Pladebehandling er en omfattende kold bearbejdningsproces til metalplader (normalt under 6 mm), herunder skæring, stansning, bøjning, svejsning, nitning, skimmelformning og overfladebehandling. Dens fremtrædende træk er, at tykkelsen af den samme del er konsistent.
Pladebehandlingsmetode: Ikke støbeform forarbejdning: Processen med pladebehandling gennem udstyr såsom numerisk stansning, laserskæring, klippemaskiner, bukkemaskiner, nittemaskiner osv. Det anvendes generelt til prøveproduktion eller lille batchproduktion, med høje omkostninger. Kort behandlingscyklus og hurtig reaktion. Formbehandling: Ved hjælp af faste forme til behandling af metalplader er der generelt skære forme og danne forme, hovedsageligt brugt til masseproduktion med lavere omkostninger. De oprindelige skimmelomkostninger er høje, og kvaliteten af delene er garanteret. Den tidlige behandlingscyklus er lang, og skimmelomkostningerne er høje. Pladebehandling proces: skæring: numerisk stansning, laserskæring, klippemaskine
Formning - bøjning, strækning, stansning: bukkemaskiner, stansemaskiner mv
Anden forarbejdning: nitning, gevindning osv.
Svejsning: tilslutningsmetoden af metalplader
Overfladebehandling: pulversprøjtning, galvanisering, trådtegning, screenprint osv.
Pladebehandlingsteknologi - De vigtigste skæremetoder til pladebehandling omfatter numerisk stansning, laserskæring, klippemaskiner og skimmelskæring. CNC er i øjeblikket en almindeligt anvendt metode, og laserskæring anvendes hovedsageligt i prøveudtagningsfasen (eller kan også behandle rustfrit stål pladedele), med høje behandlingsomkostninger.
Nedenfor vil vi primært introducere skæring af plader ved hjælp af numerisk stansning
Numerisk stansning, også kendt som tårn CNC stansemaskine, kan bruges til skæring, stansning, strækning af huller, rulleribber, stansning persienner osv Dens bearbejdning nøjagtighed kan nå +/-0,1 mm.
Tykkelsen af den CNC bearbejdbare plade er:
Koldtvalsede og varmtvalsede plader 4,0 mm
Aluminiumsplade 5, 0mm
Plade af rustfrit stål 2, 0mm
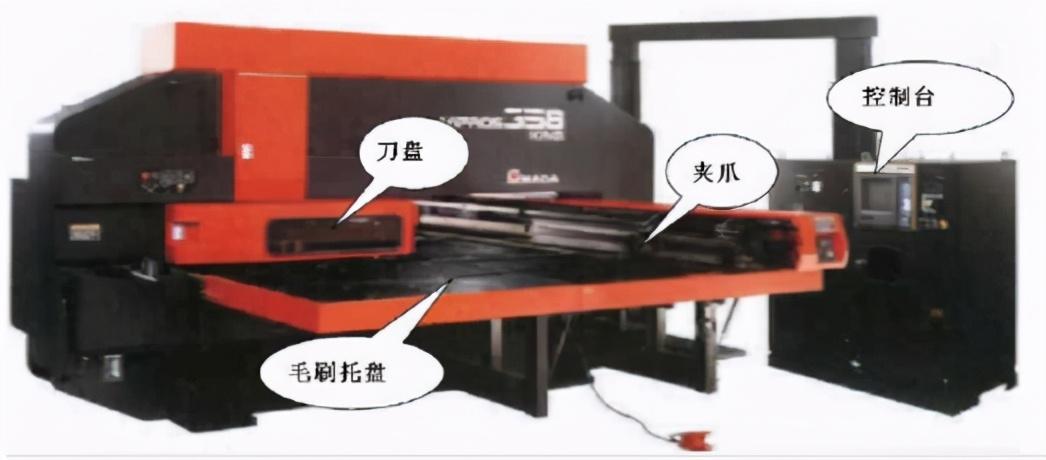
Der er et minimumsstørrelseskrav til stansning. Den mindste størrelse af stansning er relateret til hullets form, de mekaniske egenskaber af materialet og tykkelsen af materialet. (Som vist i figuren nedenfor)
2. Afstand og kantafstand af hullerne. Når den mindste afstand mellem delens stansekant og delens yderkant ikke er parallel med delens yderkant, bør den mindste afstand ikke være mindre end materialetykkelsen t. Når parallelt, bør det ikke være mindre end 1,5t. (Som vist i figuren nedenfor)
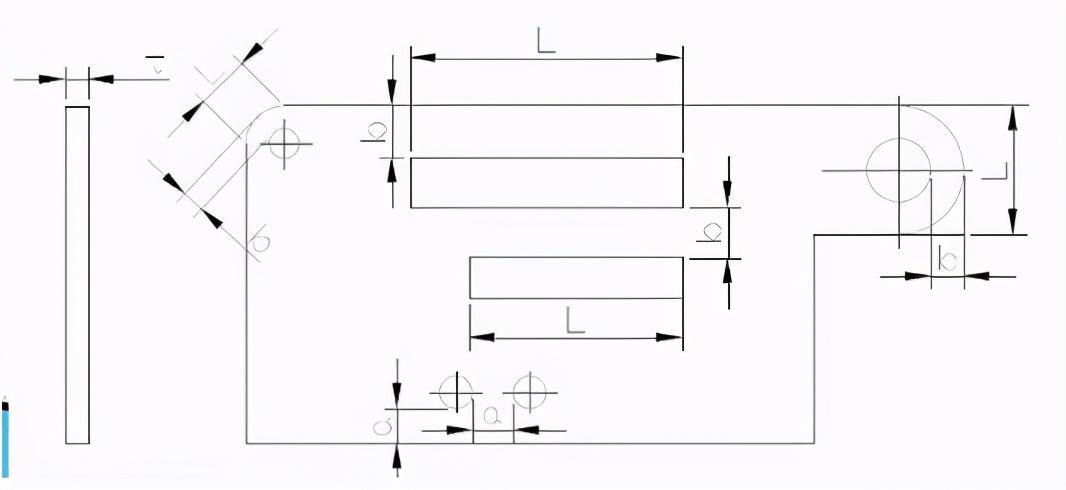
3. Ved udstrækning af huller er den mindste afstand mellem strækhullet og kanten 3T, den mindste afstand mellem to strækhuller er 6T, og den mindste sikre afstand mellem strækhullet og bøjningskanten (inde) er 3T + R (T er pladetykkelsen, R er bøjningsfilet)
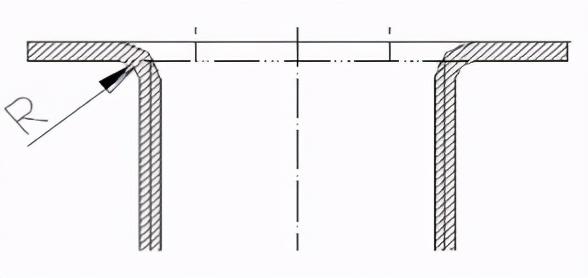
4. Ved stansning af huller i strækkede og bøjede dele og dybtrukne dele bør der opretholdes en vis afstand mellem hulvæggen og den lige væg. (Som vist i figuren nedenfor)
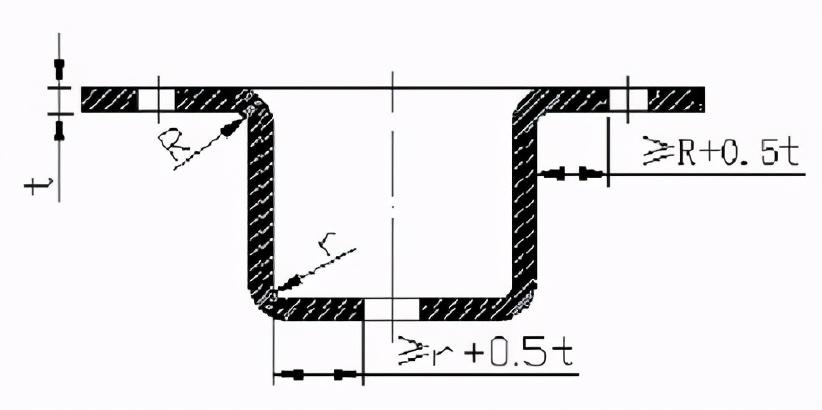
Pladebehandlingsteknologi - Formning af plader indebærer hovedsagelig bøjning og strækning af pladen.
