Ao brillo dun ollo, estiven operando un lathe CNC durante dez anos e acumulei algunhas habilidades de maquinaria e experiencia en lathes CNC. Gustaríame intercambiar ideas cos meus colegas. Debido á substitución frecuente de pezas máquinas e condicións limitadas da fábrica, estamos programando, comprobando ferramentas, depurando e completando a máquina de pezas nós mesmos durante a última década. En resumo, as nosas habilidades operacionais poden dividirse nos seguintes puntos. (Autor/Li Neng)
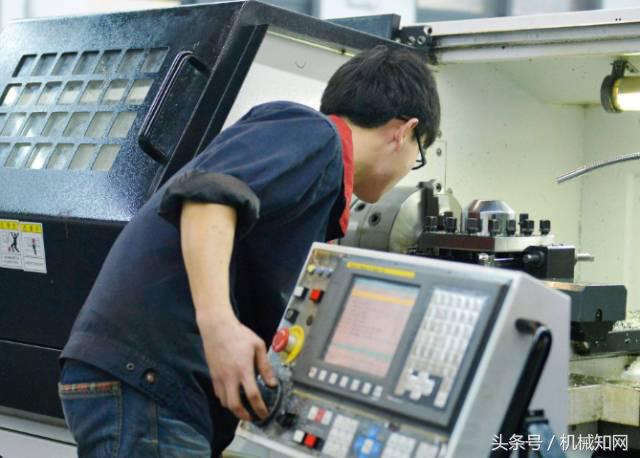
1[UNK] Capacidades de programación: Debido aos requisitos de alta precisión da nosa fábrica para os produtos procesados, hai que considerar os seguintes factores ao programar:
1. Secuencia de procesamento de partes:
Primeiro borrar e despois suavizar o final (is to é para evitar que o material diminúa durante a borrada);
Primeiro coche bruto, despois coche fino (is to é para asegurar a precisión das partes);
Primeiro procesa as que teñan tolerancias maiores, e despois procesa as que teñan tolerancias menores (isto asegura que a superficie do tamaño da pequena tolerancia non se rasgue e evita a deformación da parte).
2. Escolla unha velocidade razoábel, taxa de alimentación e profundidade de corte baseada na dureza do material:
1) Escolla materiais de aceiro de carbono con alta velocidade, alta taxa de alimentación e gran profundidade de corte. Por exemplo: 1Gr11, escolla S1600, F0. 2 e unha profundidade de corte de 2mm;
2) Escolla a baixa velocidade, a baixa taxa de alimentación e a pequena profundidade de corte das ligas duras. Por exemplo: GH4033, escolla S800, F0, 08 e unha profundidade de corte de 0, 5 mm;
3) Deberá escoller a liga de titánio con baixa velocidade, alta taxa de alimentación e pequena profundidade de corte. Por exemplo, para Ti6, escolla S400, F0, 2 e unha profundidade de corte de 0, 3 mm. Tomando como exemplo o procesamento dunha parte determinada: o material é K414, que é un material moi duro. Despois de múltiples probas, finalmente foi escollido como S360, F0, 1 e unha profundidade de corte de 0, 2 para producir unha parte calificada.
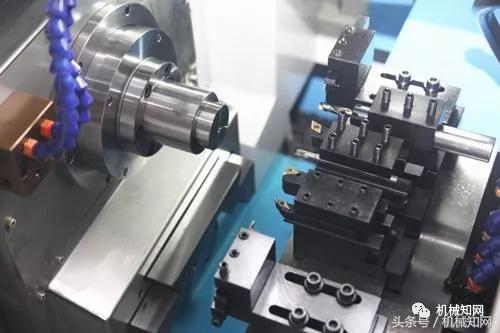
2[UNK] A técnica de aliñamento do coitelo está dividida en instrumento de aliñamento do coitelo e aliñamento directo do coitelo. A maioría dos bloqueos da fábrica non teñen un dispositivo de aliñamento de ferramentas e requiren aliñamento directo das ferramentas. As técnicas de aliñamento das ferramentas seguintes refiren a aliñamento directo das ferramentas.
