Levyn käsittely on kattava kylmätyöstöprosessi metallilevyille (yleensä alle 6 mm), mukaan lukien leikkaus, lävistys, taivutus, hitsaus, niittäminen, muottimuovaus ja pintakäsittely. Sen näkyvä piirre on, että saman osan paksuus on yhtenäinen.
Levyn käsittelymenetelmä: Ei muottikäsittely: Levyn käsittely laitteiden, kuten numeerisen lävistyksen, laserleikkauksen, leikkauskoneiden, taivutuskoneiden, niittokoneiden jne. avulla Sitä käytetään yleensä näytteen tuotantoon tai pieniin erätuotantoon, korkeilla kustannuksilla. Lyhyt käsittelysykli ja nopea reagointi. Muottien käsittely: Käyttämällä kiinteitä muotteja levyjen käsittelyyn on yleensä leikkausmuotteja ja muovausmuotoja, joita käytetään pääasiassa massatuotantoon pienemmillä kustannuksilla. Alkuperäiset muotikustannukset ovat korkeat, ja osien laatu on taattu. Varhainen käsittelysykli on pitkä ja muottikustannukset ovat korkeat. Levyn käsittely prosessi: leikkaus: numeerinen lävistys, laserleikkaus, leikkauskone
Muovaus - taivutus, venytys, lävistys: taivutuskoneet, lävistyskoneet jne.
Muu käsittely: niittaus, kierteitys jne.
Hitsaus: levyjen liitäntämenetelmä
Pintakäsittely: jauheruiskutus, galvanointi, langan piirtäminen, serigrafia jne.
Levyn käsittelytekniikka - Levyn tärkeimmät leikkausmenetelmät ovat numeerinen lävistys, laserleikkaus, leikkauskoneet ja muottileikkaus. CNC on tällä hetkellä yleisesti käytetty menetelmä, ja laserleikkausta käytetään enimmäkseen näytteenottovaiheessa (tai voi myös käsitellä ruostumattomasta teräksestä valmistettuja levyosia), joilla on korkeat käsittelykustannukset.
Alla esittelemme pääasiassa ohutlevyn leikkaamisen numeerisella lävistyksellä
Numeerista lävistystä, joka tunnetaan myös nimellä tornin CNC-lävistyskone, voidaan käyttää leikkaamiseen, lävistykseen, venytysreikien, rullaribien, lävistyskaihtimien jne. Sen koneistustarkkuus voi olla +/- 0,1 mm.
CNC työstettävän metallilevyn paksuus on:
Kylmävalssatut ja kuumavalssatut levyt 4,0 mm
Alumiinilevy 5.0mm
Ruostumattomasta teräksestä valmistettu levy 2.0mm
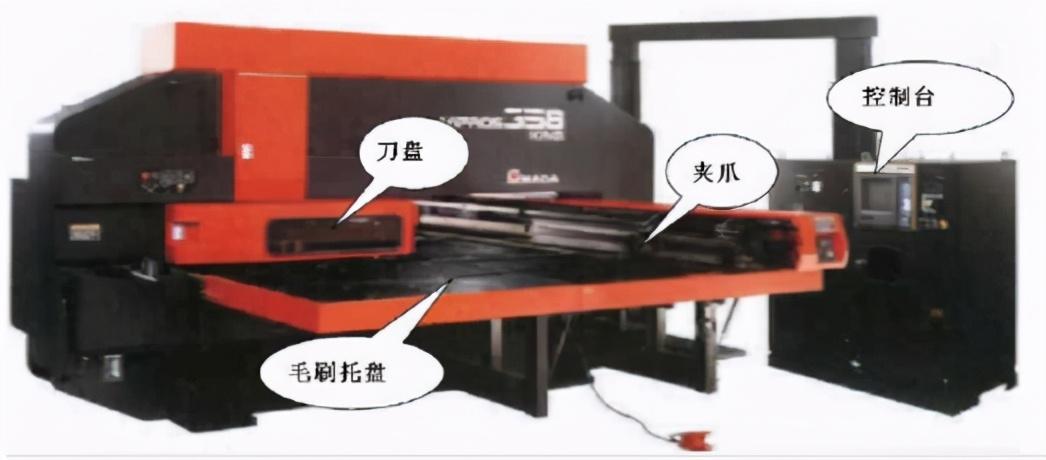
Lävistykseen on asetettu vähimmäiskokovaatimus. Lävistyksen vähimmäiskoko liittyy reiän muotoon, materiaalin mekaanisiin ominaisuuksiin ja materiaalin paksuuteen. (Kuten alla olevassa kuvassa näkyy)
2. Lävistysreikien väli ja reunaetäisyys. Jos osan lävistysreunan ja osan ulkoreunan välinen vähimmäisetäisyys ei ole yhdensuuntainen osan ulkoreunan kanssa, vähimmäisetäisyys ei saa olla pienempi kuin materiaalin paksuus t; Kun rinnakkain, sen ei pitäisi olla pienempi kuin 1,5 t. (Kuten alla olevassa kuvassa esitetään)
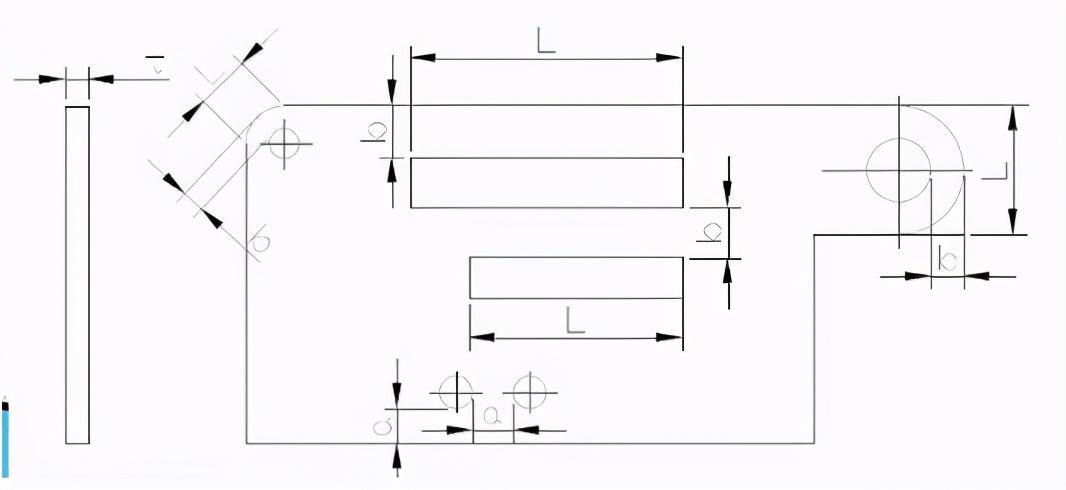
3. Venyttäessä reikiä venytysreiän ja reunan välinen vähimmäisetäisyys on 3T, kahden venytysreiän välinen vähimmäisetäisyys on 6T ja venytysreiän ja taivutusreunan välinen vähimmäisturvallinen etäisyys (sisäpuolella) on 3T + R (T on levypaksuus, R on taivutusfilee)
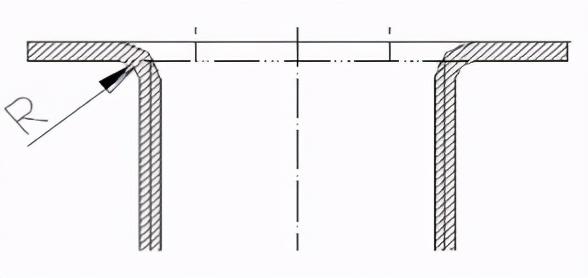
4. Kun reikiä porataan venytettyihin ja taivutettuihin osiin ja syvävedettyihin osiin, reikäseinän ja suoran seinän välillä on pidettävä tietty etäisyys. (Kuten alla olevassa kuvassa esitetään)
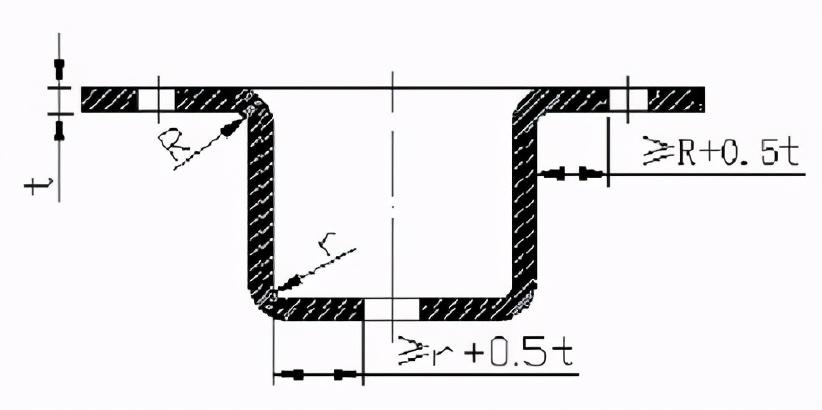
Levyn jalostustekniikka - Levyn muovaukseen kuuluu pääasiassa levyn taivutus ja venytys.