1. Pladebejsning 1.1 Pladebejsning bruger hovedsageligt bøjningsmaskiner.
Foldemaskinens bearbejdningsnøjagtighed
En fold:+/- 0, 1mm
Halv fold:+/- 0, 2mm
Over 20% rabat: +/-0,3 mm
Det grundlæggende princip for bøjning forarbejdning sekvens er at bøje indefra og ud og fra små til store.Specielle former bør bøjes først, og den tidligere proces bør ikke påvirke eller forstyrre de efterfølgende processer efter dannelse.
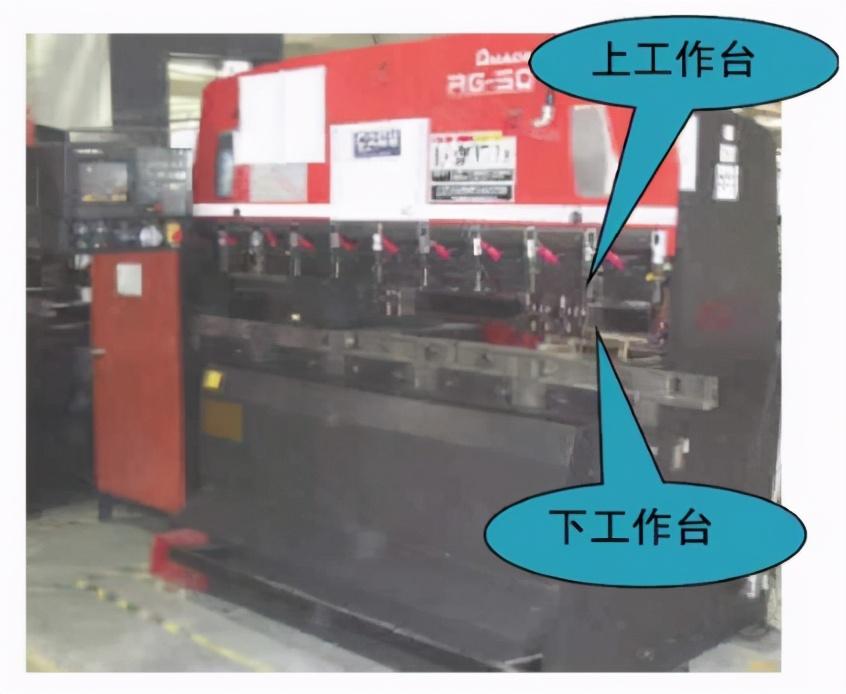
1.3 Almindelige former for bøjeknive:
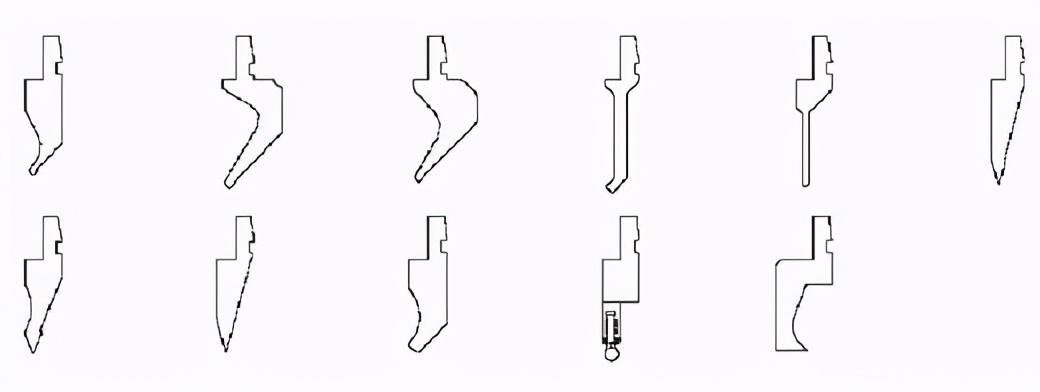
Almindelige V-rilleformer:
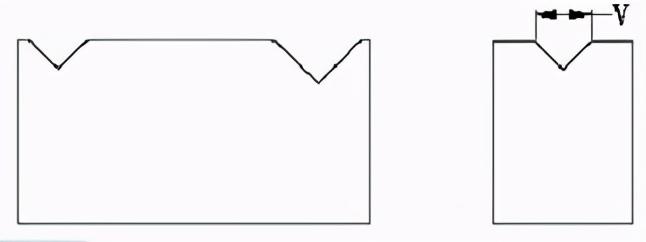
1.4 Mindste bøjningsradius for bøjede dele:
Når materialet bøjes, strækkes det ydre lag, og det indre lag komprimeres i det afrundede område. Når materialetykkelsen er konstant, jo mindre er den indre r, jo sværere er spændingen og kompressionen af materialet; Når trækstyrken i det ydre afrundede hjørne overstiger materialets ultimative styrke, vil der opstå revner og brud, og derfor bør strukturen af bøjede dele undgå for små bøjning afrundede hjørneradier. Den mindste bøjningsradius for almindeligt anvendte materialer i virksomheden er vist i tabellen nedenfor.
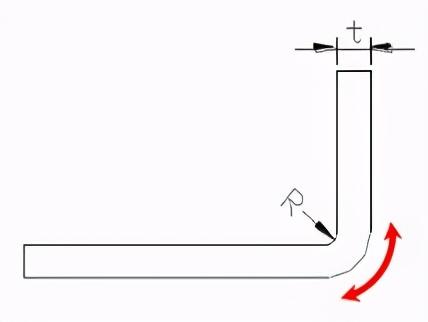
Tabel over mindste bøjneradius for bøjede dele:
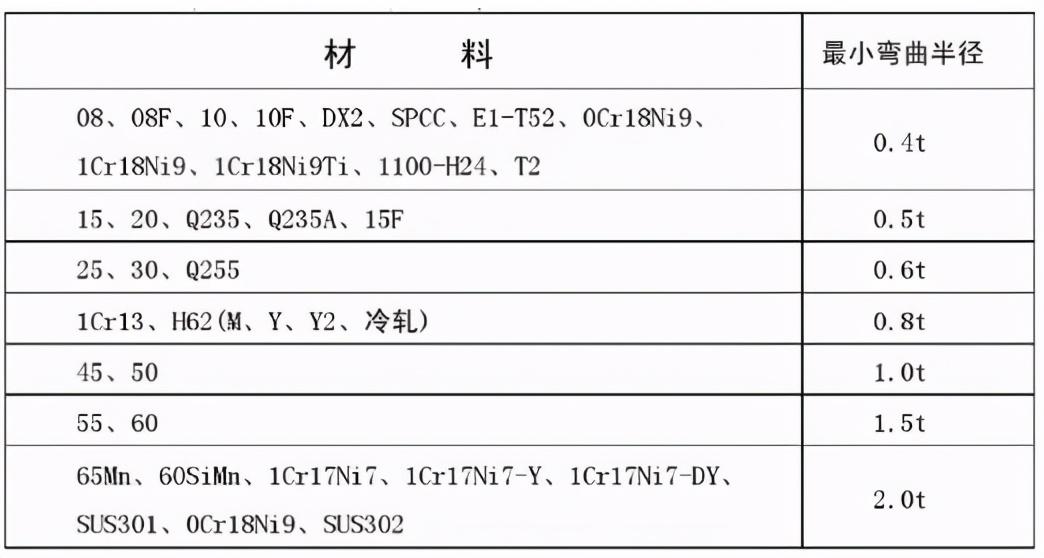
Bøjningsradius refererer til den indre radius af den bøjede del, og t er vægtykkelsen af materialet.
Den lige kanthøjde af den bøjede del er 1,5:
Generelt bør den mindste lige kanthøjde ikke være for lille, og minimumshøjdekravet er: h>2t
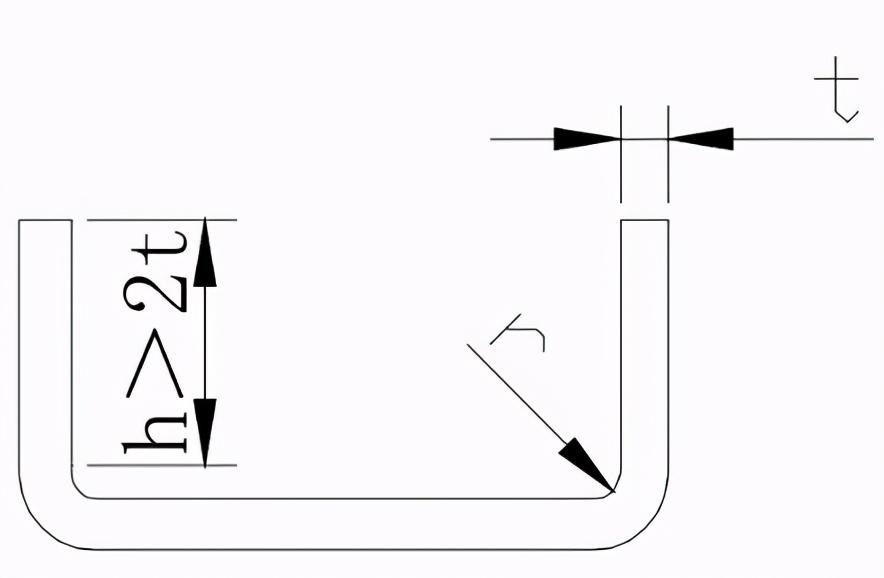
Hvis den lige kanthøjde h2t af den bøjede del er påkrævet, skal du først øge bøjningskantens højde og derefter behandle den til den ønskede størrelse efter bøjning; Eller efter behandling af lavvandede riller i bøjningsformationszonen, udføre bøjning.
