1,1,Grund für Handrad Fehlfunktion:
1. Schlechter Kontakt des Handradwellenauswahlschalters
2. Schlechter Kontakt des Auswahlschalters der Handrad-Vergrößerung
3. Handradpuls tritt auf und die Scheibe ist beschädigt
4. Das Handrad Verbindungsdraht ist gebrochen
Lösung:
1. Geben Sie die Systemdiagnose ein und beachten Sie den entsprechenden Kontaktzustand des Achsenwahlschalters (der Zustand des Anschlussdrahtes ist intakt).
Der Schalter kann das Problem lösen
2. Geben Sie das System zur Diagnose ein und beachten Sie den entsprechenden Kontaktzustand des Vergrößerungsschalters (der Zustand des Anschlusskabels ist intakt). Wenn es beschädigt ist, ersetzen Sie es
Der Schalter kann das Problem lösen
3. Entfernen Sie die Impulsscheibe und messen Sie, ob die Stromversorgung normal ist und ob der Widerstand zwischen+und A,+und B normal ist. Bei Beschädigung
ersetzen
4. Geben Sie die Systemdiagnose ein und beobachten Sie die entsprechenden Kontaktbedingungen jedes Schalters.
Sind die Kontakte der Anschlussdrähte zwischen den Stanzplatten mit den entsprechenden Punkten der Eingangssystemklemmen offen oder geschlossen? Sind sie gebrochen, können sie ausgetauscht werden.
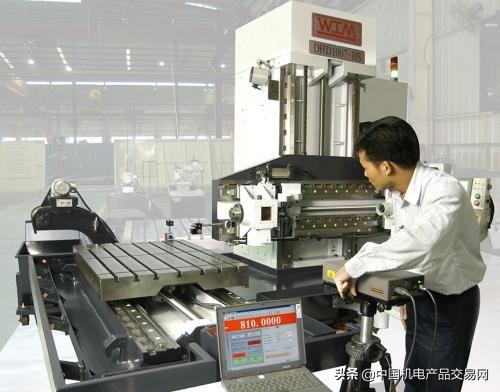
2,2Ursachen von Fehlern in X, Y, Z Achsen und Spindelgehäuse:
1. Die Y-Achse Schutzabdeckung ist deformiert und beschädigt
2. Die Y-Achse und Z-Achse Getriebelager sind beschädigt
3. Die Serverparameter entsprechen nicht den mechanischen Eigenschaften.
4. Die Verbindung zwischen dem Motor und dem Schraubenkopf ist verformt, mit verschiedenen Achsen
5. Die oberen und unteren Führungsschienen des schweren Hammers innerhalb der Säule sind lose und versetzt
6. Verschleiß und Vibration der Säulenhammer Kette und Führungsrad
7. Die Wellenrolle ist nicht parallel zur Motorendrolle
8. Der Spindelriemen ist beschädigt und verformt
Lösung:
1. Rücksendung des Schutzbleches
2. Überprüfen Sie die Haupt- und negativen Positionierlager der Welle, bestimmen Sie, welches Ende des Lagers beschädigt ist, und ersetzen Sie es
3. Passen Sie die Servoparameter an, um die Maschine anzupassen. (Servogewinn, Resonanzunterdrückung, Lastträgheit)
4. Kalibrieren Sie die Position des Steckers neu oder ersetzen Sie die Verbindung
5. Korrigieren Sie die Führungsschiene und schmieren Sie sie mit Butter
6. Überprüfen Sie den Verschleiß der Kette und des Führungsrades, korrigieren Sie das Gleichgewicht des schweren Hammers und schmieren Sie es mit Butter
7. Korrigieren Sie die Parallelität zwischen den beiden Riemenscheiben und kalibrieren Sie das dynamische Gleichgewichtsinstrument
8. Überprüfen Sie die Verformung und den schweren Schaden des Gurtes, ersetzen Sie es, reinigen Sie den Gurt und stellen Sie die Dichtigkeit des Gurtes ein.
