El procesamiento de chapa metálica es un proceso integral de procesamiento en frío para láminas metálicas (generalmente por debajo de 6 mm), que incluye corte, punzonado, flexión, soldadura, remachado, moldeo de moldes y tratamiento de superficie. Su característica distintiva es que el grosor de la misma pieza es consistente.
Método de procesamiento de chapa metálica: procesamiento sin molde: método de procesamiento de chapa metálica a través de punzonado digital, Corte láser, máquina de corte, máquina de flexión, máquina de remachado y otros equipos, generalmente utilizado para la producción de muestras o producción en pequeños lotes, el costo es alto. El ciclo de procesamiento es corto y la respuesta es rápida. Procesamiento de moldes: a través de moldes fijos, se procesa la chapa metálica, generalmente hay moldes de corte y moldes de formación, que se utilizan principalmente para la producción en masa, con un costo más bajo. El costo del molde inicial es alto y la calidad de las piezas está garantizada. El ciclo de procesamiento inicial es largo y el costo del molde es alto. Proceso de procesamiento de chapa metálica: descarga: punzonado digital, Corte láser, máquina de corte
Moldeo - flexión, estiramiento, punzonado: máquina de flexión, punzonado, etc.
Otros procesos: remachado, punzonado, etc.
Soldadura: la forma de conectar la chapa metálica
Tratamiento de superficie: polvo de pulverización, galvanoplastia, dibujo, serigrafía, etc.
Proceso de procesamiento de chapa metálica - los principales métodos de corte de chapa metálica son punzonado digital, Corte láser, cortadora de chapa, Corte de molde, etc. el control numérico es el método común actual. el corte láser se utiliza principalmente en la etapa de prueba (también se puede procesar piezas de chapa metálica de acero inoxidable), el costo de procesamiento es alto, y El Corte de molde se utiliza principalmente para el procesamiento en masa.
A continuación, introducimos principalmente el corte de la chapa metálica en varios golpes.
El punzón digital también se llama punzón CNC de Torre giratoria, que se puede utilizar para descargar, perforar, estirar agujeros, rodar barras, golpear persianas, etc., y su precisión de procesamiento puede alcanzar + / - 0,1 mm.
El espesor de la placa mecanizable CNC es:
Placa laminada en frío y placa laminada en caliente 4,0 mm
Placa de aluminio 5,0 mm
Placa de acero inoxidable 2,0 mm
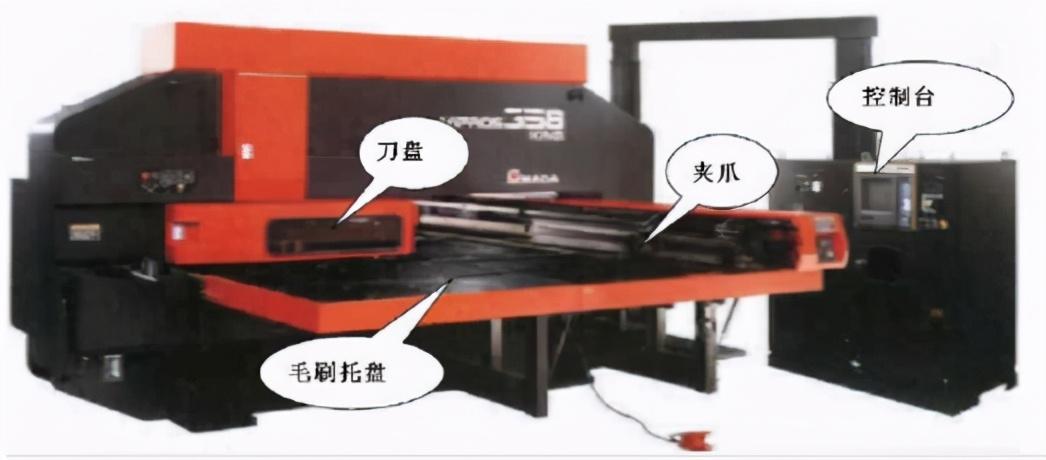
El punzonado tiene requisitos de tamaño mínimo. El tamaño mínimo del agujero de punzonado está relacionado con la forma del agujero, las propiedades mecánicas del material y el espesor del material. (la siguiente imagen)
2. la distancia entre los agujeros del punzón digital y el borde del agujero. Cuando la distancia mínima entre el borde del punzonado de la pieza y el borde de la forma de la pieza no sea paralela al borde de la forma de la pieza, la distancia mínima no debe ser inferior al espesor del material t; En paralelo, no debe ser inferior a 1,5t. (la siguiente imagen)
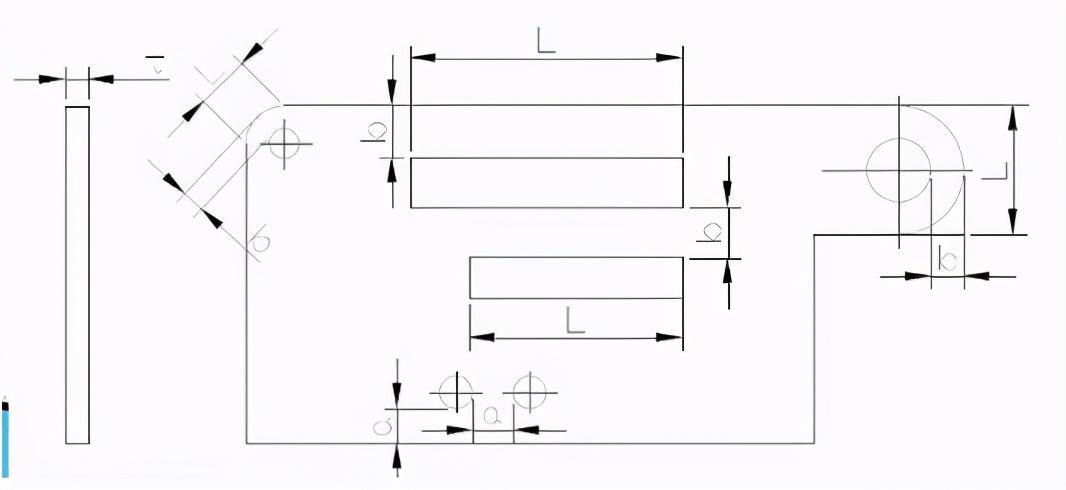
3. al estirar el agujero, la distancia mínima entre el agujero de estiramiento y el borde es de 3t, la distancia mínima entre los dos agujeros de estiramiento es de 6t, y la distancia mínima de seguridad entre el agujero de estiramiento y el borde de flexión (interior) es de 3T + R (t es el espesor de la chapa metálica y R es El redondeado de flexión).
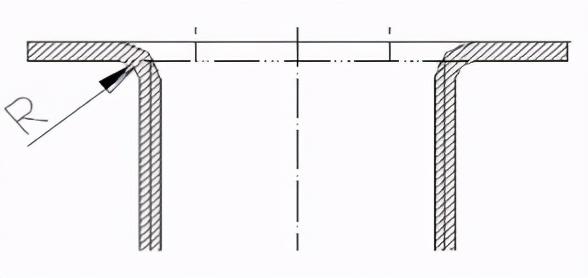
4. al estirar los agujeros de las piezas dobladas y las piezas de dibujo profundo, se debe mantener una cierta distancia entre la pared del agujero y la pared recta. (la siguiente imagen)
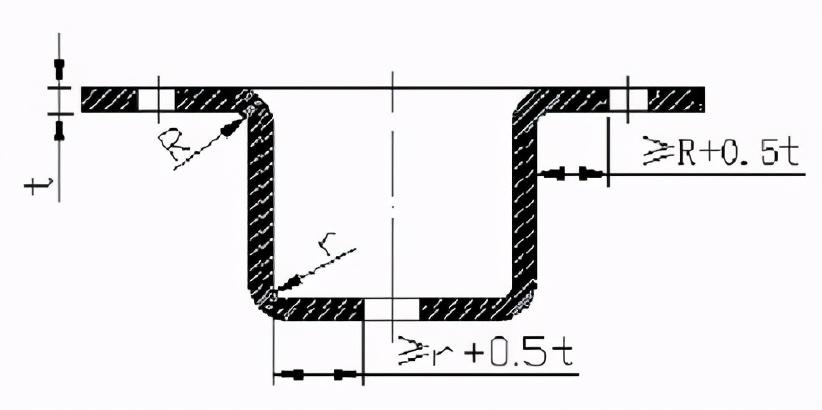
Proceso de procesamiento de chapa metálica - la formación de chapa metálica formada es principalmente la flexión y el estiramiento de la chapa metálica.
1. la flexión de la chapa metálica 1.1 se realiza principalmente con máquinas herramienta de flexión.