1. Levyn taivutus 1.1 Levyn taivutus käyttää pääasiassa taivutuskoneita.
taittokoneen koneistustarkkuus;
Yksi taitto: +/-0,1 mm
Half Fold: +/-0,2 mm
Yli 20% alennus: +/-0,3 mm
Taivutusprosessin perusperiaatteena on taivuttaa sisältä ulos ja pienistä suuriin. Erityismuodot on taivutettava ensin, eikä edellinen prosessi saa vaikuttaa tai häiritä seuraavia prosesseja muovauksen jälkeen.
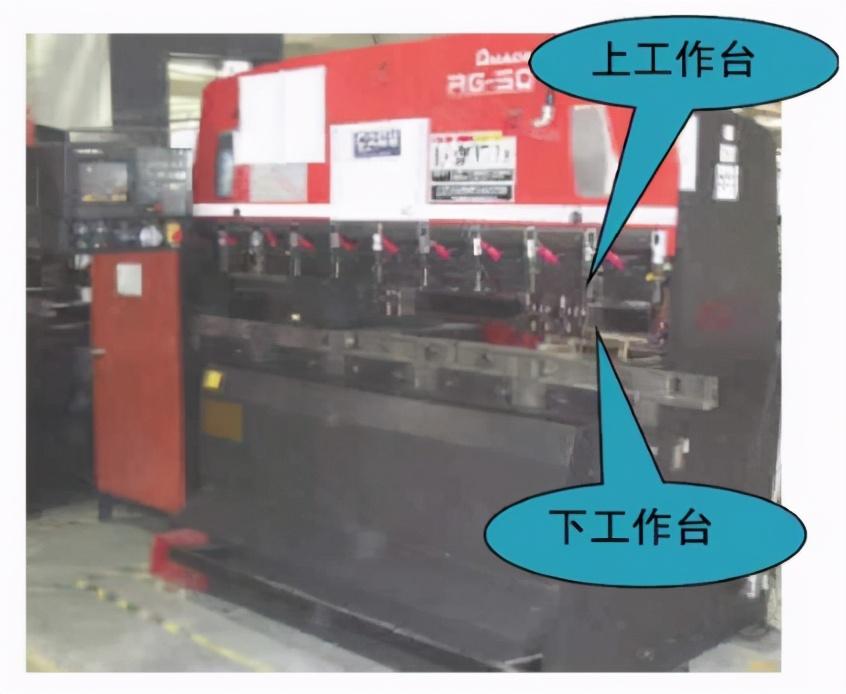
1.3 Yleiset taivutusveitsen muodot:
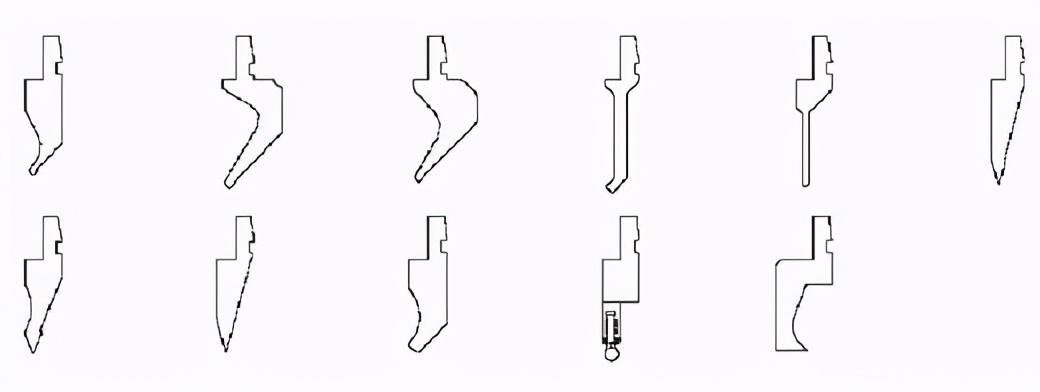
Tavalliset V-uramuodot:
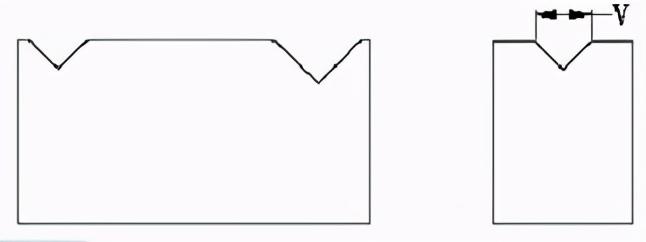
1.4 Taivutettujen osien vähimmäistaivutussäde:
Kun materiaali taivutetaan, ulompi kerros venytetään ja sisäkerros puristetaan pyöristetyllä alueella. Kun materiaalin paksuus on vakio, mitä pienempi sisäinen r, sitä ankarampi materiaalin jännitys ja puristus; Kun ulomman pyöristetyn kulman vetojännitys ylittää materiaalin lopullisen lujuuden, syntyy halkeamia ja murtumia, joten taivutettujen osien rakenteessa tulisi välttää liian pieniä taivutuskulman säteitä. Yrityksen yleisesti käytettyjen materiaalien vähimmäistaivutussäde on esitetty alla olevassa taulukossa.
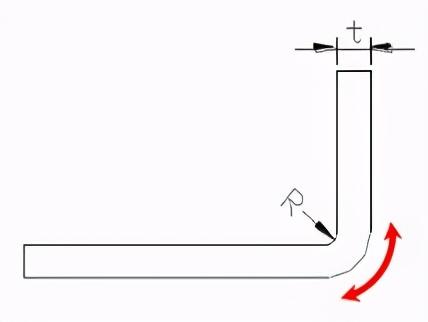
Taivutettujen osien vähimmäistaivutussäde:
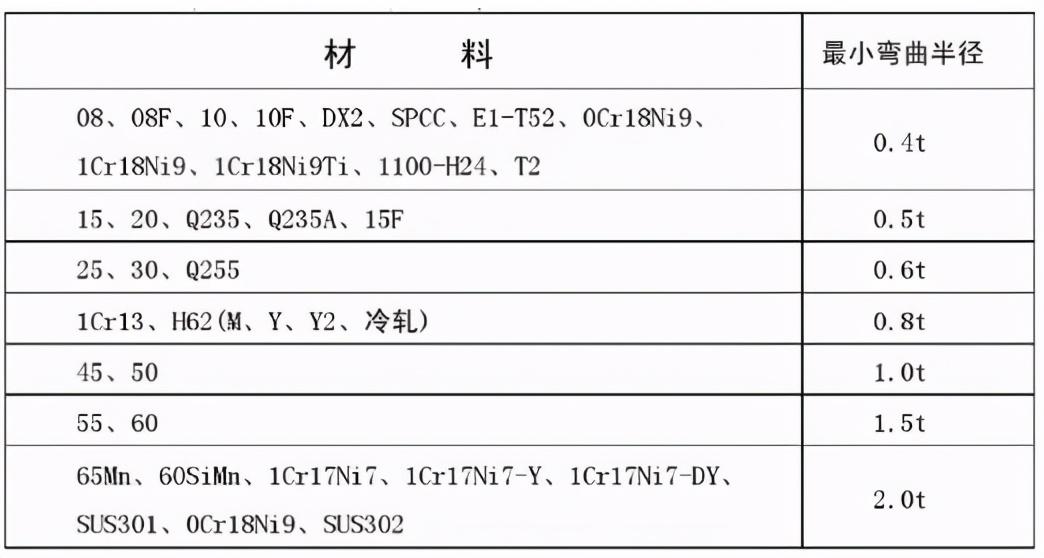
Taivutussäde viittaa taivutetun osan sisäsäteeseen ja t on materiaalin seinämän paksuus.
Taivutetun osan suora reunakorkeus on 1,5:
Yleensä suoran reunan vähimmäiskorkeus ei saa olla liian pieni, ja vähimmäiskorkeus vaatimus on: h>2t
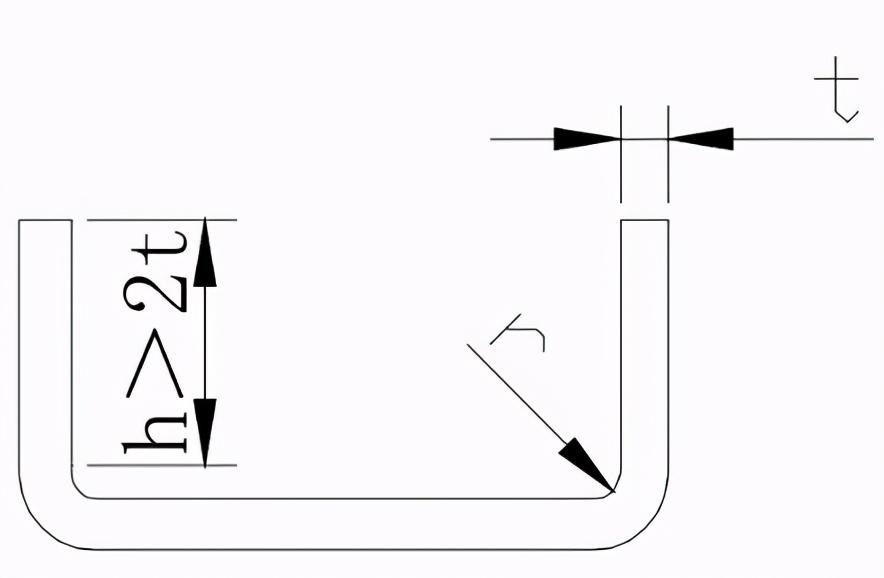
Jos taivutetun osan suora reunakorkeus h2t vaaditaan, lisää ensin taivutusreunan korkeus ja käsittele se sitten vaadittuun kokoon taivutuksen jälkeen; Tai kun olet käsitellyt matalat urat taivutusmuodonmuutosalueella, suorita taivutus.
