Die numerische Steuerdrehmaschine ist eine hochpräzise und hocheffiziente automatisierte Werkzeugmaschine. Die Verwendung der numerischen Steuerdrehmaschine kann die Verarbeitungseffizienz verbessern und mehr Wert schaffen. Das Aufkommen der numerischen Steuerdrehmaschine hat es Unternehmen ermöglicht, veraltete Bearbeitungstechnologie loszuwerden. Die Verarbeitungstechnologie der numerischen Steuerdrehmaschine ist ähnlich wie die der gewöhnlichen Drehmaschine. Da numerische Steuerdrehmaschine jedoch eine einmalige Spann- und kontinuierliche automatische Verarbeitung ist, um alle Drehprozesse abzuschließen, sollten die folgenden Aspekte beachtet werden.
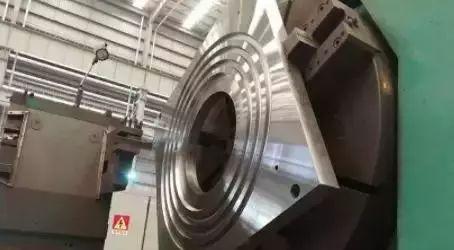
Schneidparameter sinnvoll wählen
Für eine effiziente Metallbearbeitung sind das zu bearbeitende Material, Schneidwerkzeuge und Schneidbedingungen die drei wichtigsten Elemente. Diese bestimmen die Bearbeitungszeit, Standzeit und Verarbeitungsqualität. Das wirtschaftlich wirksame Verarbeitungsverfahren muss eine vernünftige Wahl der Schneidbedingungen sein.
Die drei Elemente der Schneidbedingungen: Schnittgeschwindigkeit, Vorschub und Schnitttiefe verursachen direkt Werkzeugschäden. Mit zunehmender Schnittgeschwindigkeit steigt die Temperatur der Schneide an, was zu mechanischem, chemischem und thermischem Verschleiß führt. Eine Erhöhung der Schnittgeschwindigkeit um 20% reduziert die Standzeit um die Hälfte.
Der Zusammenhang zwischen Vorschubbedingungen und Werkzeugverschleiß tritt innerhalb eines sehr kleinen Bereichs auf. Aber mit einer großen Vorschubgeschwindigkeit steigt die Schnitttemperatur an und es kommt später zu erheblichem Verschleiß. Es hat weniger Einfluss auf das Schneidwerkzeug als die Schnittgeschwindigkeit. Obwohl der Einfluss der Schnitttiefe auf Schneidwerkzeuge nicht so signifikant ist wie die Schnittgeschwindigkeit und Vorschubgeschwindigkeit, erzeugt das zu schneidende Material beim Mikroschneiden eine gehärtete Schicht, die auch die Lebensdauer des Werkzeugs beeinflusst.
Benutzer müssen die Schnittgeschwindigkeit basierend auf dem zu verarbeitenden Material, Härte, Schneidzustand, Materialtyp, Vorschub, Schnitttiefe usw. wählen.
Die Auswahl der am besten geeigneten Verarbeitungsbedingungen basiert auf diesen Faktoren. Regelmäßiger und stabiler Verschleiß zur Erreichung der Lebensdauer ist die ideale Voraussetzung.
In der Praxis hängt die Wahl der Standzeit jedoch von Werkzeugverschleiß, Änderungen der bearbeiteten Abmessungen, Oberflächenqualität, Schneidgeräusch, Bearbeitungswärme und anderen Faktoren ab. Bei der Festlegung der Verarbeitungsbedingungen ist es notwendig, Untersuchungen auf der Grundlage der tatsächlichen Situation durchzuführen. Für schwer zu bearbeitende Materialien wie Edelstahl und hitzebeständige Legierungen können Kühlmittel oder Klingen mit guter Steifigkeit verwendet werden.
Wie die drei Elemente der Schneidbearbeitung zu bestimmen
Wie man diese drei Elemente richtig auswählt, ist ein Hauptinhalt des Kurses über Metallschneidprinzipien, und die Grundprinzipien für die Auswahl dieser drei Elemente sind:
(1) Schnittgeschwindigkeit (Liniengeschwindigkeit, Umfangsgeschwindigkeit) V (m/min)
Um die Spindeldrehungen pro Minute auszuwählen, muss zunächst die Schnittliniengeschwindigkeit V angegeben werden. Die Wahl des V hängt vom Werkzeugmaterial, Werkstückmaterial, Bearbeitungsbedingungen usw. ab.