Precisión de procesamiento de la cama plegable;
Descuento: + / - 0,1 mm
20% de descuento: + / - 0,2 mm
Más del 20% de descuento: + / - 0,3 mm
1.2 principios básicos del orden de procesamiento de flexión: doblar de adentro hacia afuera, doblar de pequeño a grande, doblar primero formas especiales, después de la formación del proceso anterior, no hay impacto ni interferencia en el proceso posterior.
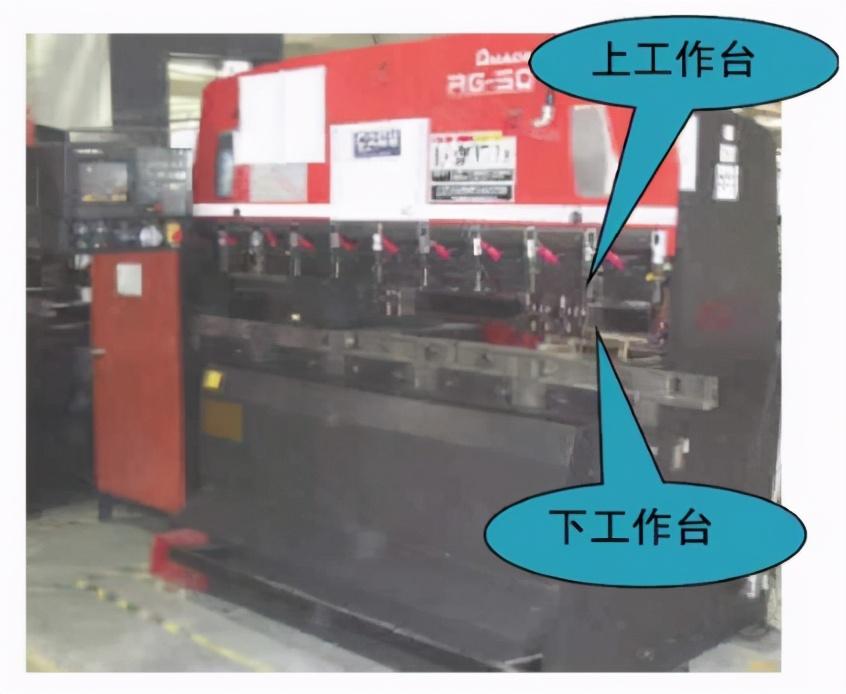
1.3 forma común de cuchillo de flexión:
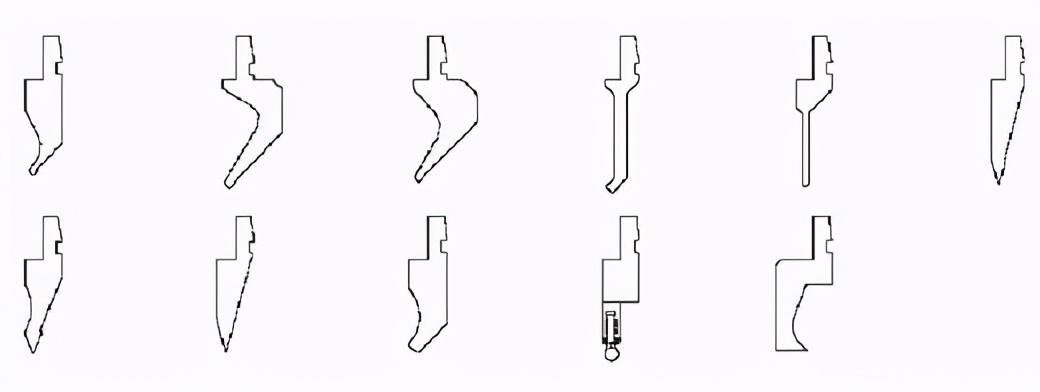
Forma común de la ranura v:
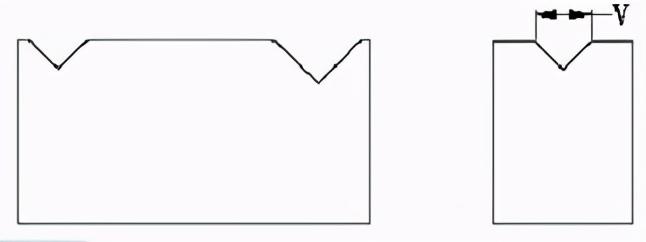
1.4 radio mínimo de flexión de la pieza doblada:
Cuando el material se dobla, en su zona redondeada, la capa exterior se estira y la capa interior se comprime. Cuando el espesor del material es cierto, cuanto menor es el R interno, más grave es el estiramiento y la compresión del material; Cuando el esfuerzo de tracción del redondeado exterior supera la resistencia límite del material, se producen grietas y rotura, por lo que el diseño estructural de la pieza doblada debe evitar un radio de redondeado curvo demasiado pequeño. El radio mínimo de flexión de los materiales comunes de la compañía se muestra en la siguiente tabla.
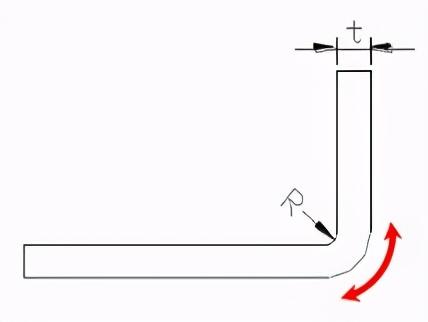
Tabla del radio mínimo de flexión de las piezas dobladas:
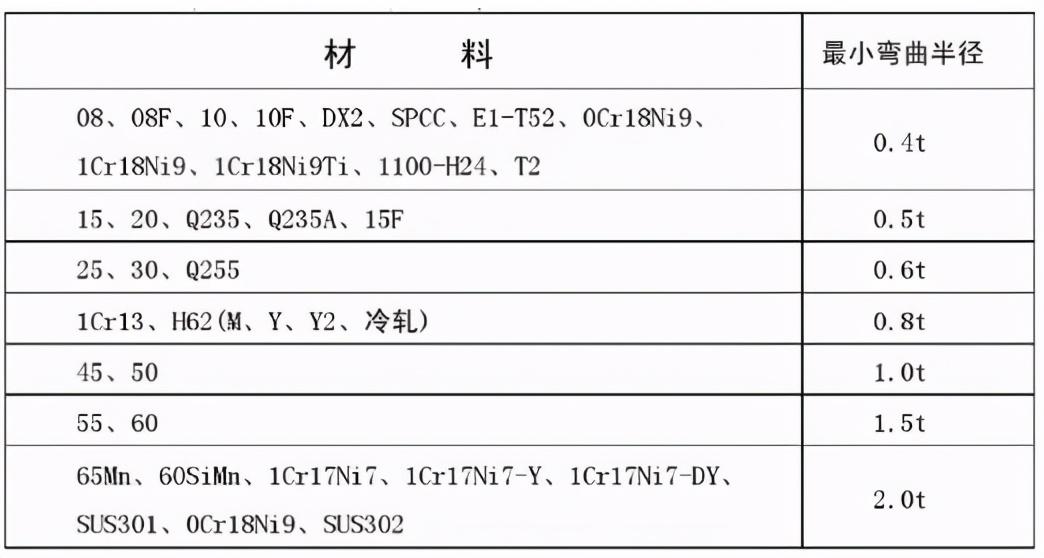
El radio de flexión se refiere al radio interior de la pieza doblada, y T es el espesor de la pared del material.
1.5 altura del borde recto de la pieza doblada:
En general, la altura mínima del borde recto no debe ser demasiado pequeña, y el requisito de altura mínima: H > 2t
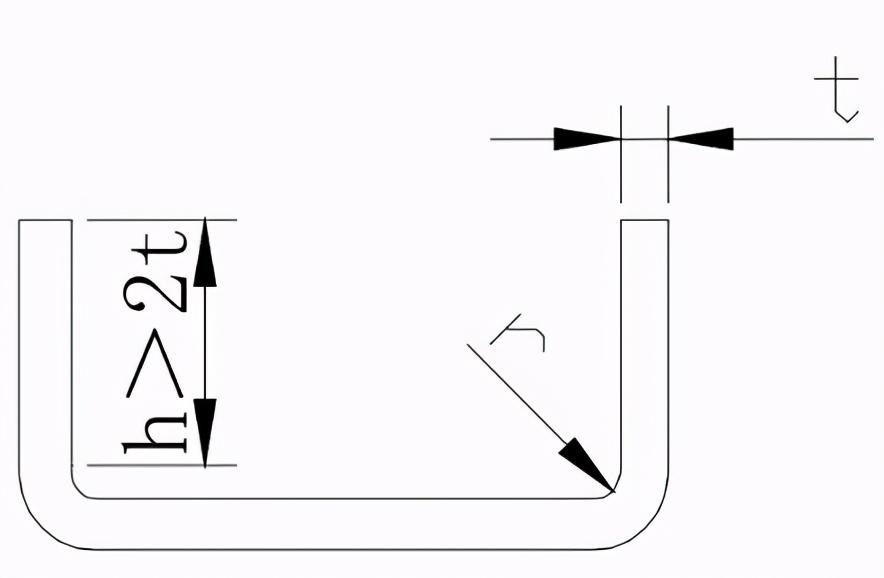
Si se necesita la altura del borde recto de la pieza doblada H 2t, primero se debe aumentar la altura del borde curvo, y luego se debe doblar antes de procesarlo hasta el tamaño necesario; O después de procesar ranuras poco profundas en la zona de deformación de flexión, se dobla.
