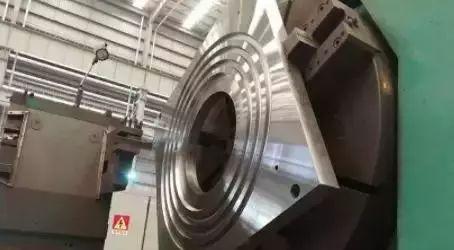
Ésszerűen válassza ki a vágási paramétereket
A hatékony fémvágás érdekében a megmunkált anyag, a vágószerszámok és a vágási körülmények a három fő elem. Ezek határozzák meg a feldolgozási időt, a szerszám élettartamát és a feldolgozási minőséget. A gazdaságilag hatékony feldolgozási módszernek a vágási feltételek ésszerű megválasztásának kell lennie.
A vágási körülmények három eleme: a vágási sebesség, az előtolási sebesség és a vágási mélység közvetlenül a szerszámkárosodást okozza. A forgácsolási sebesség növekedésével a forgácsolóél hőmérséklete emelkedik, ami mechanikai, vegyi és hőkopást eredményez. A vágási sebesség 20%-kal történő növelése felére csökkenti a szerszám élettartamát.
A takarmányozási körülmények és a szerszám kopása közötti kapcsolat nagyon kis tartományban fordul elő. De nagy adagolási sebességgel a vágási hőmérséklet emelkedik, és később jelentős kopás tapasztalható. Kevesebb hatással van a vágószerszámra, mint a vágási sebességre. Bár a vágási mélység hatása a vágószerszámokra nem olyan jelentős, mint a vágási sebesség és az előtolási sebesség, mikromélységvágás esetén a vágott anyag edzett réteget eredményez, ami szintén befolyásolja a szerszám élettartamát.
A felhasználóknak a feldolgozott anyag, keménység, vágási állapot, anyagtípus, előtolási sebesség, vágási mélység stb. alapján kell kiválasztaniuk a vágási sebességet.
A legmegfelelőbb feldolgozási feltételek kiválasztása ezen tényezők alapján történik. Az élettartam elérése érdekében rendszeres és stabil kopás az ideális feltétel.
A gyakorlati műveletek során azonban a szerszám élettartamának megválasztása a szerszám kopásával, a megmunkált méretek változásával, a felületi minőséggel, a vágási zajjal, a megmunkálási hővel és egyéb tényezőkkel függ össze. Az adatkezelési feltételek meghatározásakor a tényleges helyzet alapján kutatást kell végezni. Nehezen megmunkálható anyagok, mint például rozsdamentes acél és hőálló ötvözetek, hűtőfolyadékok vagy jó merevségű pengék használhatók.
Hogyan határozzuk meg a vágási feldolgozás három elemét?
A három elem helyes kiválasztása a fémvágási elvekről szóló tanfolyam fő tartalma, és ezen három elem kiválasztásának alapelvei:
(1) Vágási sebesség (vonalsebesség, kerületi sebesség) V (m/perc)
Az orsó percenkénti fordulatszámának kiválasztásához először tudni kell, hogy mennyi V vágóvonal fordulatszámot kell bevenni. Az V kiválasztása a szerszám anyagától, a munkadarab anyagától, a feldolgozási körülményektől stb.
Szerszám anyaga:
Kemény ötvözet, V magas értéket érhet el, általában 100 méter / perc felett, és a műszaki paramétereket általában a pengék vásárlásakor adják meg:
Milyen anyagok feldolgozásakor hány vonalsebesség választható ki. Nagy sebességű acél: V csak viszonylag alacsony szinten kapható, általában nem haladja meg a 70 méter percenként, és a legtöbb esetben 20-30 méter percenként.
Munkadarab anyaga:
Nagy keménység, alacsony V érték; Az alacsony V értékű öntöttvas 70-80 méter percenként kemény ötvözetből készült vágószerszámokhoz használható; Az alacsony széndioxid-kibocsátású acél percenként 100 méter feletti V értékű lehet, míg a színesfémek magasabb V értékűek lehetnek (100-200 méter percenként). A lecsukott acélnak és a rozsdamentes acélnak alacsonyabb V értékkel kell rendelkeznie.
