Für Unternehmen, die in der Präzisionsbearbeitung tätig sind, sollte klar sein, dass die Prozessspezifikation das wichtigste technische Dokument für die Verarbeitung von Luftfahrtkomponenten ist. Es spezifiziert den Prozess und die Summe der Verarbeitung von Rohstoffen in qualifizierte Teile. Im Allgemeinen enthält der Inhalt des Prozessspezifikationsprozessdiagramms Ausrüstungsinformationen, Prozessausrüstungsinformationen, Verarbeitungsanforderungen und Betriebsschritte. Produktionsoperatoren müssen die Teile nur gemäß der Reihenfolge des Prozessdiagramms in der Prozessspezifikation und dem Inhalt in der Prozesskarte verarbeiten, um die Rohstoffe zu Produkten zu verarbeiten, die den Konstruktionszeichnungen von Tonghu entsprechen.
Mit der Aktualisierung und Iteration von Flugzeugmotoren verbessern sich die Energie und Zuverlässigkeit der Triebwerke allmählich. Ein einziges helles Schwert hat mehr Funktionen, und die Struktur der Teile wird immer komplexer. Auch die Präzision, die für die Konstruktion erforderlich ist, steigt von Jahr zu Jahr. Das traditionelle Prozessspezifikationsmodell reicht nicht mehr aus, um die Konstruktionsanforderungen von Motorkomponenten sowie die Produktionsanforderungen an hohe Effizienz, hohe Qualität und niedrige Kosten zu erfüllen. Es eignet sich auch nicht für CNC-Bearbeitung und Informationsmanagement. Die Erforschung neuer Prozessspezifikationsmodelle und die Verbesserung der aktuellen Prozessspezifikationssituation sind wichtige Themen, die viele Motorkomponenten-Bearbeitung und technisches Personal berücksichtigen müssen.
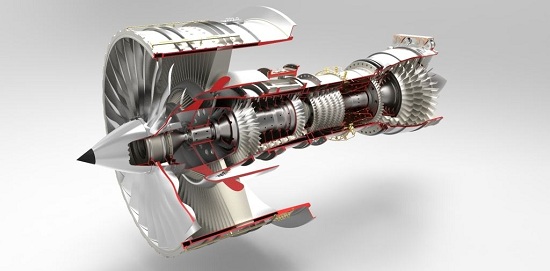
1,Analyse des aktuellen Status der Regelungen zur Bauteilverarbeitung
Die traditionelle Art der Prozessspezifikation ist sehr einfach, und die Arbeitsschritte sind nicht detailliert genug. Es gibt viele unsichere Faktoren, die das Baupersonal nicht gut führen können. Verschiedene Betreiber haben unterschiedliche Einführungen in den Inhalt der Prozessspezifikation. Die Produktqualität und Verarbeitungseffizienz hängen hauptsächlich vom Betreiber ab. Verglichen mit dem internationalen fortschrittlichen Flugzeugtriebwerksprozessspezifikationsmodus, ist die Lücke immer noch ziemlich offensichtlich.
In der Prozessspezifikation hat jeder Bearbeitungsschritt ein entsprechendes Prozessdiagramm. Die traditionelle Art des Prozessdiagramms ist relativ einfach. Das Prozessdiagramm enthält hauptsächlich das schematische Diagramm der Teilebearbeitung, den Arbeitsinhalt, die Anzahl der Spannformen, Schneidwerkzeuge, die verwendeten Messwerkzeuge, die Größe und die technischen Anforderungen, die nach der Verarbeitung erfüllt werden sollten, und die Angelegenheiten, die beachtet werden müssen. Abbildung 1 ist ein Diagramm des Drehprozesses. Die Skizze links ist ein schematisches Diagramm des Bearbeitungsprozesses, normalerweise durch eine zweidimensionale Ansicht dargestellt. Die dicke Volllinie stellt die Oberfläche dar, die bearbeitet werden muss, die dünne Volllinie stellt die nicht bearbeitete Oberfläche dar, und die Großbuchstaben A, B, C usw. stellen die Positionierungsreferenz, Stützfläche, Spann- oder Pressfläche des Teils dar. Im schematischen Diagramm werden Maßlinien verwendet, um die Maß- und Lagetoleranzen anzuzeigen, die nach Fertigstellung der bearbeiteten Oberfläche gewährleistet werden sollen. Jede Dimension und Lagetoleranz ist mit einer Sequenznummer gekennzeichnet. Die Spalte mit Auftragsinhalt auf der rechten Seite besteht normalerweise aus drei Teilen. Im ersten Teil geht es um die Ausrichtungsanforderungen vor der Bearbeitung. Normalerweise muss die Ausrichtungsvorrichtung die Oberfläche, die radiale Oberfläche und die axiale Oberfläche des Teils lokalisieren und den maximal zulässigen Auslaufwert angeben. Die zweite ist der Inhalt der Drehbearbeitung in diesem Prozess, in der Regel durch Größenfolgenummern dargestellt, die den Sequenznummern im Bearbeitungsdiagramm entsprechen; Die dritte ist die Anforderung an Form- und Lagetoleranzen nach dem Drehen, die der Sequenznummer im Bearbeitungsdiagramm entspricht.