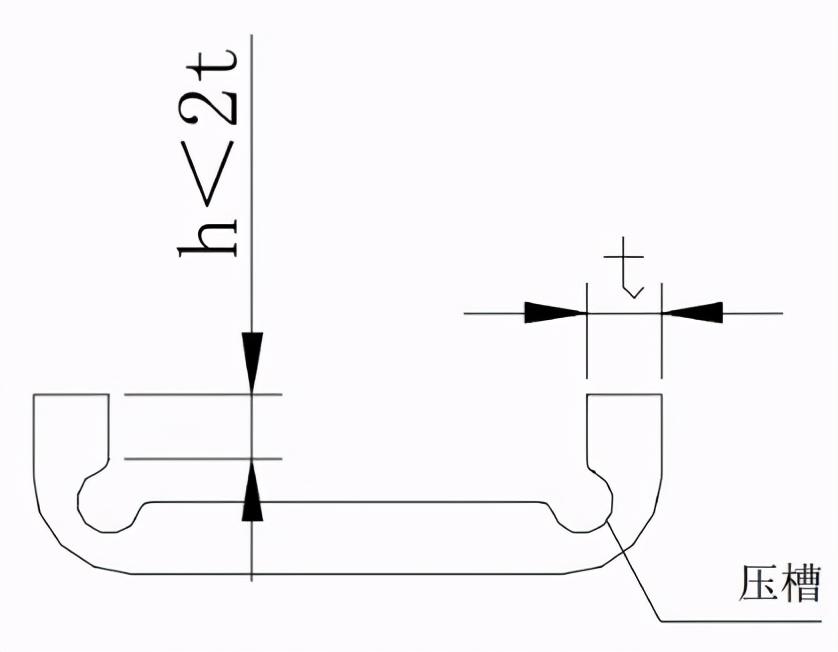
1.6 altura mínima del borde recto curvo con ángulos oblicuos en el lado curvo:
Cuando hay piezas dobladas con ángulos oblicuos en el lado de la curva, la altura mínima en el lado es: h = (2 a 4) T & gt; 3 mm
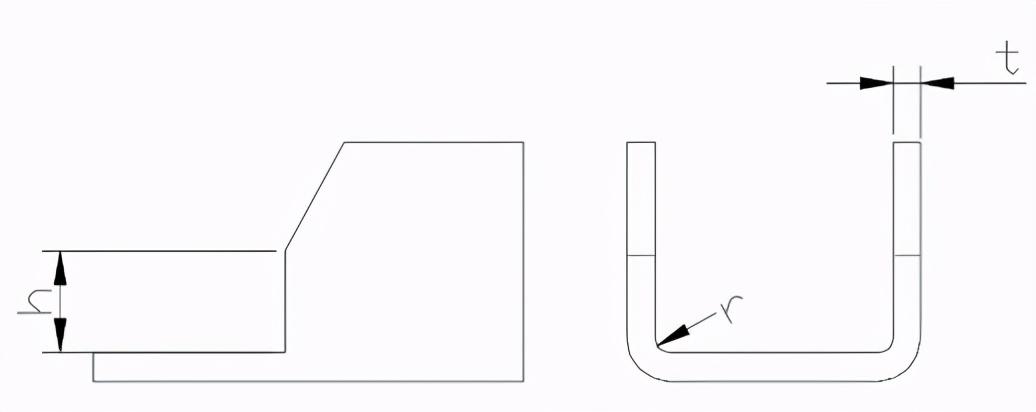
1.7 margen del agujero en la pieza doblada:
Margen del agujero: primero perforar el agujero y luego doblar, la posición del agujero debe estar fuera de la zona de deformación de flexión para evitar la deformación del agujero cuando se dobla. La distancia entre la pared del agujero y el borde curvo se muestra en la siguiente tabla.
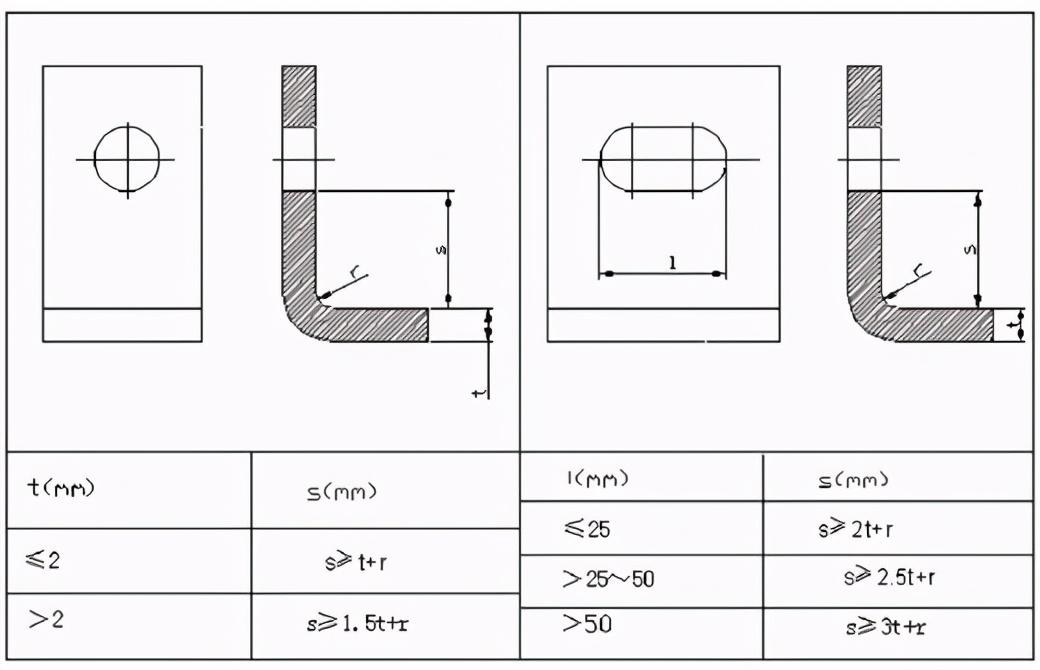
1.8 incisión artesanal doblada localmente:
La línea de flexión de la pieza doblada debe evitar la posición de mutación de tamaño. Al doblar parcialmente un borde, para evitar que la concentración de esfuerzo de las esquinas afiladas produzca grietas de flexión, la curva de flexión se puede mover a cierta distancia para salir de la mutación de tamaño (figura a), o abrir la ranura de proceso (figura b), o perforar el agujero de proceso (figura c). Preste atención a los requisitos de tamaño en la imagen: sr; Ancho de la ranura kt; Profundidad de la ranura LT + R + K / 2.