Grund für Fehlfunktion der Führungsschienenölpumpe und der Schneidölpumpe:
1. Unzureichender Ölstand in der Führungsschienenölpumpe
2. Das Öldruckventil der Führungsschienenölpumpe ist beschädigt
3. Der Ölkreislauf der Werkzeugmaschine ist beschädigt
4. Der Filtersieb des Führungsschienenölpumpenkerns ist blockiert
5. Die Qualität des vom Kunden gekauften Führungsschienenöls übersteigt den Standard
6. Falsche Öleinspritzzeit Einstellung für Führungsschienenölpumpe
7. Der Leistungsschalter im Überlastungselektrischen Kasten der Schneidölpumpe ist ausgelöst
8. Luftleckage am Gelenk der Schneidölpumpe
9. Das Einwegventil der Schneidölpumpe ist beschädigt
10. Kurzschluss der Schneidölpumpe Motorspule
11. Schneiden des Ölpumpenmotors in entgegengesetzter Richtung
Lösung:
1. Einspritzen von Führungsschienenöl
2. Überprüfen Sie, ob das Öldruckventil unzureichenden Druck hat, und ersetzen Sie es, wenn es beschädigt ist
3. Überprüfen Sie, ob die Ölkreisläufe jeder Achse der Werkzeugmaschine ungehindert, gebrochen sind und ob der Ölaustrag beschädigt ist. Bei Beschädigung ersetzen
4. Reinigen Sie den Ölpumpenfilter Bildschirm
5. Ersetzen Sie das qualifizierte Führungsschienenöl, das die Anforderungen der Ölpumpe erfüllt
6. Setzen Sie die richtige Ölzeit zurück
7. Nachdem Sie überprüft haben, ob die Führungsschienenölpumpe intakt ist, stellen Sie den Kurzschluss wieder zurück
8. Finden Sie die undichte Verbindung und schließen Sie sie wieder an
9. Überprüfen Sie, ob das Einwegventil blockiert oder beschädigt ist, und ersetzen Sie es, wenn es beschädigt ist
10. Ersetzen Sie den Schneidölpumpenmotor, indem Sie die Motorspule testen
11. Korrigieren Sie die Richtung des Motors der Schneidölpumpe
4,4,Grund für Verarbeitungsfehler:
1. Falsche Kompensation für das Gegenspiel von X-, Y- und Z-Achsen
2. Der Haupteinsatzstreifen in X-, Y- und Z-Richtungen ist lose
3. Die X Y Z Lager sind beschädigt
4. Mechanische geometrische Genauigkeitsabweichung des Flugzeugkörpers
5. Axiale und radiale Bewegung der Hauptwelle
6. Unsachgemäße Einstellung der Systemservoparameter und der Verarbeitungsparameter
7. Programmierfehler beim Kunden
8. Verschleiß von X-, Y- und Z-Achsenschrauben und Muttern
Lösung:
1. Richtige Kalibrierung des Zifferblatts mit umgekehrtem Abstand
2. Passen Sie die Dichtigkeit jedes Achsen-Hauptstreifens an und beobachten Sie die Systemlast, um sie auf den optimalen Zustand einzustellen
3. Überprüfen Sie den Zustand der Lager und ersetzen Sie sie, wenn beschädigt
4. Verwenden Sie ein Marmorwinkellineal und einen Golfschläger, um die geometrische Genauigkeit jedes Artikels zu messen, z. B. Abweichungskorrektur
5. Reparieren Sie die Genauigkeit des Spindelinnenlochs und das Spiel der Spindellagerbewegung. Wenn es nicht repariert werden kann, ersetzen Sie es
6. Stellen Sie die Servopositionsschleife, Geschwindigkeitsschleifengewinn, Lastträgheitsverhältnis, Bearbeitungsgenauigkeitskoeffizient, Beschleunigungs- und Verzögerungszeitkonstante ein
7. Programmierungsprozesse optimieren und anpassen
8. Verwenden Sie ein Laserinterferometer, um den Spalt zwischen den Schrauben auszugleichen
5,Grund für lose Klinge Fehlfunktion:
1. Das Lösemesser Magnetventil ist beschädigt
2. Der Spindelschneidzylinder ist beschädigt
3. Beschädigte Spindelfederplatte