1. Aktueller Stand der Verfahrensspezifikationen
Jeder Bearbeitungsprozess in der Prozessspezifikation hat ein entsprechendes Prozessdiagramm. Die traditionelle Art des Prozessdiagramms ist relativ einfach. Das Prozessdiagramm enthält hauptsächlich das Bearbeitungsschematische Diagramm und den Arbeitsinhalt der Komponenten, die Vorrichtungen, Formen, Schneidwerkzeuge, Messwerkzeuge usw., die verwendet werden, die Abmessungen und technischen Anforderungen, die nach Abschluss der Bearbeitung erfüllt werden sollten, und die wichtigsten Punkte, die beachtet werden müssen.
2. Analyse des aktuellen Status der Verfahrensvorschriften
1) Vorbereitungsanalyse vor der Verarbeitung
Vor der Verarbeitung lesen Bediener normalerweise die Prozesstabelle. Wenn es sich um einen CNC-Bearbeitungsprozess handelt, müssen sie auch die CNC-Schrittkarte lesen. Arbeiter bereiten die Prozessausrüstung gemäß dem Prozessdiagramm vor. Für die allgemeine Prozessausrüstung, die in dem Prozess verwendet wird, da die meisten Prozessdokumente keine klaren Bestimmungen haben, bereiten sich die Arbeiter basierend auf ihren eigenen Erkenntnissen und Erfahrungen und den bestehenden Prozessausrüstungsbedingungen in der Produktionswerkstatt vor. Bei der Auswahl allgemeiner Schneidwerkzeuge können die Arbeiter unklar über die Schneidleistung von Teilen und Werkzeugmaterialien sein und können durch die Werkzeugreserven der Produktionswerkstatt begrenzt werden. Arbeiter können Werkzeuge willkürlich wählen, und die ausgewählten Materialien und instabilen geometrischen Abmessungen können abweichen. Die verwendeten Parameter können unangemessen sein, in der Genauigkeit und Qualität der Teile resultieren. Ungenaue Werkzeugverbrauchsstatistiken erschweren die Vorbereitung und Umsetzung von Produktionsplänen. Ebenso können bei der Wahl von Messwerkzeugen die von ihnen verwendeten Messmethoden ungenau sein, und die Genauigkeit der ausgewählten Messwerkzeuge kann nicht mit der Genauigkeit der gemessenen Abmessungen übereinstimmen, was zu ungenauen Messergebnissen führt.
