他の熱切断方法と比較して、レーザー切断の一般的な特徴は、高速切断と高品質です。具体的には、次の側面に要約されます。
(1)良好な切断品質
レーザースポットが小さく、エネルギー密度が高く、切断速度が速いため、レーザー切断はより良い切断品質を達成できます。
①レーザー切断は細く、切断継ぎ目は両側が平行で表面に垂直であり、切断部品のスケール精度は0.05 mmに達する可能性があります。
②切断面は滑らかで美しく、表面粗さはわずか数十ミクロンで、レーザー切断でも最終工程として使用でき、機械加工を必要とせず、部品を直接使用できます。
③データをレーザー切断した後、熱影響部の幅が非常に小さく、隣接するデータの切断継ぎ目の性能にほとんど影響がなく、ワークピースの変形が小さく、切断精度が高く、切断継ぎ目の形状がいくつかあります。良好であり、切断継ぎ目の断面形状は比較的規則的な長方形を示しています。レーザー切断、オキシアセチレン切断、プラズマ切断方法の比較を表1に示します。切断材料は厚さ6.2 mmの低炭素鋼板です。
(2)高い切断効率レーザーの透過特性により、レーザー切断機には複数のCNCテーブルが装備されており、切断プロセス全体でCNCを実現できます。操作時には、CNCプログラムを変更するだけで、さまざまな形状の部品の切断に適用でき、2 D切断と3 D切断の両方を実現できます。
③切開速度が速い
厚さ2 mmの低炭素鋼板を1200 Wのレーザーで切断すると、切断速度は600 cm/minに達する可能性があります。厚さ5 mmのポリプロピレン樹脂板を切断すると、切断速度は1200 cm/minに達する可能性があります。レーザー切断時にデータをクランプして固定する必要がないため、工具治具を節約できるだけでなく、材料の上下の補助時間も節約できます。
(4)非接触切開
レーザー切断時にトーチとワークは接触せず、物の摩耗は存在しない。異なる形状の部品を加工するには、「工具」を交換する必要はなく、レーザーの出力パラメータを変更するだけでよい。レーザー切断プロセスは騒音が低く、振動が小さく、汚染がない。
切開資料の品種が多い
オキシアセチレン切断やプラズマ切断と比較して、レーザー切断材料には、金属、非金属、金属ベースおよび非金属ベースの複合材料、皮革、木材、繊維など、さまざまな種類があります。ただし、異なる材料に関しては、それ自体の熱物理的特性とレーザーの吸収率が異なるため、異なるレーザー切断適応性を示します。CO2レーザーを選択すると、さまざまな材料のレーザー切断性能を表2に示します。
短所レーザー切断レーザーの出力と装置のサイズによって制限されるため、レーザー切断は中程度の厚さのシートとパイプしか切断できず、ワークピースの厚さが増すにつれて切断速度が大幅に低下します。
レーザー切開設備は費用が高く、一括出資が大きい。
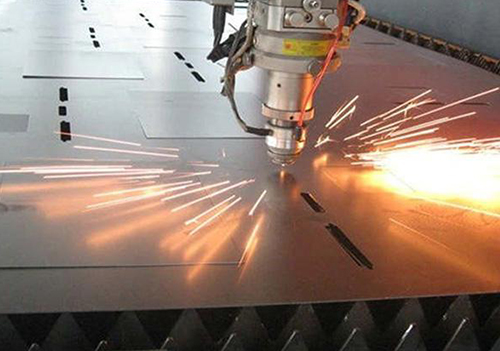