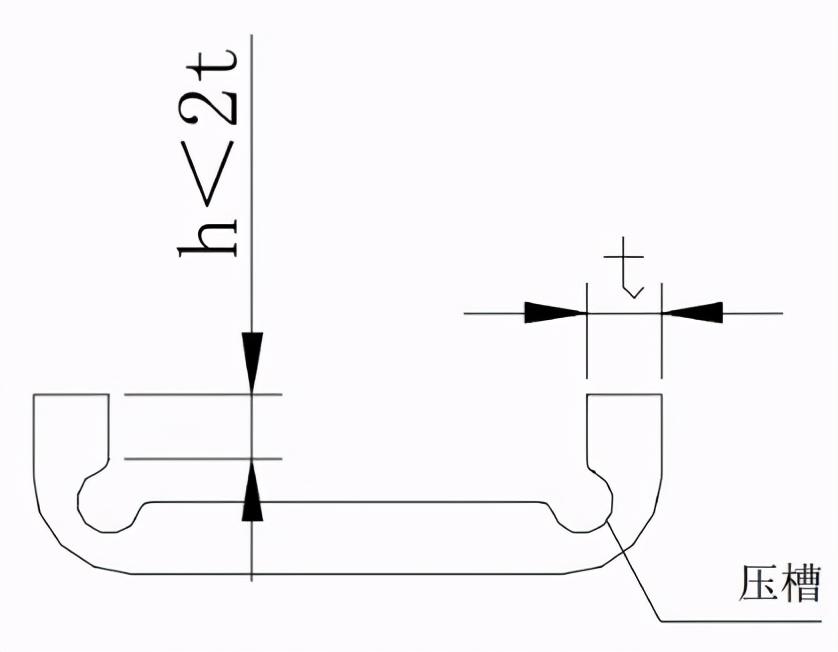
1.6 Suoran taivutusreunan vähimmäiskorkeus kaarevan reunan vinossa kulmassa:
Kun kaareva osa, jossa on viisto reuna, taivutetaan, sivun vähimmäiskorkeus on: h=(2-4) t> 3 mm
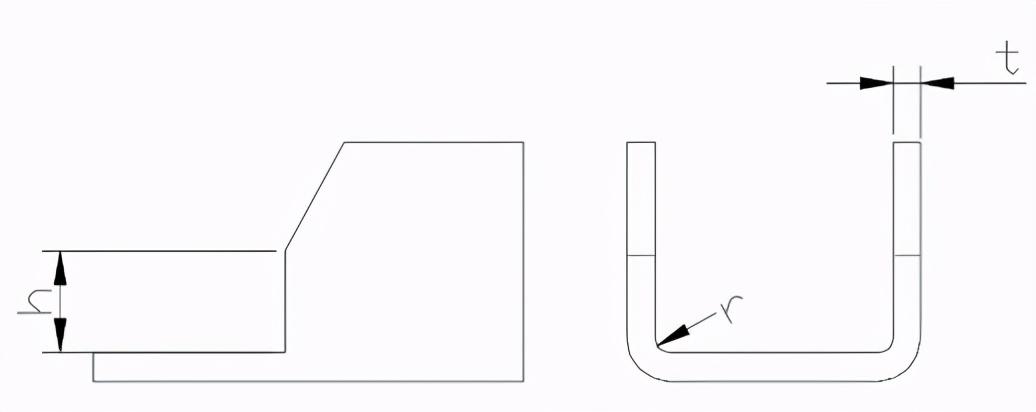
1.7 Reikien reunaetäisyys taivutetuissa osissa:
Reiän reunan etäisyys: Lävistä reikä ensin ja taivuta se. Reiän sijainnin tulisi olla taivutuksen muodonmuutosalueen ulkopuolella, jotta reikä ei muodostu taivutuksen aikana. Alla olevassa taulukossa on esitetty etäisyys reiän seinämästä kaarevaan reunaan.
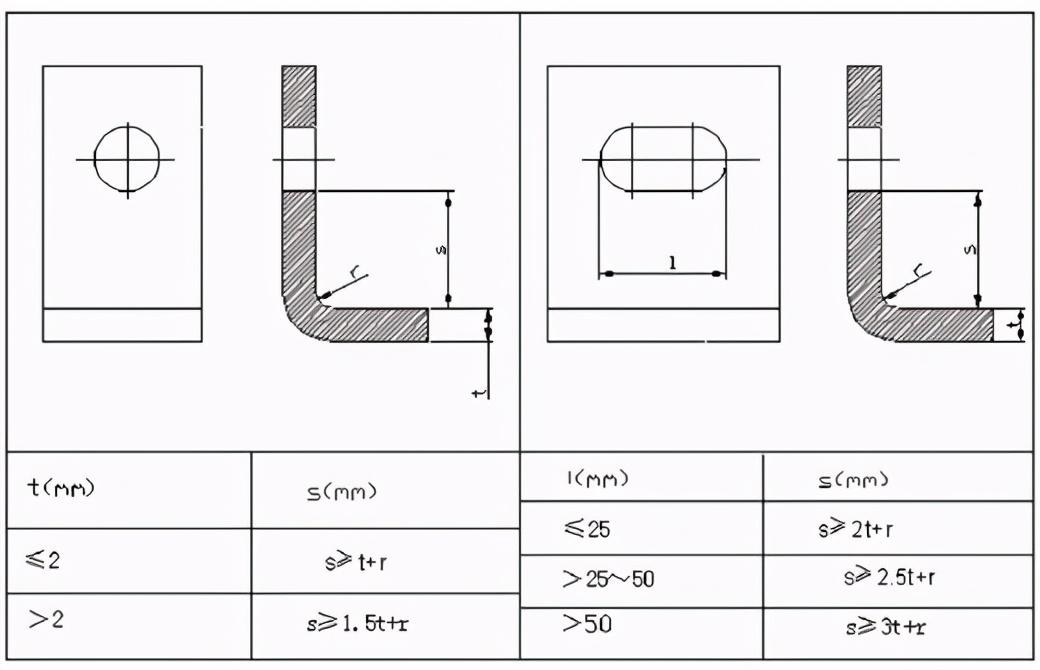
1.8 Prosessiviilto paikallista taivutusta varten:
Taivutetun osan taivutuslinjan tulisi välttää äkillisten kokomuutosten asentoa. Kun taivutetaan tiettyä reunan segmenttiä paikallisesti jännityksen keskittymisen ja särkymisen estämiseksi terävissä kulmissa, taivutuskäyrää voidaan siirtää tietyn etäisyyden jättämään äkillinen koon muutos (kuva a), tai prosessin ura (kuva b) voidaan avata tai prosessireikä voidaan lävistää (kuva c). Kiinnitä huomiota kaavion kokovaatimuksiin: SR; Aukon leveys kt; Aukon syvyys Lt+R+k/2.