2) Installationsanalyse von Vorrichtungen und Teilen
Zum Beispiel sollte bei der Installation von Vorrichtungen und Teilen die Achse der Teile so konsistent wie möglich mit dem Rotationszentrum des Arbeitstisches der Werkzeugmaschine sein, und die Querschnittsmaschine der Teile sollte so senkrecht wie möglich zum Rotationszentrum des Arbeitstisches der Werkzeugmaschine sein, um die gegenseitigen Positionsanforderungen zwischen den verschiedenen Oberflächen der Teile nach der Bearbeitung sicherzustellen. Für Teile, die hohe Konstruktionsgenauigkeit erfordern, relativ große Abmessungen haben und anfällig für Verformungen sind die Installation, Kalibrierung und Spannschritte von Vorrichtungen und Teilen entscheidend, was einen erheblichen Einfluss auf die Genauigkeit der Bearbeitungsteile haben wird. Aufgrund der fehlenden Ansichten und Ansichten für die Bedienung von Vorrichtungen und Teilen können nur Teile nach den Anforderungen des Personals installiert werden. Die Prozessspezifikation erfordert, dass der Auslauf des inneren Lochs des Teils vor der Verarbeitung nicht überschreitet 0.05mm. Aufgrund des Fehlens von klarer Punktkorrektur und kontinuierlicher Korrektur können Arbeiter Punkt-zu-Punkt-Korrektur oder kontinuierliche Korrektur während des Betriebsprozesses annehmen. Die Punkt-zu-Punkt-Kalibrierung erfordert eine relativ kurze Zeit und ist leicht zu erreichen, aber die Kalibrierergebnisse sind nicht genau. Kontinuierliche Kalibrierung erfordert eine lange Zeit und ist auch schwierig, aber die Kalibrierergebnisse werden genauer sein. Die beiden Kalibriermethoden führen zu wesentlichen Unterschieden in den Bearbeitungsergebnissen der Bauteile. Für die Kompression von Teilen spezifiziert die Prozessspezifikation nur die Verwendung von Druckplatten, um die Teile zu komprimieren, ohne die Umsetzungsschritte, die Größe der Druckkraft und die zu treffenden Vorsichtsmaßnahmen anzugeben. Arbeiter arbeiten im Allgemeinen nach ihrer eigenen Erfahrung und Gewohnheiten, was zu übermäßiger oder ungleichmäßiger Druckkraft führt, die Schäden oder Verformungen an den Teilen verursachen kann.
3) Prozessanalyse der Verarbeitung
Beim Schneiden von Teilen bearbeiten die Arbeiter sie nach den Größennummern in der Spalte Auftragsinhalt und den entsprechenden Abmessungen in der Skizze. Für Schneidprozesse ordnen die Arbeiter die Bearbeitungssequenz, den Schneidweg und die Schnittparameter der Teileoberfläche basierend auf ihren eigenen Bearbeitungserfahrungen und Gewohnheiten an. Für CNC-Bearbeitungsprozesse ordnen CNC-Programmierer die oben genannten Inhalte basierend auf ihren eigenen Prozesserfahrungen und Gewohnheiten an. Aufgrund der Einschränkungen und des gewohnheitsmäßigen Denkens des Bearbeitungspersonals und der CNC-Programmierer bei der Beherrschung der mechanischen Bearbeitungstechnologie, bei der Anordnung der Bearbeitungssequenz, des Schneidweges und der Schneidparameter der Teileoberfläche, betrachten sie im Allgemeinen mehr, ob es bequem ist, zu verarbeiten, und weniger berücksichtigen die Unterschiede in der Teilestruktur, den Einfluss der Werkzeuglebensdauer und den Einfluss der Schneidkraft und Schneidkraft auf die Verformung der Teilebearbeitung. Wenn es eine große Anzahl von Oberflächen gibt, die in einem Prozess bearbeitet werden müssen, werden die Änderungen der inneren Spannung des Teils unterschiedlich sein, wenn der Bearbeitungsprozess der bearbeiteten Oberfläche unterschiedlich ist. Wenn der Schneidweg unterschiedlich ist, werden die Schneidkraft und Spannung und der Verschleiß des Werkzeugs erzeugt. Wenn die Schneidparameter unterschiedlich sind, variieren auch die Größe der Schneidkraft, des Werkzeugverschleißes, der Bearbeitungsqualität der Teileoberfläche und der Bearbeitungsverformung des Teils.
Prozessspezifikationsskizzen verwenden normalerweise zweidimensionale Ansichten. Für rotierende Teile und strukturell einfache Teile können zweidimensionale Ansichten die strukturelle Form der Teile klar ausdrücken. Jedoch für Teile mit komplexen Konstruktionsmechanismen, Oberflächendesigns mit Nuten, Vorsprüngen und Lochsystemen oder nicht rotierende Teile werden sie im Allgemeinen auf mehrachsigen CNC-Bearbeitungszentren bearbeitet, und zweidimensionale Ansichten können diese strukturellen Formen und Positionsbeziehungen nicht eindeutig ausdrücken.