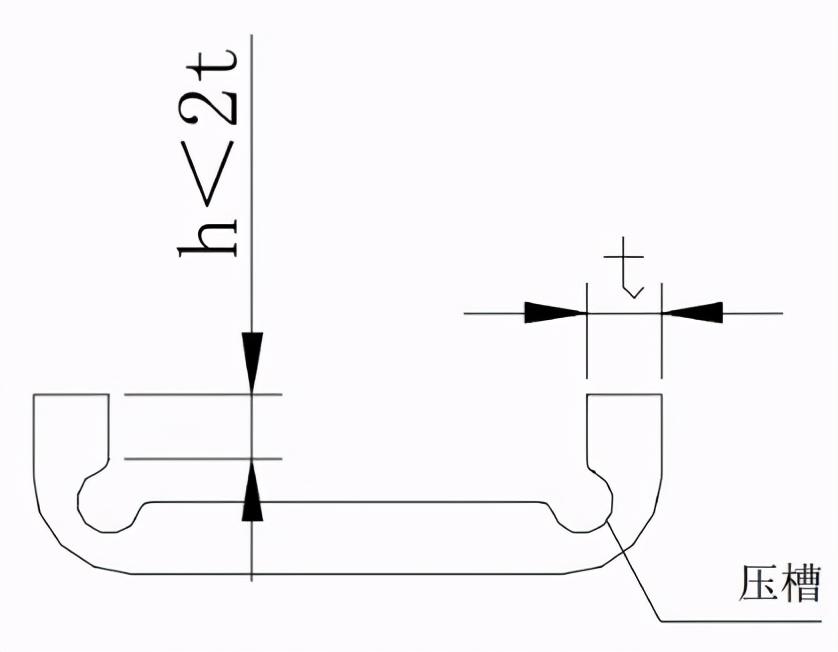
1.6 Minimum bøjning lige kanthøjde med skrå vinkel på den buede kant:
Når en buet del med skrå kant bøjes, er sidens minimumshøjde: h=(2-4) t> 3 mm
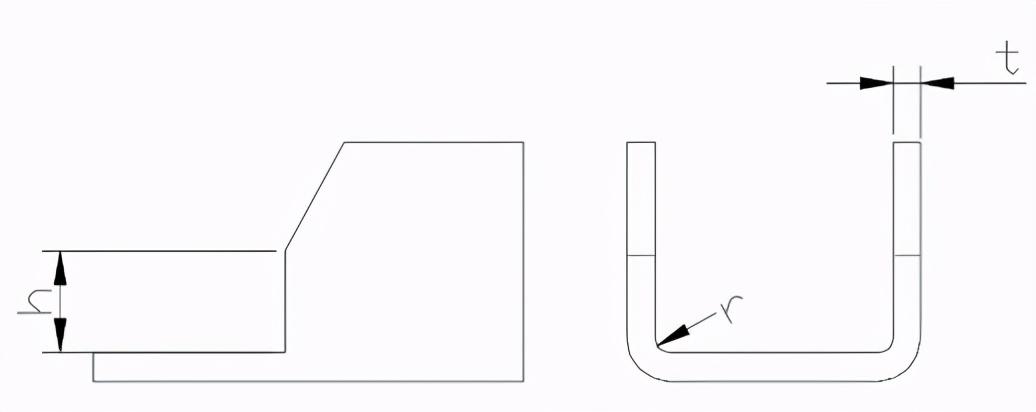
1.7 Kantsafstand af huller på bøjede dele:
Hulafstand: Stans hullet først og derefter bøj det.Placeringen af hullet skal være uden for bøjningsdeformationszonen for at undgå deformation af hullet under bøjning. Afstanden fra hulvæggen til den buede kant er vist i tabellen nedenfor.
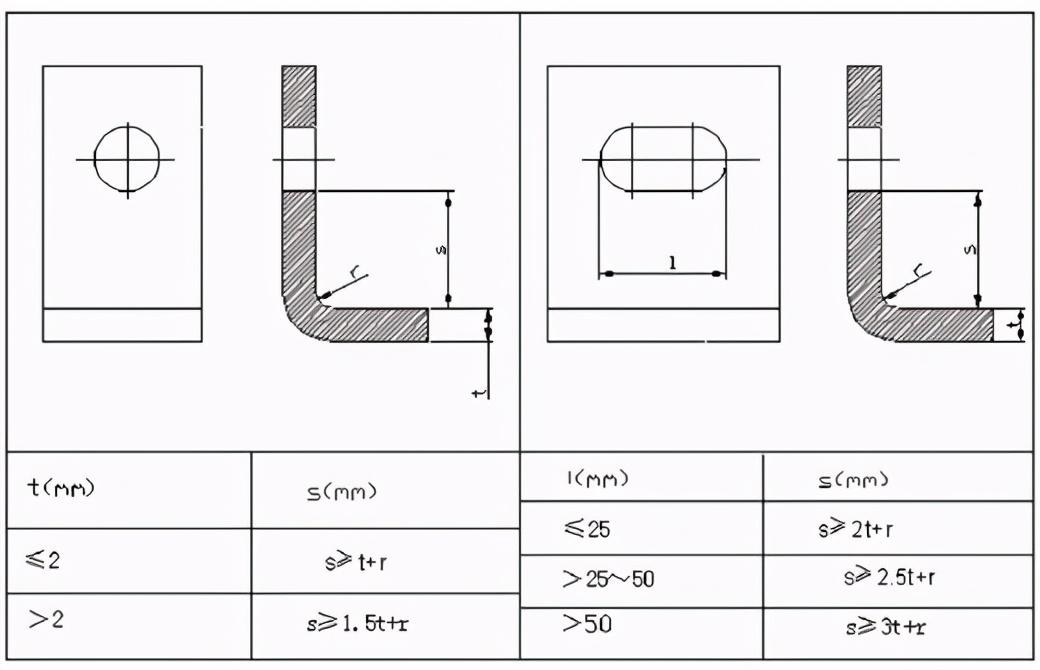
1.8 Processnit til lokal bøjning:
Bøjningslinjen af den bøjede del bør undgå placeringen af pludselige størrelsesændringer. Ved bøjning af et bestemt segment af kanten lokalt, for at forhindre spændingskoncentration og revner i skarpe hjørner, kan bøjningskurven flyttes en vis afstand for at forlade den pludselige ændring i størrelse (figur a), eller en procesrille (figur b) kan åbnes, eller et proceshul kan stanses (figur c). Vær opmærksom på størrelseskravene i diagrammet: SR; Slotbredde kt Slotdybde Lt+R+k/2.
