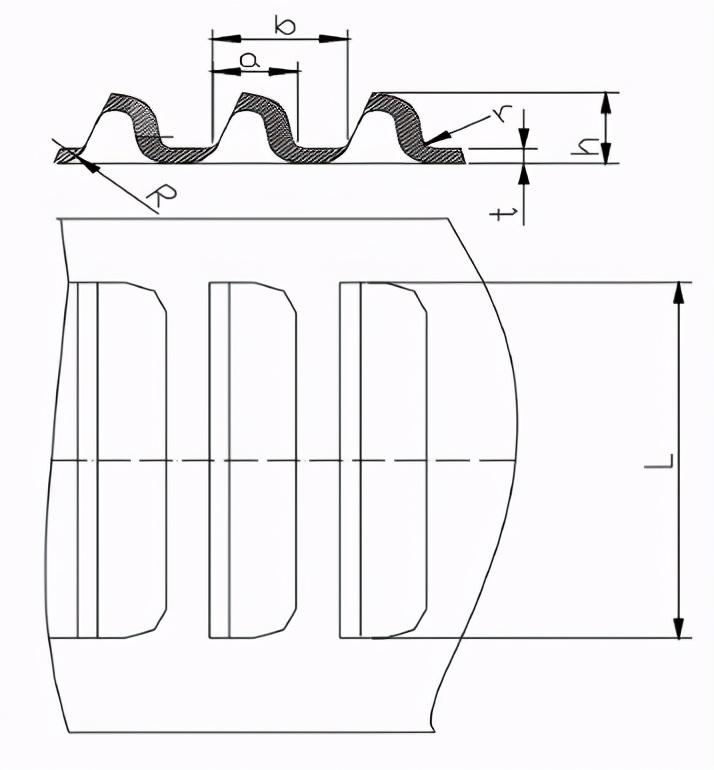
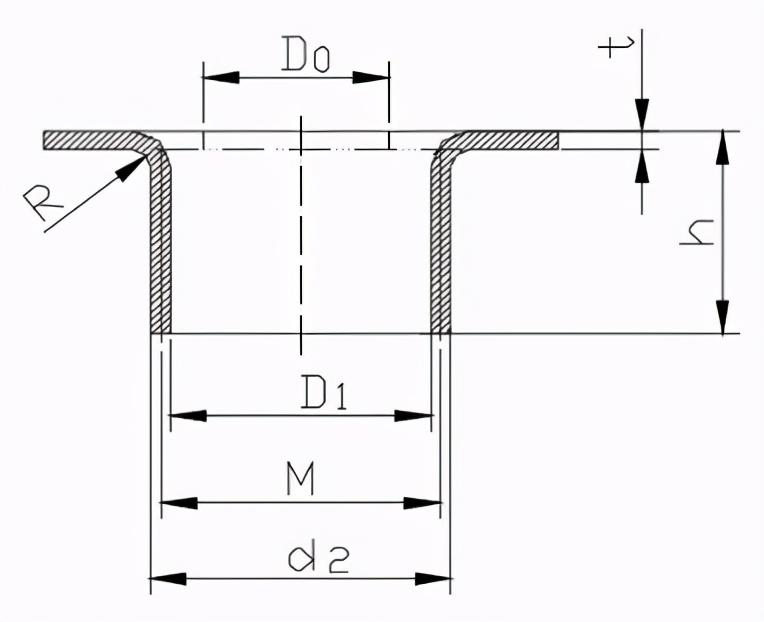
Technologie zpracování plechu umožňuje nýtování dalších zpracovaných plechových příslušenství, jako jsou nýtovací matice, nýtovací šrouby, vodicí sloupy nýtů atd.
2. Zlepování závitových otvorů na plech.
tloušťka plechu t< V 1.5 hodinu použijte otočený okraj klepání. Pokud je tloušťka plechu t1.5, lze použít přímé závitové řezání.
Technologie zpracování plechů Při svařování v návrhu konstrukcí svařování plechů by měla být implementována tak, aby "symetricky uspořádala svary a svařovací body a zabránilo průniku, agregaci a překrývání.Sekundární svary a svařovací body mohou být přerušeny a hlavní svary a svařovací body by měly být propojeny."
Svařování běžně používané v plechu zahrnuje obloukové svařování, odporové svařování atd.
Mezi obloukovým svařovaným plechem by měl být dostatečný svařovací prostor a maximální svařovací mezera by měla být mezi 0,5 a 0,8mm. Svařovací šv by měl být rovnoměrný a plochý.