Feldolgozási feltételek:
Durva megmunkálás, vegyen egy alacsonyabb V értéket; Precíziós megmunkálás, magasabb V értékkel. A szerszámgépek, munkadarabok és vágószerszámok merevségi rendszere gyenge, V pedig alacsony. Ha a CNC program S-t használ percenkénti orsófordulatszámként, akkor az S-t (percenkénti orsófordulatszám) a munkadarab átmérője és V vágóvonal sebessége alapján kell kiszámítani, ahol S=V (vágóvonal sebessége) * 1000/(3,1416 * munkadarab átmérője). Ha a CNC program állandó vonalsebességet használ, S közvetlenül használhatja a vágóvonal sebességét V (méter/perc)
(2) Takarmány mennyisége (takarmány mennyisége)
Az F főként a munkadarab feldolgozásának felületi érdességi követelményeitől függ. Precíziós megmunkálás esetén a felületi követelmények magasak, és a vágási mennyiségnek kicsinek kell lennie: 0,06 ~ 0,12 mm / orsó forgalomonként. Durva megmunkálás esetén nagyobb lehet. Ez főként a szerszám szilárdságától függ, amely általában 0,3 fölött lehet. Ha a szerszám fő gereblye szöge nagy, a szerszám szilárdsága gyenge, és az előtolási sebesség nem lehet túl nagy. Ezenkívül figyelembe kell venni a szerszámgép teljesítményét, valamint a munkadarab és a vágószerszám merevségét is. A CNC program két adagolási sebességet használ: mm/perc és mm/orsó/fordulat. A fent használt egységek mindegyike mm/orsó/fordulat. Ha mm/perc, a képlet segítségével átalakítható: adagolási sebesség per perc = adagolási sebesség per fordulat * orsó/perc
(3) Vágási mélység (vágási mélység)
Precíziós megmunkálás esetén általában ajánlatos 0,5 vagy annál kisebb sugárértéket venni. Durva megmunkálás során a munkadarab, a szerszám és a szerszámgép állapota alapján határozzák meg. Általában kis eszterga (maximális megmunkálási átmérője 400 mm vagy annál kisebb) használatos 45 # acél normalizált állapotban forgatására, és a radiális vágószerszám mélysége általában nem nagyobb, mint 5 mm. Ezenkívül meg kell jegyezni, hogy ha az eszterga orsósebessége rendes változó frekvenciafordulatszámot alkalmaz, amikor az orsó sebessége percenként nagyon alacsony (100-200 fordulat alatt), a motor kimeneti teljesítménye jelentősen csökken, és a vágási mélység és előtolási sebesség ebben az időben csak nagyon kevés.
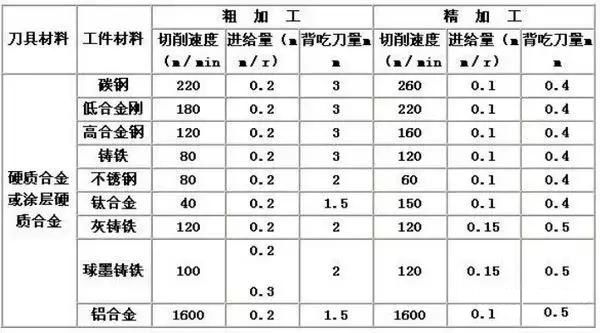
A vágószerszámok ésszerű kiválasztása
Durva esztergálás esetén nagy szilárdságú és jó tartósságú vágószerszámokat kell kiválasztani, hogy megfeleljenek a nagy hátsó vágás és a nagy előtolási sebesség követelményeinek durva esztergálás során.
Precíziós megmunkálás esetén nagy pontosságú és jó tartósságú szerszámokat kell kiválasztani a szükséges megmunkálási pontosság biztosítása érdekében.
A szerszámcserélési idő csökkentése és a szerszám beállításának megkönnyítése érdekében a lehető legnagyobb mértékben a gépbe rögzített késeket és a gépbe rögzített pengéket kell használni.
Ésszerűen válassza ki a berendezéseket
1. Próbálja meg univerzális rögzítőelemeket használni a munkadarabok rögzítésére, és kerülje a speciális rögzítőelemek használatát;
2. Állítsa be az alkatrészek pozíciós referenciaértékeit a pozíciós hibák csökkentése érdekében.
A feldolgozási útvonal meghatározása
A megmunkálási útvonal a CNC megmunkálási folyamat során a szerszám mozgási pályájára és irányára utal.
1. Képesnek kell lennie biztosítani a megmunkálási pontosság és a felületi érdesség követelményeit;
2. A feldolgozási útvonalat a lehető legnagyobb mértékben le kell rövidíteni a szerszám üresjárati idejének csökkentése érdekében.
A feldolgozási út és a megmunkálási támogatás közötti kapcsolat
Jelenleg a CNC eszterga széles körű használata hiányában általában túlzott mértékű engedélyt kell biztosítani a vakra, különösen a kovácsolt vagy öntött kemény bőrrétegeket tartalmazó támogatást a hagyományos eszterga feldolgozására. Ha CNC eszterga használatára van szükség a megmunkáláshoz, figyelmet kell fordítani a program rugalmas elrendezésére.
A berendezések beépítésének kulcsfontosságú pontjai
Jelenleg a hidraulikus tokmány és a hidraulikus rögzítőhenger közötti kapcsolatot egy húzórúddal érjük el. A hidraulikus tokmány rögzítésének kulcsfontosságú pontjai a következők: először egy fogantyúval távolítsuk el a hidraulikus hengeren lévő anyát, távolítsuk el a húzócsőt és húzzuk ki az orsó hátsó végéből, majd egy fogantyúval távolítsuk el a tokmány rögzítőcsavarját a tokmány eltávolításához.