Im Handumdrehen bediene ich seit zehn Jahren eine CNC-Drehmaschine und habe einige Bearbeitungskenntnisse und Erfahrungen mit CNC-Drehmaschinen gesammelt und möchte mich mit meinen Kollegen austauschen. Aufgrund des häufigen Austauschs von bearbeiteten Teilen und begrenzten Werksbedingungen programmieren, prüfen, debuggen und fertigen wir die Bearbeitung von Teilen seit zehn Jahren selbst. Zusammenfassend können unsere operativen Fähigkeiten in die folgenden Punkte unterteilt werden. (Autor/Li Neng)
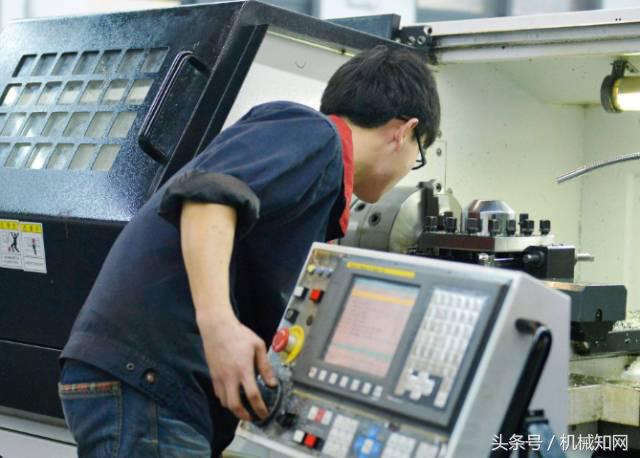
Programmierfähigkeiten: Aufgrund der hohen Präzisionsanforderungen unserer Fabrik für verarbeitete Produkte müssen die folgenden Faktoren bei der Programmierung berücksichtigt werden:
1. Bearbeitungsreihenfolge der Teile:
Bohren Sie zuerst und dann das Ende flach (dies soll Materialschrumpfung während des Bohrens verhindern);
Zuerst raues Auto, dann feines Auto (dies ist, um die Genauigkeit der Teile sicherzustellen);
Verarbeiten Sie zuerst diejenigen mit größeren Toleranzen und dann diejenigen mit kleineren Toleranzen (so wird sichergestellt, dass die Oberfläche der kleinen Toleranzgröße nicht zerkratzt wird und die Bauteilverformung verhindert wird).
2. Wählen Sie eine angemessene Geschwindigkeit, Vorschubgeschwindigkeit und Schnitttiefe basierend auf der Härte des Materials:
1) Wählen Sie Kohlenstoffstahlmaterialien mit hoher Geschwindigkeit, hoher Vorschubrate und großer Schnitttiefe. Zum Beispiel: 1Gr11, wählen Sie S1600, F0.2 und eine Schnitttiefe von 2mm;
2) Wählen Sie niedrige Geschwindigkeit, niedrige Vorschubrate und kleine Schnitttiefe für harte Legierungen. Zum Beispiel: GH4033, wählen Sie S800, F0.08 und eine Schnitttiefe von 0.5mm;
3) Titanlegierung sollte mit niedriger Geschwindigkeit, hoher Vorschubrate und kleiner Schnitttiefe ausgewählt werden. Wählen Sie beispielsweise für Ti6 S400, F0.2 und eine Schnitttiefe von 0,3mm. Am Beispiel der Bearbeitung eines bestimmten Teils: Das Material ist K414, ein sehr hartes Material. Nach mehreren Tests wurde es schließlich als S360, F0.1 und eine Schnitttiefe von 0.2 ausgewählt, um ein qualifiziertes Teil zu produzieren.
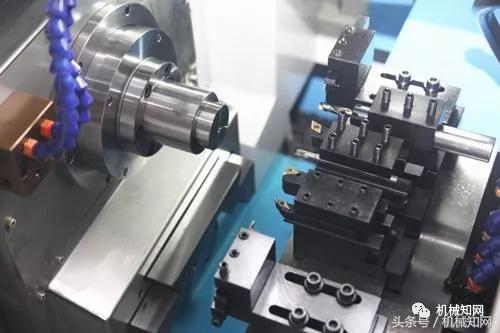
2,Die Messerausrichtung Technik ist unterteilt in Messerausrichtung Instrument und direkte Messerausrichtung. Die meisten Drehmaschinen in unserem Werk haben keine Werkzeugausrichtvorrichtung und erfordern eine direkte Werkzeugausrichtung. Die folgenden Werkzeugausrichttechniken beziehen sich auf die direkte Werkzeugausrichtung.
