1. Schermaterial: bezieht sich auf den Prozess, bei dem Material durch eine Schermaschine läuft, um ein rechteckiges Werkstück zu erhalten.
2, Schneiden: bezieht sich auf das Werkstück durch LASER Schneiden oder numerische Steuerung Stanzen Prozess.
3. Blanking: bezieht sich auf den Prozess der Verarbeitung einer Produktform unter Verwendung einer Matrize auf einem gewöhnlichen Stempel oder einer anderen Ausrüstung.
4. Stanzen: bezieht sich auf den Prozess der Bearbeitung von Löchern für Werkstücke durch gewöhnliche Stanzmaschinen und Formen.
5. Biegen: bezieht sich auf den Prozess der Formung eines Werkstücks durch eine Biegemaschine.
6. Umformen: bezieht sich auf den Prozess der Verwendung von Formen auf gewöhnlichen Stanzformen oder anderen Geräten zum Verformen von Werkstücken.
7. Lochauszug: auch bekannt als "Bördeln", bezieht sich auf den Prozess der Verwendung einer Form auf einem gewöhnlichen Stempel oder einer anderen Ausrüstung, um ein rundes Loch auf dem Werkstück zu bilden und es aufzudrehen.
8. Gewindeschneiden: bezieht sich auf den Prozess der Bearbeitung von Innengewinden an einem Werkstück.
9. Reiben: bezeichnet das Verfahren, bei dem kleine Löcher in einem Werkstück mit einem Bohrer oder Fräser in große Löcher bearbeitet werden.
10. Senkbohrung: bezieht sich auf den Prozess der Bearbeitung eines konischen Lochs auf dem Werkstück, um einen Verbinder ähnlich einer Senkschraube zu montieren.
11. Nieten: bezieht sich auf den Prozess des festen Andrückens von Befestigungselementen wie Nietmuttern, Nietschrauben oder Nietmutternsäulen auf das Werkstück mit Hilfe eines Stempels oder einer hydraulischen Presse
12. Steigniet: bezieht sich auf den Prozess, bei dem das Werkstück zunächst versenkt und dann mit einem Stempel oder einer hydraulischen Presse die Steignietmutter fest auf das Werkstück gedrückt wird.
13. Zugmutter: bezieht sich auf den Prozess der Verwendung eines nietähnlichen Verfahrens. Der Prozess der festen Verbindung der Verbindungsteile wie der Zugnietmutter (POP) mit dem Werkstück mit einer Zugmutterpistole.
14. Nieten: bezieht sich auf das Verfahren, bei dem eine Nietpistole als Werkzeug verwendet wird, um zwei oder mehr Werkstücke mit Zugnägeln eng miteinander zu verbinden.
15. Nieten: Der Vorgang, bei dem zwei oder mehr Werkstücke mit Nieten frontal verbunden werden. Wenn ein Senkkopfnieten erforderlich ist, muss das Werkstück zuerst versenkt werden.
16. Stanzen der konvexen Hülle: bezieht sich auf das Verfahren zur Herstellung einer konvexen Form eines Werkstücks mit einer Matrize in einem Stempel oder einer hydraulischen Presse.
17. Stanzen und Reißen: Auch "Stanzbrücke" genannt, bezieht es sich auf den Prozess, ein Werkstück mit einer Matrize auf einem Stempel oder einer hydraulischen Presse in eine brückenartige Form zu bringen.
18. Drucken: bezieht sich auf das Verfahren, bei dem mit einer Form Text, Symbole oder andere Abdrücke auf ein Werkstück gedruckt werden.
19. Eckenschneiden: bezeichnet den Prozess des Abschneidens der Ecken des Werkstücks mit einer Matrize auf einem Stempel oder einer hydraulischen Presse.
20, Stanzen von Löchern: bezieht sich auf die gewöhnliche Stanze oder numerische Steuerung Stanze mit einer Matrize auf dem Werkstück Stanzen Löcher.
21. Abflachung: bezieht sich auf den Prozess des Übergangs eines Werkstücks mit einer bestimmten Form in ein flaches Werkstück.
22. Bohren: bezeichnet das Bohren eines Werkstücks mit einem Bohrer auf einer Bohr- oder Fräsmaschine.
23. Anfasen: bezieht sich auf den Prozess der Bearbeitung der scharfen Ecken eines Werkstücks mit Formen, Feilen, Schleifmaschinen usw.
24. Nivellieren: bezieht sich auf den Prozess des Nivellierens des Werkstücks vor und nach der Bearbeitung und die Verwendung anderer Geräte zum Nivellieren des Werkstücks.
25. Zahnrücklauf: bezieht sich auf den Prozess der Reparatur des zweiten Schraubzahns auf dem vorgewindeten Werkstück.
26. Schutzfolie: bezieht sich auf den Prozess der Verwendung einer Folie, die die Oberfläche des Werkstücks schützen kann, um die Oberfläche des Werkstücks zu schützen.