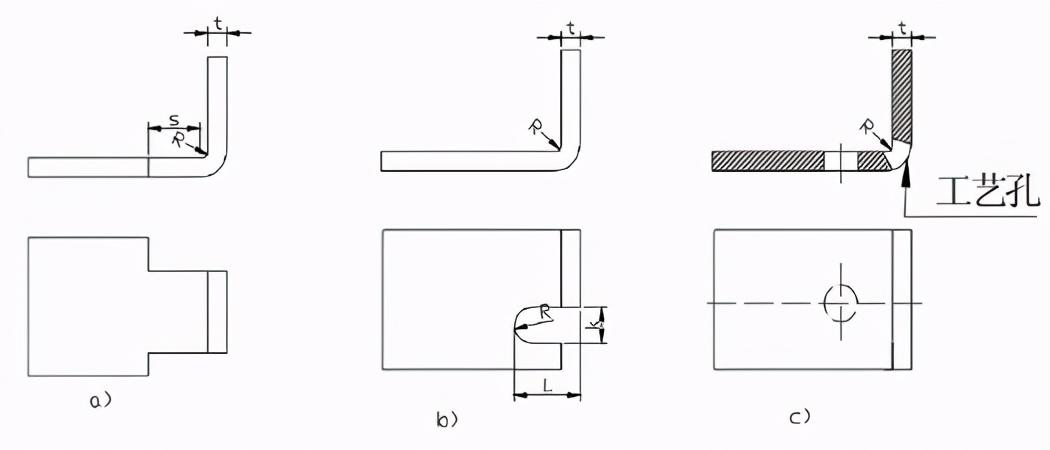
1.9 Taivutusreunat viisteisillä reunoilla välttävät muodonmuutosalueita:
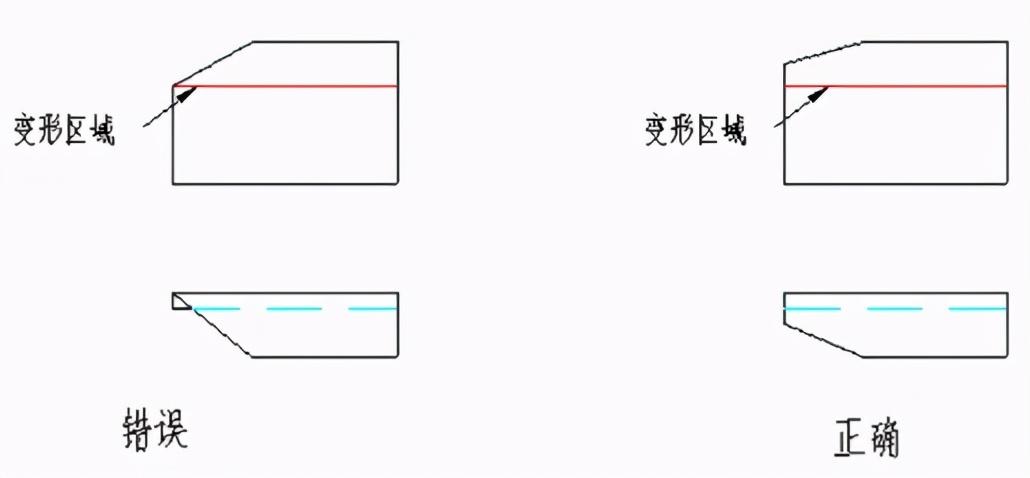
1.10 Levymetallilaskoksia (kuolleet reunat) koskevat suunnitteluvaatimukset:
Levyn laskosten kuolleen reunan pituus liittyy materiaalin paksuuteen. Kuten seuraavassa kuvassa näkyy, kuolleen reunan vähimmäispituus on yleensä L3,5t + R.
Niistä t on materiaalin seinämän paksuus ja R on edellisen prosessin pienin sisäinen taivutussäde (kuten kuvassa oikealla näkyy) ennen reunan tappamista.

1.11 Prosessin paikannusreiät on lisätty:
Jotta varmistettaisiin aihion tarkka sijoittaminen muottiin ja estettäisiin aihion poikkeama taivutuksen aikana, prosessin paikannusreiät on lisättävä etukäteen suunnittelun aikana, kuten seuraavassa kuvassa esitetään. Erityisesti useaan otteeseen taivutetuissa osissa prosessireikiä on käytettävä paikannusreferenssinä kumulatiivisten virheiden vähentämiseksi ja tuotteen laadun varmistamiseksi.
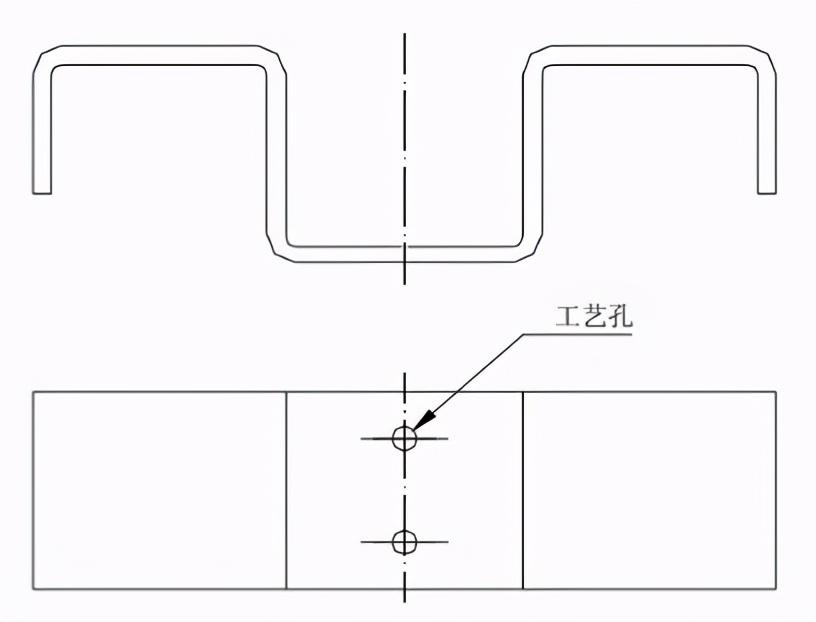
Taivutettujen osien mittoja merkittäessä on otettava huomioon käsiteltävyys:
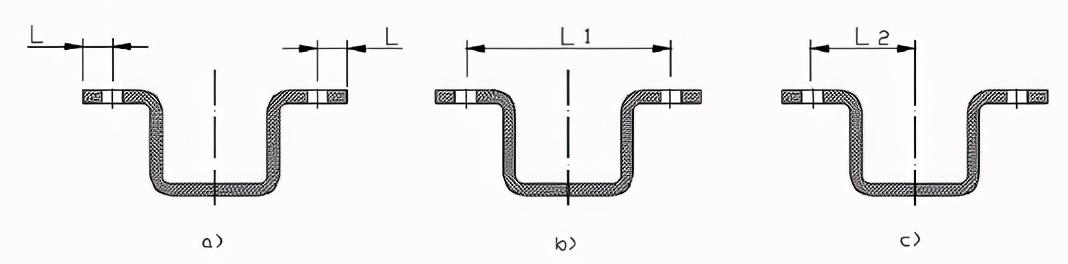
Kuten yllä olevassa kuvassa näkyy, a) lävistys ensin ja sitten taivutus, L-mittatarkkuus on helppo varmistaa ja käsittely on kätevä. b) Jos mittakaavan L tarkkuusvaatimus on korkea, on ensin taivutettava ja sitten käsiteltävä reikä, joka on hankala käsitellä.
Taivutettujen osien jousitukseen vaikuttavat monet tekijät, kuten materiaalin mekaaniset ominaisuudet, seinämän paksuus, taivutussäte ja positiivinen paine taivutuksen aikana. Mitä suurempi on taivutetun osan sisäsäde levyn paksuuteen, sitä suurempi on rebound. Valmistajat välttävät tällä hetkellä pääasiassa menetelmän, jolla vaimennetaan reboundin suunnittelun näkökulmasta, kuten taivutettujen osien reboundin, toteuttamalla tiettyjä toimenpiteitä. Samaan aikaan tiettyjen rakenteiden parantaminen suunnittelussa voi vähentää ponnahduskulmaa, kuten seuraavassa kuvassa näkyy: Vahvistusten puristaminen taivutusalueella voi paitsi lisätä työkappaleen jäykkyyttä myös auttaa vaimentamaan ponnahduskulmaa.
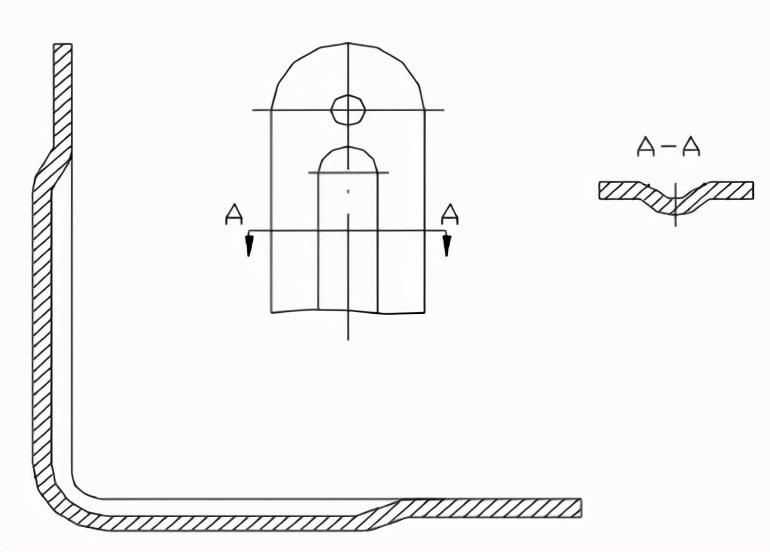
Levyn venytys Levyn venytys suoritetaan pääasiassa CNC- tai perinteisellä lävistyksellä, joka vaatii erilaisia venytyslävistyksiä tai muotteja.
Venytetyn osan muodon tulisi olla mahdollisimman yksinkertainen ja symmetrinen, ja se tulisi muodostaa yhdessä venymässä mahdollisimman paljon.
Useita venytyksiä vaativien osien tulisi mahdollistaa mahdolliset pintajäljet venytyksen aikana.
Asennusvaatimusten varmistamiseksi olisi sallittava venyttää sivuseiniä tietyllä kaltevuudella.
