Olen käyttänyt CNC-sorvia silmänräpäyksessä kymmenen vuoden ajan ja hankkinut työstötaitoja ja kokemusta CNC-sorveista. Haluaisin vaihtaa ideoita kollegojeni kanssa. Työstettyjen osien toistuvan vaihdon ja rajallisten tehdasolosuhteiden vuoksi olemme ohjelmoineet, tarkistaneet työkalut, korjanneet virheenkorjauksen ja suorittaneet osien työstön itse viimeisen vuosikymmenen ajan. Yhteenvetona operatiiviset osaamisemme voidaan jakaa seuraaviin kohtiin. (Kirjoittaja/Li Neng)
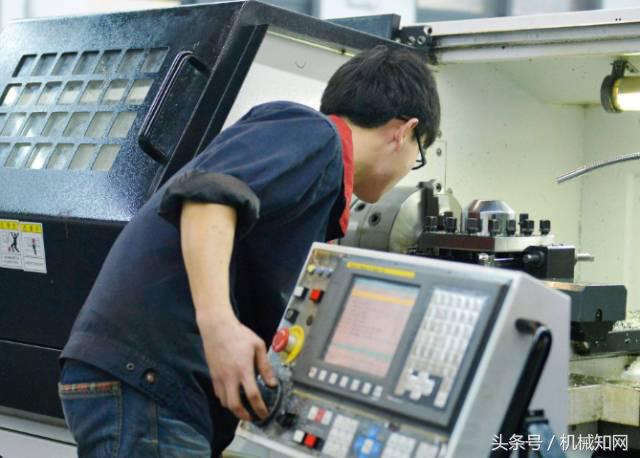
1,Ohjelmointitaidot: Tehtaamme jalostettujen tuotteiden korkean tarkkuuden vaatimusten vuoksi ohjelmoinnissa on otettava huomioon seuraavat tekijät:
1. Osien käsittelyjärjestys:
Poraa ensin ja sitten tasoita pää (näin estetään materiaalin kutistuminen porauksen aikana);
Ensin karkea auto, sitten hieno auto (tämä on osien tarkkuuden varmistamiseksi);
Käsittele ensin ne, joilla on suuremmat toleranssit, ja sitten ne, joilla on pienemmät toleranssit (tämä varmistaa, että pienen toleranssin koko ei naarmu ja estää osien muodonmuutokset).
2. Valitse kohtuullinen nopeus, syöttönopeus ja leikkaussyvyys materiaalin kovuuden perusteella:
1) Valitse hiiliteräsmateriaalit, joilla on suuri nopeus, suuri syöttönopeus ja suuri leikkaussyvyys. Esimerkiksi: 1Gr11, valitse S1600, F0.2 ja leikkaussyvyys 2 mm;
2) Valitse kova nopeus, alhainen syöttönopeus ja pieni leikkaussyvyys. Esimerkiksi: GH4033, valitse S800, F0.08 ja leikkaussyvyys 0,5 mm;
3) Titaaniseos on valittava alhaisella nopeudella, suurella syöttönopeudella ja pienellä leikkaussyvyydellä. Valitse esimerkiksi Ti6:ssa S400, F0.2 ja leikkaussyvyys 0,3 mm. Esimerkiksi tietyn osan käsittely: materiaali on K414, joka on erittäin kova materiaali. Useiden testien jälkeen se valittiin lopulta S360, F0.1, ja leikkaussyvyys 0,2 tuottaa pätevä osa.
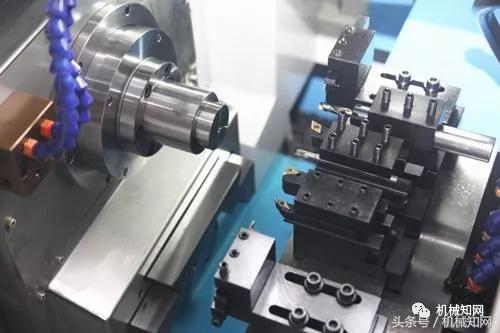
2,Veitsen kohdistustekniikka on jaettu veitsen kohdistustekniikkaan ja suoraan veitsen kohdistukseen. Useimmissa tehtaamme sorveissa ei ole työkalujen kohdistuslaitetta ja ne vaativat työkalujen suoran kohdistuksen.Seuraavat työkalujen kohdistustekniikat viittaavat työkalujen suoraan kohdistukseen.