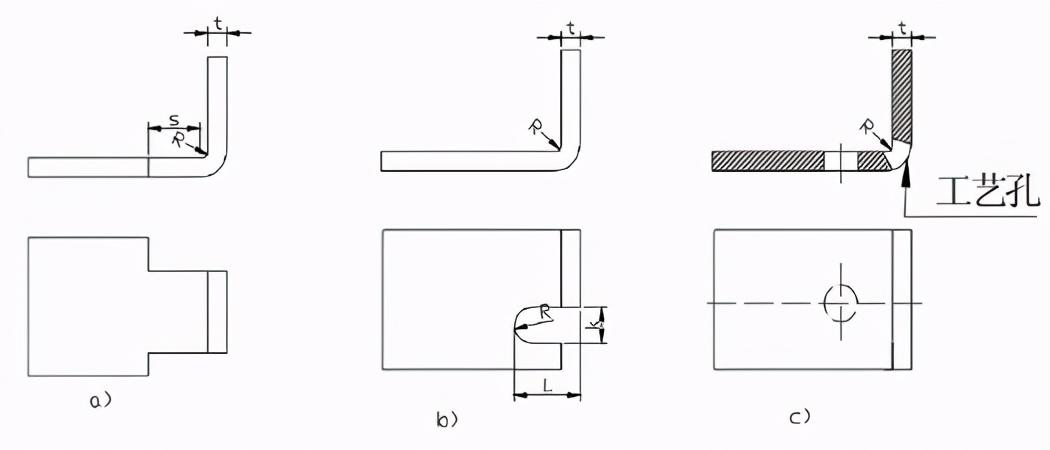
1.9 Bøjningskanter med skrå kanter bør undgå deformationszoner:
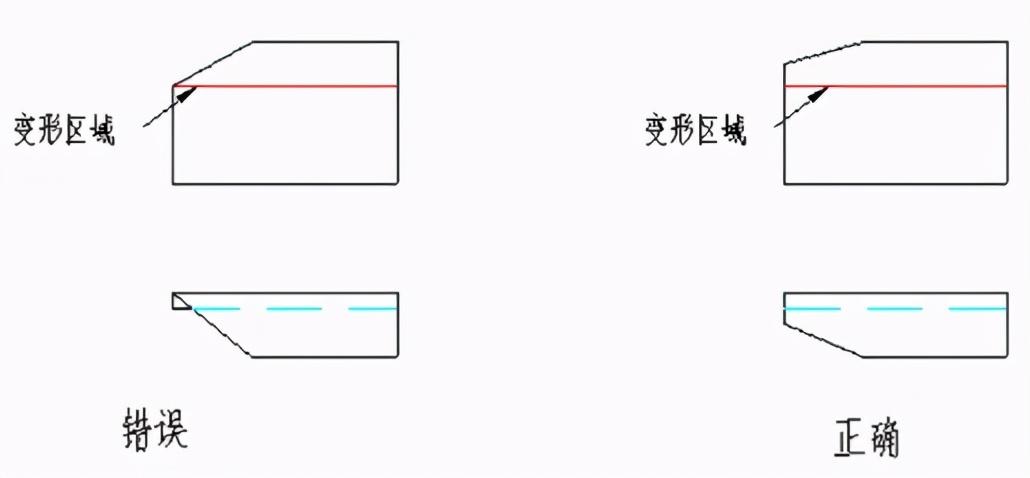
1.10 Konstruktionskrav til pladebelæg (døde kanter):
Den døde kant længde af plader læg er relateret til tykkelsen af materialet. Som vist i følgende figur er den mindste længde af en død kant generelt L3,5t+R.
Blandt dem er t materialevægtykkelsen, og R er den mindste indre bøjningsradius af den tidligere proces (som vist til højre i figuren nedenfor), før kanten dræbes.

1.11 Tilføjet procespositioneringshuller:
For at sikre den nøjagtige placering af emnet i formen og forhindre afvigelsen af emnet under bøjning, skal procespositioneringshuller tilføjes på forhånd under design, som vist i følgende figur. Specielt for dele, der er blevet bøjet flere gange, skal proceshullerne bruges som positioneringsreference for at reducere kumulative fejl og sikre produktkvaliteten.
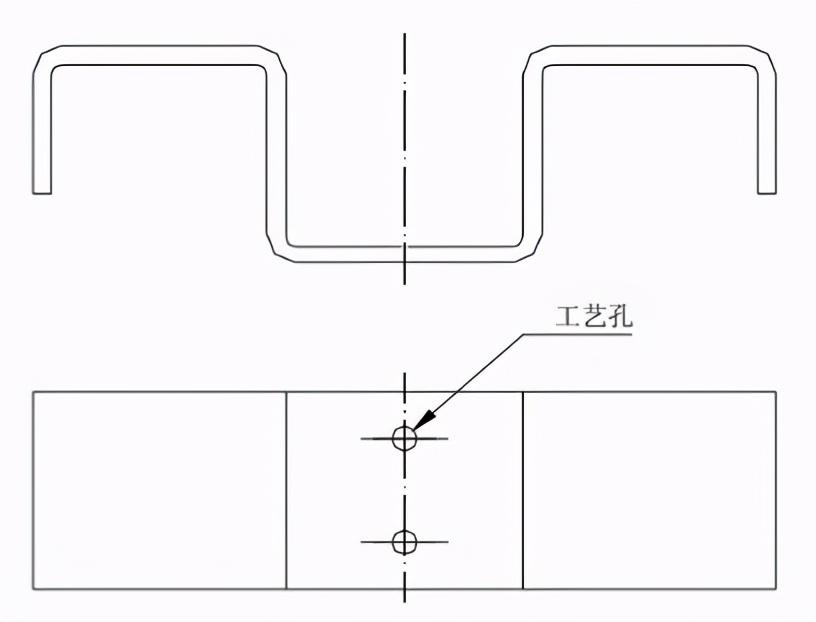
Ved mærkning af dimensionerne af bøjede dele bør der tages hensyn til bearbejdningsevnen:
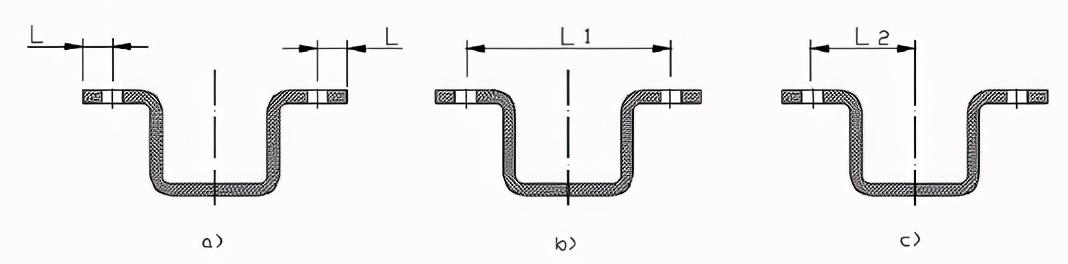
Som vist i ovenstående figur, a) stansning først og derefter bøjning, L dimension nøjagtighed er let at sikre, og behandlingen er praktisk. b) Hvis præcisionskravet for dimension L er højt, er det nødvendigt at bøje først og derefter behandle hullet, hvilket er besværligt at behandle.
Der er mange faktorer, der påvirker springback af bøjede dele, herunder materialets mekaniske egenskaber, vægtykkelse, bøjningsradius og positivt tryk under bøjning. Jo større forholdet mellem den indre radius af den bøjede del og pladetykkelsen, jo større er rebound. Metoden til at undertrykke rebound fra et designperspektiv, såsom rebound af bøjede dele, undgås i øjeblikket hovedsageligt af producenter under skimmeldesign ved at træffe visse foranstaltninger. Samtidig kan forbedring af visse strukturer i design reducere springback vinklen, som vist i følgende figur: presning af forstærkningsribber i bøjningsområdet kan ikke kun øge arbejdsemnets stivhed, men også hjælpe med at undertrykke springback.
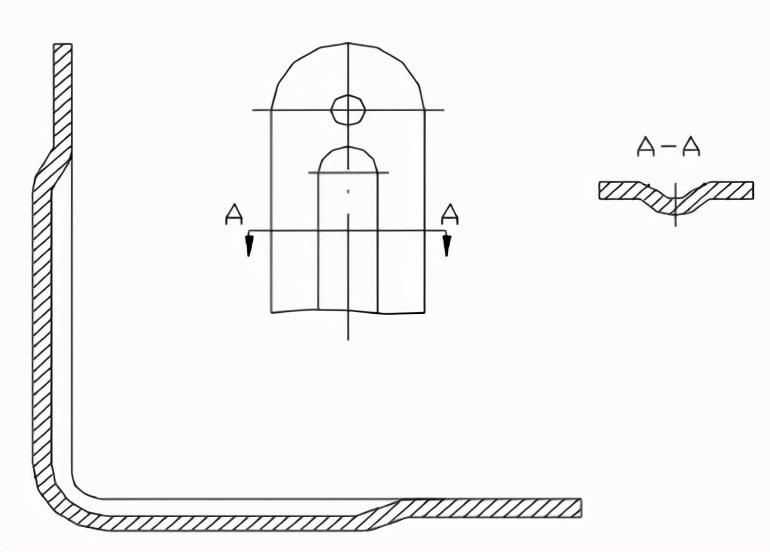
Strækningen af plader afsluttes hovedsageligt af CNC eller konventionel stansning, der kræver forskellige strækningsstanser eller forme.
Formen på den strakte del skal være så enkel og symmetrisk som muligt, og skal dannes i ét stræk så meget som muligt.
Dele, der kræver flere strækninger, skal give mulighed for mulige overflademarker under strækningsprocessen.
På forudsætning af at sikre monteringskrav bør det være tilladt at strække sidevæggene med en vis hældning.
