Toimetaja korraldab kõigile palju praktilisi teadmisi ja kuumi uudiseid. Palun pöörake rohkem tähelepanu ja teile esitatakse paremat sisu.
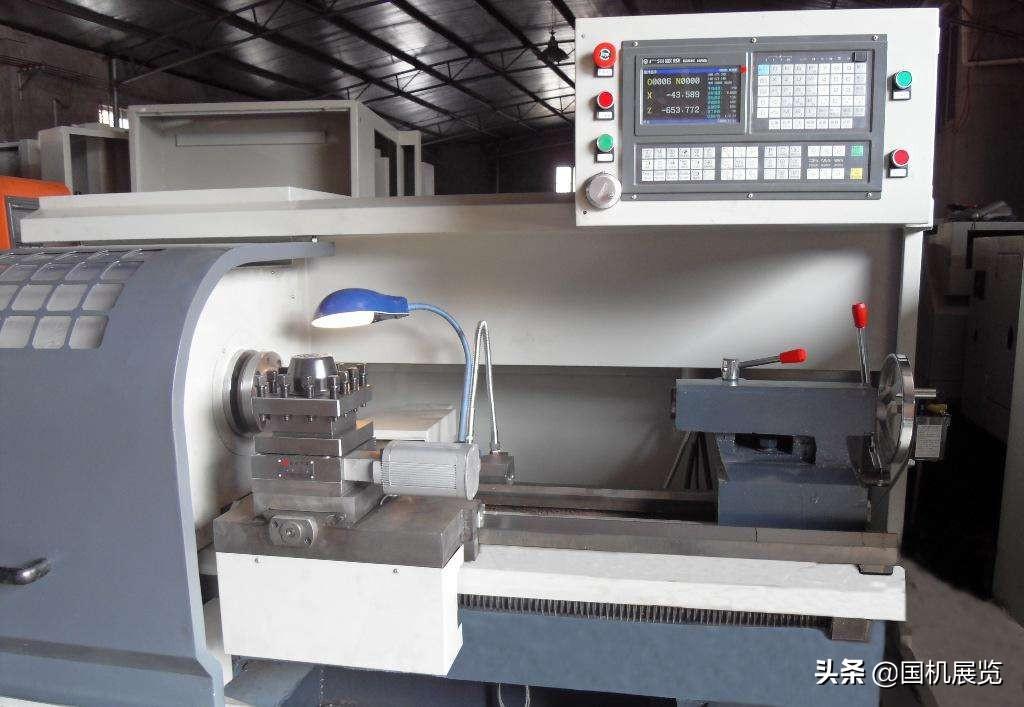
CNC treipingil on võimalik töödelda neli standardset keermet: meetriline, toll, moodul ja radiaalne. Olenemata sellest, millist tüüpi keermet töödeldakse, tuleb treipingi ja tööriista vahel säilitada range liikumissuhe: see tähendab, et treipingi iga pöörlemise (st ühe pöörlemise) korral peab tööriist liikuma ühtlaselt ühe plii kauguse (töödeldava detaili) võrra. Analüüsides tavalisi niite, püüame parandada oma arusaamist nendest, et neid paremini töödelda.
1,Tavaliste niitide mõõtmete analüüs
Tavaliste keermete töötlemine CNC treipidega nõuab mitmeid mõõtmeid ning tavaliseks keermetöötlemiseks vajalik suuruse arvutamine ja analüüs hõlmavad peamiselt järgmist kahte aspekti:
1. Töödeldava detaili läbimõõt enne keermestamist
Arvestades keermeprofiili laienemist keermetöötluse ajal, on töödeldava detaili läbimõõt enne keermetöötlemist d / d-0,1p, mis on keermevahe vähendamine 0,1 võrra keerme suuremast läbimõõdust. Üldiselt, materjali deformatsioonivõime põhjal, võetakse väiksem läbimõõt 0,1 kuni 0,5 võrreldes keerme suurema läbimõõduga.
2. Keermetöötluse söötmise kiirus
Keerme sisestamise kogus võib viidata keerme põhjaläbimõõdule, mis on keermelõikuri lõplik lõikeasend.
Niidi läbimõõt on: suur läbimõõt -2 korda hamba kõrgus; Hamba kõrgus = 0,54p (p on samm)
Keermetöötluse söödakiirust tuleks pidevalt vähendada ning spetsiifiline söödakiirus tuleks valida tööriista ja töötlusmaterjali põhjal.
2,Tavaliste niitide lõikamise tööriistade montaaž ja ühtlustamine
Kui lõiketööriist on paigaldatud liiga kõrgele või liiga madalale või liiga kõrgele, kui lõikamine jõuab teatud sügavuseni, surub lõiketööriista tagakülg töödeldava detaili vastu, suurendades hõõrdumist ja isegi painutades töödeldava detaili, põhjustades tööriista hammustamise nähtust; Kui kiip on liiga madal, on kiipe tühjendamine raske. Treimistööriista radiaalse jõu suund asub töödeldava detaili keskel. Lisaks on põikkruvi ja mutri vaheline kliirens liiga suur, mis põhjustab lõikesügavuse automaatset suurenemist, tõstes seeläbi töödeldava detaili ja põhjustades tööriista hammustamist. Selles punktis tuleb treimistööriista kõrgust õigeaegselt reguleerida, et tagada, et selle ots oleks töödeldava detaili teljega samal kõrgusel (tööriista saab joonda tagaosa otsaga). Töötlemata ja pooltäpse töötlemise ajal on tööriista otsa asend umbes 1% d kõrgem kui töödeldava detaili keskpunkt (d tähistab töödeldava detaili läbimõõtu).