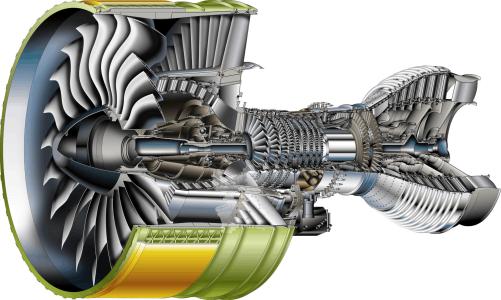
2,Vorschläge für Verbesserungsmaßnahmen der Prozessspezifikationen
Die Verbesserung des Prozessspezifikationsmodus ist nicht nur eine einfache Verbesserung des Prozesstabellenstils, sondern ein komplexes Systemengineering zur facettenreichen Verbesserung der Prozesstechnik. Nachfolgend finden Sie Vorschläge für die Verbesserungsmaßnahmen des Prozessspezifikationsmodus:
1. Verfeinern Sie die Installation und Einstellung von Vorrichtungen und Teilen
Im Prozessdiagramm der Prozessspezifikation sollte ein schematisches Diagramm der Installation von Vorrichtungen und Teilen gezeichnet werden, das die Betriebsmethoden und spezifischen Schritte für Vorrichtungs- und Teileinstallation, Kalibrierung und Spannen detailliert beschreibt, damit jeder Arbeiter gemäß der Prozessspezifikation ohne Unterschiede arbeiten kann.Die Prozessspezifikation für Vorrichtungs- und Teileinstallation im Teiledrehprozess spezifiziert die Arbeitsschritte:
1) Verwenden Sie einen Ölstein, um Vorsprünge, Grate und Unebenheiten auf der Arbeitsfläche der Werkzeugmaschine sowie auf dem Boden des Pads zu entfernen. Wischen Sie mit einem sauberen Tuch sauber, legen Sie das Pad auf die Arbeitsfläche der Werkzeugmaschine, richten Sie den radialen Rundlauf und die Endfläche des Mittelzylinders des Pads innerhalb der angegebenen Werte aus und verwenden Sie einen Ölstein, um Vorsprünge und Grate auf der oberen Endfläche des Pads zu entfernen;
2) Heben Sie die Vorrichtung mit dem bezeichneten Kran an, entfernen Sie etwaige Vorsprünge oder Grate auf dem Installationsgrund mit einem Ölstein, wischen Sie sie mit einem sauberen Tuch ab, legen Sie die Vorrichtung auf das Pad, richten Sie die Mitte visuell aus, verwenden Sie die angegebene Anzahl von Schrauben, um die Vorrichtung und das Pad sanft zu verbinden, richten Sie den radialen Rundlauf und die Stirnfläche der Vorrichtung innerhalb der angegebenen Werte aus, ziehen Sie die Schrauben an, um die Vorrichtung an den Arbeiter zu befestigen, und überprüfen Sie dann erneut, dass die radiale und Stirnfläche Auslaufen der Vorrichtung die angegebenen Werte nicht überschreiten sollten;
3) Wischen Sie die Vorderseite des Teils und die Positionierfläche der Vorrichtung mit einem Tuch sauber ab, überprüfen Sie auf Vorsprünge, Grate usw., platzieren Sie das Teil auf die Vorrichtung, richten Sie das innere Loch des Teils und das Springen der Stirnfläche innerhalb des angegebenen Wertes aus, justieren und festziehen Sie die axiale Wellenunterstützung während des Prozesses aus, verwenden Sie dann die angegebene Anzahl von Druckplatten, um das Teil fest zu drücken, und verwenden Sie dann ein Zifferblatt, um zu überprüfen, ob die Oberflächenbewegung während der axialen Kompression innerhalb des angegebenen Wertes ist;
4) Ziehen Sie die radialen Antibewegungsschrauben auf der Außenfläche der Teile vorsichtig an, ohne sie zu bewegen.
2. 3D Bearbeitungsansicht
Mit der kontinuierlichen Zunahme und Aktualisierung der CNC-Ausrüstung in verschiedenen Luftfahrtunternehmen, mehrachsige CNC-Bearbeitungszentren sind weit verbreitet für komplexe Fräs- und Lochbearbeitungsprozesse verwendet worden. Der Bearbeitungsprozess wird hauptsächlich durch CNC-Programme gesteuert. Wenn die Bearbeitungsskizze der Prozessspezifikation immer noch eine zweidimensionale Ansicht verwendet, kann es nicht intuitiv die strukturelle Form der Bearbeitungsergänzung und die Positionsbeziehung zwischen jedem Bearbeitungsteil ausdrücken.