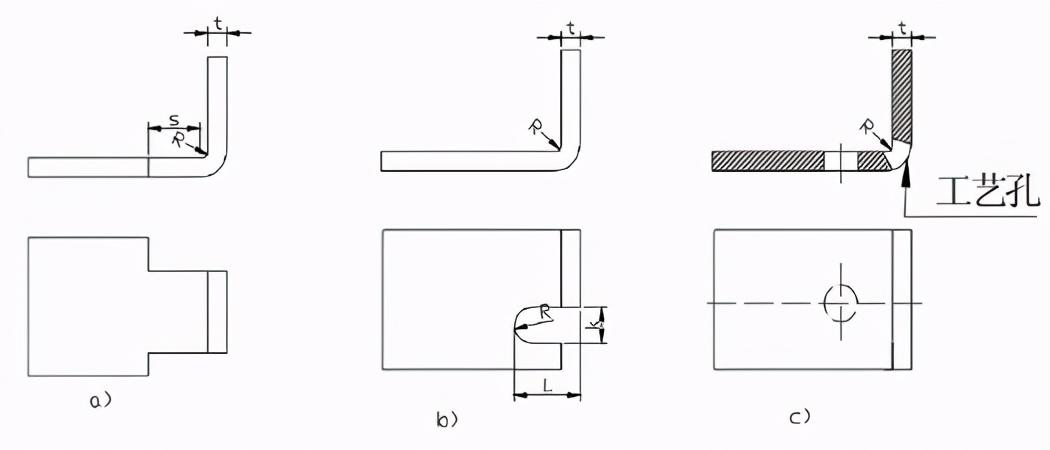
1.9 los bordes curvos con bordes oblicuos deben evitar las zonas de deformación:
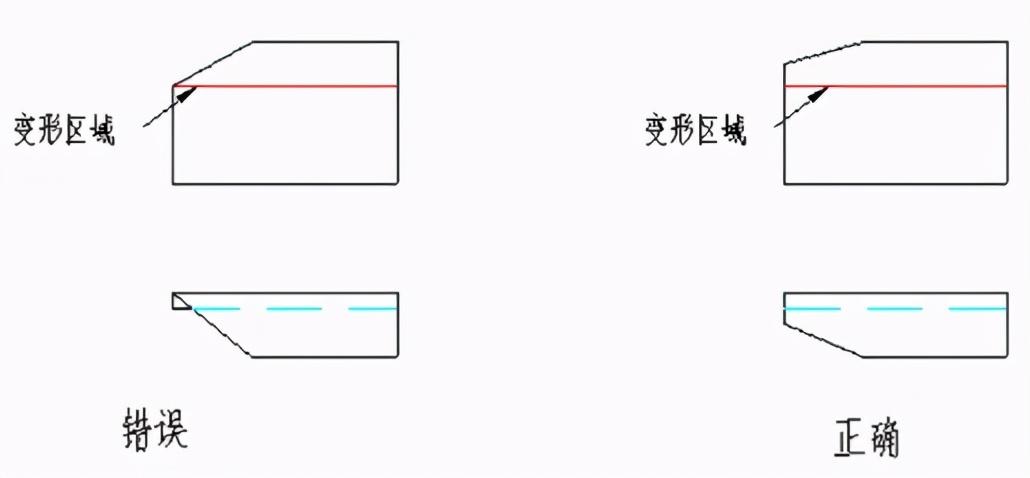
1.10 requisitos de diseño para los volantes de chapa metálica (bordes muertos):
La longitud del borde muerto del pliegue de la chapa metálica está relacionada con el grosor del material. Como se muestra en la siguiente imagen, la longitud mínima general del borde muerto es l3.5t + R.
Entre ellos, t es el espesor de la pared del material y R es el radio mínimo de flexión interna del proceso anterior del borde de la muerte (como se muestra a la derecha en la imagen de abajo).

1.11 agujeros de posicionamiento del proceso añadidos:
Para garantizar el posicionamiento preciso del blanco en el molde y evitar la generación de residuos debido al desplazamiento del blanco durante la flexión, se deben agregar agujeros de posicionamiento del proceso en el diseño con antelación, como se muestra en la siguiente imagen. En particular, las piezas formadas por flexión múltiple deben basarse en agujeros de proceso como referencia de posicionamiento para reducir los errores acumulados y garantizar la calidad del producto.
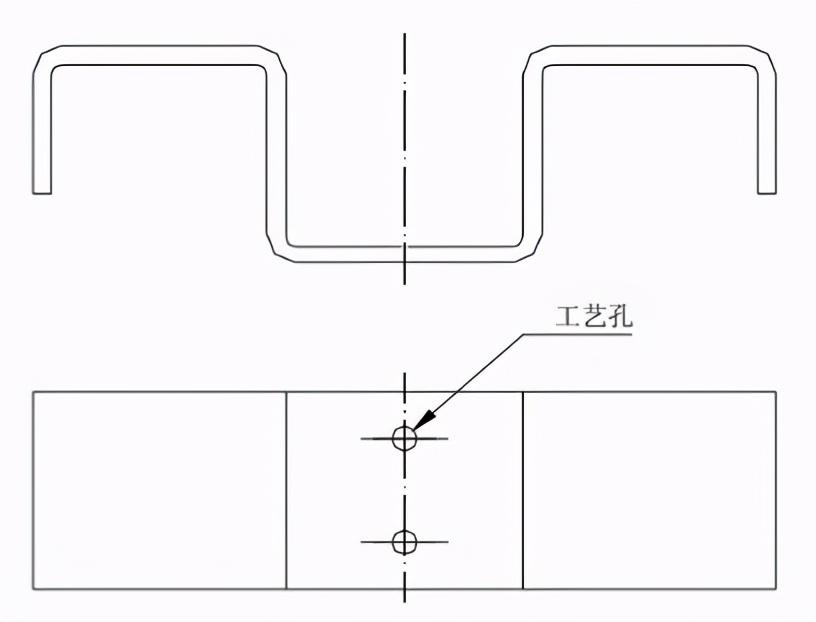
1.12 al marcar las dimensiones relacionadas con las piezas dobladas, se debe considerar la artesanía:
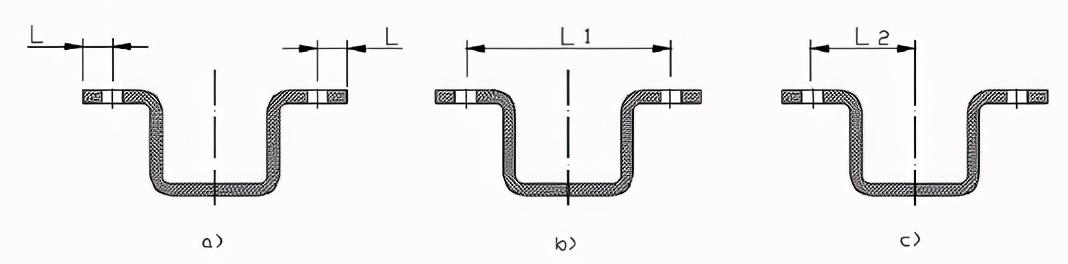
Como se muestra en la imagen de arriba, a) primero se golpea el agujero y luego se dobla, la precisión del tamaño L se garantiza fácilmente y el procesamiento es conveniente. B) y c) si la precisión de la dimensión l es alta, es necesario doblar primero y luego mecanizar el agujero, lo que es problemático de mecanizar.
1.13 hay muchos factores que afectan el rebote de las piezas dobladas, incluyendo: propiedades mecánicas del material, espesor de la pared, Radio de flexión y presión positiva al doblar. Cuanto mayor sea la relación entre el radio del círculo interior de la pieza doblada y el grosor de la placa, mayor será el rebote. Ejemplos de métodos para frenar el rebote en el diseño son el rebote de las piezas dobladas, que actualmente es evitado principalmente por los fabricantes cuando diseñan moldes, tomando ciertas medidas. Al mismo tiempo, la mejora de algunas estructuras desde el diseño hace que el ángulo de rebote sea menos simple como se muestra en la siguiente imagen: presionar las costillas de refuerzo en la zona de flexión no solo puede aumentar la rigidez de la pieza de trabajo, sino también ayudar a frenar el rebote.
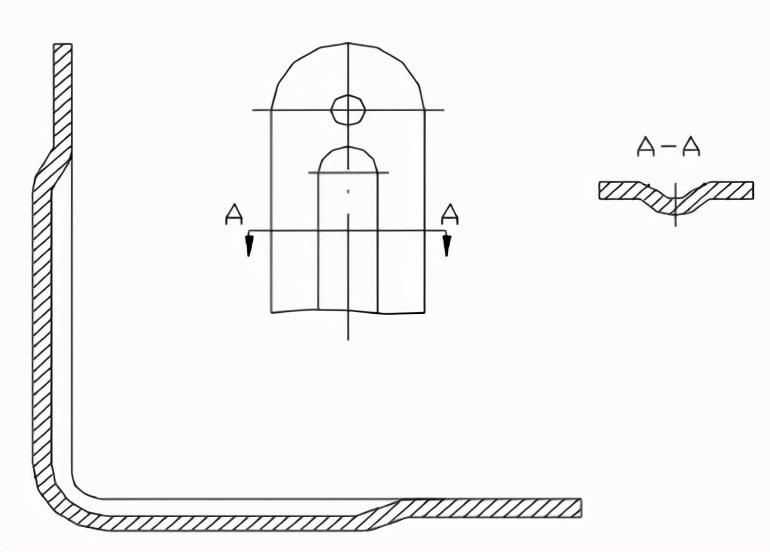
2. el estiramiento de la chapa metálica estirada de la chapa metálica se realiza principalmente por CNC o punzonado general, que requiere varios punzones o moldes de estiramiento.
La forma de la pieza de dibujo debe ser lo más simple y simétrica posible, y debe formarse lo más posible una vez.
Las piezas que requieren múltiples estiramientos deben permitir posibles marcas de la superficie durante el estiramiento.
Bajo la premisa de garantizar los requisitos de montaje, se debe permitir una cierta inclinación de la pared lateral estirada.
