Korkean tarkkuuden CNC-koneistus on menetelmä, jossa käytetään tietokonenumeerista ohjaustekniikkaa, jolla on suurempi tarkkuus ja tehokkuus verrattuna perinteiseen mekaaniseen koneistukseen. Sitä voidaan soveltaa useilla aloilla, kuten ilmailu-, autoteollisuudessa, elektroniikkalaitteissa jne., mikä tuo monia etuja tuotteeseen.
Ensinnäkin suuri tarkkuus on CNC-koneistuksen suuri etu. Perinteiseen mekaaniseen koneistukseen verrattuna CNC-koneistus voi saavuttaa suuremman tarkkuuden ja pienemmät virheet. Se voi tarkasti ohjata työkalun liikkeen lentorataa ja työstösyvyyttä tuotesuunnittelun vaatimusten mukaisesti, jolloin työstetty tuote vastaa paremmin suunnitteluvaatimuksia. Perinteinen käsittely perustuu usein manuaaliseen käyttöön, ja tarkkuus riippuu suurelta osin käyttäjien kokemuksesta ja teknisestä tasosta, mikä voi helposti johtaa virheisiin.
Toiseksi, erittäin tarkka CNC koneistus on nopeampaa. Koska CNC-koneistus on tietokoneohjattu, koneistusohjelma voidaan suorittaa automaattisesti ilman manuaalista puuttumista. Näin voidaan välttää manuaalisen käytön aiheuttamat viivästykset ja alhainen tehokkuus. Samaan aikaan CNC-koneistus voi suorittaa useita työstövaiheita samanaikaisesti, mikä parantaa huomattavasti koneistuksen tehokkuutta. Tämä on erityisen tärkeää suurtuotantoa harjoittaville yrityksille, koska se voi merkittävästi lyhentää tuotantosykliä ja parantaa tuotannon tehokkuutta.
Lisäksi erittäin tarkka CNC-koneistus on hyvä johdonmukaisuus ja toistettavuus. CNC-koneistuksessa tuotteen työstöparametreja ohjataan periaatteessa tietokoneella, ja ne voidaan suorittaa täysin suunnitteluvaatimusten mukaisesti. Siksi sama tuote voi säilyttää saman koon ja muodon eri käsittelyerissä, erittäin hyvällä johdonmukaisuudella ja toistettavuudella. Perinteinen käsittely perustuu usein toimijoiden taitoihin ja kokemukseen, minkä vuoksi täydellisen johdonmukaisuuden saavuttaminen on vaikeaa.
Lisäksi korkean tarkkuuden CNC-koneistuksella on myös vahva mukautumiskyky. CNC-koneistusta voidaan soveltaa erilaisiin materiaaleihin, mukaan lukien metalli, muovi, puu jne. Se voi mukautua erilaisiin materiaaleihin ja käsittelyvaatimuksiin erilaisten leikkaustyökalujen ja käsittelytekniikoiden avulla. Perinteisessä koneistuksessa on usein tarpeen vaihtaa erilaisia työstökoneita ja työkaluja, kun taas CNC-koneistus voi mukautua erilaisiin koneistustarpeisiin vaihtamalla leikkaustyökaluja ja säätämällä työstöohjelmia.
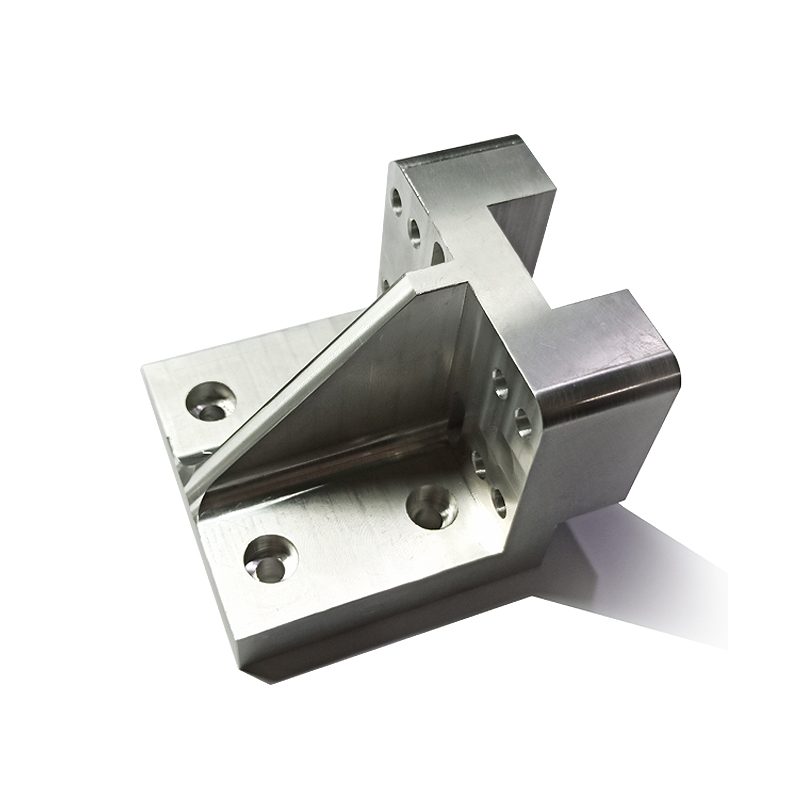
Lisäksi korkean tarkkuuden CNC-koneistuksella on myös parempi turvallisuus ja luotettavuus. CNC-koneistuksessa useimpia toimintoja ohjataan tietokoneilla, jotka voivat saavuttaa automaattisen koneistuksen ja välttää manuaalisten toimintojen aiheuttamat turvallisuusriskit. Useimmat CNC-koneistuslaitteet on varustettu myös automaattisilla valvonta- ja hälytysjärjestelmillä, jotka voivat seurata epänormaaleja tilanteita työstöprosessin aikana reaaliajassa ja antaa ajoissa hälytyksiä. Tämä voi parantaa työturvallisuutta ja luotettavuutta sekä vähentää onnettomuuksia.
Lopuksi erittäin tarkka CNC-koneistus voi myös vähentää työvoimakustannuksia ja parantaa yritysten kilpailukykyä. Koska CNC-koneistus voi saavuttaa automaattisen tuotannon ja vähentää manuaalisten toimintojen tarvetta, se voi vähentää huomattavasti työvoimakustannuksia. Perinteiseen koneistukseen verrattuna CNC-koneistus vaatii vähemmän henkilöstöä ja suhteellisen pienemmät tekniset vaatimukset. Tämä voi lievittää yritysten työvoimapaineita ja parantaa niiden kilpailukykyä markkinoilla.
Yhteenvetona voidaan todeta, että korkean tarkkuuden CNC-työstön etuja ovat pääasiassa korkea tarkkuus, korkea tehokkuus, hyvä johdonmukaisuus ja toistettavuus, vahva mukautuvuus, turvallisuus ja luotettavuus sekä alhaisemmat työvoimakustannukset. Nämä edut tekevät CNC-koneistuksesta korvaamattoman osan nykyaikaista valmistusta, jolla on suuri merkitys tuotteiden laadun parantamiseksi, tuotannon tehokkuuden lisäämiseksi ja kustannusten vähentämiseksi. Teknologian jatkuvan kehityksen myötä CNC-koneistustekniikasta tulee älykkäämpi ja tehokkaampi, mikä tuo lisää uusia etuja tuotteisiin.