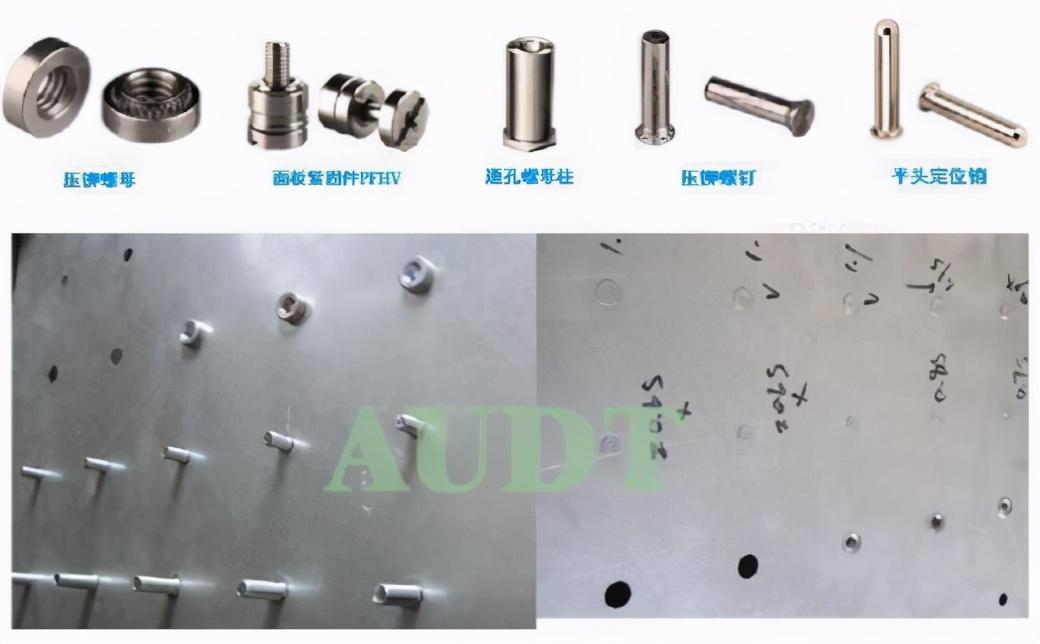
2. Svařovací povrch odporového svařování by měl být plochý, bez vrásek, odrazu atd.
Rozměry odporového svařování jsou uvedeny v tabulce níže:
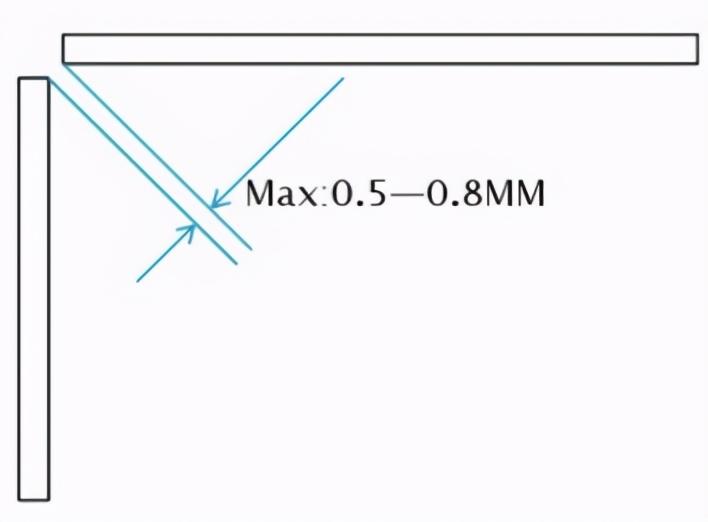
Vzdálenost mezi odporovými pájecími spoji
V praktických aplikacích, při svařování malých dílů, lze odkazovat na údaje v níže uvedené tabulce.
Při svařování velkých dílů může být vzdálenost mezi body vhodně zvětšena, obecně ne menší než 40-50mm. U nepřetížených dílů lze vzdálenost mezi svařovacími body zvětšit na 70-80mm.
Tloušťka desky t, průměr pájecího spoje d, minimální průměr pájecího spoje dmin a minimální vzdálenost e mezi pájecími spoji. Pokud je deska kombinací různých tloušťek, vyberte podle nejtenčí desky.