2.1 requisitos de tamaño del radio de redondeo entre la parte inferior de la pieza de estiramiento y la pared recta:
Como se muestra en la siguiente imagen, el radio de redondeo entre la parte inferior de la pieza de estiramiento y la pared recta debe ser mayor que el espesor de la placa, es decir, r1t. Para que el estiramiento se realice sin problemas, generalmente se toma R1 = (3 a 5) t, y el radio máximo del círculo debe ser inferior o igual a 8 veces el espesor de la placa, es decir, r18t.
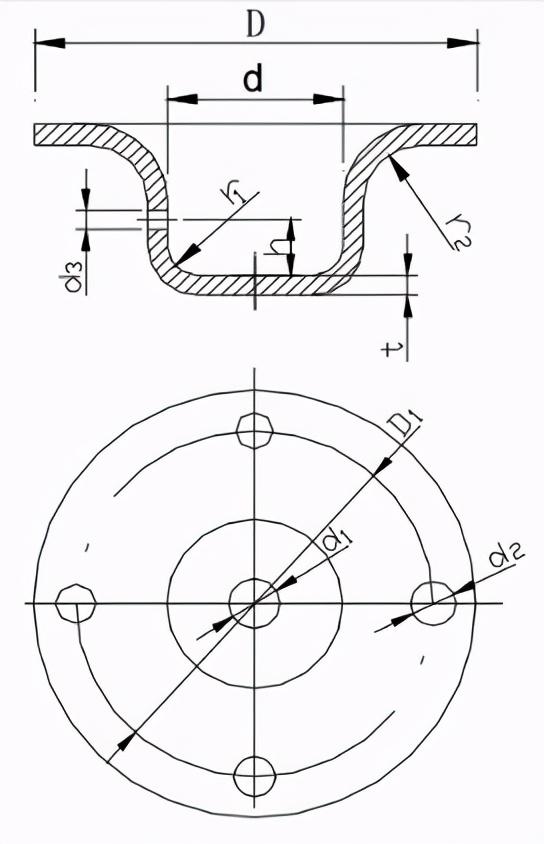
2.2 Radio redondeado entre la brida y la pared de la pieza de tracción
El radio de redondeo entre la brida y la pared de la pieza de estiramiento debe ser mayor que el doble del espesor de la placa, es decir, r22t. para que el estiramiento se realice sin problemas, generalmente se toma R2 = (5 a 10) t, y el radio máximo de la brida debe ser inferior o igual a 8 veces el espesor de La placa, es decir, r28t. (ver la imagen de arriba)
2.3 diámetro de la cavidad interna de la pieza de tracción circular
El diámetro de la cavidad interna de la pieza de estiramiento circular debe tomar D + 10T para que la placa de presión no se arrugue al estirarse. (ver la imagen de arriba)
2.4 Radio redondeado entre las dos paredes adyacentes de la pieza de tracción rectangular
El radio redondeado entre las dos paredes adyacentes de la pieza de estiramiento rectangular debe tomar R3 3t, y para reducir el número de estiramientos, R3 H / 5 debe tomarse en la medida de lo posible para sacarlo una y otra vez.
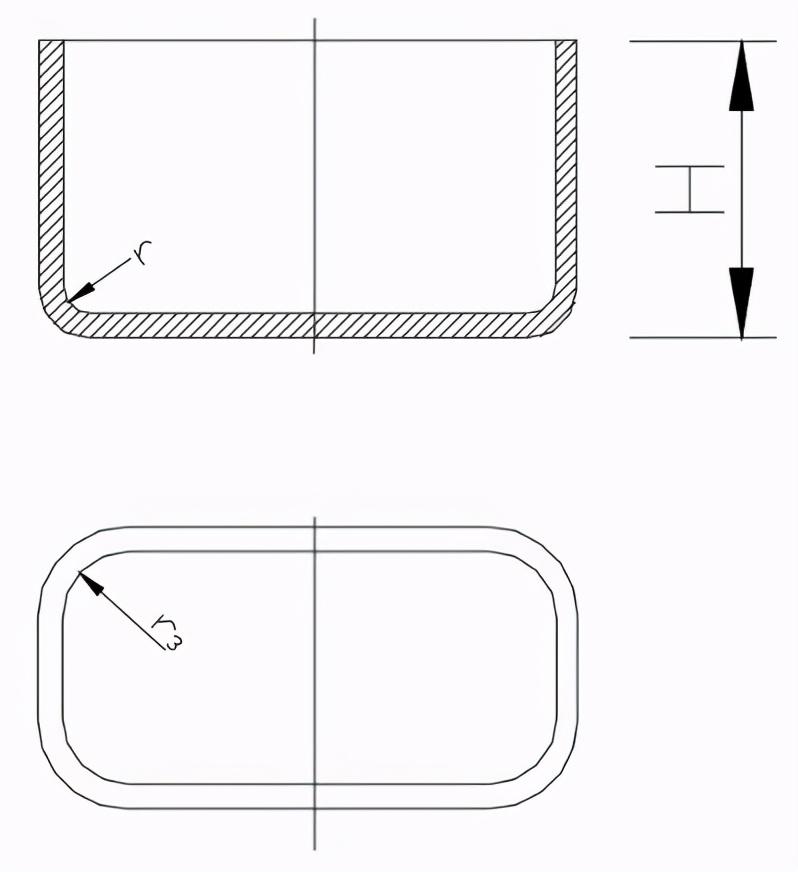
2.5 requisitos de la relación de tamaño entre la altura y el diámetro de una pieza de dibujo redonda sin brida en una sola formación
La relación entre la altura H y el diámetro D debe ser inferior o igual a 0,4, es decir, H / D 0,4, cuando se forma una pieza redonda sin brida, como se muestra en la siguiente imagen.
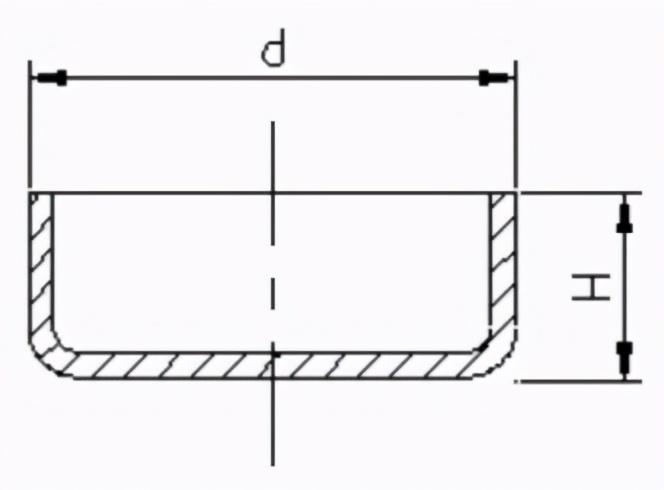
2.6 cambios en el grosor de los materiales de las piezas de tracción:
Debido a que el tamaño del estrés varía de un lugar a otro, el espesor del material después del estiramiento cambia. En términos generales, el Centro inferior mantiene el grosor original, el material se adelgaza en el redondeado inferior, el material se engrosa en la parte superior cerca de la brida y el material se engrosa en el redondeado alrededor de la pieza de tracción rectangular.
2.7 método de etiquetado del tamaño del producto de la pieza de dibujo
Al diseñar el producto de estiramiento, las dimensiones en el dibujo del producto deben indicar claramente que las dimensiones externas o internas deben garantizarse, y las dimensiones internas y externas no deben marcarse al mismo tiempo.
2.8 método de etiquetado de la tolerancia dimensional de las piezas de dibujo
El radio interior del arco convexo y convexo de la pieza de tracción y la tolerancia a la altura y dimensión de la pieza de tracción cilíndrica formada de una sola vez son desviaciones simétricas de doble cara, y su valor de desviación es la mitad del valor absoluto de la tolerancia de precisión del nivel 16 de la norma nacional (gb), y está numerado.
3. otras formas de chapa metálica: costillas de refuerzo - las costillas de presión sobre piezas metálicas en forma de placa ayudan a aumentar la rigidez estructural.
Las persianas - las persianas se utilizan generalmente en varias carcasas o carcasas para ventilar y disipar el calor.
Flanqueado del agujero (agujero de estiramiento) - utilizado para mecanizar hilos o aumentar la rigidez del agujero.