2.1 Krav til filetteradius mellem bunden af den strakte del og den lige væg:
Som vist i figuren nedenfor skal filetteradius mellem bunden af den strakte del og den lige væg være større end pladetykkelsen, dvs. r1t. For at gøre strækningsprocessen glattere tages normalt r1=(3-5) t, og den maksimale filetteradius bør være mindre end eller lig med 8 gange pladetykkelsen, som er r18t.
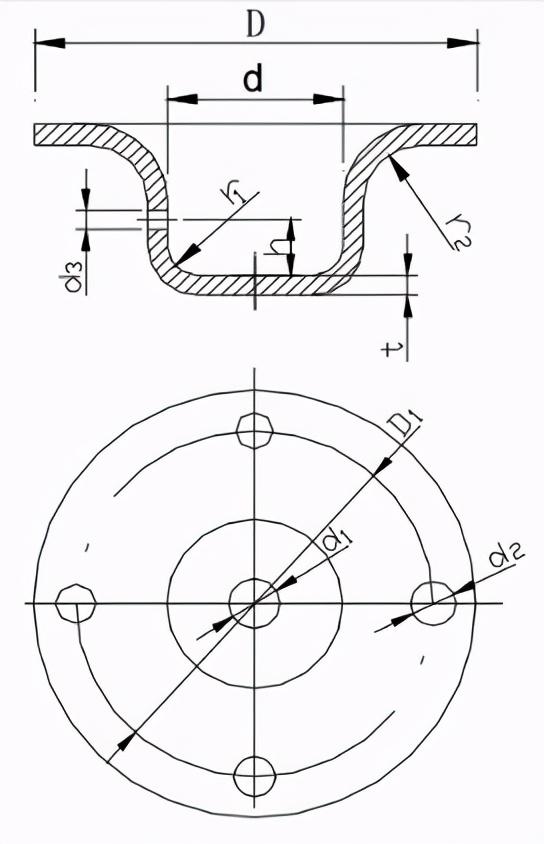
2.2 Afrundingsradius mellem flangen og væggen af den strækkede del
Filtens radius mellem flangen og væggen af den strækkede del bør være større end dobbelt så tykkelse pladen, dvs. r22t. For at gøre strækningsprocessen glattere, tages r2=(5-10) t generelt, og den maksimale flangeradius bør være mindre end eller lig med 8 gange tykkelsen af pladen, dvs. r28t. (Se ovenstående figur)
2.3 Indre hulrum diameter af cirkulære strækkede dele
Den indre diameter af det cirkulære strækstykke skal tages som D d+10t, så trykpladen trykkes tæt uden rynker under strækning. (Se ovenstående figur)
2.4 Afrundingsradius mellem tilstødende vægge af rektangulære strækkede dele
Radius af filetet mellem tilstødende vægge af et rektangulært strækket stykke bør tages som r3 3t. For at reducere antallet af strækninger bør r3 H/5 tages så meget som muligt, så det kan trækkes ud på én gang.
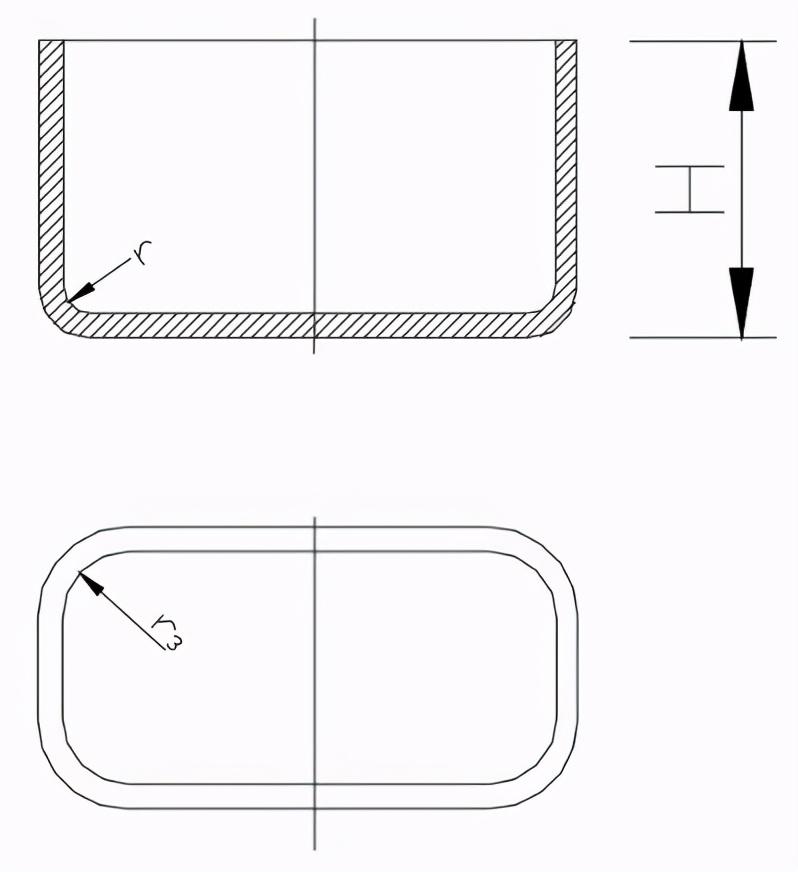
Krav til dimensionsforholdet mellem højde og diameter af en 2,5 rund flangefri strækningsdel under engangsformning
Ved dannelse af en cirkulær flangefri strækningsdel på én gang, bør forholdet mellem højde H og diameter d være mindre end eller lig med 0,4, dvs. H/d 0,4, som vist i følgende figur.
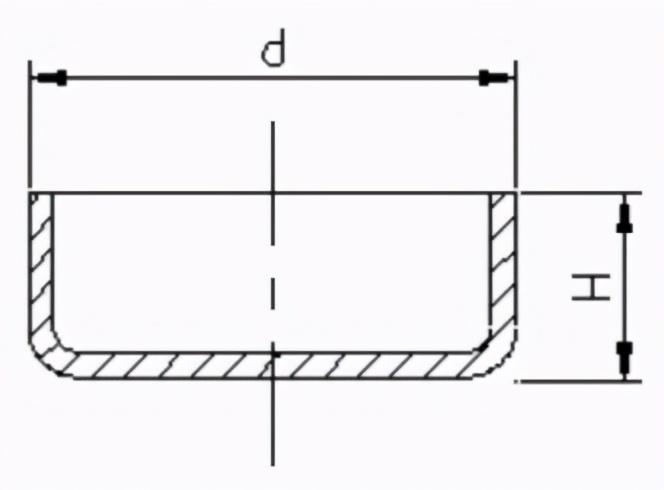
2.6 Tykkelse variation af strækket materiale:
Tykkelsen af det strækkede materiale ændrer sig på grund af de varierende belastningsniveauer, der påføres hver del. Generelt fastholdes den oprindelige tykkelse midt i bunden, materialet i de afrundede hjørner af bunden bliver tyndere, materialet nær flangen øverst bliver tykkere, og materialet omkring de afrundede hjørner af den rektangulære strækkede del bliver tykkere.
2.7 Mærkningsmetode for produktdimensioner på strækkede dele
Ved udformning af strækprodukter bør dimensionerne på produkttegningen være tydeligt angivet for at sikre, at både eksterne og indvendige dimensioner garanteres, og indvendige og udvendige dimensioner ikke kan mærkes samtidigt.
2.8 Metode til anmærkning af dimensionelle tolerancer for strækkede dele
Den indre radius af den konkave konvekse bue af den strækkede del og højdemål tolerance for den cylindriske strækkede del dannet på én gang er dobbeltsidede symmetriske afvigelser med en afvigelsesværdi på halvdelen af den absolutte værdi af præcisionstolerance for den nationale standard (GB) niveau 16, og nummereres.
3. Anden formning af plader: Forstærkning ribber - Tryk ribber på flade metaldele bidrager til at øge strukturel stivhed.
Louvers - Louvers er almindeligt anvendt på forskellige hylstre eller hylstre til at give ventilation og varmeafledning.
Hulflange (strækhul) - bruges til at bearbejde gevind eller øge stivheden af hulubningen.
