Alumiiniset tarkkuusosat ja -tuotteet ovat suosittuja kevyen painonsa ja erinomaisen ulkonäkönsä vuoksi, ja niitä käytetään laajalti teollisuudessa ja päivittäisissä tarpeissa. Teknologian jatkuvan kehityksen myötä ihmisten kysyntä tuotemonimuotoisuudelle kasvaa yhä voimakkaammaksi. Siksi alumiiniseostuotteiden prosessivaatimukset nousevat yhä suuremmiksi, ja markkinoiden kysyntä kasvaa myös. Vastatakseen ihmisten kysyntään alumiiniseosten kuorituotteiden monimuotoisuudesta ja korkeasta laadusta alumiiniseosten CNC-koneistusvalmistajat ovat tiivistäneet prosessitekniikat ja ongelmat, jotka on huomioitava alumiinin CNC-koneistuksessa.
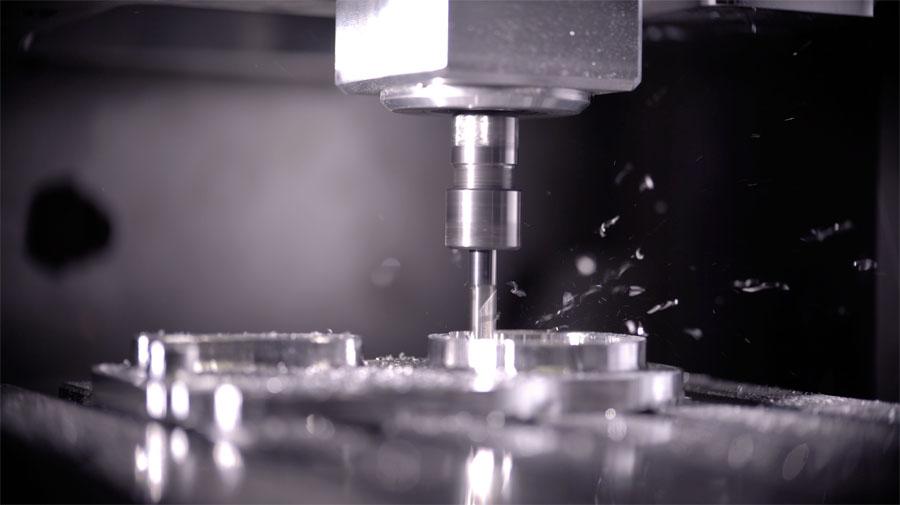
1. Valitse sopiva käsittelymenetelmä
Numeerinen säätöleikkaus on virtaviivainen leikkausmenetelmä ja yleisesti käytetty prosessi alumiinimateriaalien tarkkuustyöstöön. Käytän päätymyllyä, jolla on monisuuntainen leikkauskyky, spiraalileikkauksen interpolointi ja ääriviivaleikkausinterpolointi. Käsittele vähemmän reikiä vähemmällä työkalulla.
2. Kuulaputkimyllyjä voidaan käyttää spiraalien interpoloinnin yhteydessä kartioitujen reikien jatkuvaan käsittelyyn.
Kaivaukseen ja viistämiseen voidaan käyttää kuulapäätsijyrsimiä ja spiraalien interpolointiporakoneita. Loppumyllyjä voidaan käyttää yhdessä ääriviivaleikkauksen interpoloinnin kanssa reikien puolitarkkuustyötöissä ja osien tarkkuustyötöissä. Kierteiden työstöön käytettävää päätymyllyä voidaan käyttää spiraalien interpoloinnin yhteydessä erilaisten kierteitettyjen reikien koneistamiseen.
Tehokkaat alumiiniseoksen tarkkuusosat voidaan koneistaa erikokoisissa tarkkuusreikissä työkaluinterpoloinnin avulla. Jokaisen hampaan kuormitus on suhteellisen kevyt, varsinkin kun käytetään nopeita jyrsinkoneita. Siksi samaa päällystettyä kovametallista valmistettua päätymyllyä voidaan käyttää erilaisten työstömateriaalien nopeaan ja tarkkaan poraukseen.
3. Valitse sopiva leikkausmäärä
Henkilökunta voi valita käytettävän leikkausnopeuden käsiteltävän materiaalin, kovuuden, leikkausolosuhteiden, materiaalin tyypin ja leikkaussyvyyden perusteella. Nämä olosuhteet ovat välttämättömiä koneen kulumisen vähentämiseksi tehokkaasti.
4. Valitse sopivat työkalut.
Harake kulma: Oikea harake kulma tulee valita samalla kun reunan lujuus säilyy. Toinen puoli voi hioa teräviä leikkausreunoja leikkaamisen muodonmuutoksen vähentämiseksi, sirun poiston tasaisemmaksi ja leikkaamisen kestävyyden ja lämmön vähentämiseksi. Älä käytä työkaluja, joiden etukulma on negatiivinen.