3.1 fortalecimiento de los músculos:
Estructura de las costillas de refuerzo y su selección de tamaño
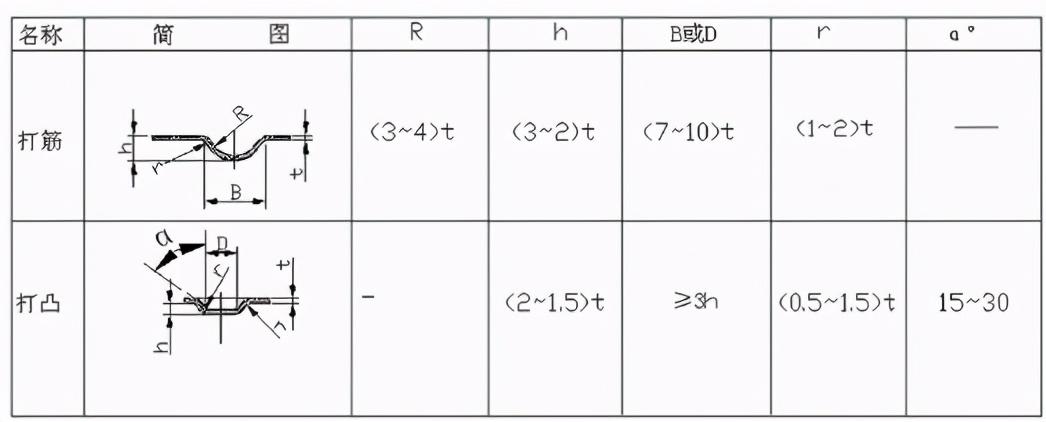
Las dimensiones límite de la distancia entre los bordes convexos y los bordes convexos se seleccionan de acuerdo con la tabla.
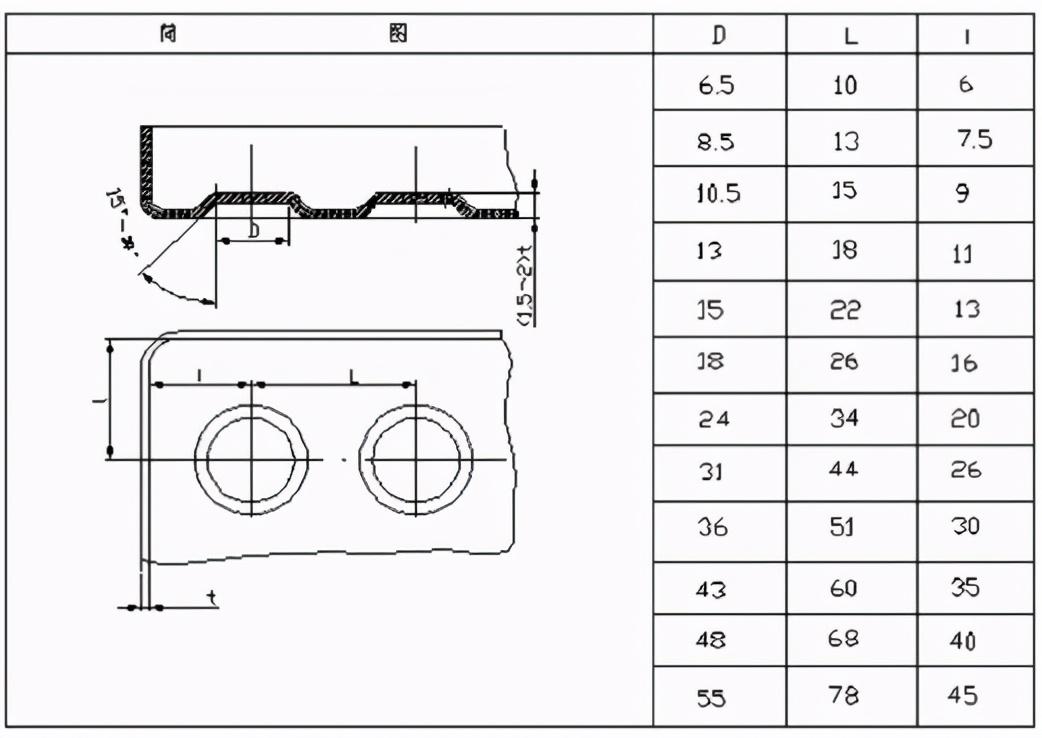
3.2 persianas
El método de formación de la persiana consiste en cortar el material a través del Filo de un lado del punzón, mientras que el resto del punzón deforma el material en tensión al mismo tiempo, formando una forma ondulada de una apertura lateral.
La estructura típica de las persianas se muestra en la siguiente imagen.
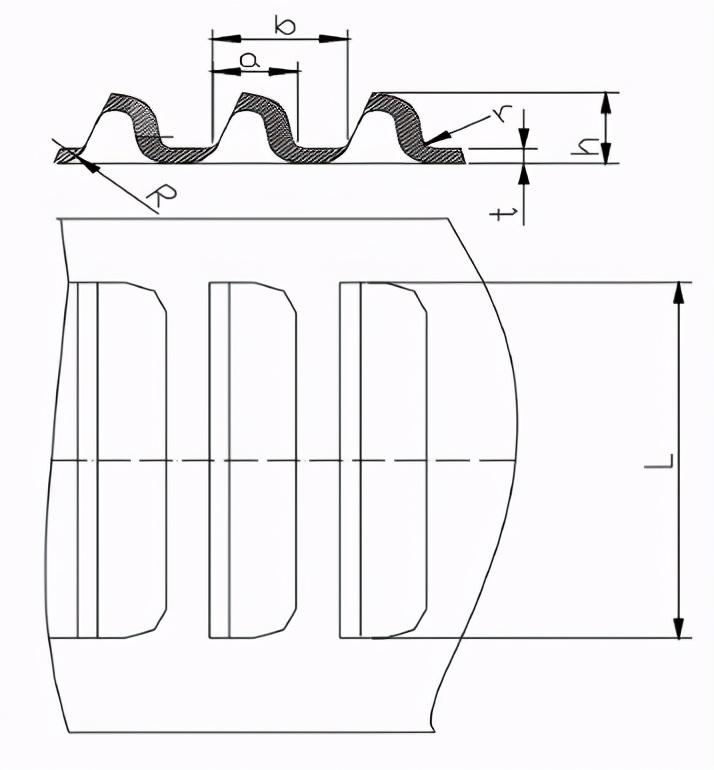
Requisitos de tamaño de las persianas: a4t; b6t;h5t;L24t;r0.5t。
3.3 orificios flanqueados (orificios de estiramiento)
Hay muchas formas de volantes de agujeros, y lo común es procesar los volantes de agujeros internos de los hilos.
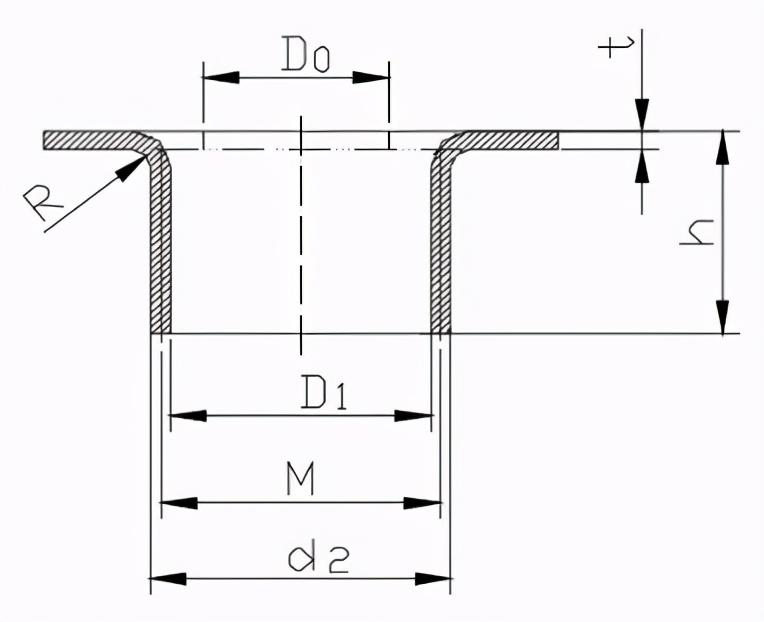
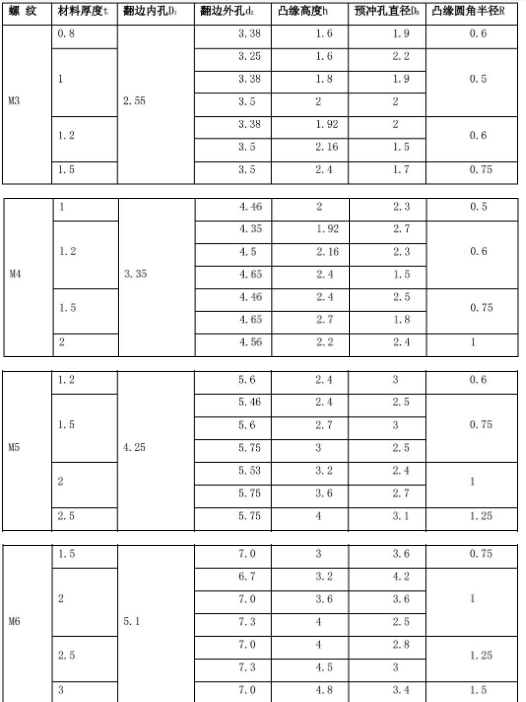
Proceso de procesamiento de chapa metálica - remachado de otras piezas auxiliares de chapa metálica procesadas, como tuercas remachadas, pernos remachados, columnas guía remachadas, etc.