3.1 Forstærkning:
Forstærkningsstruktur og valg af størrelse
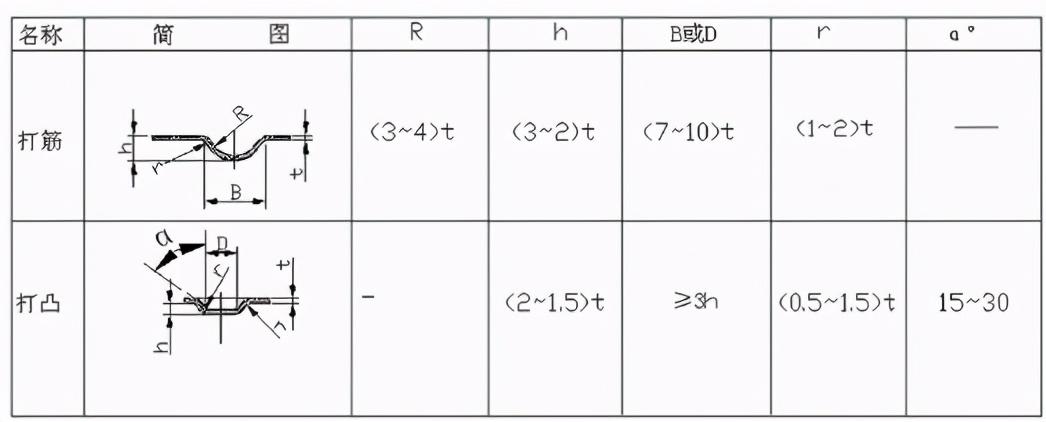
De maksimale dimensioner for konveks afstand og konveks kantafstand vælges i henhold til tabellen nedenfor.
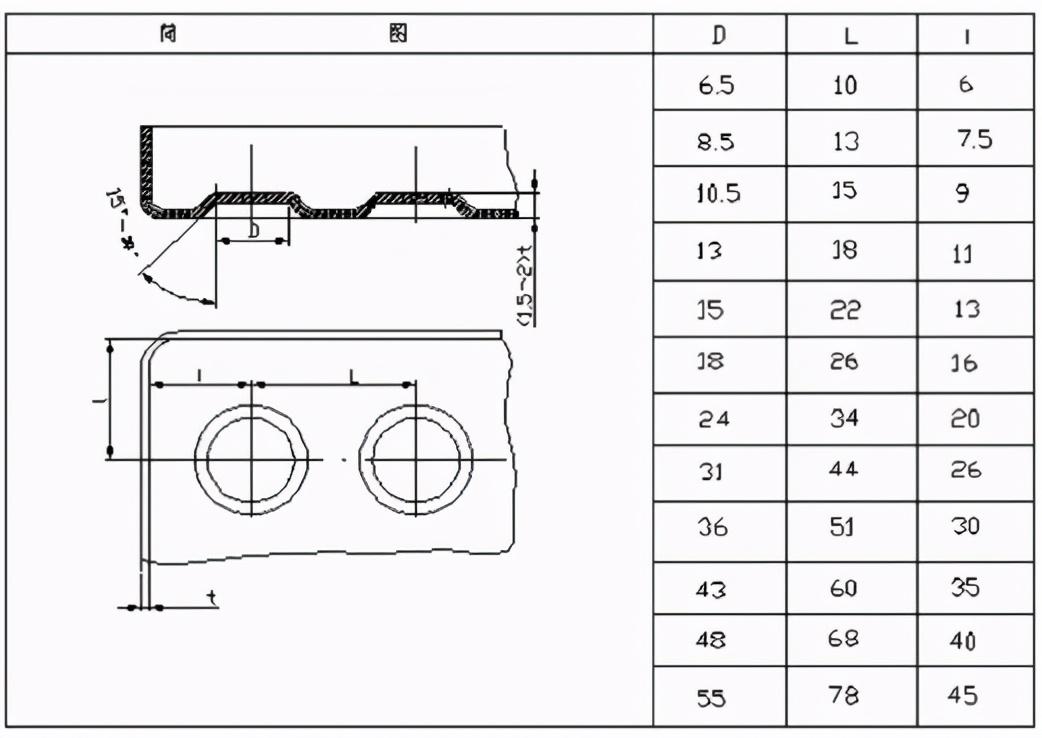
3. 2 Louvers
Metoden til dannelse af persienner er at skære åbne materialet ved hjælp af en kant af den konvekse skimmel, mens de resterende dele af den konvekse skimmel samtidig strækker og deformerer materialet og danner en bølgende form med en sideåbning.
Den typiske struktur af lamelen er vist i følgende figur
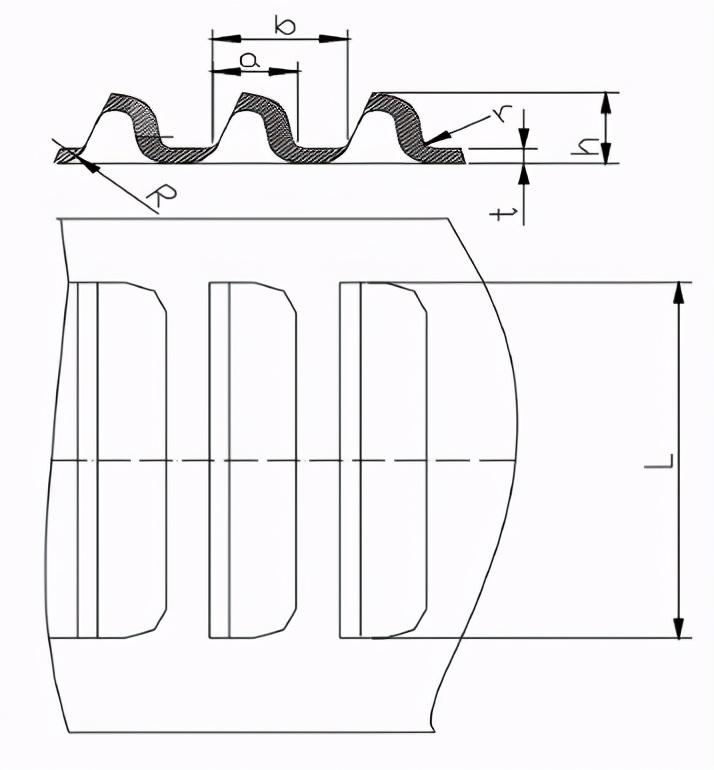
Krav til højttalerstørrelse: a4t b6t;h5t;L24t;r0.5t。
3.3 Flanging af huller (udstrækning af huller)
Der er mange former for hulflangning, og den fælles er at bearbejde den indre hulflangning af gevind.
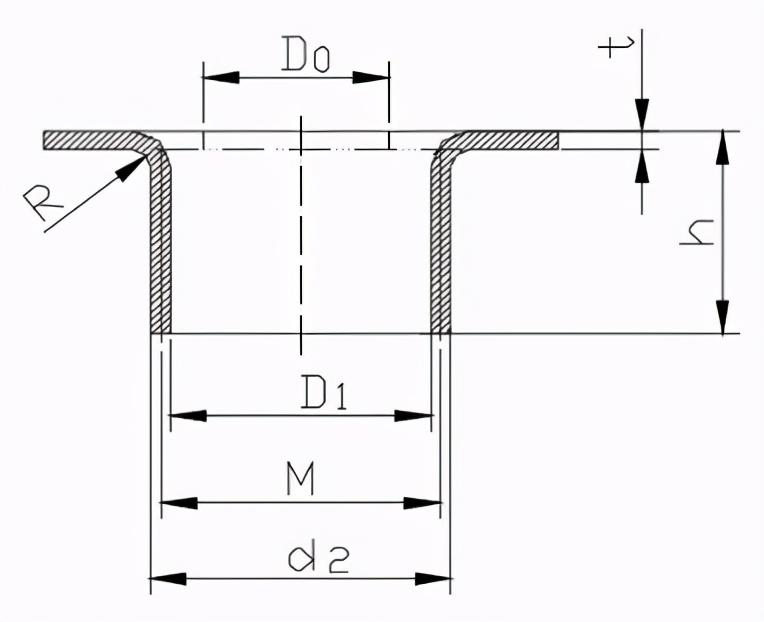
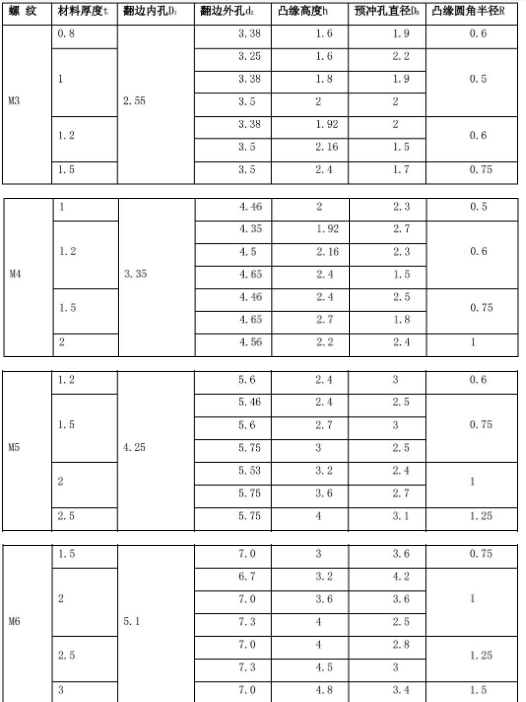
Pladebehandlingsteknologi - nitning af andre forarbejdede pladebehandlinger, såsom nitmøtrikker, nittebolte, nitteføringssøjler osv.