Wählen Sie zuerst die Mitte der rechten Stirnseite des Teils als Ausrichtungspunkt des Werkzeugs und legen Sie ihn als Nullpunkt fest. Nachdem die Werkzeugmaschine zum Ursprung zurückkehrt, wird jedes Werkzeug, das verwendet werden muss, mit der Mitte der rechten Stirnseite des Teils als Nullpunkt ausgerichtet. Wenn das Werkzeug mit der rechten Stirnfläche in Berührung kommt, geben Sie Z0 ein und klicken Sie auf die Messtaste. Der Kompensationswert des Werkzeugs zeichnet automatisch den Messwert auf, was anzeigt, dass die Z-Achse korrekt ausgerichtet ist. Die X-Achse dient zum Probeschneiden, und wenn Sie das Werkzeug verwenden, um den Außenkreis des Teils anzupassen, geben Sie x20 ein, um den Außenkreiswert des justierten Teils zu messen (z. B. x beträgt 20mm). Klicken Sie auf die Messtaste, und der Kompensationswert zeichnet automatisch den Messwert auf. An dieser Stelle wird auch die X-Achse korrekt ausgerichtet; Diese Werkzeugausrichtmethode, auch wenn die Werkzeugmaschine ausgeschaltet ist, ändert den Ausrichtwert nach dem Einschalten und Neustart nicht. Sie eignet sich für die Groß- und Langzeitfertigung desselben Teils, bei der die Drehmaschine nicht neu ausgerichtet werden muss.
3,3Debugging Fähigkeiten: Nach der Programmierung und Ausrichtung des Werkzeugs müssen die Teile getestet und debugged werden. Um Fehler in der Programm- und Werkzeugausrichtung zu vermeiden, die Kollisionsunfälle verursachen können, sollten wir zuerst Leerhub Simulation Bearbeitung durchführen. Im Koordinatensystem der Werkzeugmaschine sollte das Werkzeug nach rechts um 2-3 Mal die Gesamtlänge des Teils als Ganzes verschoben werden; Nachdem die Simulationsbearbeitung abgeschlossen ist, bestätigen Sie, dass das Programm und die Werkzeugausrichtung korrekt sind, und beginnen Sie dann mit der Bearbeitung der Teile. Nachdem das erste Stück des Teils bearbeitet wurde, überprüfen Sie selbst und bestätigen Sie, dass es qualifiziert ist, und suchen Sie dann einen speziellen Inspektor, um es zu überprüfen. Erst nachdem der dedizierte Inspektor bestätigt, dass es qualifiziert ist, kann das Debugging abgeschlossen werden.
4,Nachdem das erste Stück des Probeschneidens abgeschlossen ist, müssen die bearbeiteten Teile in Massenproduktion hergestellt werden. Jedoch bedeutet die Qualifizierung des ersten Stücks nicht, dass die gesamte Charge von Teilen qualifiziert sein wird, weil während der Verarbeitung verschiedene Verarbeitungsmaterialien Werkzeugverschleiß verursachen. Weiche Verarbeitungsmaterialien haben weniger Werkzeugverschleiß, während harte Verarbeitungsmaterialien schnelleren Werkzeugverschleiß haben. Daher ist es während der Verarbeitung notwendig, häufige Inspektionen durchzuführen und rechtzeitige Erhöhung oder Verringerung des Werkzeugausgleichswerts, um die Qualifizierung der Teile sicherzustellen.
Ein bestimmtes Teil als Beispiel ist das Bearbeitungsmaterial K414, mit einer Gesamtbearbeitungslänge von 180mm. Aufgrund des extrem harten Materials ist der Werkzeugverschleiß sehr schnell während der Bearbeitung. Vom Startpunkt bis zum Endpunkt wird eine leichte Abweichung von 10-20mm durch Werkzeugverschleiß erzeugt. Daher müssen wir manuell eine leichte Abweichung von 10-20mm im Programm hinzufügen, um die Qualifizierung des Teils sicherzustellen.
Kurz gesagt, das Grundprinzip der Verarbeitung besteht darin, zuerst die Maschine zu groben, überschüssiges Material vom Werkstück und dann die Präzisionsmaschine zu entfernen; Vibrationen sollten während der Verarbeitung vermieden werden; Es gibt viele Gründe, Vibrationen zu vermeiden, die durch thermische Verformung während der Werkstückbearbeitung verursacht werden, die auf übermäßige Belastung zurückzuführen sein kann; Es kann Resonanz zwischen der Werkzeugmaschine und dem Werkstück oder unzureichende Steifigkeit der Werkzeugmaschine sein, oder es kann durch Werkzeugpassivierung verursacht werden. Verringern Sie den seitlichen Vorschub und die Bearbeitungstiefe, überprüfen Sie, ob die Werkstückspannung sicher ist, erhöhen Sie die Werkzeuggeschwindigkeit, was Resonanz reduzieren kann, indem Sie die Geschwindigkeit senken. Überprüfen Sie zusätzlich, ob das Werkzeug durch ein neues ersetzt werden muss.