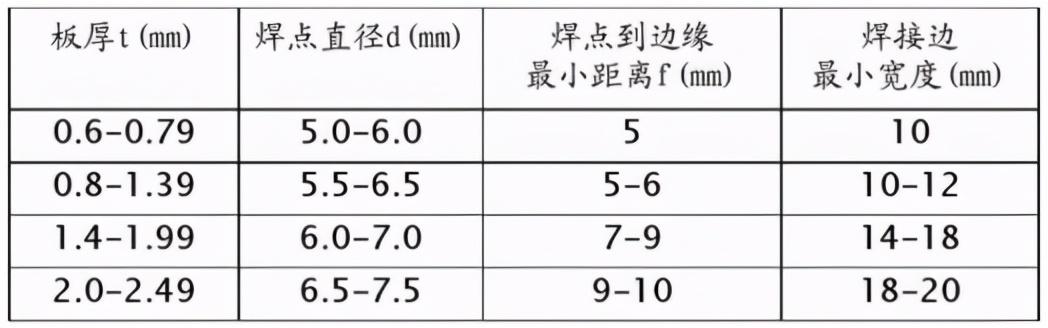
Počet vrstev a poměr tloušťky materiálu odporového svařování plechu
Plech pro odporové bodové svařování je obecně 2-vrstvý, s maximálně 3-vrstvy. tloušťkový poměr každé vrstvy svařovaného spoje by měl být mezi 1/3 a 3.
Pokud je nutné svařovat třívrstvou desku, je třeba nejprve zkontrolovat poměr tloušťky materiálu. Pokud je to rozumné, může být provedeno svařování. Pokud to není přiměřené, měly by být zváženy procesní otvory nebo procesní zářezy. Pro dvouvrstvé svařování by měly být body svařovány stupňovány.
Technologie zpracování plechu. Metody připojení: To především zavádí metody připojení plechu během zpracování, včetně nýtování nýtů, svařování (jak je uvedeno výše), nýtování otvorů a TOX nýtování.
Nýtování nýtů: Tento typ nýtu je běžně označován jako tažný nýt, který zahrnuje nýtování dvou kusů plechu dohromady tažným nýtem. Běžné nýtovací tvary jsou zobrazeny na obrázku:
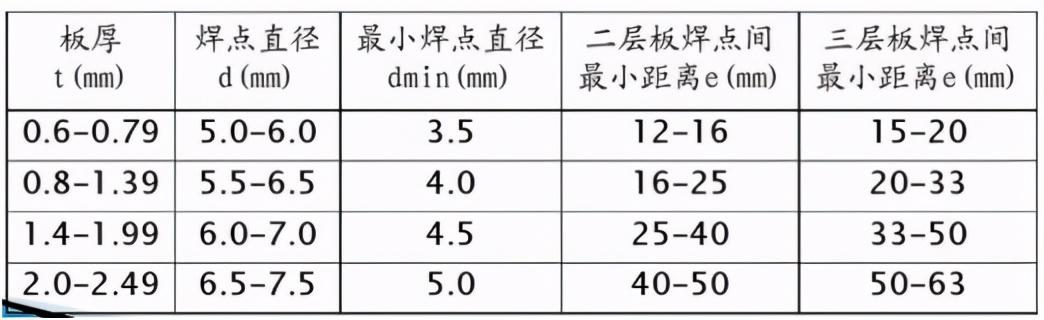
2. Svařování (jak bylo zmíněno výše) 3. Kreslení a nýtování: Jedna část je tažný dír a druhá část je zapuštěný otvor, který je vyroben do neoddělitelného spojovacího těla prostřednictvím nýtování.
Nadřazenost: Odsávací otvor a jeho odpovídající potápěcí otvor mají polohovací funkci. Pevnost nýtování je vysoká a účinnost nýtování formami je také relativně vysoká.