2. Taping af gevindhuller på plader.
Pladetykkelse t< Klokken 1,5, brug vendt kant tryk. Når pladetykkelsen er t1,5, kan direkte gevindning anvendes.
Pladebehandlingsteknologi - Ved svejsning i design af pladebehandlingsstrukturer, bør det implementeres for at "symmetrisk arrangere svejsninger og svejsepunkter, og undgå skæring, aggregering og overlapning Sekundære svejsninger og svejsepunkter kan afbrydes, og hovedsvejsninger og svejsepunkter skal forbindes."
Svejsning, der almindeligvis anvendes i metalplader, omfatter buesvejsning, modstandssvejsning osv.
Der skal være tilstrækkelig svejseplads mellem buesvejsede plader, og den maksimale svejsning mellem 0,5 og 0,8 mm Svejsesømmen skal være ensartet og flad.
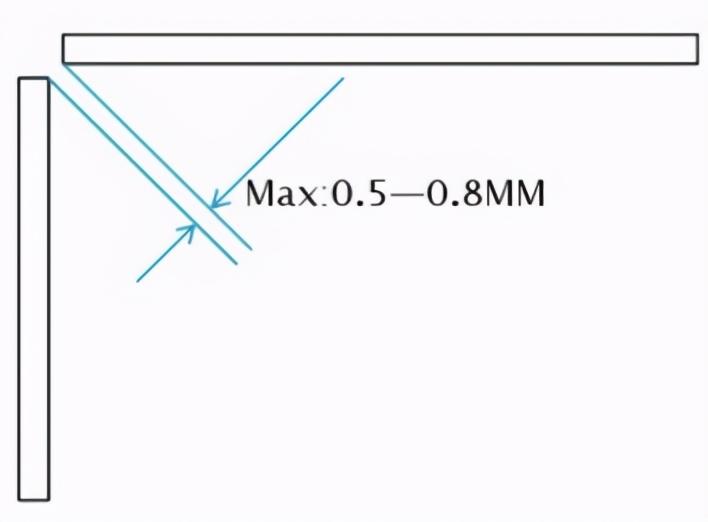
2. svejseoverfladen af modstandssvejsning skal være flad, uden rynker, rebound osv.
Målene for modstandssvejsning er vist i nedenstående tabel:
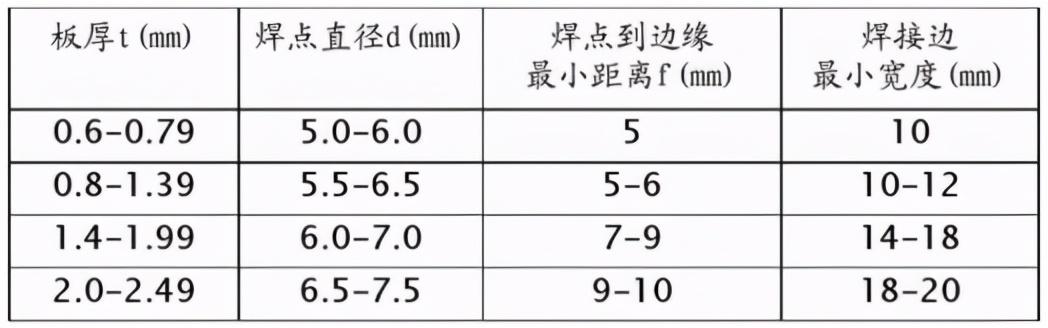
Afstand mellem modstandsledninger
Ved svejsning af små dele i praksis kan dataene i tabellen nedenfor henvises til.
Ved svejsning af store dele kan afstanden mellem punkterne øges passende, generelt ikke mindre end 40-50mm. For ikke-stressede dele kan afstanden mellem svejsepunkterne forstørres til 70-80mm.
Pladetykkelse t, loddediameter d, mindste loddediameter dmin og mindste afstand e mellem loddediameter Hvis pladen er en kombination af forskellige tykkelser, vælges efter den tyndeste plade.
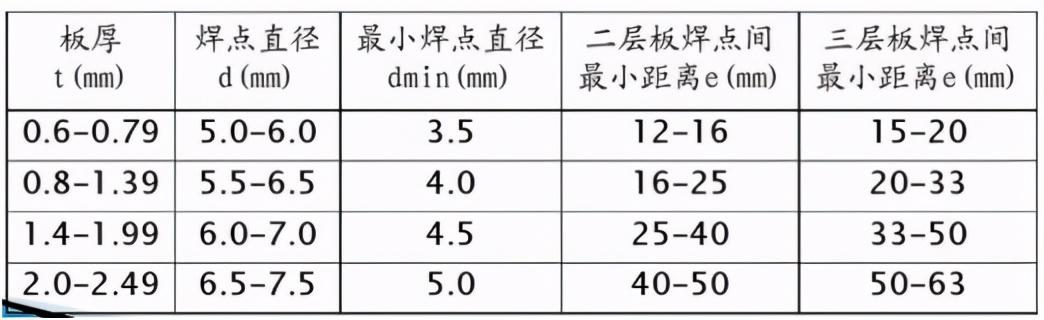
Antal lag og materialetykkelsesforhold for modstandssvejseplader
Pladen til modstandspladssvejsning er generelt 2 lag, med højst 3 lag Tykkelsesforholdet for hvert lag af svejsede led skal være mellem 1/3 og 3.
Hvis det er nødvendigt at svejse en tre-lags plade, skal materialetykkelsesforholdet kontrolleres først. Hvis det er rimeligt, kan svejsning udføres. Hvis det ikke er rimeligt, bør der overvejes proceshuller eller proceshak. Ved to-lags svejsning skal svejsepunkterne forskudes.
Pladebehandlingsteknologi - Tilslutningsmetoder: Dette introducerer hovedsageligt tilslutningsmetoderne for plader under forarbejdningen, herunder nittenitning, svejsning (som nævnt ovenfor), hultregning nitning og TOX nitning.
Nitning: Denne type nitte kaldes almindeligvis en trænitte, som indebærer at nitte to stykker plade sammen gennem en trænitte. De almindelige nitteformer er vist i figuren:
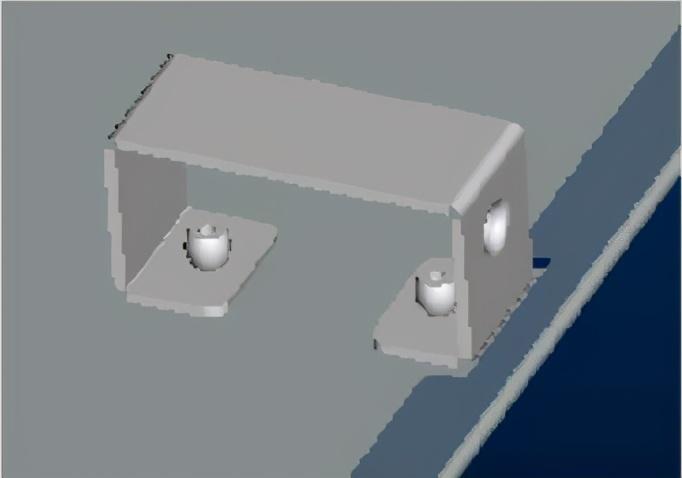
2. svejsning (som nævnt tidligere) 3. tegning og nitning: Den ene del er et tegnehul, og den anden del er et forsænket hul, som er lavet til en uadskillelig forbindelseskrop gennem nitning.
Overlegenhed: Udsugningshullet og dets tilsvarende synkehul har positioneringsfunktion. Nitningsstyrken er høj, og effektiviteten af nitning gennem forme er også relativt høj.