Primeiro, escolla o centro da face dereita da parte como punto de aliñamento da ferramenta e pona como punto cero. Despois que a ferramenta da máquina regrese á orixe, cada ferramenta que precisa ser empregada está aliñada co centro da face dereita da parte como punto cero; Cando a ferramenta entra en contacto co extremo dereito, introduza Z0 e prema no botón de medición. O valor de compensación da ferramenta gravará automaticamente o valor medido, indicando que o eixo Z está aliñado correctamente. O eixo X é para corte de ensaio, e cando se emprega a ferramenta para axustar o círculo exterior da parte, introduza x20 para medir o valor do círculo exterior da parte que está a ser axustada (como x é 20mm). Prema no botón de medición e o valor de compensación gravará automaticamente o valor medido. Neste punto, o eixo X tamén está aliñado correctamente; Este método de alineamento de ferramentas, mesmo se a ferramenta de máquina está apagada, non mudará o valor de alineamento despois de activar e reiniciar a enerxía. É axeitado para a produción a gran escala e a longo prazo da mesma parte, durante a que o lathe non precisa de ser alineado de novo.
3[UNK] Capacidades de depuración: Despois de programar e aliñar a ferramenta, as partes precisan ser probadas e depuradas. Para evitar erros no programa e no aliñamento das ferramentas, que poden causar accidentes de colisión, deberíamos primeiro realizar máquinas de simulación de trazos baleiros. No sistema de coordenadas da ferramenta da máquina, a ferramenta debería mudarse á dereita de 2- 3 veces a lonxitude total da parte en todo; Entón comeza a simular a máquina. Despois de rematar a máquina de simulación, confirma que o programa e a ferramenta están correctos e logo comeza a maquinar as partes. Despois de que se maquine a primeira peza da parte, comprobe e confirme que está calificada, e logo atope un inspector dedicado para inspeccionala. Só despois de que o inspector dedicado confirme que está calificado pode rematar a depuración.
4[UNK] Despois de completar a primeira peza de corte de ensaio, as partes procesadas precisan ser producidas en masa. Porén, a calificación da primeira peza non significa que todo o lote de partes sexa calificado, porque durante o procesamento diferentes materiais de procesamento causarán desgaste de ferramentas. Os materiais de procesamento suave teñen menos desgaste de ferramentas, mentres os materiais de procesamento duro teñen desgaste de ferramentas máis rápido. Polo tanto, durante o procesamento, é preciso realizar inspeccións frecuentes e aumentar ou diminuir o valor de compensación
Tomando unha parte determinada como exemplo, o material de procesamento é K414, cunha lonxitude total de procesamento de 180 mm. Debido ao material extremamente duro, o uso de ferramentas é moi rápido durante o procesamento. Desde o punto de partida até o punto final, xerarase unha ligeira desviación de 10- 20 mm debido ao uso de ferramentas. Por iso, debemos engadir manualmente unha ligeira desviación de 10- 20 mm no program a para asegurar a calificación da parte.
En resumo, o principio básico do procesamento é primeiro a máquina bruta, eliminar o exceso de material da peza de traballo e despois a máquina de precisión; Debería evitarse a vibración durante o procesamento; Hai moitas razóns para evitar vibracións causadas pola deformación térmica durante o procesamento de pezas de traballo, o que pode ser debido a carga excesiva; Pode ser a resonancia entre a ferramenta da máquina e a peza de traballo, ou a ríxidez insuficiente da ferramenta da máquina, ou pode ser causada pola pasivación das ferramentas. Podemos reducir a vibración polos seguintes métodos:; Reducir a taxa lateral de alimentación e a profundidade da máquina, comprobar se o aperto da peza de traballo está seguro, aumentar a velocidade da ferramenta, que pode reducir a resonancia baixando a velocidade. Ademais, comprobar se é necesario substituír a ferramenta cunha nova.
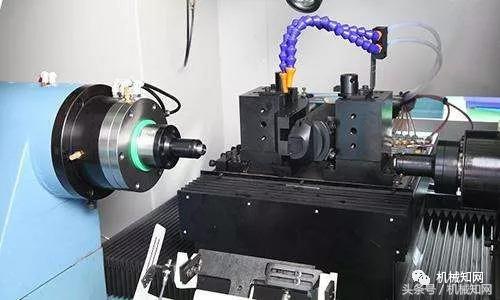
5[UNK] A experiencia de prevenir colisións entre ferramentas máquinas danifica moito a precisión das ferramentas máquinas, e o impacto varia para diferentes tipos de ferramentas máquinas. En xeral, ten un impacto maior nas ferramentas máquinas con débil ríxidez. As í que para os bloqueos de alta precisión do CNC, as colisións deben ser absolutamente eliminadas. Mentres o operador sexa coidadoso e domina certos métodos anti-colisión, as colisións poden ser completamente evitadas e evitadas.