3. Planen Sie die Oberflächenverarbeitungsequenz und den Schneidweg
In vielen Fällen gibt es zwei oder mehr Bearbeitungsflächen in einem Prozess, und jede Bearbeitungsfläche wird nicht in einem Durchgang bearbeitet. Daher sollte in der Prozessdiagrammskizze die Anzahl der Male angegeben werden, die jede Oberfläche bearbeitet werden muss, und jeder Schnitt sollte mit einer Seriennummer standardisiert werden. Die Seriennummer sollte entsprechend der Schnittfolge der Prozessplanung markiert werden, und die Schnittfolge sollte klar in der Spalte Arbeitsinhalt gefüllt werden. Die dünne feste Linie mit Pfeilen in der Skizze zeigt den Weg und die Richtung jedes Schnittes an. Bei der Bestimmung der Schnittfolge jeder Oberfläche und Planung des Schneidweges und der Schneidrichtung sollten die Prinzipien befolgt werden, um die Verformung des Bearbeitungsprozesses während der Steuerung des Bearbeitungszyklus zu erreichen, so dass bestimmte Bearbeitungswerkzeuge relativ stabil sind und die Lebensdauer verlängern, so dass die Bearbeitungsqualität relativ stabil ist.
4. Ressourcen zur Verbesserung der Prozessinformation
1) Abbrechen Sie die CNC-Schrittkarte und integrieren Sie die CNC-Programminformationen und Werkzeuginformationen von der CNC-Schrittkarte in die Prozessspezifikation. Dies kann effektiv die Schwierigkeit der Prozessdatei-Verwaltung reduzieren und auch die Komplexität der Arbeiter beseitigen, die sowohl die Prozessspezifikation als auch die CNC-Schrittkarte gleichzeitig ausleihen müssen;
2) Verbesserung der Informationen von Schneidwerkzeugen und Messwerkzeugen. Zusätzlich zu den speziellen Schneidwerkzeugnummern, die in der Prozesstabelle markiert sind, sollten auch die Informationen von allgemeinen Schneidwerkzeugen angegeben werden. Für CNC-Bearbeitungsprozesse sollten die Auswahlansicht und Größenanforderungen des Werkzeughalters, Werkzeughalters und Klinge für jeden Satz Schneidwerkzeuge gezeichnet werden, und die Nummern des Werkzeughalters, Werkzeughalters und der Klinge ausgestattet sollten angegeben werden. Die Positionsnummer jedes Sets von Schneidwerkzeugen im Werkzeugmaschinenmagazin sollte ebenfalls markiert werden. Zusätzlich zu den speziellen Messwerkzeugnummern, die in der Prozesstabelle markiert sind, sollten auch die Informationen von allgemeinen Messwerkzeugen markiert sein;

Zusammenfassung
In den letzten Jahrzehnten hat die Art der Verarbeitung von Technologievorschriften für inländische Luftfahrtmotorenkomponenten keine wesentlichen Änderungen erfahren, und es gibt immer noch viel Raum für Verbesserungen im Vergleich zu internationalen fortschrittlichen Technologievorschriften. In den letzten zehn Jahren haben viele inländische Luftfahrtmotorunternehmen mit internationalen fortschrittlichen Luftfahrtmotorunternehmen zusammengearbeitet, um Unterauftragsproduktion durchzuführen und Entwurfsprojekte für Scheibenringteile, Blechschweißteile, Gehäuseteile usw. Wenn die fortschrittlichen Managementmethoden und Verarbeitungstechnologien, die in dieser Unterauftragskomponente gemeistert werden, schnell auf die Forschung und Produktion von inländischen Luftfahrtprodukten angewendet werden können, wird es das Tempo der inländischen Luftfahrtmotorenentwicklung beschleunigen.
Shenzhen EMAR Precision Technology Co., Ltd. konzentriert sich auf hochpräzise CNC-Werkzeugmaschinen für die externe Bearbeitung. Derzeit ist unser Unternehmen mit CNC-Ausrüstung einschließlich Schwerpunkt CNC-Drehmaschinen, Werkzeuglaufmaschinen CNC-Drehmaschinen, Drehfräsen Composite-Bearbeitungszentren und CNC-vertikalen Bearbeitungszentren ausgestattet. Mehr als 100 CNC-Ausrüstung kann die Anpassung und Chargenverarbeitungsaufgaben von Präzisionsteilen erfüllen. Unsere Produktpalette umfasst Luftfahrtteile, Automobilteile, medizinische Teile, Kommunikationsteile und andere Serien. Das Unternehmen hat mehr als 20-Jahre Erfahrung in der Präzisionsbearbeitung und kann die Genauigkeit und rechtzeitige Lieferung von Produkten gewährleisten. Willkommen, uns anzurufen, und wir werden gewidmet, Ihnen zu dienen.