Takakulma: Takakulman koko vaikuttaa suoraan takakulman pinnan kulumiseen ja koneistetun pinnan laatuun. Leikkauspaksuus on tärkeä kriteeri selkäkulman valinnassa. Karkeassa koneistuksessa syöttönopeus on suuri, leikkauskuorma on korkea ja lämmöntuotanto on suuri, joten työkalulla on hyvät lämmönpoistoolosuhteet. Siksi olisi valittava pienempi takakulma. Tarkkuustyöstettäessä jyrsintä on tarpeen hioa leikkuureuna kitkan vähentämiseksi takaleikkuupinnan ja työstöpinnan välillä ja elastisen muodonmuutoksen minimoimiseksi. Siksi olisi valittava suurempi takakulma.
Kiertokulma: Kiertokulma on valittava niin suuri kuin mahdollista, jotta jyrsinkone on sileä ja jyrsinkoneen rasitus vähenee.
Lähestymiskulma: Lähestymiskulman pienentäminen asianmukaisesti voi tehokkaasti parantaa lämmönpoisto-olosuhteita ja alentaa käsittelyalueen keskimääräistä lämpötilaa.
Vähennä jyrsintähampaiden määrää ja lisää tilaa lastujen poistoon.
Alumiiniseosmateriaalien korkean plastisuuden vuoksi käsittelyn aikana on merkittävä leikkausmuodonmuutos, mikä johtaa suureen lastutilaan. Sirun uran alaräteen on oltava suuri ja jyrsimen hampaiden määrän on oltava pieni. Esimerkiksi jyrsimet, joiden halkaisija on alle 20 mm, käyttävät 2 hammasta, mutta jyrsimet, joiden halkaisija on 30 ~ 60 mm, on parhaiten varustettu 3 hampaalla estämään ohuiden alumiiniseososien muodonmuutos lastun tukkeutumisen vuoksi.
Hieno hionta hampaat: Hampaan reunan karheusarvon tulisi olla pienempi kuin Ra = 0,4um. Ennen uuden veitsen käyttöä sen etu- ja takaosa on kiillotettava kevyesti hienolla öljykivellä poistaaksesi hionnan aikana jäljelle jääneet purrut tai pienet sahaukset. Tällä tavoin leikkauslämpöä voidaan vähentää, mutta leikkausmuodonmuutos on myös suhteellisen pieni.
Tarkka työkalujen kulumisstandardien valvonta. Työkalun kuluessa työkappaleen pinnan karheusarvo nousee, leikkauslämpötila nousee ja työkappaleen muodonmuutos kasvaa. Siksi hyvän kulutuskestävyyden omaavien työkalumateriaalien valinnan lisäksi kulutusstandardi ei saa ylittää 0,2 mm. Muussa tapauksessa on helppo kehittää roskakasvaimia. Leikkauksen aikana työkappaleen lämpötila ei yleensä saa ylittää 100 ℃ muodonmuutoksen estämiseksi.
5. Valitse kohtuullinen kaluste.
Osien on täytettävä täysin koneen tarpeet tarpeettomien paikannusvirheiden vähentämiseksi, ja erityisiä kiinnitystyökaluja on valittava.
6. Määritä kohtuullinen käsittelyreitti.
Yritä pitää käsittelyreitti mahdollisimman lyhyenä koneen kulumisen vähentämiseksi.
Nopeassa leikkauksessa työstömäärä on suuri ja leikkaus on ajoittaista, joten jyrsinnän aikana syntyy tärinää, mikä vaikuttaa koneistuksen tarkkuuteen ja pinnan karheuteen. Siksi CNC-nopea leikkaus voidaan yleensä jakaa karkeaan koneistukseen puolitarkkuustyötä, kulmanpuhdistusta, tarkkuustyötä ja muita prosesseja.
Jos osat vaativat suurta tarkkuutta, sekundaarinen puoliviimeistely voi olla tarpeen ennen tarkkuustyötä. Karkean työstön jälkeen osat jäähdytetään luonnollisesti karkean työstön aiheuttaman sisäisen rasituksen poistamiseksi ja muodonmuutoksen vähentämiseksi. Jäljelle jäävän määrän karkean työstön jälkeen pitäisi olla suurempi kuin muodonmuutosmäärä (yleensä 1-2 mm). Tarkkuustyöstöprosessin aikana osan tarkalla työstöpinnalla on ylläpidettävä yhdenmukaiset työstötoleranssit. 0.2-0.5mm on yleensä hyvä. Tämä pitää työkalun vakaana työstöprosessin aikana ja vähentää merkittävästi leikkausmuodonmuutoksia. Hanki hyvä pintakäsittelylaatu tuotteen tarkkuuden varmistamiseksi.