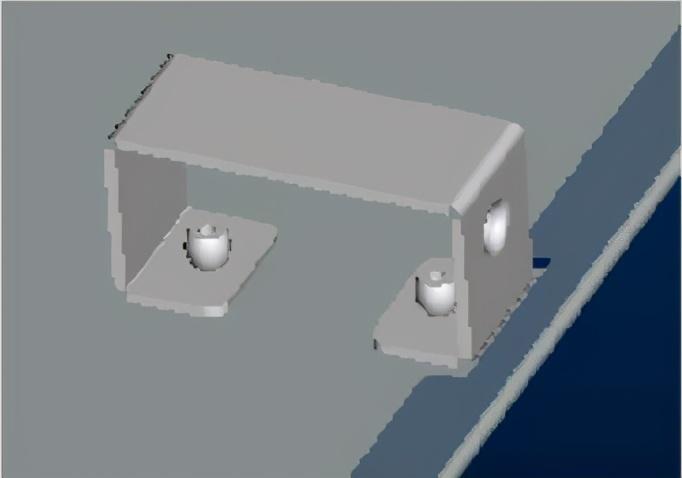
4. TOX nýtování: Zatlačte připojenou část do konkávní formy prostřednictvím jednoduché konvexní formy. Pod dalším tlakem materiál uvnitř konkávní formy proudí ven. Výsledkem je kruhový spojovací bod bez hran nebo otřepů, což neovlivňuje jeho odolnost proti korozi. Dokonce i u desek s nátěrem nebo stříkací vrstvou barvy na povrchu lze zachovat původní charakteristiky odolnosti proti korozi a korozi, protože nátěr a laková vrstva mohou také zachovat původní charakteristiky odolnosti proti korozi a korozi, protože nátěr a laková vrstva se deformují a proudí dohromady. Materiál se stlačuje směrem k obou stranám a do desky vedle konkávní formy a tvoří tak spojovací body TOX. Jak je uvedeno na následujícím obrázku:
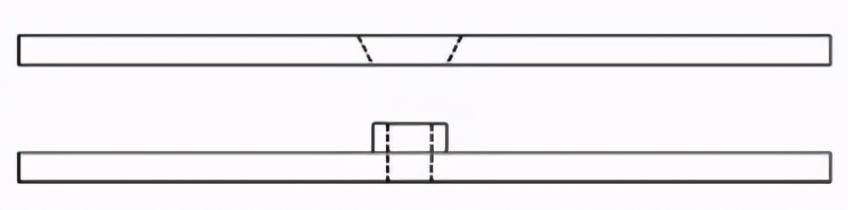
Povrchová úprava může poskytnout antikorozní ochranu a dekorativní účinky na povrchu plechu. Mezi běžné povrchové úpravy plechů patří práškové postřikování, galvanizování, žárové zinkování, oxidace povrchu, povrchové kreslení, sítotisk atd.
Před povrchovou úpravou plechu by měly být z povrchu plechu odstraněny olejové skvrny, rez, svařovací struska atd.
Práškové postřikování: Existují dva typy povrchového postřikování plechu: tekutá a prášková barva. Běžně používaná je prášková barva. Stříkáním prášku, elektrostatickou adsorpcí, vysokoteplotním pečením a dalšími metodami se na povrch plechu postříká vrstva různých barev barvy, která zkrášlí vzhled a zvýší antikorozní výkon materiálu. Jedná se o běžně používanou metodu povrchové úpravy.
Poznámka: V barvách stříkaných různými výrobci může být určitý barevný rozdíl, takže plech stejné barvy na stejném zařízení by měl být co nejvíce postříkán od stejného výrobce.
2. Povrchové zinkování pozinkovaného a žárově pozinkovaného plechu je běžně používaná metoda povrchového antikorozního ošetření a může hrát určitou roli při zkrášlení vzhledu. Galvanizaci lze rozdělit na galvanizaci a žárové zinkování.
Vzhled galvanizace je relativně jasný a plochý, s tenkou pozinkovanou vrstvou, která se běžně používá.
Žárový zinkový nátěr je silnější a může vytvořit vrstvu ze slitiny železa zinku, která má silnější odolnost proti korozi než elektrozinkování.
3. Povrchová oxidace: To především zavádí povrchovou anodizaci hliníku a hliníkových slitin.
Povrchové eloxování hliníku a hliníkových slitin může být oxidováno do různých barev, což poskytuje jak ochranné, tak dekorativní efekty. Současně může být na povrchu materiálu vytvořen anodický oxidový film, který má vysokou tvrdost a odolnost proti opotřebení, stejně jako dobré elektrické izolační a tepelně izolační vlastnosti.
4. Povrchové tažení drátu: Umístěte materiál mezi horní a dolní válečky stroje na tažení drátu, s pískovým pásem připojeným k válcům. Poháněný motorem, materiál prochází horními a dolními pískovými pásy, zanechává stopy na povrchu materiálu. Tloušťka značek se liší v závislosti na typu pískového pásu a jejich hlavní funkcí je zkrášlit vzhled. Metoda povrchové úpravy tažení drátu se obecně uvažuje u hliníkových materiálů.
5. Sítotisk je proces tisku různých značení na povrch materiálů. Obecně existují dvě metody: plochý sítotisk a transferový tisk. Plochý sítotisk se používá hlavně na obecných plochých povrchách, ale pokud existují hlubší jámy, je nutný transferový tisk.
Hedvábný sítotisk vyžaduje hedvábnou formu.