4. Die Spindelklaue ist beschädigt
5. Unzureichende Gasversorgung der Kunden
6. Schlechter Kontakt des lösenden Messerknopfes
7. Leitungsbruch
8. Der Ölbecher des Messerzylinders ist kurz an Öl
9. Der Griff des Kunden Latin entspricht nicht den erforderlichen Spezifikationen
Lösung:
1. Überprüfen Sie den Betrieb des Magnetventils und ersetzen Sie es, wenn es beschädigt ist
2. Überprüfen Sie die Wirkung des Messerzylinders, ersetzen Sie es, wenn es beschädigt ist
3. Überprüfen Sie den Grad der Beschädigung der Federplatte und ersetzen Sie sie
4. Überprüfen Sie, ob die Spindelklaue intakt, beschädigt oder verschlissen ist, und ersetzen Sie sie
5. Überprüfen Sie den Grad der Beschädigung der Taste und ersetzen Sie sie, wenn sie beschädigt ist
6. Überprüfen Sie, ob der Stromkreis gebrochen ist
7. Füllen Sie den Ölbecher des Messerzylinders mit Öl
8. Installation in Übereinstimmung mit Standard Latein
6,Grund, warum die Werkzeugmaschine nicht auf Null zurückkehren kann:
1. Der Kontakt des Ausgangsschalters bleibt stecken und kann sich nicht bewegen
2. Der Ursprungsblock kann den Ursprungsschalter nicht in die Schalterwerksposition drücken
3. Wassereintritt in den Ausgangsschalter verursacht schlechten Kontakt zwischen den Schalterkontakten
4. Der Ursprungsschalter wird getrennt oder die Eingangssignalquelle ist fehlerhaft
5. SPS-Eingangspunkt ausgebrannt
Gegenmaßnahmen:
1. Reinigen Sie den festsitzenden Bereich, um eine reibungslose Bewegung seiner beweglichen Teile sicherzustellen, oder ersetzen Sie den Fahrschalter
2. Stellen Sie die Einbauposition des Fahrschalters so ein, dass der Nullpunktschalterkontakt durch den Stopper glatt in die Schalterwerksposition gedrückt werden kann
3. Ersetzen Sie den Reiseschalter und ergreifen Sie wasserdichte Maßnahmen
4. Überprüfen Sie, ob es offene oder Kurzschlüsse im Schaltkreis gibt und ob es eine Signalquelle gibt (+24V DC Netzteil)
5. Ersetzen Sie die Eingangspunkte auf der I/O-Platine, stellen Sie die Parameter ein und ändern Sie das SPS-Programm
7,Unter normalen Umständen tritt der positive und negative harte Grenzalarm der Werkzeugmaschine nicht auf. Es kann auftreten, wenn die Werkzeugmaschine vor der Rückkehr zu Null betrieben wird, da das System nicht zu Null zurückkehrt
Es gibt kein festes mechanisches Koordinatensystem, sondern willkürliche Positionierung, und die weiche Grenze ist ungültig, so dass es notwendig ist, auf Null zurückzukehren, bevor die Werkzeugmaschine betrieben wird
Grund:
1. Der Kontakt des Reiseschalters wird gedrückt und geklebt (über Reise)
2. Der Fahrschalter ist beschädigt
3. Es gibt einen offenen Stromkreis, Kurzschluss und keine Signalquelle in der Fahrschalter-Schaltung
4. Der Endblock kann den Schalterkontakt nicht in die Aktionsposition drücken
5. SPS-Eingangspunkt ausgebrannt
Gegenmaßnahmen:
1. Schütteln Sie das Handrad manuell oder manuell von der sicheren Position weg oder reinigen Sie die Schalterkontakte
2. Ersetzen Sie den Fahrschalter
3. Überprüfen Sie, ob sich ein Kurzschluss im Fahrschalter befindet. Wenn es einen Kurzschluss gibt, verarbeiten Sie ihn erneut. Überprüfen Sie die Signalquelle (+24V DC Netzteil)
4. Stellen Sie die Einbauposition des Fahrschalters so ein, dass er auf den Schalterkontakt normalerweise in die Aktionsposition gedrückt werden kann
