Bei der Verwendung der Shenyang Laserschneidmaschine zum Schneiden von Blechen treten häufig verschiedene Probleme auf. Um die Schnittqualität sicherzustellen, sind die folgenden häufigen Probleme und gemeinsame Lösungen:
1. Schneid- und Perforationstechnik:
Jede thermische Schneidtechnik, mit Ausnahme einiger Fälle, in denen sie von der Kante des Brettes beginnen kann, erfordert im Allgemeinen ein kleines Loch, das durch das Brett gebohrt wird. Früher wurde auf Laser-Stanzmaschinen ein Loch zuerst mit einem Stanz ausgestanzt, und dann mit dem Laser begann man mit dem Schneiden aus dem kleinen Loch. Es gibt zwei grundlegende Methoden für das Stanzen von Laserschneidmaschinen ohne Stanzgeräte:
Nach kontinuierlicher Laserbestrahlung wird im Kern des Materials eine Grube gebildet, und dann wird das geschmolzene Material schnell durch einen Sauerstoffstrom koaxial mit dem Laserstrahl entfernt, um ein Loch zu bilden. Die Größe des allgemeinen Lochs hängt von der Dicke der Platte ab, und der durchschnittliche Durchmesser der Strahlplochung ist die Hälfte der Plattendicke. Daher für dickere Platten, ist der Strahlplochdurchmesser größer und nicht rund, und es ist nicht geeignet für den Einsatz auf Teilen mit hohen Verarbeitungsgenauigkeitsanforderungen. Es kann nur auf Abfallmaterialien verwendet werden. Darüber hinaus kommt es aufgrund des gleichen Sauerstoffdrucks, wie beim Schneiden, zu einem größeren Spritzer.
Pulsperforationsbohrung mit Pulslaser mit hoher Spitzenleistung, um eine kleine Menge Material zu schmelzen oder zu verdampfen, üblicherweise unter Verwendung von Luft oder Stickstoff als Hilfsgas, um die Lochexpansion aufgrund exothermer Oxidation zu reduzieren, und der Gasdruck ist niedriger als der Sauerstoffdruck während des Schneidens. Jeder Pulslaser erzeugt nur kleine Partikelstrahlen, die allmählich tiefer eindringen, so dass die Perforationszeit für dicke Platten einige Sekunden dauert. Sobald die Perforation abgeschlossen ist, ersetzen Sie sofort das Hilfsgas durch Sauerstoff zum Schneiden. Auf diese Weise ist der Perforationsdurchmesser kleiner und die Perforationsqualität ist besser als die der Strahlenperforation. Der dafür verwendete Laser sollte nicht nur eine hohe Ausgangsleistung haben; Noch wichtiger ist, dass die zeitlichen und räumlichen Eigenschaften des Strahls wichtig sind, so dass transversale Strömungs-CO2-Laser im Allgemeinen die Anforderungen des Laserschneidens nicht erfüllen können. Darüber hinaus erfordert die Pulsperforation eine zuverlässige Gaswegregelung, um das Umschalten von Gasarten und Drücken sowie die Steuerung der Perforationszeit zu erreichen.
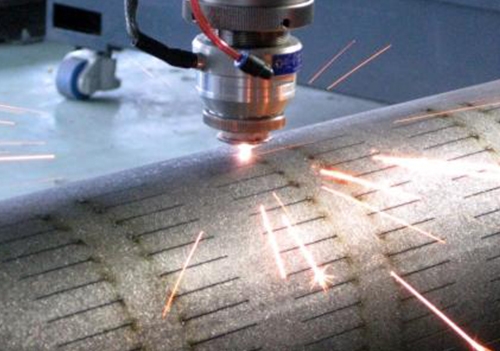
Bei der Verwendung der Pulsperforation ist zur Erzielung hochwertiger Schnitte die Übergangstechnik von der Impulsperforation im stationären Zustand zum kontinuierlichen Schneiden des Werkstücks mit konstanter Geschwindigkeit ernst zu nehmen. Theoretisch ist es normalerweise möglich, die Schneidbedingungen des Beschleunigungsabschnitts, wie Brennweite, Düsenposition, Gasdruck usw., zu ändern, aber in der Praxis ist die Möglichkeit, diese Bedingungen aufgrund der kurzen Zeit zu ändern, unwahrscheinlich. In der industriellen Produktion ist es praktischer, hauptsächlich die Methode zur Änderung der durchschnittlichen Laserleistung zu verwenden, insbesondere durch Änderung der Pulsbreite; Pulsfrequenz ändern; Gleichzeitige Änderung der Pulsbreite und Frequenz. Die tatsächlichen Ergebnisse zeigen, dass der dritte Effekt sehr gut sein wird.
2. Analyse der Verformung kleiner Löcher (Durchmesser klein und Plattendicke) während des Schneidens und der Verarbeitung:
Dies liegt daran, dass Werkzeugmaschinen (nur für Hochleistungslaserschneidemaschinen) bei der Bearbeitung kleiner Löcher keine explosive Perforation verwenden, sondern Pulsperforation (weiche Punktion), die die Laserenergie auf einem kleinen Bereich zu konzentriert macht, auch den nicht bearbeiteten Bereich verbrennt, Verformung des Lochs verursacht und die Verarbeitungsqualität beeinträchtigt. An diesem Punkt sollten wir die Pulsperforationsmethode (weiche Punktion) in die Strahlenperforationsmethode (gewöhnliche Punktion) im Verarbeitungsprogramm ändern, um das Problem zu lösen. Bei kleineren Leistungsschneidmaschinen ist das Gegenteil der Fall: Bei der Bearbeitung kleiner Löcher sollte eine Pulsperforation verwendet werden, um eine bessere Oberflächenglätte zu erzielen.
Der Inhalt des Artikels stammt aus dem Internet. Wenn Sie Fragen haben, kontaktieren Sie mich bitte, um ihn zu löschen!