Valitse ensin osan oikean päätypinnan keskipiste työkalun kohdistuspisteeksi ja aseta se nollapisteeksi. Kun työstökone palaa alkuun, jokainen käytettävä työkalu on kohdistettu osan oikean päätypinnan keskipisteen kanssa nollapisteenä; Kun työkalu joutuu kosketuksiin oikean pään pintaan, syötä Z0 ja napsauta mittauspainiketta. Työkalun kompensaatioarvo kirjaa automaattisesti mitatun arvon, mikä osoittaa, että Z-akseli on kohdistettu oikein. X-akseli on koeleikkausta varten, ja kun työkalua käytetään osan ulomman ympyrän säätämiseen, syötä x20 mitatakseen säädettävän osan ulomman ympyrän arvo (esim. x on 20 mm). Napsauta mittauspainiketta, niin kompensaatioarvo kirjaa automaattisesti mitatun arvon. Tällöin myös X-akseli on kohdistettu oikein; Tämä työkalun kohdistusmenetelmä, vaikka kone olisi kytketty pois päältä, ei muuta kohdistusarvoa virran ja uudelleenkäynnistyksen jälkeen. Se soveltuu saman osan laajamittaiseen ja pitkäaikaiseen tuotantoon, jolloin sorvia ei tarvitse kohdistaa uudelleen.
3,Virheenkorjaus taidot: Ohjelmoinnin ja työkalun kohdistamisen jälkeen osat on testattava ja virheenkorjattava. Jotta vältetään virheet ohjelman ja työkalun kohdistuksessa, jotka voivat aiheuttaa törmäysvaaroja, meidän pitäisi ensin suorittaa tyhjä isku simulointi koneistus. Konetyökalun koordinaattijärjestelmässä työkalu olisi siirrettävä oikealle 2-3 kertaa koko osan kokonaispituus; Sen jälkeen aloita työstön simulointi. Kun simulointikoneistus on valmis, varmista, että ohjelma ja työkalun kohdistus ovat oikein, ja aloita sitten osien työstö. Kun ensimmäinen osa on koneistettu, tarkista itse ja vahvista, että se on pätevä, ja etsi sitten erityinen tarkastaja tarkastamaan sen. Vasta kun erikoistunut tarkastaja on vahvistanut, että se on pätevä, virheenkorjaus voidaan suorittaa.
4,Kun ensimmäinen koeleikkaus on valmis, käsitellyt osat on tuotettava massassa. Ensimmäisen kappaleen pätevyys ei kuitenkaan tarkoita, että koko osien erä hyväksytään, koska käsittelyn aikana erilaiset käsittelymateriaalit aiheuttavat työkalun kulumista. Pehmeillä käsittelymateriaaleilla on vähemmän työkalun kulumista, kun taas kovilla käsittelymateriaaleilla on nopeampi työkalun kuluminen. Siksi käsittelyn aikana on tarpeen suorittaa säännöllisiä tarkastuksia ja oikea-aikaisesti lisätä tai vähentää työkalun korvausarvoa osien pätevyyden varmistamiseksi.
Käsittelymateriaali on esimerkiksi K414, jonka kokonaispituus on 180mm. Erittäin kovan materiaalin ansiosta työkalun kuluminen on erittäin nopeaa käsittelyn aikana. Lähtöpisteestä loppupisteeseen syntyy pieni 10-20mm poikkeama työkalun kulumisesta. Siksi meidän on lisättävä manuaalisesti 10-20mm poikkeama ohjelman pätevyyden varmistamiseksi.
Lyhyesti sanottuna käsittelyn perusperiaatteena on ensin karkea kone, poistaa ylimääräinen materiaali työkappaleesta ja sitten tarkkuuskone; Tärinää on vältettävä käsittelyn aikana. On monia syitä välttää lämpömuodonmuutoksen aiheuttamaa tärinää työkappaleen käsittelyn aikana, mikä voi johtua liiallisesta kuormituksesta; Se voi olla työstökoneen ja työkappaleen välinen resonanssi tai työstökoneen riittämätön jäykkyys tai se voi johtua työkalun passiivisuudesta. Värähtelyä voidaan vähentää seuraavilla menetelmillä:; Vähennä sivuttaissyöttönopeutta ja työstösyvyyttä, tarkista, onko työkappaleen kiinnitys turvallinen, lisää työkalun nopeutta, mikä voi vähentää resonanssia alentamalla nopeutta. Lisäksi tarkista, onko työkalu vaihdettava uuteen.
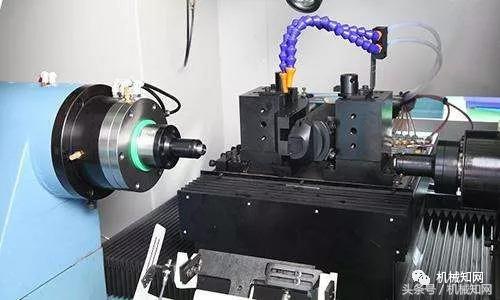
5,Kokemus törmäysten estämisestä työstökoneiden välillä vahingoittaa suuresti työstökoneiden tarkkuutta, ja vaikutus vaihtelee erityyppisten työstökoneiden. Yleisesti ottaen sillä on suurempi vaikutus työstökoneisiin, joilla on heikko jäykkyys. Niin kauan kuin käyttäjä on varovainen ja hallitsee tietyt törmäystekniikat, törmäykset voidaan täysin ehkäistä ja välttää.
