Da die meisten inländischen Stanzformhersteller kleine und mittlere Unternehmen sind und ein geeigneter Teil dieser Unternehmen sich noch in der traditionellen Produktionsmanagementphase im Werkstattstil befindet, vernachlässigen sie oft die Stabilität von Formen, was zu langen Formentwicklungszyklen und hohen Produktionskosten führt, die das Tempo der Unternehmensentwicklung stark einschränken.
Wie bekannt, umfassen die Metallmaterialien, die in Stanzformen verwendet werden, viele Sorten, und die Anforderungen und Auswahlkriterien für ihre Materialien sind auch aufgrund der unterschiedlichen Auswirkungen verschiedener Teile in der Form unterschiedlich. Daher ist die vernünftige Auswahl von Formmaterialien zu einer der sehr wichtigen Aufgaben im Formenbau geworden.
Bei der Auswahl von Formmaterialien ist es neben der Anforderung, dass das Material eine hohe Festigkeit, hohe Verschleißfestigkeit und angemessene Zähigkeit aufweist, auch notwendig, die Eigenschaften und Produktionsanforderungen des verarbeiteten Produktmaterials vollständig zu berücksichtigen, um die Stabilitätsanforderungen der Formgebung zu erreichen.
Im praktischen Betrieb neigen Formenbauer dazu, Formenmaterialien basierend auf persönlichen Erfahrungen auszuwählen, was oft zu instabiler Formenbildung aufgrund einer falschen Materialauswahl von Formenteilen beim Stanzen führt. Es ist erwähnenswert, dass während des Stanzprozesses jede Art von Stanzblatt ihre eigene chemische Zusammensetzung, mechanische Funktion und charakteristische Werte hat, die eng mit der Stanzfunktion zusammenhängen.Die Instabilität der Stanzmaterialfunktion, Schwankungen in der Stanzmaterialdicke und Änderungen im Stanzmaterial beeinflussen nicht nur direkt die Genauigkeit und Qualität der Stanzverarbeitung, sondern können auch zu Schäden an Stanzformen führen.
Um das Problem der Formstabilität zu lösen, ist es notwendig, von den folgenden Aspekten streng zu kontrollieren:
1. In der Prozessplanungsphase können durch die Analyse des Produkts potenzielle Fehler, die während der Produktion auftreten können, vorhergesagt werden, und dann kann ein stabiler Produktionsprozessplan entwickelt werden;
2. Einführung der Standardisierung der Produktionsprozesse und Produktionstechniken;
3. Eine Datenbank aufbauen und kontinuierlich zusammenfassen und optimieren; Mit Hilfe des CAE-Analysesoftware-Systems erhalten Sie den optimalen Lösungsplan.
Dieser Artikel stammt von EMAR Mold Co., Ltd. Für weitere Informationen zu EMAR klicken Sie bitte auf www.sjt-ic.com,
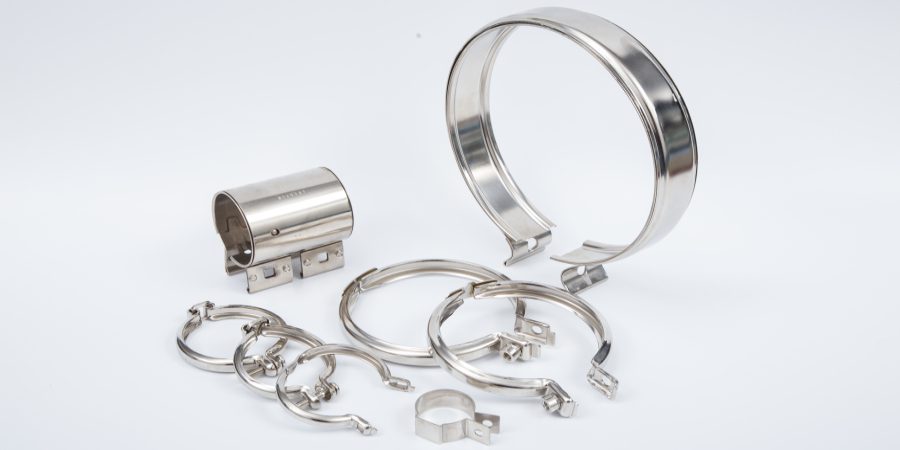