2.1 Venytetyn osan pohjan ja suoran seinämän välistä fileen sädettä koskevat vaatimukset:
Kuten alla olevassa kuvassa esitetään, venytetyn osan pohjan ja suoran seinämän välisen fileen säteen on oltava suurempi kuin levyn paksuus, ts. r1t. Venytysprosessin sujuvuuden helpottamiseksi otetaan yleensä r1 =(3-5) t, ja fileen enimmäissäde on enintään 8 kertaa levyn paksuus, joka on r18t.
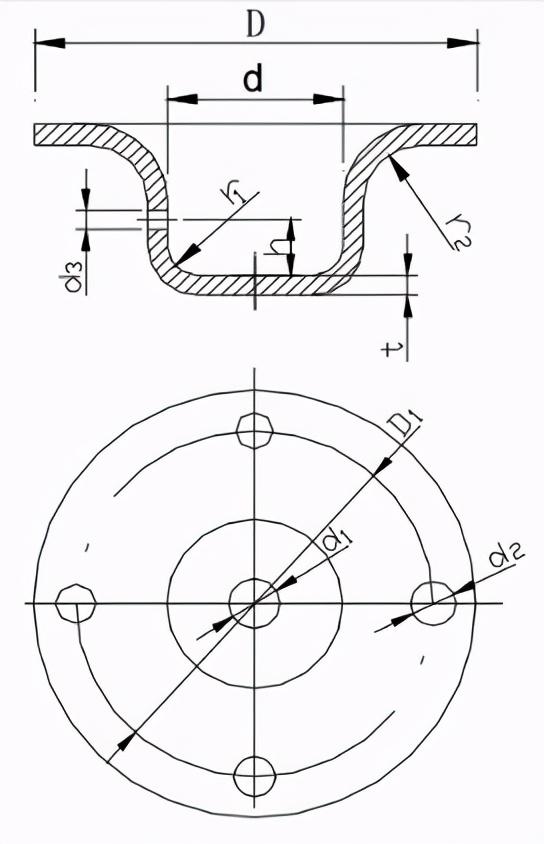
2.2 Pyöristyssäde venytetyn osan laipan ja seinän välillä
Laipan ja venytetyn osan seinämän välisen fileen säteen on oltava suurempi kuin kaksi kertaa levyn paksuus, ts. r22t. Venytysprosessin sujuvuuden parantamiseksi otetaan yleensä r2=(5-10) t ja enimmäislaipan säteen on oltava enintään 8 kertaa levyn paksuus, ts. r28t. (Katso edellä oleva kuva)
2.3 Pyörien venytettyjen osien sisäontelon halkaisija
Pyöreän venytyskappaleen sisähalkaisija tulee ottaa D d+10t, niin että painelevy puristetaan tiukasti ryppymättä venytyksen aikana. (Katso edellä oleva kuva)
2.4 Suorakulmaisten venytettyjen osien vierekkäisten seinien pyöristyssäde
Suorakaiteen muotoisen venytetyn kappaleen viereisten seinien väliin jäävän fileen säde on otettava r3 3t. Venytysten määrän vähentämiseksi r3 H/5 on otettava mahdollisimman paljon, jotta se voidaan vetää ulos kerralla.
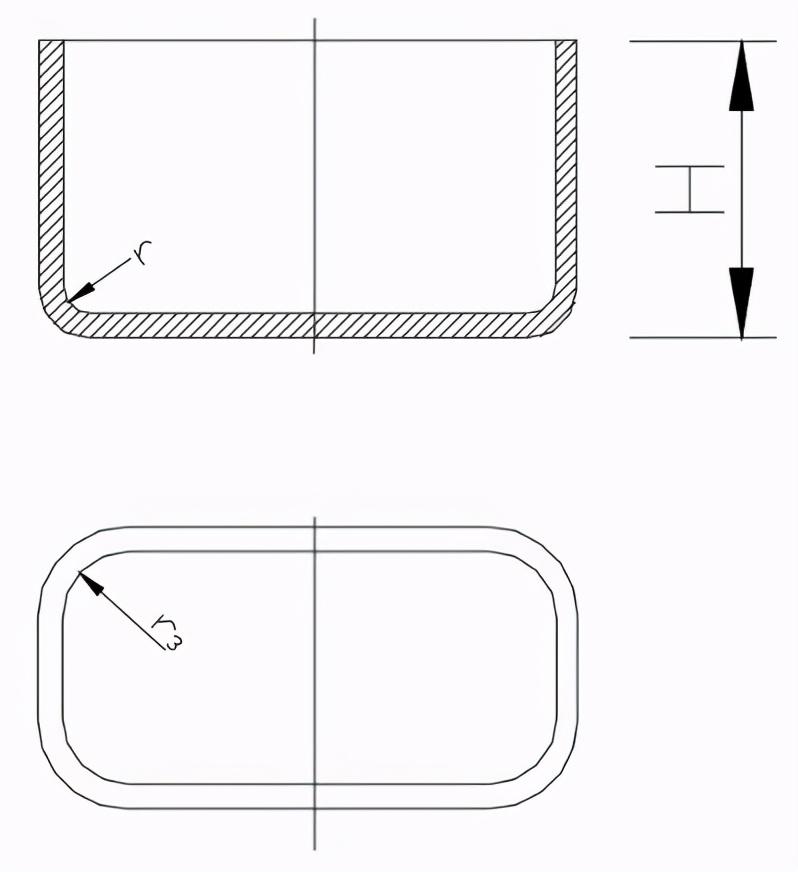
Vaatimukset, jotka koskevat 2,5 pyöreän laipattoman venytysosan korkeuden ja halkaisijan välistä mittasuhdetta kertamuovauksen aikana
Kun muodostat pyöreän laipan vapaan venytysosan kerralla, korkeus H:n ja halkaisijan d:n suhteen on oltava pienempi tai yhtä suuri kuin 0,4, eli H/d 0,4, kuten seuraavassa kuvassa esitetään.
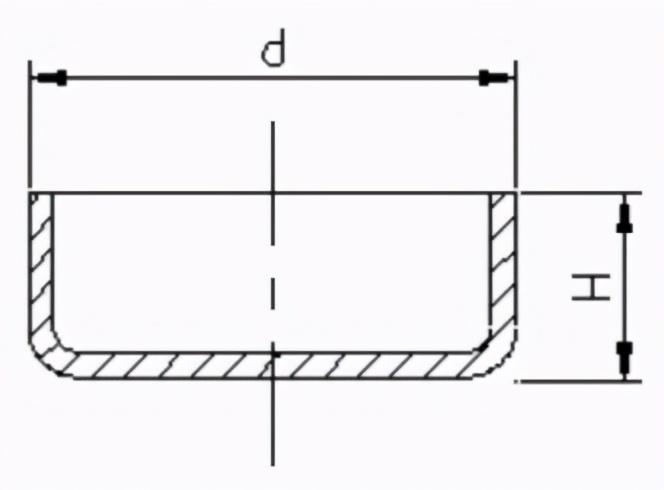
2.6 Venytetyn materiaalin paksuuden vaihtelu:
Venytetyn materiaalin paksuus muuttuu, koska kuhunkin osaan kohdistuu erilaisia jännitystasoja. Yleisesti ottaen alkuperäinen paksuus säilytetään pohjan keskellä, materiaali pohjan pyöristetyissä kulmissa ohuenee, materiaali lähellä laipan yläosassa paksuuntuu ja materiaali suorakulmaisen venytetyn osan pyöristettyjen kulmien ympärillä paksuuntuu.
2.7 Venytettyjen osien tuotemittojen merkintämenetelmä
Venytystuotteita suunniteltaessa tuotteen piirustuksen mitat on ilmoitettava selkeästi, jotta varmistetaan sekä ulkoiset että sisäiset mitat, eikä sisäisiä ja ulkoisia ulottuvuuksia voida merkitä samanaikaisesti.
2.8 Menetelmä venytettyjen osien mittatoleranssien merkitsemiseksi
Venytetyn osan koveran kuperan kaaren sisäsäde ja yhdellä kertaa muodostetun lieriömäisen venytetyn osan korkeusmittatoleranssi ovat kaksipuolisia symmetrisiä poikkeamia, joiden poikkeama-arvo on puolet kansallisen standardin (GB) tason 16 tarkkuusmittauksen absoluuttisesta arvosta, ja ne numeroidaan.
3. Muu levyjen muovaus: Vahvistusribit - Ribien puristaminen litteisiin metalliosiin auttaa lisäämään rakenteellista jäykkyyttä.
Säleikkeet - Säleikkeitä käytetään yleisesti erilaisissa koteloissa tai koteloissa ilmanvaihdon ja lämmön haihtumisen varmistamiseksi.
Reiälaippa (venytysreikä) - käytetään kierteiden koneistamiseen tai reiän aukon jäykkyyden lisäämiseen.
