Análisis del proceso de soldadura del montaje de procesamiento de chapa metálica
El procesamiento de chapa metálica es muy común en la producción de la industria mecánica, es una parte importante de la producción mecánica y tiene una amplia gama de aplicaciones en automóviles, aeroespacial y otros campos. Determina directamente la apariencia de la máquina y refleja su madurez. Con el rápido desarrollo de la industria de fabricación de maquinaria, la forma de las piezas de chapa metálica se ha vuelto cada vez más compleja. Los procesos de cálculo, flexión, soldadura y pulverización del desarrollo de materiales metálicos determinan directamente si las piezas de chapa metálica pueden tener una buena apariencia, suficiente resistencia y la precisión necesaria. Por lo tanto, calcular con precisión su tamaño de despliegue se ha convertido en la tarea principal del diseño de la chapa metálica, y la flexión de la chapa metálica es un proceso muy importante en el proceso de procesamiento de la chapa metálica. La calidad del proceso de flexión afecta directamente el tamaño y la apariencia de las piezas, especialmente la calidad del proceso de montaje y soldadura posterior. Desde el punto de vista del proceso, combinado con el proceso de producción real, este artículo analiza el cálculo del desarrollo de la chapa metálica, el proceso de flexión, la soldadura, la pulverización y otros procesos, y propone soluciones al problema.
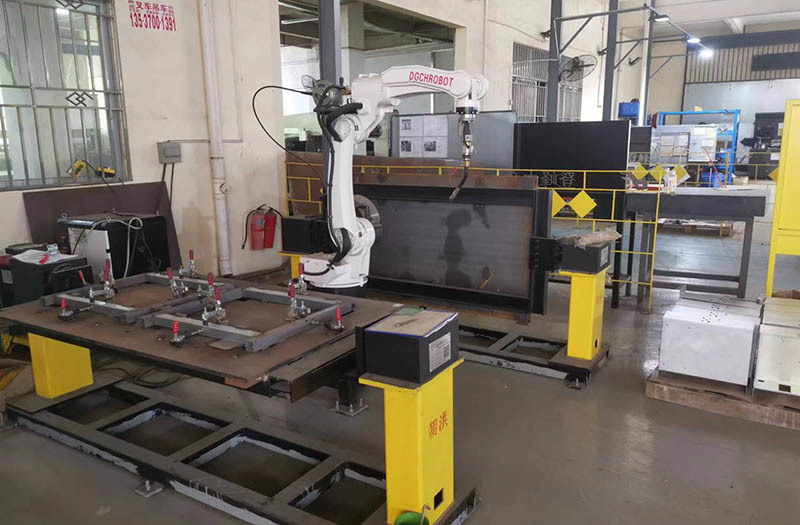
Antes de que comience el trabajo de flexión, es necesario calcular con precisión las dimensiones de cada pieza después del despliegue, así como la ubicación de sus ranuras o agujeros en el dibujo. Esto es para resolver el problema de que la diferencia entre la posición del agujero y el tamaño general causada por el corte láser excede la tolerancia. El material exterior se alargará bajo el momento de flexión de la placa metálica interior, pero la longitud de la capa neutra no cambiará entre el estiramiento y la compresión. Por lo tanto, en términos generales, calcular la longitud de desarrollo de las piezas de chapa metálica es calcular la longitud de la capa neutral. La longitud real del componente de chapa metálica es la suma de su longitud recta y la longitud de la capa neutra. La longitud de la capa característica está estrechamente relacionada con el tipo de material utilizado, el grosor y el molde. Sin embargo, en el mecanizado real, debido a que el molde y el radio de flexión de la pieza de chapa metálica son los mismos, el cálculo del radio de flexión es un algoritmo simple sin requisitos especiales, mientras que el tamaño del radio de flexión real se ignora básicamente. A continuación se dan 90. Método de cálculo simplificado para piezas dobladas. La fórmula de cálculo simple es la siguiente: L = D1 + d2 - a
Entre ellos, l es la longitud desplegada y D1 y D2 son 90. Cuando se dobla, los dos bordes rectangulares de la pieza son su tamaño total y a es su valor de compensación de flexión. El algoritmo es adecuado para la mayoría de las piezas dobladas de chapa metálica en el procesamiento de chapa metálica, especialmente cuando el radio de flexión está entre 0,5 mm y 2 mm, y el espesor de la placa es inferior a 2,5 mm, el cálculo es muy conveniente.
Sin embargo, en la producción y la vida real, en la mayoría de los casos, se desconoce el valor de compensación de flexión de las piezas de chapa metálica. En este momento, es necesario usar & ldkuo; Prueba de flexión & rdkuo; Método para obtener su valor de compensación de flexión. Las operaciones específicas son las siguientes: primero, se utilizan máquinas herramienta para cortar dos materiales cuadrados de igual tamaño del proveedor de materiales a probar, luego se miden con precisión las dimensiones en ambas direcciones, luego se doblan en direcciones paralelas y verticales, y luego se miden las longitudes de los dos lados rectos después de la flexión. En este momento, el valor de compensación de flexión es igual a la longitud de dos ángulos rectos y la longitud del material cuadrado original, de modo que se pueden obtener valores de compensación en todas las direcciones de la materia prima.