Tärkein syy törmäyksiin:
Yksi on leikkaustyökalun halkaisijan ja pituuden syöttövirhe;
Toiseksi työkappaleen mittojen ja muiden niihin liittyvien geometristen mittojen syöttämisessä on virheitä sekä työkappaleen alkuperäisen sijainnin virheitä;
Kolmanneksi työkappaleen koordinaattijärjestelmä on asetettu väärin tai nollapiste nollataan työstöprosessin aikana, mikä johtaa muutoksiin. Konetyökalun törmäykset tapahtuvat useimmiten koneen nopean liikkeen aikana, ja tällaisten törmäysten vaarat ovat myös suurimmat, mikä on ehdottomasti vältettävä.
Operaattoreiden tulisi siis kiinnittää erityistä huomiota ohjelman suorittamisen alkuvaiheeseen ja työkalujen vaihtoon. Jos ohjelmaa muokataan väärin tai työkalun halkaisija ja pituus syötetään väärin, törmäyksiä todennäköisesti tapahtuu. Ohjelman loppuvaiheessa, jos CNC-akselin kelaustoiminto on virheellinen, voi myös tapahtua törmäyksiä.
Yllä mainittujen törmäysten välttämiseksi käyttäjän tulee hyödyntää kasvonpiirteensä toimintoja työstökonetta käytettäessä, tarkkailla, esiintyykö epänormaaleja liikkeitä, kipinöitä, melua, epänormaaleja ääniä, tärinää tai palaneita hajuja. Jos jokin poikkeava tilanne havaitaan, ohjelma on lopetettava välittömästi, sillä kone voi jatkaa toimintaansa vasta sängyn ongelman ratkeamisen jälkeen.
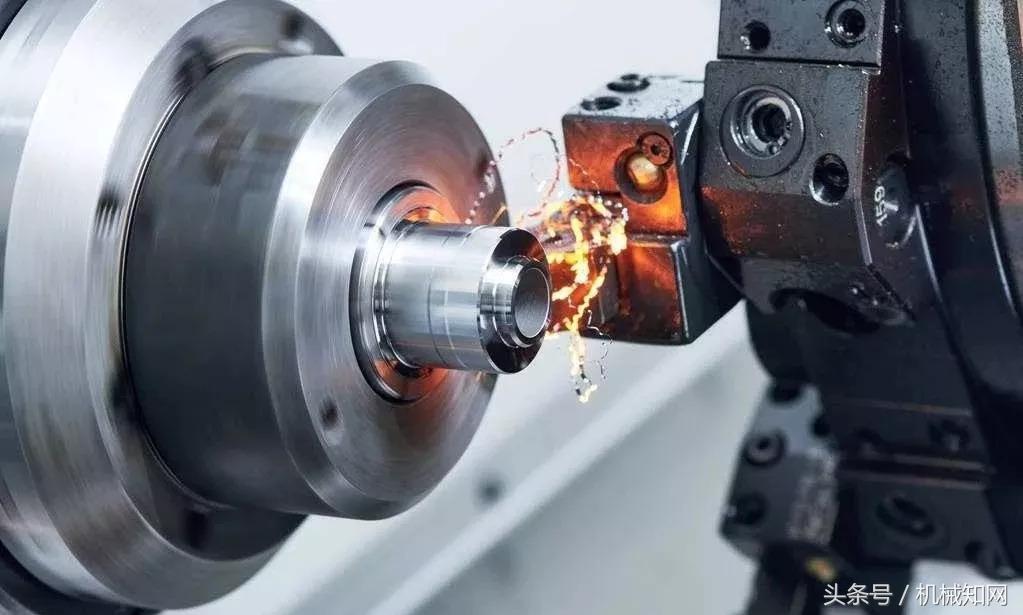
Lyhyesti sanottuna CNC-työstökoneiden käyttötaitojen hallinta on asteittainen prosessi, jota ei voida saavuttaa yhdessä yössä. Se perustuu työstökoneiden peruskäyttöön, mekaanisen käsittelyn perustietoon ja ohjelmoinnin perustietoon. CNC-työstökoneiden käyttötaidot eivät ole kiinteitä, ne edellyttävät käyttäjää hyödyntämään täysin mielikuvitustaan ja käytännön kykyään orgaanisessa yhdistelmässä, joka on innovatiivinen työ.