27. Schutzfolie abreißen: bezieht sich auf den Prozess der Reinigung der Oberflächenschutzfolie des Werkstücks.
28. Formkorrektur: bezieht sich auf den Prozess der Einstellung des bearbeiteten und geformten Werkstücks.
29. Wärmeschrumpfung: bezieht sich auf den Prozess der Verwendung von Heizgeräten (Heißluftpistole, Backofen), um den Kunststoff, der das Werkstück bedeckt, festzuziehen.
30. Beschriftung: bezieht sich auf den Prozess der Anbringung des Etiketts an der vorgesehenen Stelle des Werkstücks.
31. Drahtziehen: bezieht sich auf den Prozess der Verwendung einer Drahtziehmaschine und eines Schleifbandes zur Behandlung der Oberfläche des Werkstücks.
32. Polieren: bezieht sich auf den Prozess der Verwendung von Poliergeräten, um die Oberfläche eines Werkstücks aufzuhellen.
33. Wärmebehandlung: bezieht sich auf den Prozess der Durchführung einer speziellen Behandlung zur Erhöhung der Härte des Werkstücks.
34. Entgraten: bezieht sich auf den Prozess des Entfernens der Gratkante des Werkstücks mit Werkzeugen wie Schleifmaschinen und Feilen während der Blechbearbeitung, um die Bearbeitung des Werkstücks glatt und flach zu machen.
35. Argon-Lichtbogenschweißen: bezeichnet das Schweißen des Werkstücks und des Werkstücks mit einer Argon-Lichtbogenschweißmaschine an der Kante oder Naht des Werkstücks. Es wird unterteilt in intermittierendes Schweißen, Vollschweißen usw., die in den Zeichnungen deutlich gekennzeichnet sein sollten.
36. Berührungsschweißen: auch bekannt als: "Punktschweißen", bezieht sich auf das Schweißen des Werkstücks von Angesicht zu Angesicht mit einer Berührungsschweißmaschine.
37. Anlagenschweißen: bezieht sich auf das Verfahren, bei dem die Anlagenschweißschrauben mit einem Anlagenschweißbrenner fest mit dem Werkstück verschweißt werden.
38. Schweißen und Schleifen: bezieht sich hauptsächlich auf den Prozess der Verwendung von Werkzeugen wie Schleifmaschinen und Feilen, um die Schweißnarbe des Werkstücks glatt und flach zu machen.
39. Vorbehandlung: bezieht sich auf den Prozess der Entfettung, Rostentfernung, Oberflächenbeschichtung (z. B. Phosphatierungsfolie) und Reinigung des Werkstücks mit einer Elektrolytlösung vor dem Lackieren oder Pulverspritzen nach Abschluss der Blechbearbeitung des Werkstücks.
40. Schaben: bezieht sich auf den Prozess der Verwendung von Atomasche, um Fehler auf der Oberfläche des Werkstücks, wie Schweißspalten oder Vertiefungen, auszugleichen.
41. Schaben und Polieren: bezieht sich hauptsächlich auf den Prozess des Oberflächenpolierens des Werkstücks nach dem Schaben mit einer Flachschleifmaschine oder einem Schmirgelleinen. 42. Öleinspritzung: bezieht sich auf den Prozess der Verwendung einer speziellen Spritzpistole, um die Farbe gleichmäßig auf die Oberfläche des Werkstücks zu sprühen.
43. Pulversprühen: bezieht sich auf das Verfahren, bei dem mit einer Spritzpistole Pulver gleichmäßig auf die Oberfläche des Werkstücks gesprüht wird.
44. Siebdruck: bezeichnet das Verfahren, bei dem eine spezielle Tinte verwendet wird, um ein spezielles Gitter zu durchdringen und Text oder Muster auf der Oberfläche des Werkstücks zu bilden.
45. Galvanisieren: bezieht sich auf das Verfahren, bei dem eine Metallschicht auf die Oberfläche eines Werkstücks aufgetragen wird, um dessen Aussehen zu schützen oder zu verbessern.
46. Oxidation: bezieht sich auf den Prozess der Bildung einer Oxidschicht auf der Oberfläche eines Werkstücks, um dessen Aussehen zu schützen oder zu verbessern.
47. Sandstrahlen: bezieht sich auf das Verfahren zur Behandlung der Oberfläche des Werkstücks durch Sandstrahlen
47. Montage: bezieht sich auf den Prozess des Zusammensetzens von mehr als zwei Werkstücken.
48. Verpackung: bezieht sich auf den Prozess des Schutzes des Werkstücks für den einfachen Transport.
49. Andere: Brechen, Ziehen (Matrize), Gegendruck, Zahnextraktion (Gewindeschneiden nach Lochextraktion), Salat (Gegengewicht) durch Loch
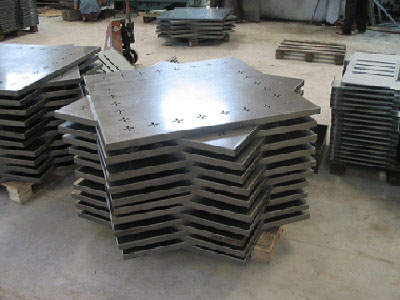