5. Ersetzen Sie die Eingangspunkte auf der I/O-Platine und nehmen Sie Parametereinstellungen vor, ändern Sie das SPS-Programm
8,8,Grund für Werkzeugwechsel Fehlfunktion:
1. Unzureichender Luftdruck
2. Schlechter Kontakt oder offener Kreislauf des losen Messerknopfes
3. Loser Messerknopf PLC Eingang Adresspunkt ausgebrannt oder keine Signalquelle (+24V)
4. Das lose Messerrelais funktioniert nicht
5. Das Lösemesser Magnetventil ist beschädigt
6. Unzureichende Schnittmenge
7. Der Ölbecher des Messerzylinders ist kurz an Öl
8. Fehlfunktion des Messerzylinders
Gegenmaßnahmen:
1. Überprüfen Sie den Luftdruck, bis er 6 Kilogramm plus oder minus 1 Kilogramm erreicht
2. Ersetzen Sie den Schalter oder überprüfen Sie die Schaltung
3. Ersetzen Sie den PLC-Eingangsport auf der I/O-Platine oder überprüfen Sie die PLC-Eingangssignalquelle, ändern Sie das PLC-Programm
4. Überprüfen Sie das Vorhandensein/Fehlen von SPS-Ausgangssignalen, ob der SPS-Ausgangsport ausgebrannt ist, und ändern Sie das SPS-Programm
5. Wenn die Magnetventilspule ausgebrannt und ersetzt wird und der Magnetventilkörper Luft ausläuft oder der Kolben sich nicht bewegt, ersetzen Sie dann den Ventilkörper
6. Stellen Sie die Schnittmenge ein, um ein reibungsloses Lösen der Klinge zu gewährleisten
7. Fügen Sie Hydrauliköl zum Ölbecher des Schneidzylinders hinzu
Wenn die Schrauben im Messerzylinder lose oder undicht sind, müssen die Schrauben erneut angezogen und der Dichtungsring im Zylinderkörper ausgetauscht werden.
Wenn es nicht repariert werden kann, ersetzen Sie den Messerzylinder
9,9,Grund für anormalen Klang während des Drei-Achsen-Betriebs:
1. Lagerstörung
2. Die Schraubschiene und die Führungsschiene sind unausgewogen
3. Starker Verschleiß der verschleißfesten Platte führt zu starken Kratzern auf der Führungsschiene
4. Ungleichmäßiger Servomotor Verstärkung
Gegenmaßnahmen:
1. Ersetzen Sie das Lager
2. Korrigieren Sie die Führungsschraube Sammelschiene
3. Befestigen Sie die verschleißfeste Platte erneut, und wenn die Schiene stark zerkratzt ist, muss sie wiederverarbeitet werden
4. Passen Sie die Servogewinnparameter an, um den mechanischen Spezifikationen zu entsprechen
10,Grund für Schmierfehler:
1. Der Öltank der Schmierpumpe ist kurz von Öl
2. Die Schmierpumpe hat eine kurze Ölzeit
3. Der Druckentlastungsmechanismus der Schmierpumpe gibt Druck zu schnell frei
4. Es gibt Ölleckage im Ölrohr und Ölkreislauf
5. Das Einwegventil im Ölkreislauf funktioniert nicht
6. Beschädigter Motor der Ölpumpe
7. Die Steuerplatine der Schmierpumpe ist beschädigt
Gegenmaßnahmen:
1. Schmieröl zur oberen Grenzlinienposition hinzufügen
2. Passen Sie die Ölzeit auf 32 Minuten und ölen für 16 Sekunden an
Wenn die einstellbare Druckentlastungsgeschwindigkeit eingestellt werden kann, muss sie ersetzt werden, wenn sie nicht eingestellt werden kann
4. Überprüfen Sie die Ölrohr- und Ölkreisschnittstelle und behandeln Sie sie richtig
5. Ersetzen Sie das Einwegventil
6. Ersetzen Sie die Schmierpumpe
7. Ersetzen Sie die Steuerplatine
Wenn in einer Notsituation M64S in der I/F-Diagnose auf 1A und E60 bis 32 erzwingen, und die Werkzeugmaschine kann vorübergehend arbeiten
11,Das Programm kann nicht übertragen werden, was zu Alarmen P460, P461 und P462 führt.