A razón principal das colisións:
Un é o erro de entrada do diámetro e lonxitude da ferramenta de corte;
En segundo lugar, hai erros na introdución das dimensións e outras dimensións xeométricas conexas da peza de traballo, as í como erros na posición inicial da peza de traballo;
En terceiro lugar, o sistema de coordenadas de pezas de traballo da ferramenta máquina está configurado incorrectamente, ou o punto cero da ferramenta máquina é reiniciado durante o proceso de máquina, resultando en cambios. As colisións de ferramentas máquinas ocorren principalmente durante o movimento rápido da ferramenta máquina, e os perigos destas colisións son tamén os maiores, o que debe ser absolutamente evitado.
Así que os operadores deberían prestar atención especial á etapa inicial da execución do programa e a substitución das ferramentas. Se o programa é editado incorrectamente ou se introducen incorrectamente o diámetro e a lonxitude da ferramenta, probablemente ocorrarán colisións. Na fase final do programa, se a secuencia da retirada do eixo CNC é incorrecta, tamén poden ocorrer colisións.
Para evitar as colisións mencionadas, o operador debería utilizar plenamente as funcións das súas características faciais ao funcionar a ferramenta da máquina, observar se hai movementos anormais, espiras, ruído, sons anormais, vibracións ou odores queimados. Se se atopa unha situación anormal, o programa debe pararse inmediatamente. A ferramenta máquina só pode continuar a funcionar despois de resolver o problema da cama.
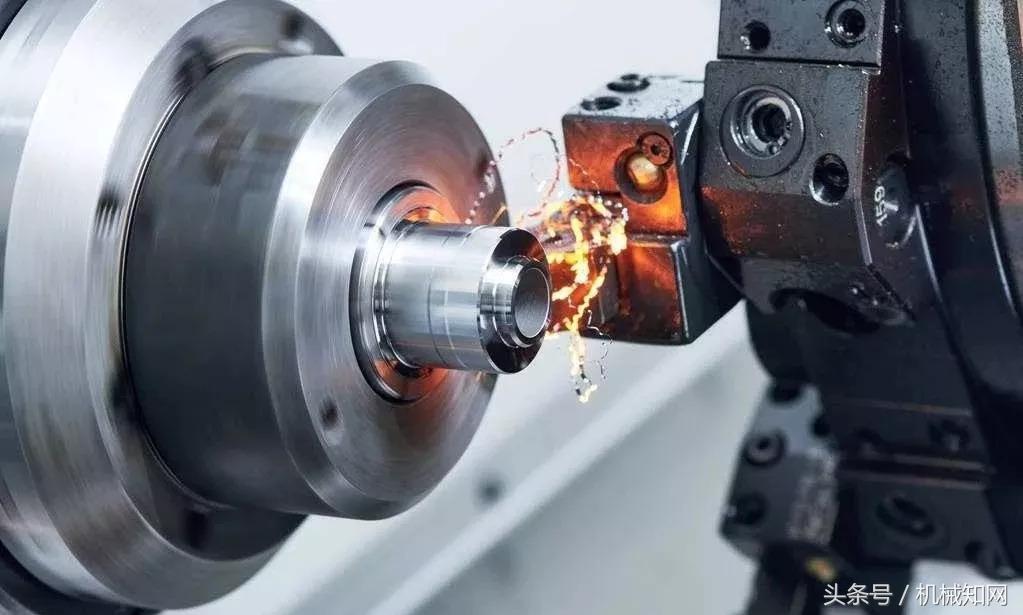
En resumo, dominar as habilidades de funcionamento das ferramentas máquinas CNC é un proceso gradual e non se pode alcanzar durante a noite. É baseado na xestión do funcionamento básico das ferramentas de máquina, o coñecemento fundamental do procesamento mecánico e o coñecemento básico da programación. As habilidades de funcionamento das ferramentas máquinas CNC non están fixadas, requiren que o operador utilize plenamente a súa imaxinación e capacidade manual nunha combinación orgánica, que é un traballo inovador.