Prozesazio mekanikoa laneko zatiak makineratzeko metodo bat da nahi duen forma eta tamaina moztzeko, sartzeko, argitzeko eta beste metodoak. Prozesazio mekanikoan zehaztasun zatiak lortzea oso arazo garrantzitsua da. Zatien zehaztasunak zehaztasun dimenzionala, forma zehaztasuna eta posizioaren zehaztasuna ditu. Behean, zehaztasunez, prozesazio mekanikoa nola gertatzen den zehaztasun parte batzuk, makina-tresna hautapena, tresna hautapena, prozesu-parametro hautapena eta prozesu-kontrola bezalako aspektu batzuetatik, zehaztasun zehaztasuna erakusten dug
Lehenengo, makina egokia hautatzea garrantzitsua da zatien zehaztasuna seguratzeko. Makinaren tresnaren rigiditatea eta stabilitatea oso inportanteak dira. Zehaztasun handiko beharrezko zatiak hautatu beharko litzateke, berdintasun handi eta stabilitate ona duten makina tresnak. Gainera, makinaren tresnaren zehaztasuna ere garrantzitsua da, adibidez, gidaren trafikoaren zehaztasuna, sarreraren gaitasuna eta stabilitatea, eta abar. Faktore hauek guztiak parteen makina-zehaztasunaren eragina dute.
Bigarrenik, mozketa-tresna egokia hautatzeak parteen makina-zehaztasuna hobeto dezake. Kalitatea, gogortasuna eta tresnak moztzeko resistentzia eragiten dute makina-zehaztasunari zuzenean. Kalitate handiko tresnaren materialak eragintza ongi mozten dute, zerbitzu luzeak bizitza, eta zehaztasun hobeak mantentzeko eragintza. Ertzaren formak, gorputz-angeluak eta tresnaren gorputz-angeluak ere eragin handia dute zatiaren makina-zehaztasunaren gainean. Horregatik, makina mekanikoaren prozesuan, mozteko tresna egokia hautatzeak makina-zehaztasuna eraginez hobeto dezake.
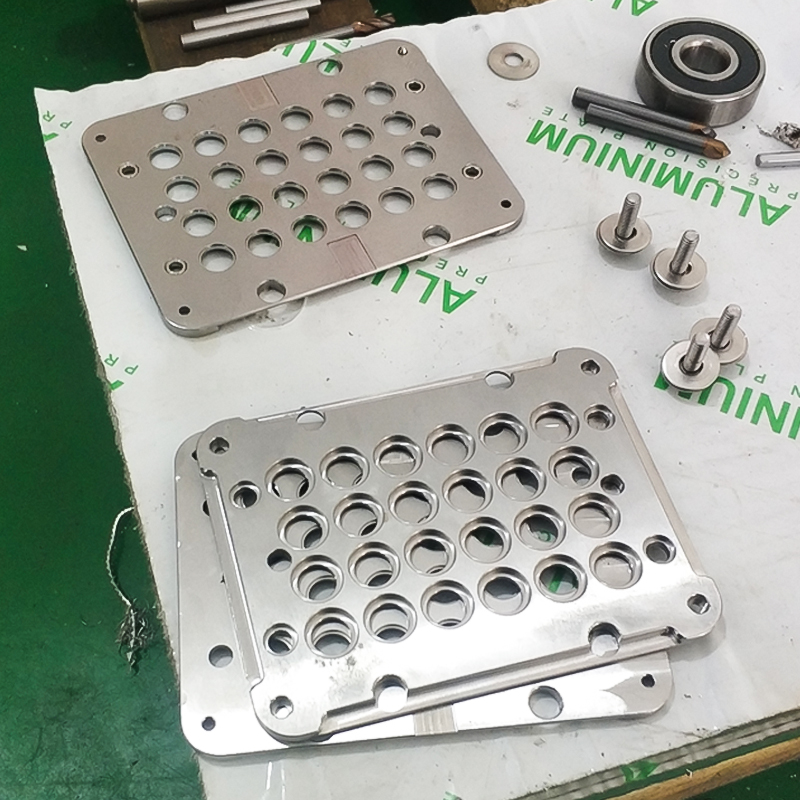
Gainera, prozesuaren parametroen hautapena arrazoizkoa da zati zehatza lortzeko gakoa. Prozesuaren parametroak abiadura moztea, iturburu-tasa eta sakonera moztea dute. Parametro horien hautapena zuzenean eragin egingo du indarrak moztea eta temperatura moztea bezalako faktoreak, zeinak, orduan, zatien makina-kalitatea eta zehaztasuna eragin dezake. Prozesatze mekanikoaren prozesuan, prozesuaren parametro egokia hautatzea, funtzionaren material eta forma, tresna mota eta funtzioak zatien makina-zehaztasun handia lor dezake.
Azkenean, prozesuaren kontrola ona ere bide garrantzitsua da zatien zehaztasuna hobetzeko. Prozesuaren kontrola, tresna kontrola eta eragiketa kontrola barne. Prozesu zientifikoa eta arrazoigabea kontrolak erroreak eraginkorki gutxiago ditzake eta prozesu mekaniko maila bakoitzean makina-zehaztasunean fluktuakzioak minimizatu ditzake. Adibidez, iturburu-kontrolan, itxitako zirkulu-kontrol sistema batek erabiliz iturburu-abiaduraren eta posizioaren zehaztasunaren kontrola zehatz lor dezake; Erakutsi prozesuaren bitartean, tresna-konpensazio-sistema automatiko baten erabilera tresna-bizitza denbora batean doitu dezake, tresna-eragiketa eta makina-zehaztasuna seguru dezake. Horregatik, prozesuaren kontrola ona zatien zehaztasun handia lortzeko gakoa da.
Lehentasunean, prozesatze mekanikoan parte zehatza lortzeko gakoa makina-tresna egokia hautatzea da, tresna moztea, prozesuaren parametroak eta prozesuaren kontrola. Egiazko produkzioan, prozesatzeko metodoak eta erlazionatutako parametroak hautatu behar dira laneko zatiaren beharrez zehatz oinarrituta, karaktere materialekin eta prozesatzeko teknologiaren beharrez batera. Prozesazio mekanikoaren maila teknikoa eta kalitate-ziurtasunaren gaitasuna etengabe optimizatzen eta hobetzean, hobe dezakegu zati-zehatzaren beharreak.