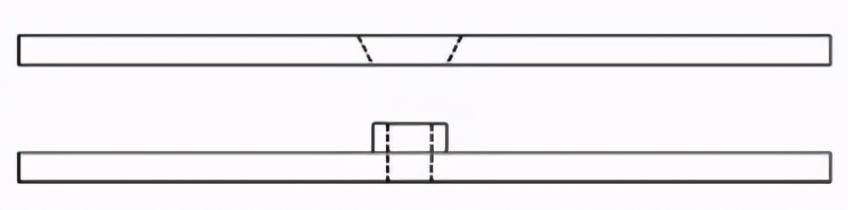
4. TOX nitte: Tryk den tilsluttede del ind i den konkave form gennem en simpel konveks form. Under yderligere pres flyder materialet inde i den konkave skimmel udad. Resultatet er et cirkulært tilslutningspunkt uden kanter eller fræser, hvilket ikke påvirker korrosionsbestandigheden Selv for plader med belægning eller sprøjtelag på overfladen kan de oprindelige rust- og korrosionsbestandighedsegenskaber bevares, fordi belægnings- og malingsbestandighedsegenskaber også kan bevare de oprindelige rust- og korrosionsbestandighedsegenskaber, da belægningen og malingslaget også deformeres og strømmer sammen. Materialet presses mod begge sider og ind i pladen ved siden af den konkave form og danner TOX forbindelsesprikker. Som vist i følgende figur:
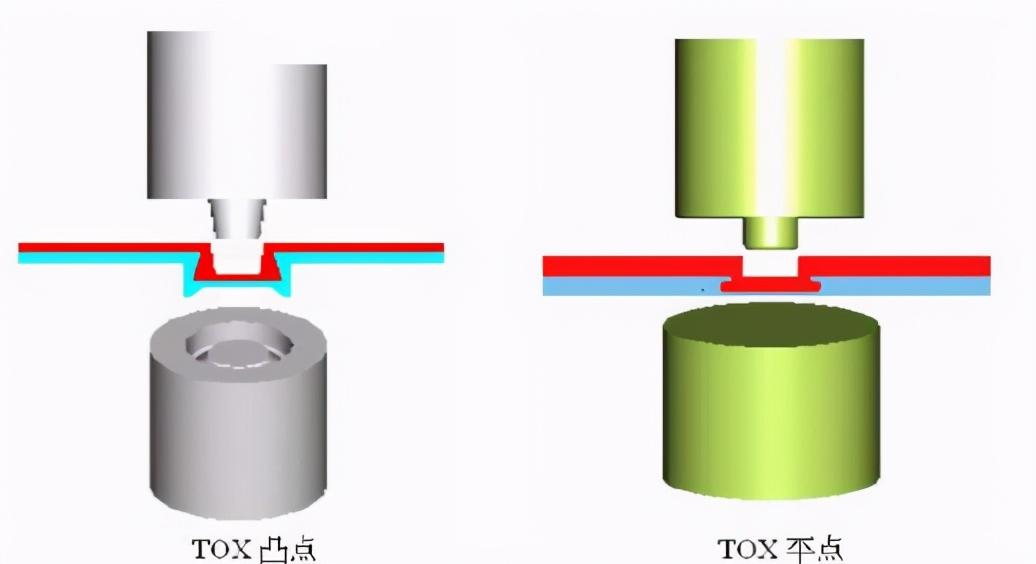
Pladebehandlingsteknologi - Overfladebehandling kan give korrosionsbeskyttelse og dekorative effekter på overfladen af plader. De almindelige overfladebehandlinger til metalplader omfatter pulversprøjtning, elektrogalvanisering, varmgalvanisering, overfladeoxidation, overfladetegning, screenprint osv.
Før overfladebehandling af plader, olie pletter, rust, svejseslag osv. skal fjernes fra overfladen af pladen.
Pulversprøjtning: Der er to typer overfladesprøjtning til plader: flydende og pulvermaling.Den almindeligt anvendte er pulvermaling.Ved sprøjtning pulver, elektrostatisk adsorption, høj temperatur bagning og andre metoder, et lag af forskellige farver af maling sprøjtes på overfladen af pladen for at forskønne udseendet og øge anti-korrosion ydeevne af materialet. Det er en almindeligt anvendt overfladebehandlingsmetode.
Bemærk: Der kan være en vis farveforskel i farverne sprøjtet af forskellige producenter, så plader af samme farve på det samme udstyr bør sprøjtes fra samme producent så meget som muligt.
2.Overfladevankning af galvaniseret og varmgalvaniseret plade er en almindeligt anvendt overfladebehandlingsmetode mod korrosion og kan spille en vis rolle i forskønnelse af udseendet. Galvanisering kan opdeles i elektrogalvanisering og varmgalvanisering.
Udseendet af elektrogalvanisering er relativt lys og flad, med et tyndt galvaniseret lag, som er almindeligt anvendt.
Hot-dip zink belægning er tykkere og kan producere et jern zink legering lag, som har stærkere korrosionsbestandighed end elektrogalvanisering.
3. Overflade oxidation: Dette introducerer hovedsageligt overflade anodisering af aluminium og aluminiumslegeringer.
Overfladen anodisering af aluminium og aluminiumslegeringer kan oxideres i forskellige farver, hvilket giver både beskyttende og dekorative effekter. Samtidig kan der dannes en anodisk oxidfilm på overfladen af materialet, som har høj hårdhed og slidstyrke samt gode elektriske isolerings- og varmeisoleringsegenskaber.
4. Overflade trådtegning: Placer materialet mellem de øverste og nedre ruller af trådtegningsmaskinen, med et sandbælte fastgjort til rullerne. Drevet af en motor, passerer materialet gennem de øverste og nedre sandbælter, efterlader mærker på overfladen af materialet. Tykkelsen af mærkerne varierer afhængigt af typen af sandbælte, og deres vigtigste funktion er at forskønne udseendet. Overfladebehandlingsmetoden til trådtrækning overvejes generelt for aluminiumsmaterialer.
5. Screen print er en proces med udskrivning af forskellige mærkninger på overfladen af materialer. Der er generelt to metoder: fladskærmsudskrivning og overførselsudskrivning. Fladskærmsudskrivning anvendes hovedsageligt på generelle flade overflader, men hvis der er dybere gruber, overførselsudskrivning er nødvendig.
Silke screen print kræver en silke form.
Referenceværktøj til nøjagtighed ved bearbejdning af plader:
GBT13914-2002 Dimensional tolerance for stemplede dele
GBT13915-2002-T stempling dele vinkeltolerance
GB-T15005-2007 Stemplede dele - Begrænsning af afvigelser uden specificerede tolerancer
GB-T 13916-2002 Stemplede dele - Form og position uden angivne tolerancer
Evnen af almindeligt anvendt pladebehandlingsudstyr og behandlingsområdet af almindeligt pladebehandlingsudstyr
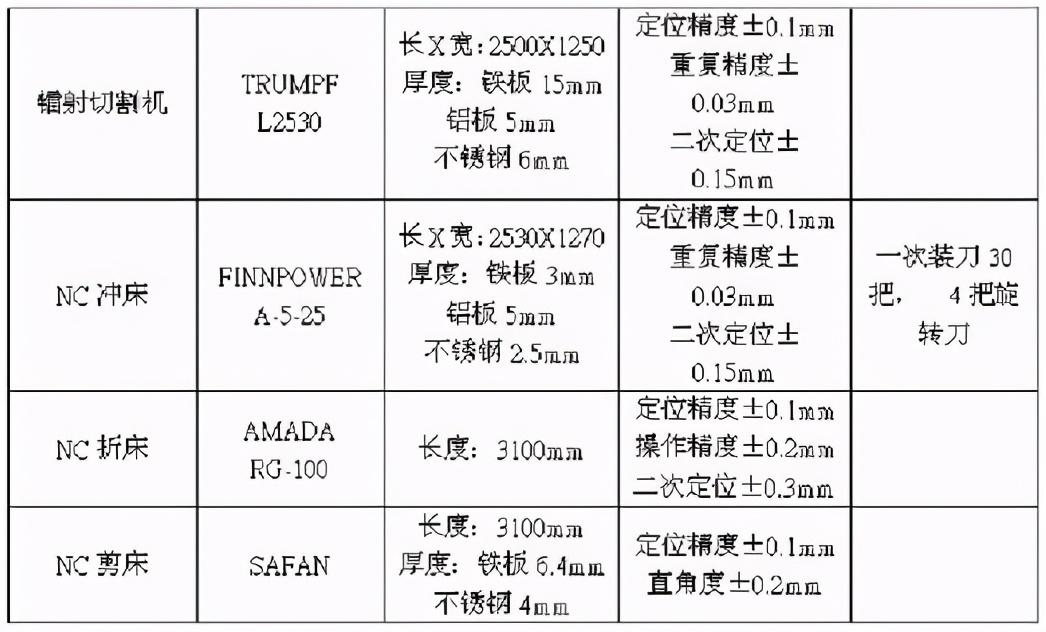