Při používání laserového řezacího stroje Shenyang k řezání plechu se často vyskytují různé problémy. Aby byla zajištěna kvalita řezání, následuje několik běžných problémů a běžných řešení:
1. Technologie řezání a perforace:
Jakákoli technika tepelného řezání, s výjimkou několika případů, kdy může začít od okraje desky, obvykle vyžaduje vyvrtání malého otvoru skrz desku. Dříve, na laserových lisovacích kompozitních strojích, byl děrovač použit nejprve k vyděrování díry a pak laser byl použit k zahájení řezání z malé díry. Existují dvě základní metody pro propíchání laserových řezacích strojů bez lisovacích zařízení:
Po kontinuálním laserovém ozáření se v jádru materiálu vytvoří jáma a poté je roztavený materiál rychle odstraněn prouděním kyslíku koaxiálním s laserovým paprskem, aby vytvořil otvor. Velikost obecného otvoru souvisí s tloušťkou desky a průměrný průměr tryskací perforace je polovina tloušťky desky. Proto u silnějších desek je průměr tryskací perforace větší a není kulatý a není vhodný pro použití na díly s vysokými požadavky na přesnost zpracování. Může být použit pouze na odpadní materiály. Navíc vzhledem ke stejnému tlaku kyslíku používanému pro perforaci jako při řezání dochází k většímu stříkání.
Pulsní perforační blok pomocí pulzního laseru s vysokým špičkovým výkonem k tavení nebo odpařování malého množství materiálu, běžně používá vzduch nebo dusík jako pomocný plyn ke snížení rozšíření otvorů v důsledku exotermické oxidace a tlak plynu je nižší než tlak kyslíku během řezání. Každý pulsní laser vytváří pouze malé částicové trysky, které postupně pronikají hlouběji, takže doba perforace u tlustých desek trvá několik sekund. Po dokončení perforace okamžitě vyměňte pomocný plyn kyslíkem pro řezání. Tímto způsobem je průměr perforace menší a kvalita perforace je lepší než průměr tryskání. Laser použitý k tomu by měl mít nejen vysoký výstupní výkon; Důležitější je, že časové a prostorové charakteristiky paprsku jsou důležité, takže příčné proudění CO2 lasery obecně nemohou splnit požadavky laserového řezání. Pulsní perforace navíc vyžaduje spolehlivý systém řízení plynové dráhy pro dosažení spínání typů plynů a tlaků, stejně jako řízení doby perforace.
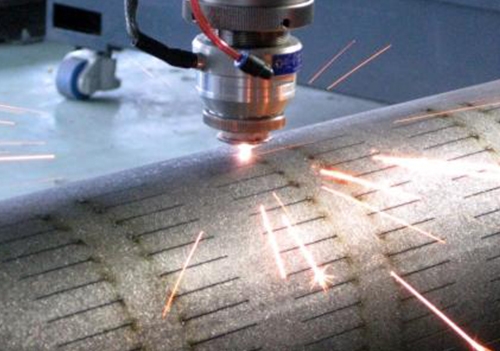
V případě použití pulzní perforace, aby bylo dosaženo vysoce kvalitních řezů, je třeba brát vážně technologii přechodu z pulzní perforace při stacionárním obrobku na kontinuální řezání obrobku s konstantní rychlostí. Teoreticky je obvykle možné změnit řezné podmínky akcelerační sekce, jako je ohnisková vzdálenost, poloha trysky, tlak plynu atd., ale v praxi je možnost změny těchto podmínek nepravděpodobná kvůli krátké době. V průmyslové výrobě je praktičtější používat zejména metodu změny průměrného laserového výkonu, konkrétně změnou šířky pulzu; Změnit frekvenci pulzu; Současně mění šířku a frekvenci pulzu. Skutečné výsledky ukazují, že třetí efekt bude velmi dobrý.
2. Analýza deformace malých otvorů (průměr malý a tloušťka desky) při řezání a zpracování:
Je to proto, že obráběcí stroje (pouze u vysoce výkonných laserových řezacích strojů) nepoužívají výbušnou perforaci při zpracování malých otvorů, ale používají pulzní perforaci (měkké punkce), což způsobuje příliš koncentrovanou laserovou energii na malé ploše, spaluje rovněž neopracovatelnou oblast, což způsobuje deformaci otvoru a ovlivňuje kvalitu zpracování. V tomto bodě bychom měli změnit metodu pulsní perforace (měkké punkce) na metodu tryskací perforace (běžné punkce) v programu zpracování, abychom problém vyřešili. U menších výkonových laserových řezacích strojů platí opak. Při zpracování malých otvorů by měla být přijata pulzní perforace, aby bylo dosaženo lepší hladkosti povrchu.
Obsah článku pochází z internetu. V případě jakýchkoli dotazů mě prosím kontaktujte a smažte ho!