Jak určit procesní parametry laserového řezání v Shenyang?
Pracovní princip laserového řezání
Laserové řezání nahrazuje tradiční mechanické nože neviditelnými paprsky a má vlastnosti vysoce přesného, rychlého řezání, nikoli omezeného na řezné vzory, automatického psaní pro úsporu materiálů, hladkého řezání a nízkých nákladů na zpracování.Postupně zlepší nebo nahradí tradiční kovové řezání zařízení. Mechanická část laserové čepele nemá žádný kontakt s obrobkem a nezpůsobí poškrábání na povrchu obrobku během provozu; Rychlost řezání laserem je rychlá, řez je hladký a plochý a obecně nevyžaduje další zpracování; Řezná tepelně ovlivněná zóna je malá, deformace desky je malá a řezný šv je (0.1mm~0.3mm); Řez nemá mechanické namáhání a žádné smykové otřepy; Vysoká přesnost zpracování, dobrá opakovatelnost a žádné poškození povrchu materiálu; Numerické řídicí programování, schopné zpracovat libovolný plochý plán, dokáže řezat velké celé desky bez potřeby forem, což šetří čas a hospodárnost.
Složení laserového řezacího zařízení
Laserové řezací zařízení se skládá zejména z laseru, systému světla, CNC pohybového systému, automatické výškové nastavení řezné hlavy, pracovní plošiny a vysokotlakého systému foukání plynu. Mnoho parametrů může ovlivnit proces řezání laserem, z nichž některé závisí na technickém výkonu laseru a obráběcího stroje, zatímco jiné jsou variabilní. Hlavními parametry laserového řezání jsou:
Hlavní parametry laserového řezání
1 Režim paprsku
Základní režim, známý také jako Gaussovský režim, je ideálním režimem pro řezání, který se objevuje zejména u nízkých výkonových laserů s výkonem menším než 1kW. Multimode je směs režimů vyššího řádu, se špatným zaostřováním a nízkou schopností řezání při stejném výkonu.Single mode lasery mají lepší řezací schopnost a kvalitu než multimode lasery.
2 laserový výkon
Laserový výkon potřebný pro laserové řezání závisí hlavně na řezném materiálu, tloušťce materiálu a požadavcích na rychlost řezání. Výkon laseru má významný vliv na tloušťku řezu, rychlost řezu a šířku řezu. Obecně platí, že s rostoucím výkonem laseru se zvyšuje tloušťka materiálu, který lze řezat, zrychluje se řezná rychlost a zvyšuje se také šířka řezu.
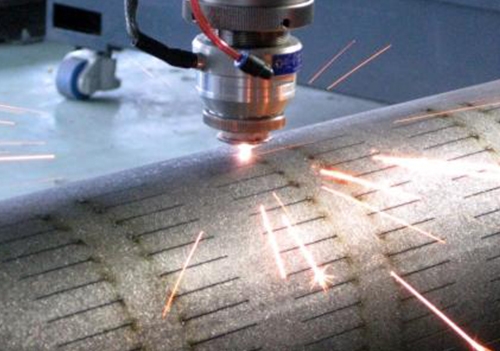
3 Polohy zaostření
ohnisková poloha má významný vliv na šířku řezu. Obecně se zaměření zvolí tak, aby bylo umístěno zhruba třetinu tloušťky pod povrchem materiálu, s větší hloubkou řezu a menší šířkou ústí.
4 ohniskové momenty
Při řezání silnějších ocelových desek by měl být použit paprsek s delší ohniskovou vzdáleností pro získání řezné plochy s dobrou svislostí. Hloubka ostření se zvyšuje, zvyšuje se také průměr světelného bodu a hustota výkonu se odpovídajícím způsobem snižuje, což vede ke snížení rychlosti řezání. Pro udržení určité rychlosti řezání je nutné zvýšit výkon laseru. Pro řezání tenkých desek je vhodné použít paprsek s menší ohniskovou vzdáleností, což vede k menšímu průměru bodu, vyšší hustotě výkonu a rychlejší řezné rychlosti.
5 Pomocné plyny
Řezání nízkouhlíkové oceli často používá kyslík jako řezný plyn k podpoře řezného procesu využitím tepla spalovací reakce železného kyslíku. Kromě toho, řezná rychlost je rychlá, řezná kvalita je dobrá a lze získat řezání bez strusky. Tlak se zvyšuje, kinetická energie se zvyšuje a kapacita vypouštění strusky se zvyšuje; Řezný tlak je určen na základě faktorů, jako je materiál, tloušťka desky, řezná rychlost a kvalita řezného povrchu.
6-struktura trysky
Struktura a tvar trysky, stejně jako velikost světelného výstupu, také ovlivňují kvalitu a účinnost laserového řezání.Různé řezací požadavky vyžadují použití různých trysek. Běžně používané tvary trysek zahrnují válcové, kuželové, čtvercové a další tvary. Laserové řezání obecně používá metodu koaxiálního foukání (proudění vzduchu soustředné s optickou osou). Pokud není proud vzduchu zarovnán s optickou osou, je během řezání snadno vytvořeno velké množství stříkání. Pro zajištění stability řezného procesu je obvykle nutné řídit vzdálenost mezi koncovou plochou trysky a povrchem obrobku, který je obecně 0.5-2.0mm, aby bylo usnadněno hladké řezání.
Obsah článku pochází z internetu. V případě jakýchkoli dotazů mě prosím kontaktujte a smažte ho!