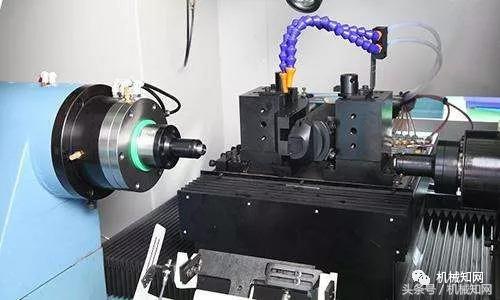
5,Die Erfahrung der Vermeidung von Kollisionen zwischen Werkzeugmaschinen stark schädigt die Genauigkeit von Werkzeugmaschinen, und der Einfluss variiert für verschiedene Arten von Werkzeugmaschinen. Im Allgemeinen hat es einen größeren Einfluss auf Werkzeugmaschinen mit schwacher Steifigkeit. So müssen bei hochpräzisen CNC-Drehmaschinen Kollisionen absolut ausgeschlossen werden. Solange der Bediener vorsichtig ist und bestimmte Anti-Kollision-Methoden beherrscht, können Kollisionen vollständig verhindert und vermieden werden.
Hauptgrund für Kollisionen:
Einer ist der Eingabefehler des Durchmessers und der Länge des Schneidwerkzeugs;
Zweitens gibt es Fehler bei der Eingabe der Abmessungen und anderer damit zusammenhängender geometrischer Abmessungen des Werkstücks sowie Fehler bei der Anfangsposition des Werkstücks;
Drittens ist das Werkstückkoordinatensystem der Werkzeugmaschine falsch eingestellt oder der Nullpunkt der Werkzeugmaschine wird während des Bearbeitungsprozesses zurückgesetzt, was zu Änderungen führt. Werkzeugmaschinenkollisionen treten meist während der schnellen Bewegung der Werkzeugmaschine auf, und die Gefahren solcher Kollisionen sind auch die größten, die unbedingt vermieden werden sollten.
Daher sollten Bediener besonders auf die Anfangsphase der Programmausführung und des Werkzeugwechsels achten. Wenn das Programm falsch bearbeitet wird oder Durchmesser und Länge des Werkzeugs falsch eingegeben werden, kann es zu Kollisionen kommen. Wenn in der Endphase des Programms die Abfolge der Rückziehaktion der CNC-Achse falsch ist, kann es auch zu Kollisionen kommen.
Um die oben genannten Kollisionen zu vermeiden, sollte der Bediener die Funktionen seiner Gesichtszüge beim Bedienen der Werkzeugmaschine voll nutzen, beobachten, ob anormale Bewegungen, Funken, Geräusche, abnormale Geräusche, Vibrationen oder verbrannte Gerüche auftreten. Wenn eine anormale Situation festgestellt wird, sollte das Programm sofort gestoppt werden. Die Werkzeugmaschine kann erst weiterarbeiten, nachdem das Bettproblem gelöst ist.
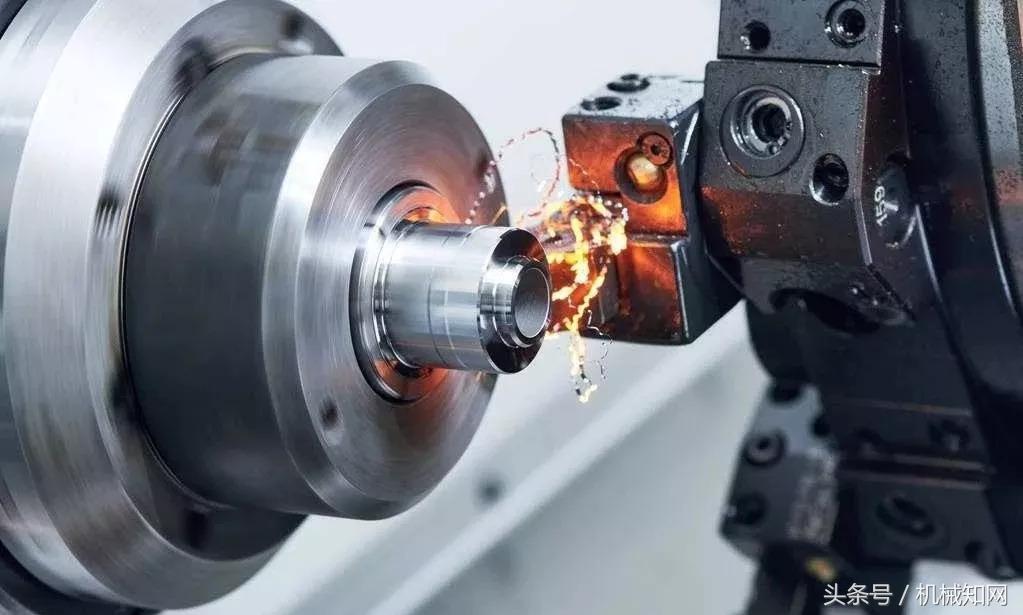
Kurz gesagt, die Beherrschung der Bedienfähigkeiten von CNC-Werkzeugmaschinen ist ein schrittweiser Prozess und kann nicht über Nacht erreicht werden. Es basiert auf der Beherrschung der grundlegenden Bedienung von Werkzeugmaschinen, grundlegenden Kenntnissen der mechanischen Bearbeitung und grundlegenden Programmierkenntnissen. Die Bedienfähigkeiten von CNC-Werkzeugmaschinen sind nicht festgelegt, sie erfordern, dass der Bediener seine Vorstellungskraft und Hands-on-Fähigkeit in einer organischen Kombination voll ausschöpft, die eine innovative Arbeit ist.