3.1 Vahvistaminen:
Vahvistusrakenteen ja koon valinta
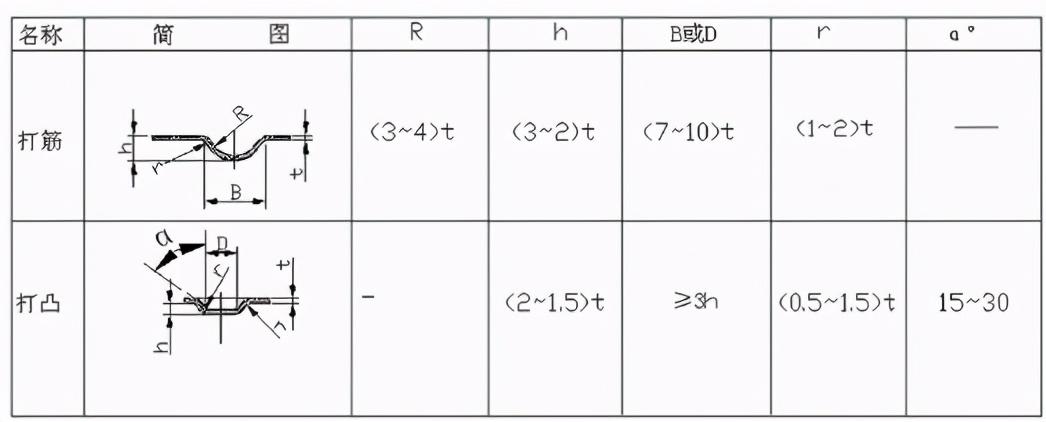
Kuvemman välimatkan ja kuperan reunaetäisyyden enimmäismitat valitaan alla olevan taulukon mukaisesti.
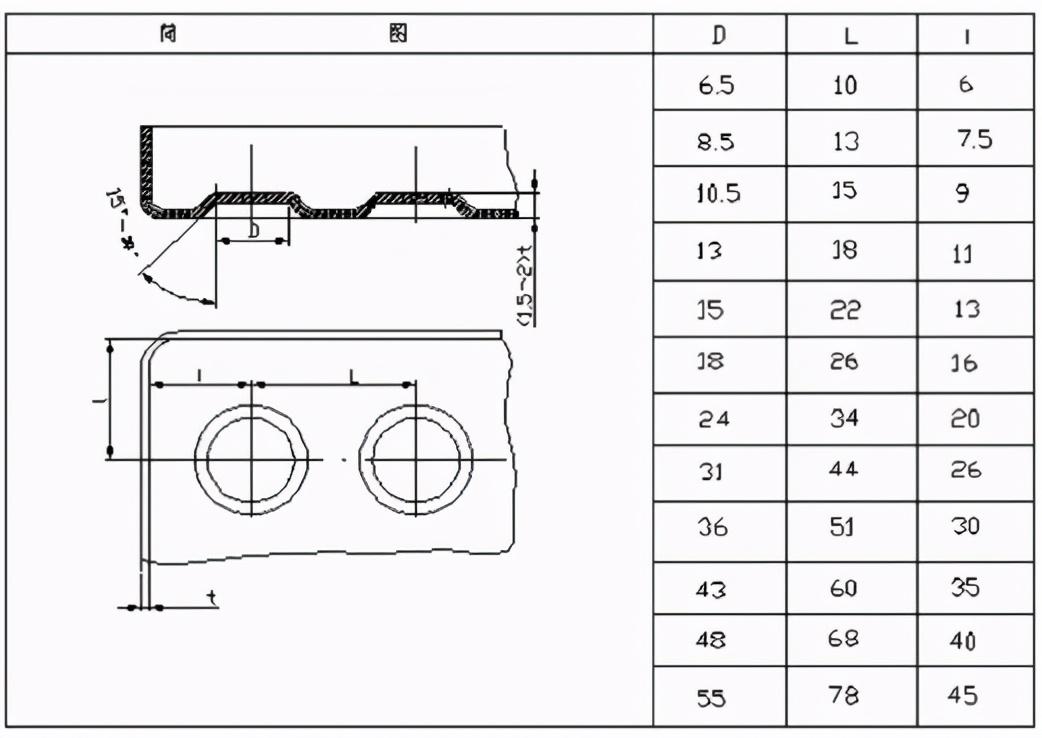
3.2 Säteilyt
Kaihtimien muodostamismenetelmä on leikata materiaali auki kuperan muotin yhdellä reunalla, kun taas kuperan muotin jäljellä olevat osat venyvät ja muodonmuutokset samanaikaisesti muodostaen aaltoilevan muodon yhdellä sivulla.
Säleikön tyypillinen rakenne esitetään seuraavassa kuvassa
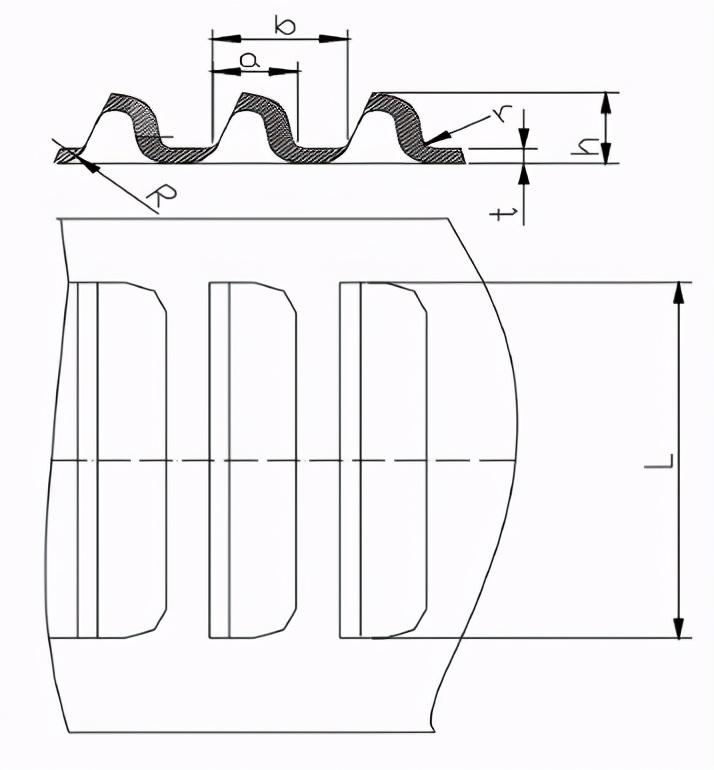
Säleikkimen kokovaatimus: a4t; b6t;h5t;L24t;r0.5t。
3.3 Reikien laippa (venytysreiät)
Reiän laippauksen muotoja on monia, ja yleinen on kierteiden sisäreiän laippauksen koneistaminen.
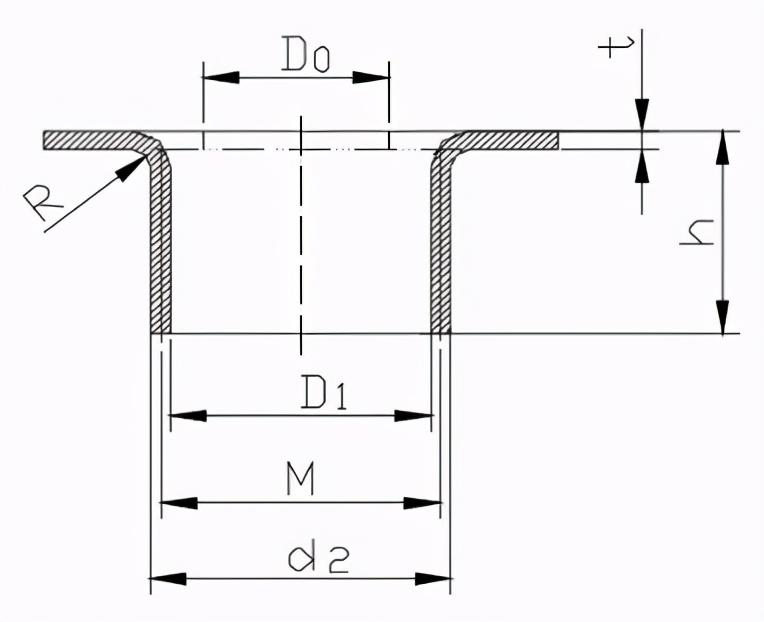
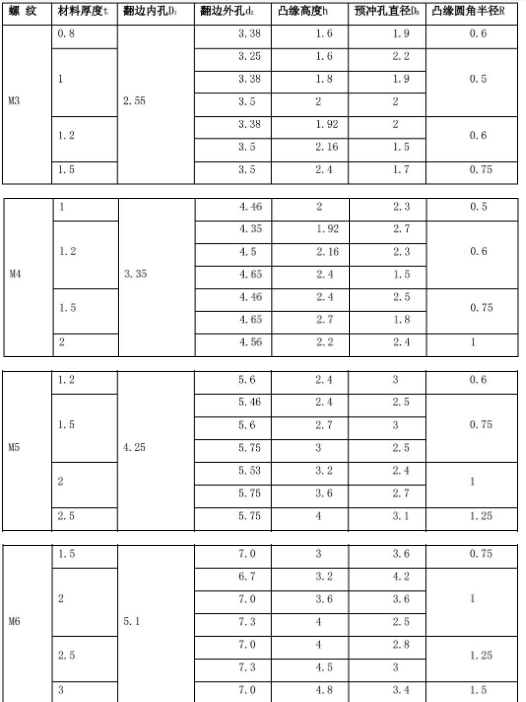
Levyn käsittelytekniikka - muiden käsiteltyjen levytarvikkeiden, kuten niittimutterien, niittimutterien, niittien ohjauspylväiden jne.