Töödeldavat detaili ei saa kindlalt kinnitada ja selle jäikus ei talu treimise ajal lõikejõudu, mis põhjustab liigset paindumist ning lõiketööriista ja töödeldava detaili vahelise keskõrguse muutmist (töödeldav detail on tõstetud), põhjustades äkilist lõikesügavuse suurenemist ja tööriista hammustamist. Sel ajal tuleb töödeldav detail kindlalt kinnitada ning tagasilõikeotsi saab kasutada töödeldava detaili jäikuse suurendamiseks.
Tavaliste keermete joondamise meetodid hõlmavad katselõikamist ja automaatset joondamist tööriista joondamisseadmega. Tööriista saab otse kasutada katselõikamiseks või töödeldava detaili nullpunkti saab seadistada G50-ga ja töödeldava detaili nullpunkti saab seadistada töödeldava detaili liikumisega joondamiseks. Nõuded tööriistade joondamisele keermetöötluses ei ole väga kõrged, eriti z-suunas, kus puuduvad ranged piirangud tööriistade joondamisele, mida saab määrata vastavalt programmeerimise mehaanilise nõuetele.
3,Tavaliste keermete programmeerimine ja töötlemine
Praegustes CNC treipingides on keermelõikamiseks üldjuhul kolm mehaanilist meetodit: g32 sirgelõikamismeetod, g92 sirgelõikamismeetod ja g76 kaldlõikamismeetod. Erinevate lõikamismeetodite ja programmeerimismeetodite tõttu on mehaaniline viga erinev. Peame oma tegevust hoolikalt analüüsima ja püüdma toota ülitäpseid osi.
1. G32 otselõikemeetodil on suur lõikejõud ja raskused lõikamisel tänu mõlema lõikeserva samaaegsele tööle, mistõttu on mõlemad lõikeservad lõikamise ajal kalduvad kuluma. Suurema sammuga niitide lõikamisel on tera kulumine suurema lõikesügavuse tõttu kiirem, mis põhjustab vigu keerme sammu läbimõõdus; Kuid selle töötlemise täpsus on suhteliselt kõrge, nii et seda kasutatakse tavaliselt väikese sammuga keermetöötlemiseks. Tänu oma tööriista liikumisele ja lõikamisele programmeerimise kaudu on mehaaniline programm suhteliselt pikk; Tera lihtsa kulumise tõttu tuleb töötlemise ajal sageli mõõta.
2. g92 otsese lõikamise meetod lihtsustab programmeerimist ja parandab tõhusust võrreldes g32 juhendiga.
3. G76 kaldu lõikemeetod on tänu oma ühepoolsele serva töötlemisele kalduv töötlustera kahjustustele ja kulumisele, mille tulemuseks on ebaühtlased keermestatud pinnad ja tööriista otsa nurga muutused, mis põhjustavad halva hammasprofiili täpsuse. Ühepoolse tera töö tõttu on tööriista koormus suhteliselt väike, laastude eemaldamine lihtne ja lõikesügavus väheneb. Seetõttu sobib see töötlemismeetod üldiselt suurte sammudega keermete töötlemiseks. Tänu oma lihtsale kiibi eemaldamisele ja headele terade töötlemistingimustele on see mehaaniline meetod mugavam olukordades, kus suurt keermetäpsust ei ole vaja. Suure täpsusega keermete töötlemisel saab töötlemise lõpuleviimiseks kasutada kahte lõikamist, kasutades esmalt töötlemata treimiseks G76 mehaanilist meetodit ja seejärel peenesttreimiseks G32 mehaanilist meetodit. Siiski on oluline märkida, et lõiketööriista lähtepunkt peaks olema täpne, vastasel juhul on lihtne vigu teha ja osade lammutamine.
4. Pärast keermetöötluse lõpuleviimist saab hinnata niidi kvaliteeti, jälgides niidiprofiili ja võttes õigeaegseid meetmeid. Kui keermeotsa ei ole suunatud, suurendab noa lõikekoguse suurendamine tegelikult niidi läbimõõtu, mis sõltub materjali plastilisusest. Kui harja on teritatud, vähendab noa lõikekoguse suurendamine proportsionaalselt läbimõõtu.
4,Tavaliste niitide kontrollimine
Üldiste standardkeermete puhul kasutatakse mõõtmiseks keermerõngamõõdikuid või pistikumõõdikuid. väliskeermete mõõtmisel, kui keer; Läbimine lõpust "; Rõngamõõtur pöörleb täpselt sisse ja; End to End "; Kui rõngamõõturit ei saa kruvida, näitab see, et töödeldud keer vastab nõuetele, vastasel juhul on see kvalifitseerimata. Sisekeermete mõõtmisel kasutage keermepistiku mõõdikut ja mõõtke sama meetodit kasutades. Lisaks mõõtmisele keermerõngamõõturitega või pistikumõõturitega võib mõõtmiseks kasutada ka muid mõõtevahendeid. Kasutage keermemikromeetrit keermevahe läbimõõdu mõõtmiseks, kasutage hamba paksuse vernieri kaliiperi trapetsiidaalse keermevahe läbimõõdu, hamba paksuse ja ussivahe läbimõõdu mõõtmiseks ning kasutage mõõtenõela, et mõõta keermevahe läbimõõt vastavalt kolme nõela mõõtmismeetodile.