Referenční příslušenství pro přesnost zpracování plechu:
GBT13914-2002 Rozměrové tolerance pro lisované díly
GBT13915-2002-T lisovací díly Tolerance úhlu
GB-T15005-2007 Ražené díly, Omezení odchylek bez specifikovaných tolerancí
GB-T 13916-2002 Ražené díly s Tvar a poloha bez stanovených tolerancí
Schopnost běžně používaných zařízení na zpracování plechu a rozsah zpracování běžných plechových zařízení
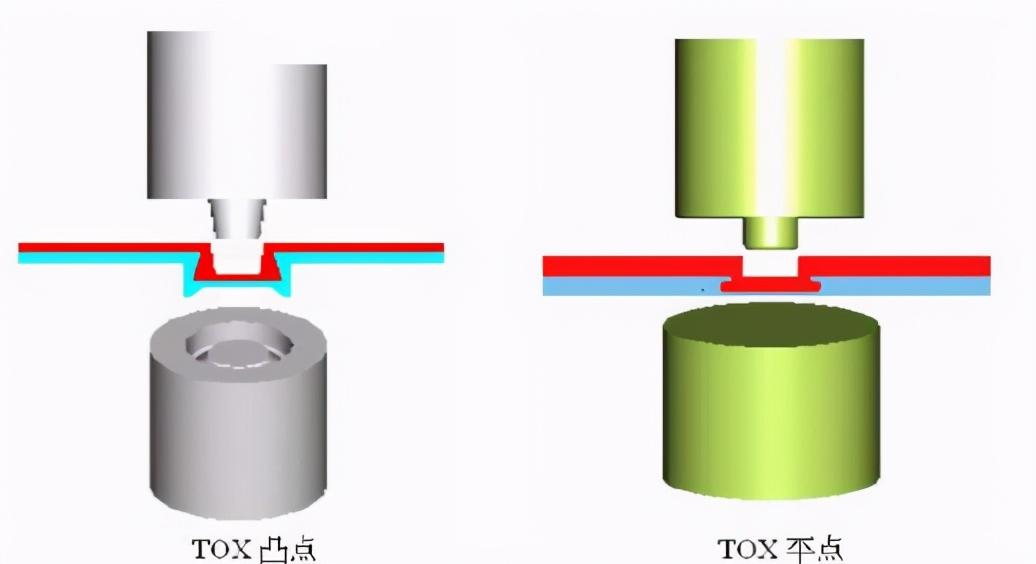
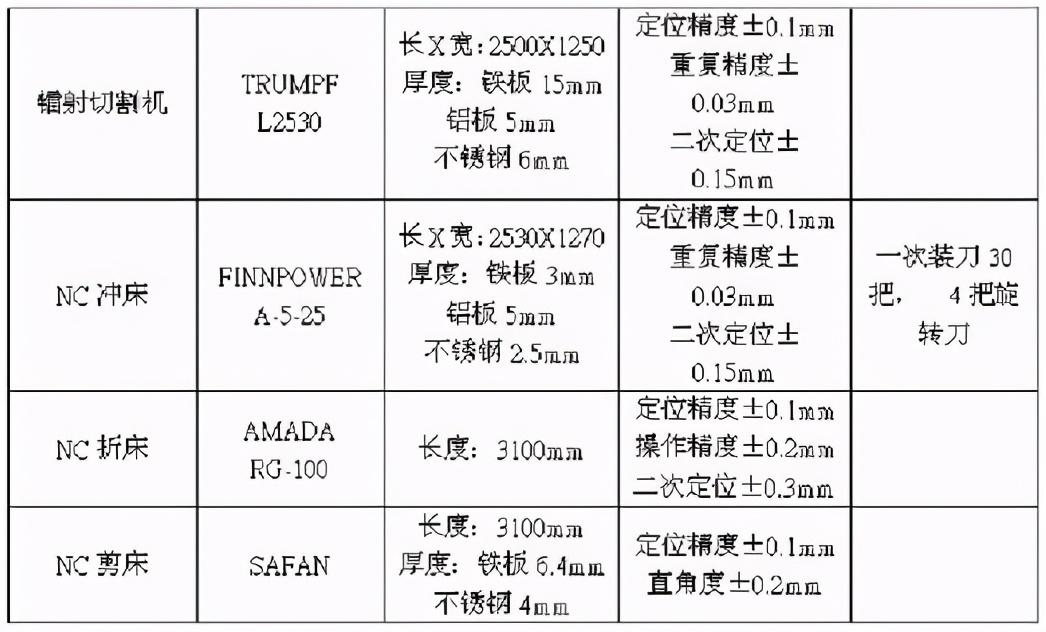