2. Kierteitettyjen reikien taputtaminen metallilevylle.
Levyn paksuus t< Kello 1.5, käytä käännettyä reunaa napauttamalla. Kun levyn paksuus on t1,5, voidaan käyttää suoraa kierteitystä.
Levyn käsittelytekniikka - Kun hitsataan levyhitsausrakenteiden suunnittelussa, se on toteutettava "symmetrisesti järjestää hitsit ja hitsauspisteet ja välttää leikkaus, aggregointi ja päällekkäisyys. Toissijaiset hitsit ja hitsauspisteet voidaan keskeyttää, ja tärkeimmät hitsit ja hitsauspisteet on kytkettävä."
Levyssä yleisesti käytetty hitsaus sisältää kaarihitsauksen, vastushitsauksen jne.
Kaarihitsatun metallilevyn välissä pitäisi olla riittävästi hitsaustilaa, ja suurimman hitsausvälin tulisi olla välillä 0,5 ja 0,8 mm. Hitsausauman tulisi olla tasainen ja tasainen.
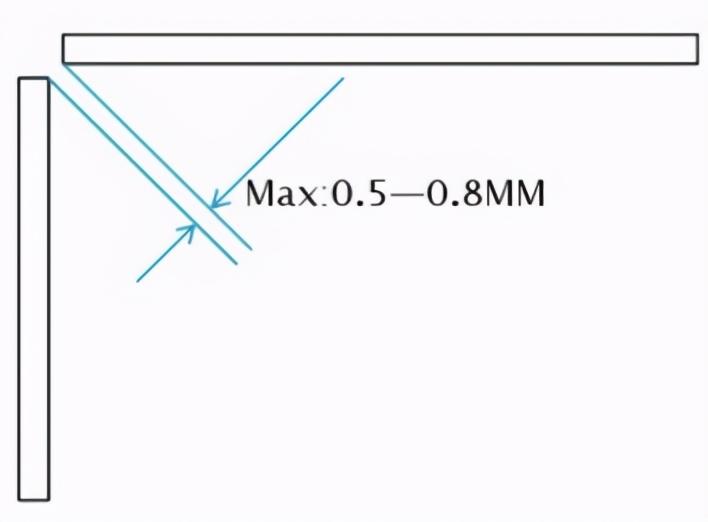
2. Vastushitsauksen hitsauspinnan tulee olla tasainen, ilman ryppyjä, rebound jne.
Vastushitsauksen mitat esitetään seuraavassa taulukossa:
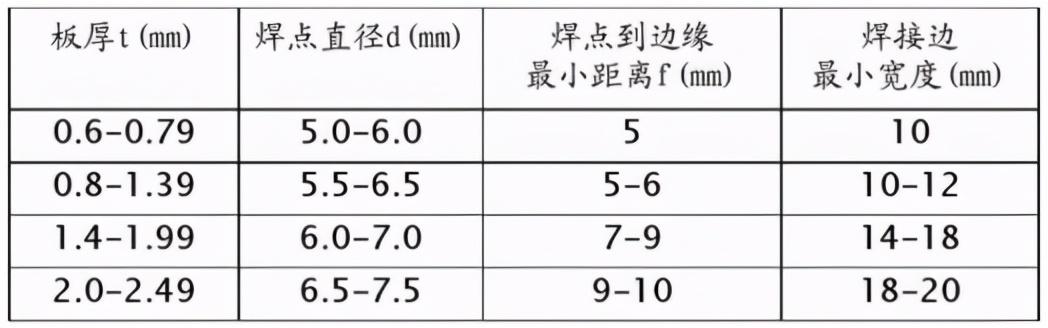
Resistanssijuotosliitosten välinen etäisyys
Käytännön sovelluksissa, kun hitsataan pieniä osia, voidaan viitata alla olevan taulukon tietoihin.
Suurten osien hitsauksessa pisteiden välistä etäisyyttä voidaan lisätä asianmukaisesti, yleensä vähintään 40-50 mm. Stressittömien osien hitsauspisteiden välistä etäisyyttä voidaan suurentaa 70-80 mm:iin.
Levyn paksuus t, juotosliitoksen halkaisija d, juotosliitoksen vähimmäishalkaisija dmin ja juotosliitosten välinen vähimmäisetäisyys e. Jos levy on yhdistelmä eri paksuuksia, valitse ohuimman levyn mukaan.
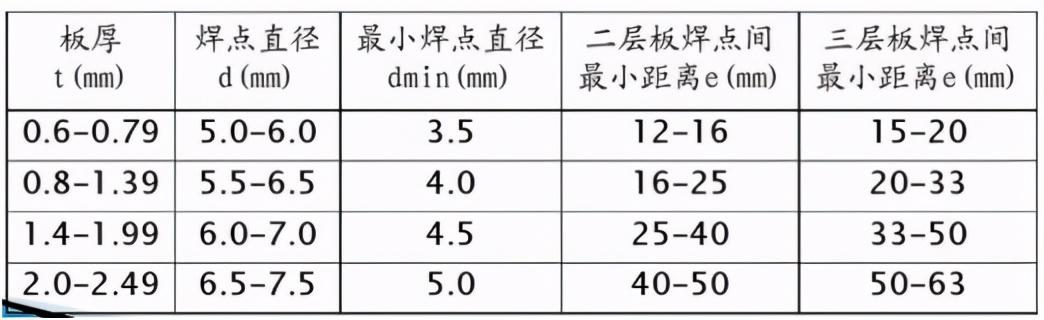
Vastushitsauslevyn kerrosten lukumäärä ja materiaalin paksuussuhde
Tasohitsaukseen tarkoitettu levy on yleensä 2 kerrosta, enintään 3 kerrosta. Hitsauksen jokaisen kerroksen paksuussuhteen tulisi olla välillä 1/3 ja 3.
Jos on tarpeen hitsata kolmikerroksinen levy, on ensin tarkistettava materiaalin paksuussuhde. Jos se on kohtuullista, hitsaus voidaan suorittaa. Jos se ei ole kohtuullista, on harkittava prosessireikiä tai prosessiloveja. Kaksikerroksisessa hitsauksessa hitsauspisteet on porrastettava.
Levyn käsittelytekniikka - Liitäntämenetelmät: Tämä esittelee pääasiassa levyn kytkentämenetelmät käsittelyn aikana, mukaan lukien niittien niittäminen, hitsaus (kuten edellä mainittiin), reiän piirtäminen niittäminen ja TOX-niittäminen.
Niitin niittäminen: Tällaista niittiä kutsutaan yleisesti vetoniittiksi, jossa kaksi levyä niitataan yhteen vetoniitin kautta. Yleiset niittimuodot esitetään kuvassa:
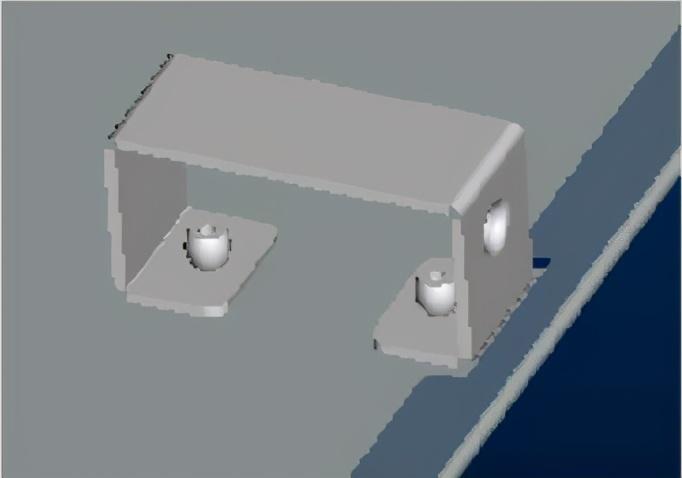
2. Hitsaus (kuten aiemmin mainittiin) 3. Piirustus ja niittäminen: Yksi osa on vetoreikä ja toinen osa on vastaupotettu reikä, joka on tehty erottamattomaksi liitoskoteloksi niittaamalla.
Superiority: Poistoretkillä ja sitä vastaavalla uppoavalla reiällä on paikannustoiminto. Niittolujuus on korkea, ja muottien läpi niittaamisen tehokkuus on myös suhteellisen korkea.