1. Überprüfen Sie auf offene Schaltungen oder virtuelles Löten in der Übertragungsleitung und stellen Sie sicher, dass der Stecker richtig eingesteckt ist
2. Die Parameter auf der Computerübertragungssoftwareseite sollten mit denen auf der Werkzeugmaschinenseite übereinstimmen
3. Ersetzen Sie den Computer und versuchen Sie zu übertragen
4. Ist die Erdung stabil
12,Grund für Messermagazin Problem:
1. Plötzlicher Stopp während des Werkzeugwechselprozesses, nicht in der Lage, Werkzeugwechsel fortzusetzen
2. Das konische Hut Stil Messermagazin kann nicht herauskommen
3. Lösen Sie das Messer während des Werkzeugwechsels nicht
4. Der Schneidkopf kann sich nicht drehen
5. Die plötzliche Umdrehung des Schneidkopfes verursacht einen Unterschied der halben Messerposition
6. Beim Wechsel des Messers gibt es einen Alarm für lose oder enge Messerfehler
Bei der Rückgabe des Werkzeugs während des Austauschvorgangs gibt es ein lautes Geräusch auf der Spindelseite
8. Nach dem Austausch kann die Spindel nicht für die Werkzeuginstallation verwendet werden (abnormales Lösen des Werkzeugs)
Gegenmaßnahmen:
1. Ist der Luftdruck ausreichend (6 Kilogramm)
2. Überprüfen Sie, ob das umgekehrte Signal des Werkzeugmagazins vorhanden ist und ob es irgendeinen Ausgang von der elektromagnetischen Ventilschaltung und SPS für den Ein- und Ausgang des Werkzeugmagazins gibt
3. Stellen Sie die Schneidmenge ein und überprüfen Sie, ob sich Wasser im Schneidzylinderkörper ansammelt
4. Wenn sich der Schneidkopf nach dem Herauskommen dreht, überprüfen Sie auf einen offenen Stromkreis im Netzkabel des Magazinmotors und auf Schäden an den Kontakten oder Relais
5. Der Bremsmechanismus des Messermagazinmotors ist locker und kann nicht normal bremsen
6. Überprüfen Sie den Luftdruck, ob der Zylinder voll aktiviert ist (ob es Wasseransammlung gibt), und ob der Löseschalter an Ort und Stelle gedrückt wird, aber nicht zu viel (vorausgesetzt, es gibt nur einen Signaleingang)
7. Stellen Sie die Schnittmenge ein;
8. Ändern Sie das Werkzeugwechselprogramm (Makro-Programm O9999)
13,9,Grund für Werkzeugmaschine nicht in der Lage, einzuschalten:
1. Schlechter dreiphasiger Kontakt oder beschädigter Schalter des Hauptstromschalters
2. Das Bedienfeld kann nicht eingeschaltet werden
Gegenmaßnahmen:
1. Ersetzen Sie den Hauptschalter
2. Überprüfen
A. Hat das Schalternetzteil Spannungsausgang (+24V)
B. Der Einschaltschalter des Systems hat schlechten Kontakt, und der Ausschaltschalter wird getrennt
C. Die Leistung des Systems auf Relais hat schlechten Kontakt und kann sich nicht selbst sperren
D. Zeilenumbruch
E. Antriebsleistung am Wechselstromkontakt, Systemleistung am Relais fehlerhaft
F. Tritt der Leistungsschalter aus
G. Funktioniert das System ordnungsgemäß? Ist die Vorbereitung abgeschlossen oder ist der Z-Achs-Treiber beschädigt? Gibt es keine automatische Stromversorgung am Signalausgang
14,9Kühlwasserpumpe Fehlfunktion 1. Überprüfen Sie, ob die Wasserpumpe ausgebrannt ist
2. Ist die Leistungsphasenfolge umgekehrt
3. Überprüfen Sie auf verbrannte Kommunikationskontakte und Relais
4. Gibt es ein Eingangssignal für den Panel-Tastenschalter
15,Blasfehler 1. Überprüfen Sie, ob das Magnetventil arbeitet
2. Überprüfen Sie, ob das Blasrelais aktiviert ist
3. Gibt es irgendwelche Signale von den Bedienfeldtasten und der SPS-Ausgangsschnittstelle