Werkzeugmaterial:
Hartlegierung, V kann einen hohen Wert erreichen, im Allgemeinen über 100 Meter pro Minute, und technische Parameter werden normalerweise beim Kauf von Klingen bereitgestellt:
Wie viele Liniengeschwindigkeiten können bei der Bearbeitung welcher Materialien ausgewählt werden. Hochgeschwindigkeitsstahl: V kann nur auf einem relativ niedrigen Niveau erhalten werden, im Allgemeinen nicht mehr als 70 Meter pro Minute und in den meisten Fällen unter 20-30 Meter pro Minute.
Werkstückmaterial:
Hohe Härte, niedriger V-Wert; Gusseisen, mit einem niedrigen V-Wert, kann für Schneidwerkzeuge aus harter Legierung mit einer Geschwindigkeit von 70-80 Metern pro Minute verwendet werden; Kohlenstoffarmer Stahl kann einen V-Wert von über 100 Meter pro Minute haben, während Nichteisenmetalle einen höheren V-Wert (100-200 Meter pro Minute) haben können. Abgehärteter Stahl und Edelstahl sollten einen niedrigeren V-Wert haben.
Verarbeitungsbedingungen:
Grobbearbeitung, nehmen Sie einen niedrigeren V-Wert; Präzisionsbearbeitung mit einem höheren V-Wert. Das Steifigkeitssystem von Werkzeugmaschinen, Werkstücken und Schneidwerkzeugen ist schlecht, und V wird als niedrig genommen. Wenn das CNC-Programm S als Spindeldrehzahl pro Minute verwendet, dann sollte S (Spindeldrehzahl pro Minute) basierend auf dem Werkstückdurchmesser und der Schnittliniengeschwindigkeit V berechnet werden, wobei S=V (Schnittliniengeschwindigkeit) * 1000/(3.1416 Werkstückdurchmesser) verwendet wird. Wenn das CNC-Programm eine konstante Liniendrehzahl verwendet, kann S direkt die Schnittliniengeschwindigkeit V (Meter/Minute) verwenden.
(2) Vorschubrate (Vorschubrate)
F hängt hauptsächlich von den Oberflächenrauheitsanforderungen der Werkstückbearbeitung ab. Bei der Präzisionsbearbeitung sind die Oberflächenanforderungen hoch, und die Schneidmenge sollte klein sein: 0.06~0.12mm/spindel pro Umdrehung. Bei der Grobbearbeitung kann es größer sein. Es hängt hauptsächlich von der Stärke des Werkzeugs ab, die im Allgemeinen über 0.3 liegen kann. Wenn der Hauptharkwinkel des Werkzeugs groß ist, ist die Stärke des Werkzeugs schlecht, und die Vorschubgeschwindigkeit kann nicht zu groß sein. Darüber hinaus sollten auch die Leistung der Werkzeugmaschine und die Steifigkeit des Werkstücks und Schneidwerkzeugs berücksichtigt werden. Das CNC-Programm verwendet zwei Einheiten der Vorschubgeschwindigkeit: mm/min und mm/spindel pro Umdrehung. Die oben verwendeten Einheiten sind alle mm/Spindel pro Umdrehung. Wenn mm/min verwendet wird, kann die Formel verwendet werden, um sie umzurechnen: Vorschubgeschwindigkeit pro Minute=Vorschubgeschwindigkeit pro Umdrehung
(3) Schnitttiefe (Schnitttiefe)
Bei der Präzisionsbearbeitung ist es im Allgemeinen ratsam, einen Radiuswert von 0,5 oder weniger zu nehmen. Während der Grobbearbeitung wird es basierend auf dem Zustand des Werkstücks, des Werkzeugs und der Werkzeugmaschine bestimmt. Im Allgemeinen werden kleine Drehmaschinen (mit einem maximalen Bearbeitungsdurchmesser von 400mm oder weniger) verwendet, um 45-Stahl in einem normalisierten Zustand zu drehen, und die Tiefe des radialen Schneidwerkzeugs ist im Allgemeinen nicht mehr als 5mm. Darüber hinaus sollte beachtet werden, dass, wenn die Spindeldrehzahl der Drehmaschine eine gewöhnliche variable Frequenzdrehzahlregelung annimmt, wenn die Spindeldrehzahl pro Minute sehr niedrig ist (unter 100-200 Umdrehungen pro Minute), die Motorleistung erheblich abnimmt, und die Schnitttiefe und Vorschubgeschwindigkeit können zu diesem Zeitpunkt nur sehr wenig erreicht werden.