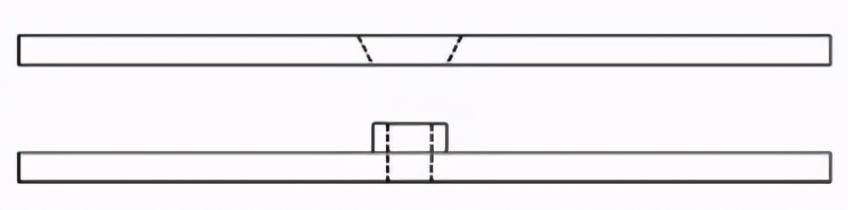
4. TOX-niittaus: Paina liitetty osa koveraan muottiin yksinkertaisen kuperan muotin kautta. Lisäpaineessa koveran muotin sisällä oleva materiaali virtaa ulospäin. Tuloksena on pyöreä liitäntäpiste, jossa ei ole reunoja tai särmiä, mikä ei vaikuta sen korroosionkestävyyteen. Jopa levyillä, joissa on pinnoite tai spray-maalikerros pinnalla, alkuperäiset ruoste- ja korroosionkestävyysominaisuudet voidaan säilyttää, koska pinnoite ja maalikerros voivat myös säilyttää alkuperäiset ruoste- ja korroosionkestävyysominaisuudet, koska pinnoite ja maalikerros myös muodostuvat ja virtaavat yhteen. Materiaali puristetaan molempia puolia kohti ja koveran muotin vieressä olevaan levyyn muodostaen TOX-liitäntäpisteitä. Kuten seuraavassa kuvassa esitetään:
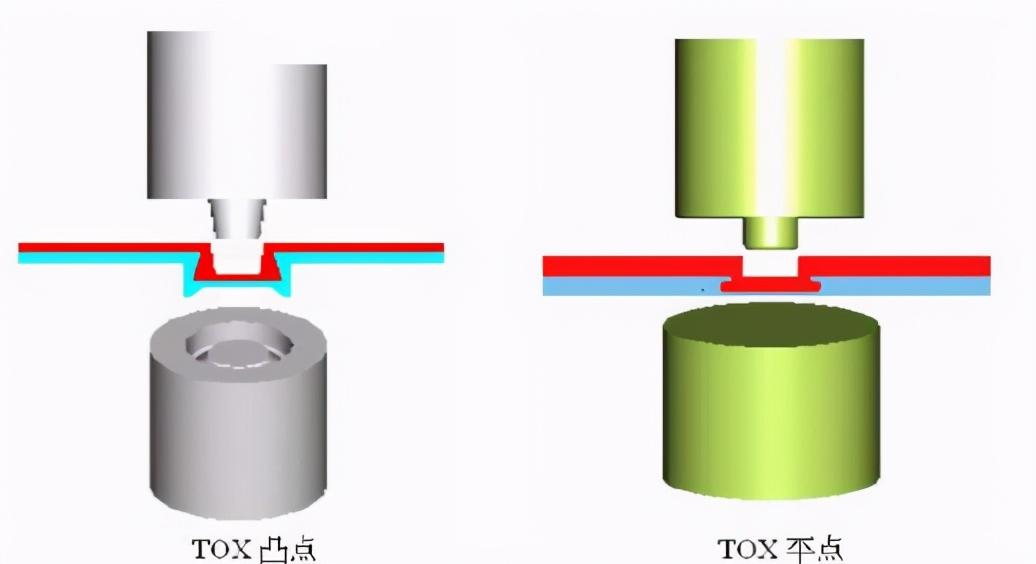
Levyn käsittelytekniikka - Pintakäsittely voi tarjota korroosioneston ja koristeellisia vaikutuksia levyn pinnalle. Levyn yleisiin pintakäsittelyihin kuuluvat jauheruiskutus, sähkösinkitys, kuumasinkitys, pinnan hapettuminen, pintapiirustus, seripainatus jne.
Ennen levyn pintakäsittelyä ohutlevyn pinnalta on poistettava öljytahrat, ruoste, hitsauskuona jne.
Jauheruiskutus: Levylle on olemassa kahdenlaisia pintaruiskutuksia: nestemäinen ja jauhemaali.Yleisesti käytetty yksi on jauhemaali.Ruiskuttamalla jauhetta, sähköstaattista adsorptiota, korkean lämpötilan paistamista ja muita menetelmiä, eri värien kerros maalia ruiskutetaan levyn pinnalle ulkonäön kaunistamiseksi ja materiaalin korroosionestokyvyn lisäämiseksi. Se on yleisesti käytetty pintakäsittelymenetelmä.
Huomautus: Eri valmistajien ruiskuttamassa väreissä saattaa olla värieroja, joten saman värinen levyä samassa laitteessa tulisi ruiskuttaa samalta valmistajalta mahdollisimman paljon.
2. Galvanoidun ja kuumasinkittyjen levyjen pintagalvanointi on yleisesti käytetty pinnan korroosionestomenetelmä, ja sillä voi olla tietty rooli ulkonäön kaunistamisessa. Galvanointi voidaan jakaa sähkösinkitys ja kuumasinkitys.
Sähkösinkitys on suhteellisen kirkas ja tasainen, ohut sinkitty kerros, jota käytetään yleisesti.
Kuumasinkipinnoite on paksumpi ja voi tuottaa rautasinkkiseoskerroksen, jolla on vahvempi korroosionkestävyys kuin sähkösinkitys.
3. Pinnan hapettuminen: Tämä ottaa pääasiassa käyttöön alumiinin ja alumiiniseosten pinnan anodisoinnin.
Alumiinin ja alumiiniseosten pinnan anodisointi voidaan hapettaa eri väreihin, mikä tarjoaa sekä suojaavia että koristeellisia vaikutuksia. Samanaikaisesti materiaalin pinnalle voidaan muodostaa anodinoksidikalvo, jolla on korkea kovuus ja kulutuskestävyys sekä hyvät sähköeristys- ja lämmöneristysominaisuudet.
4. Pintalinjan piirustus: Aseta materiaali lankapiirustuskoneen ylä- ja alarullojen väliin, jossa on hiekkahihna kiinnitettynä rulliin. Moottorilla ajettu materiaali kulkee ylä- ja alareunan hiekkahihnan läpi jättäen jälkiä materiaalin pinnalle. Merkkien paksuus vaihtelee hiekkahihnan tyypin mukaan, ja niiden päätehtävä on kaunistaa ulkonäköä. Lankapiirustuksen pintakäsittelymenetelmää pidetään yleensä alumiinimateriaaleissa.
5. Silkkipainatus on prosessi, jossa painetaan erilaisia merkintöjä materiaalien pinnalle. Yleensä on kaksi menetelmää: litteäpainatus ja siirtopainatus. Silkkipainatusta käytetään pääasiassa yleisillä tasaisilla pinnoilla, mutta jos on syvempiä kuoppia, tarvitaan siirtopainatus.
Silkkipainatus vaatii silkkimuotin.
Levyn käsittelyn tarkkuuden vertailulaite:
GBT13914-2002 Leimattujen osien mitat
GBT13915-2002-T leimausosien kulmatoleranssi
GB-T15005-2007 leimatut osat - Poikkeamien rajoittaminen ilman määritettyjä toleransseja
GB-T 13916-2002 Leimatut osat - Muoto ja sijainti ilman määritettyjä toleransseja
Yleisesti käytettyjen levyjen käsittelylaitteiden kyky ja yleisten levylaitteiden käsittelyvalikoima
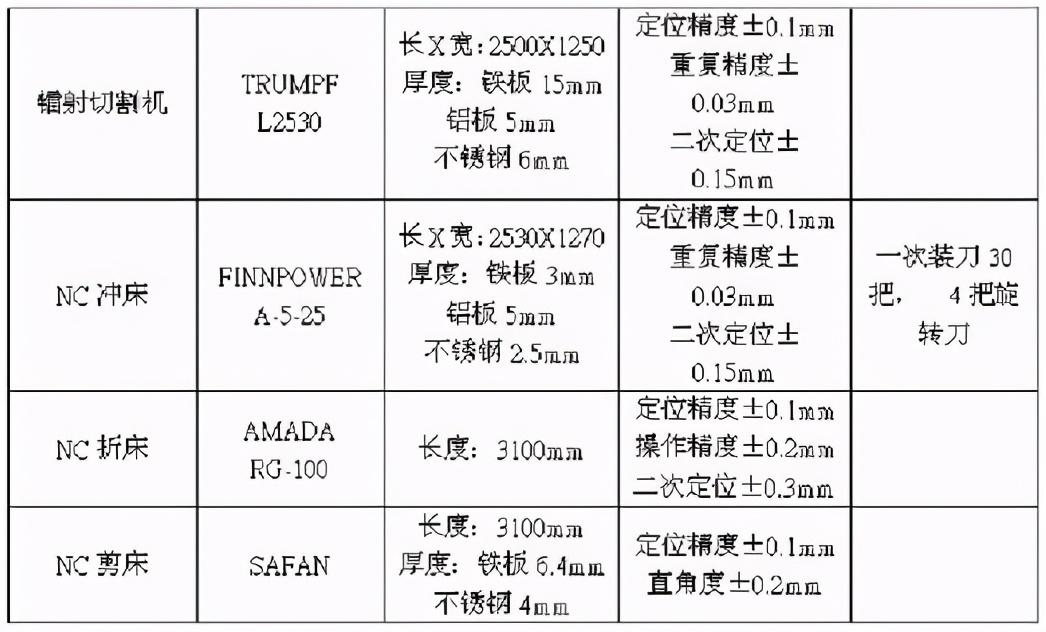