2. dientes de ataque de agujeros roscados en la chapa metálica.
Espesor de la placa de chapa T & lt; A las 1.5, se utilizó un ataque de borde. Cuando el espesor de la chapa metálica es t1.5, se puede utilizar un ataque directo.
Proceso de procesamiento de chapa metálica - la soldadura debe implementarse en el diseño de la estructura de soldadura de chapa metálica, "organizar simétricamente las costuras de soldadura y los puntos de soldadura, y evitar la confluencia, aglomeración y superposición, las costuras de soldadura secundarias y los puntos de soldadura pueden interrumpirse, y las costuras de soldadura principales y los puntos de soldadura deben conectarse".
La soldadura por arco eléctrico, la soldadura por resistencia, etc. se utilizan comúnmente en la chapa metálica.
Debe haber suficiente espacio de soldadura entre las placas metálicas de soldadura por arco, el espacio máximo de soldadura debe ser de 0,5 a 0,8 mm, y la soldadura debe ser uniforme y plana.
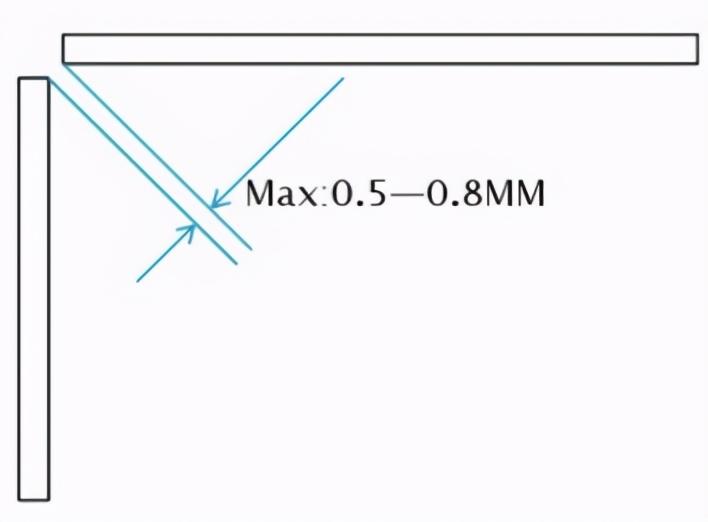
2. la superficie de soldadura de soldadura por resistencia eléctrica debe ser plana, sin pliegues, rebote, etc.
Las dimensiones de la soldadura por resistencia son las siguientes:
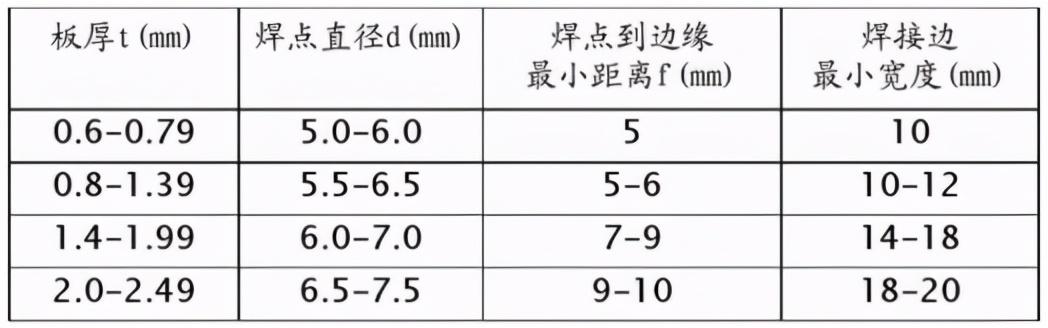
Distancia entre los puntos de soldadura de Resistencia
En la aplicación práctica, al soldar piezas pequeñas, se pueden consultar los datos de la siguiente tabla.
Al soldar piezas de gran tamaño, la distancia entre los puntos se puede aumentar adecuadamente, generalmente no menos de 40 - 50 mm, y en las Partes no estresadas, la distancia entre los puntos de soldadura se puede ampliar a 70 - 80 mm.
Espesor de la placa t, diámetro del punto de soldadura d, diámetro mínimo del punto de soldadura dmin, distancia mínima e entre los puntos de soldadura, si la placa es una combinación de diferentes grosores, se selecciona de acuerdo con la placa más delgada.
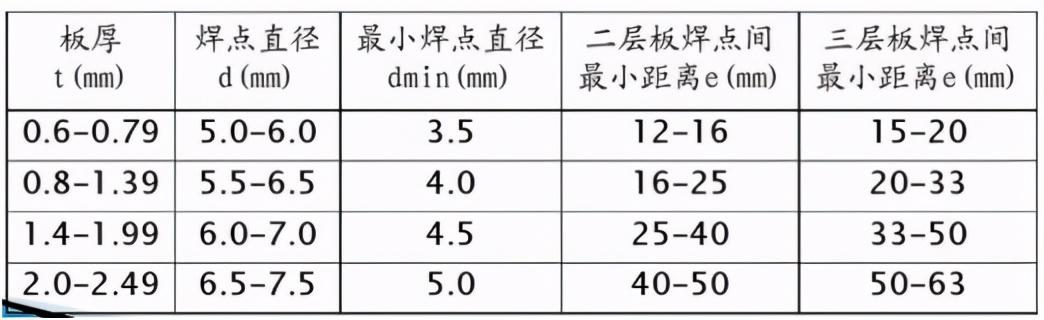
Número de capas y relación de espesor de la placa de soldadura por resistencia eléctrica
Las placas soldados por puntos de Resistencia son generalmente de 2 capas, hasta 3 capas, y la relación de espesor de las placas de cada capa de la Junta de soldadura debe estar entre 1 / 3 y 3.
Si realmente se necesita soldadura de placas de 3 capas, primero se debe comprobar la relación de espesor del material, si es razonable, se puede soldar, si no es razonable, se debe considerar abrir el agujero de proceso o la brecha de proceso, soldadura de 2 capas, escalonar los puntos de soldadura.
Proceso de procesamiento de chapa metálica - método de conexión aquí se introduce principalmente el método de conexión de la chapa metálica en el proceso de procesamiento, principalmente remachado de remaches, soldadura (mencionado anteriormente), remachado de agujeros de extracción, remachado tox.
Remachado de remaches: este tipo de remachado a menudo se llama remachado de tracción, y el remachado de dos placas a través del remachado de tracción se llama remachado de tracción. la forma común de remachado es la siguiente:
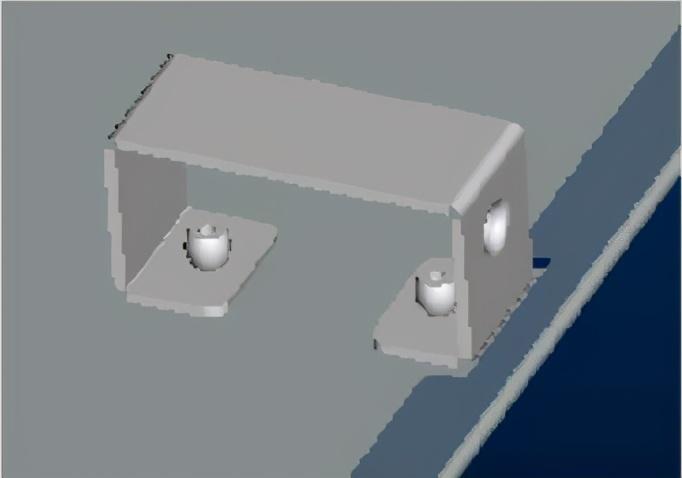
2. soldadura (mencionada anteriormente) 3. remachado de agujeros de extracción: una de las piezas es un agujero de extracción y la otra es un agujero hundido, que se convierte en una conexión no desmontable a través del remachado.
Superioridad: el agujero de extracción y el agujero hundido que coincide con él tienen una función de posicionamiento en sí mismo. La resistencia del remachado es alta y la eficiencia del remachado a través del molde también es relativamente alta.