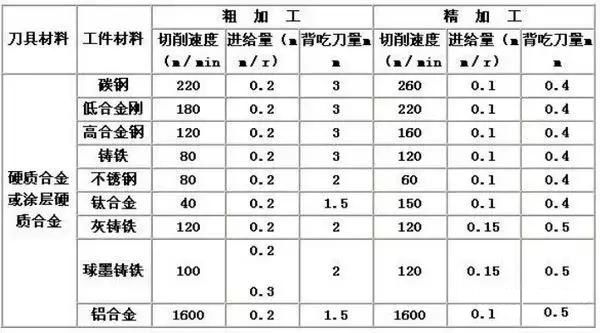
Angemessene Auswahl der Schneidwerkzeuge
Beim Grobdrehen ist es notwendig, Schneidwerkzeuge mit hoher Festigkeit und guter Haltbarkeit zu wählen, um die Anforderungen des großen Rückschnitts und des großen Vorschubs beim Grobdrehen zu erfüllen.
Bei der Präzisionsbearbeitung ist es notwendig, Werkzeuge mit hoher Präzision und guter Haltbarkeit zu wählen, um die erforderliche Bearbeitungsgenauigkeit zu gewährleisten.
Um die Werkzeugwechselzeit zu verkürzen und die Werkzeugausrichtung zu erleichtern, sollten maschinengespannte Messer und maschinengespannte Klingen so weit wie möglich verwendet werden.
Wählen Sie Armaturen vernünftig
1. Versuchen Sie, universelle Vorrichtungen zu verwenden, um Werkstücke zu spannen und vermeiden Sie die Verwendung spezieller Vorrichtungen;
2. Richten Sie die Positionierungsbenchmarks der Teile aus, um Positionierungsfehler zu reduzieren.
Bestimmen Sie den Verarbeitungsweg
Der Bearbeitungsweg bezieht sich auf die Bewegungsbahn und Richtung des Werkzeugs relativ zum Teil während des CNC-Bearbeitungsprozesses.
1. Es sollte in der Lage sein, die Bearbeitungsgenauigkeit und Oberflächenrauheitsanforderungen sicherzustellen;
2. Der Bearbeitungsweg sollte so weit wie möglich verkürzt werden, um die Standzeit des Werkzeugs zu reduzieren.
Das Verhältnis zwischen Bearbeitungsweg und Bearbeitungszulage
Derzeit sollte in Ermangelung einer weit verbreiteten Verwendung von CNC-Drehmaschinen eine übermäßige Zulage auf den Rohling, insbesondere die Zulage, die geschmiedete oder gegossene harte Hautschichten enthält, für die Verarbeitung auf gewöhnlichen Drehmaschinen im Allgemeinen angeordnet werden. Wenn es notwendig ist, eine CNC-Drehmaschine für die Bearbeitung zu verwenden, sollte auf die flexible Anordnung des Programms geachtet werden.
Wichtige Punkte für die Befestigung
Zur Zeit wird die Verbindung zwischen dem hydraulischen Spannfutter und dem hydraulischen Spannzylinder durch eine Zugstange erreicht. Die wichtigsten Punkte der hydraulischen Spannfutter-Klemmung sind wie folgt: zuerst verwenden Sie einen Griff, um die Mutter auf dem Hydraulikzylinder zu entfernen, entfernen Sie das Zugrohr und ziehen Sie es vom hinteren Ende der Spindel. Dann verwenden Sie einen Griff, um die Spannfutterbefestigungsschraube zu entfernen, um das Spannfutter zu entfernen.