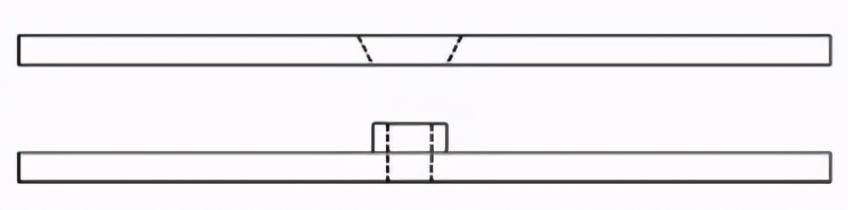
4. remachado tox: presione la pieza conectada en la cóncava a través de un simple punzón. Bajo una mayor presión, el material dentro de la matriz cóncava "fluye" hacia afuera. Como resultado, se produce un punto de conexión circular sin bordes ni rebabas y sin afectar su resistencia a la corrosión, incluso las placas con recubrimiento o pintura en la superficie pueden conservar las características anticorrosivas originales, ya que el recubrimiento y la pintura y las placas también pueden conservar las características anticorrosivas originales, ya que el recubrimiento y la pintura también se deforman y fluyen juntas. El material se aprieta a ambos lados y se aprieta en la pieza de la placa en el lado de la matriz cóncava, formando así un punto de conexión tox. Como se muestra en la siguiente imagen:
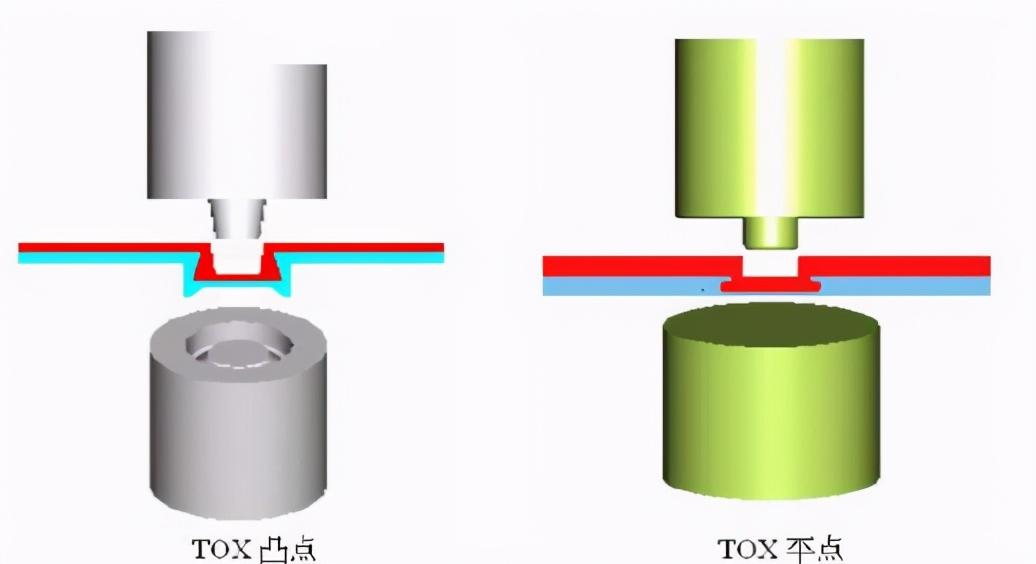
Proceso de procesamiento de chapa metálica - el tratamiento de la superficie de la chapa metálica puede desempeñar un papel de protección anticorrosiva y decoración. Los tratamientos de superficie comunes de la chapa metálica son: pulverización en polvo, galvanización eléctrica, inmersión en caliente en zinc, oxidación de la superficie, dibujo de la superficie, serigrafía, etc.
Antes del tratamiento de la superficie de la chapa metálica, se debe eliminar el aceite, la roya, la escoria de soldadura, etc. de la superficie de la chapa metálica.
Pulverización en polvo: hay dos tipos de pulverización en la superficie de la chapa metálica: pintura líquida y pintura en polvo. lo que usamos comúnmente es pintura en polvo. a través de la pulverización en polvo, adsorción estática, cocción a alta temperatura, etc., Se pulveriza una capa de pintura de varios colores en la superficie de la chapa metálica para embellecer la apariencia y aumentar la resistencia a la corrosión del material. Es un método común de tratamiento de superficie.
Nota: habrá una cierta diferencia de color en el color rociado por diferentes fabricantes, por lo que la chapa metálica del mismo color del mismo equipo debe pulverizarse en el mismo fabricante tanto como sea posible.
2. la galvanización de la superficie de las láminas de zinc galvanizadas en caliente y en caliente es un método común de tratamiento anticorrosivo de la superficie y puede desempeñar un cierto papel en el embellecimiento de la apariencia. La galvanización se puede dividir en galvanización eléctrica y galvanización en caliente.
La apariencia de la galvanización eléctrica es relativamente brillante y plana, y la capa de galvanización es relativamente delgada, que es más común.
La capa de zinc galvanizado en caliente es más gruesa y puede producir una capa de aleación de hierro y zinc, que tiene una mayor resistencia a la corrosión que la galvanización eléctrica.
3. oxidación superficial: aquí se presenta principalmente la anodización superficial de aluminio y aleaciones de aluminio.
La anodización superficial del aluminio y las aleaciones de aluminio se puede oxidar en varios colores, desempeñando un papel protector y un buen papel decorativo. Al mismo tiempo, se puede producir una película de óxido anódico en la superficie del material, que tiene una alta dureza y resistencia al desgaste, así como una buena propiedades de aislamiento eléctrico y aislamiento térmico.
4. dibujo de superficie: colocar el material entre las ruedas de rodillos superiores e inferiores de la máquina de dibujo, que se adhieren con cinturones de arena, impulsados por motores, para que el material pase por los cinturones de arena superiores e inferiores, sacando rastros en la superficie del material, según los diferentes cinturones de arena, el grosor de los rastros también es diferente, La función principal es embellecer la apariencia. Por lo general, el aluminio considera el tratamiento de la superficie con alambre.
5. el proceso de serigrafía con varios logotipos en la serigrafía de la superficie del material generalmente tiene dos métodos: serigrafía plana e impresión de desplazamiento. la serigrafía plana se utiliza principalmente en el plano general, pero si se encuentra con un lugar con una fosa más profunda, es necesario usar la impresión de desplazamiento.
La impresión de seda debe tener una impresión de seda.
Accesorios de referencia para la precisión del mecanizado de chapa metálica:
Tolerancia de las dimensiones de las piezas estampadas gbt13914 - 2002
Tolerancia del ángulo de las piezas de estampado gbt13915 - 2002 - T
GB - t15005 - 2007 estampado sin tolerancia desviación límite
GB - T 13916 - 2002 estampado sin tolerancia en forma y posición
Capacidad de los equipos de procesamiento de chapa metálica comunes alcance del procesamiento de los equipos de chapa metálica comunes
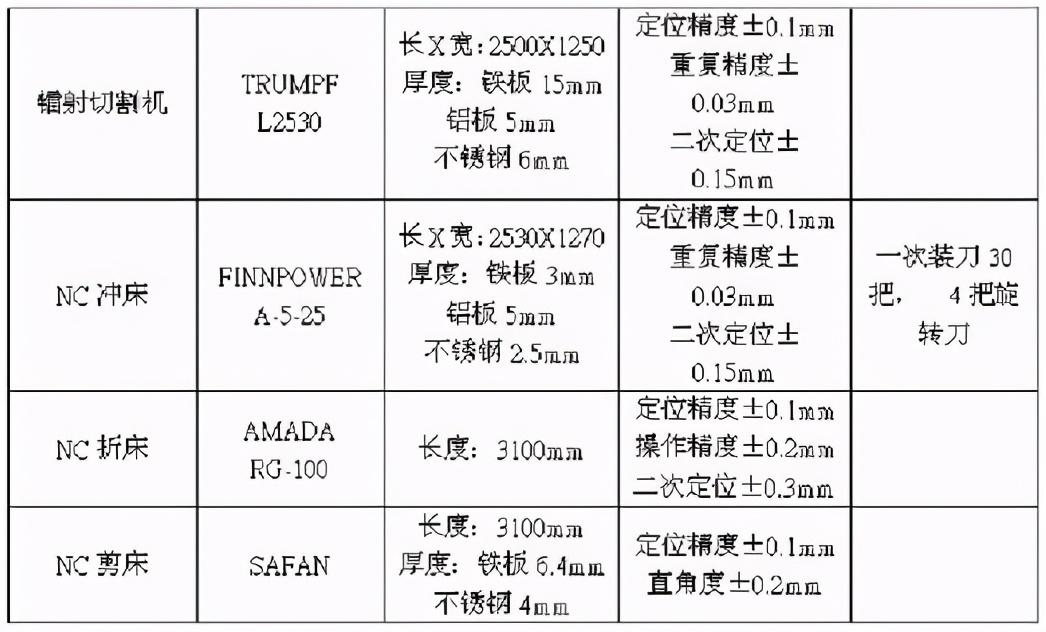