Az alumínium precíziós alkatrészek és termékek népszerűek könnyű súlyuk és kiváló megjelenésük miatt, és széles körben használják az iparban és a napi szükségletekben. A technológia folyamatos fejlődésével az emberek igénye a termékek sokféleségére egyre erősebbé válik. Ezért az alumíniumötvözet termékek folyamatkövetelményei egyre magasabbak, és a piaci kereslet is növekszik. Az alumíniumötvözet héj termékek sokszínűségének és kiváló minőségének kielégítése érdekében az alumíniumötvözet CNC megmunkáló gyártók összefoglalták azokat a folyamati technikákat és kérdéseket, amelyeket meg kell jegyezni az alumínium CNC megmunkálásban.
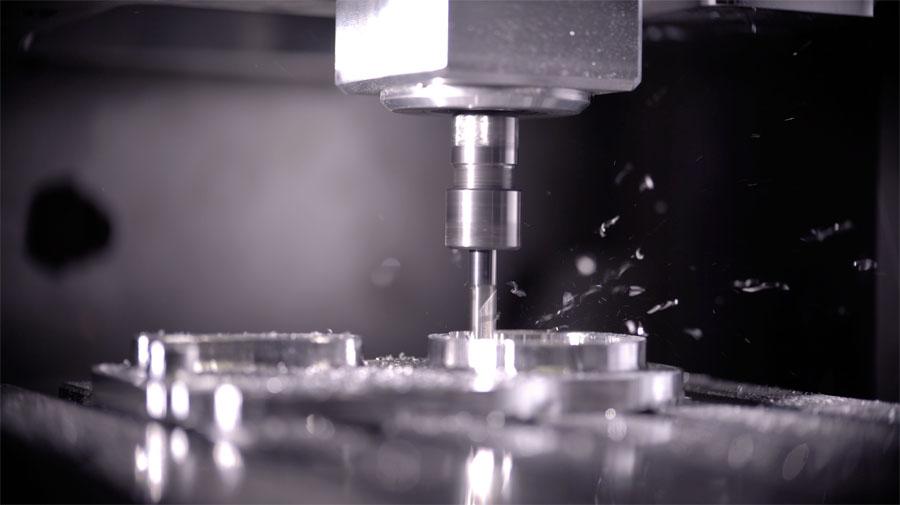
1. Válassza ki a megfelelő feldolgozási módot
A numerikus vezérlő vágás egy egyszerűsített vágási módszer és általában használt eljárás alumínium anyagok precíziós megmunkálásához. Többirányú vágási képességgel, spirálvágási interpolációval és kontúrvágási interpolációval rendelkező végmarót használok. Kevesebb lyukat dolgozzon fel kevesebb szerszámmal.
2. A gömbvégű marók spirál interpolációval együtt használhatók a kúpos furatok folyamatos feldolgozására.
Golyós végű marók és spirál interpolációs fúrók használhatók fúráshoz és maráshoz. Végmarók használhatók kontúrvágási interpolációval együtt furatok félprecíziós megmunkálásához és alkatrészek precíziós megmunkálásához. A menetmegmunkáláshoz használt végmaró spirálinterpolációval együtt használható különböző menetes furatok megmunkálására.
Hatékony alumíniumötvözet precíziós alkatrészek megmunkálhatók különböző méretű precíziós furatokban szerszám interpolációval. Az egyes fogak terhelése viszonylag könnyű, különösen nagy sebességű marógépek használata esetén. Ezért ugyanaz a bevont kemény ötvözet végmaró használható különböző megmunkáló anyagok nagy sebességű és nagy pontosságú fúrásához.
3. Válassza ki a megfelelő vágási mennyiséget
A munkatársak a feldolgozott anyag, a keménység, a vágási körülmények, az anyagtípus és a vágási mélység alapján választhatják ki, hogy melyik vágási sebességet használják. Ezek a feltételek szükségesek a gép kopásának hatékony csökkentéséhez.
4. Válassza ki a megfelelő eszközöket.
Rakásszög: A megfelelő rakásszöget kell kiválasztani az élerősség fenntartása mellett. Az egyik oldalon éles vágóéleket csiszolhat, hogy csökkentse a vágási deformációt, simábbá tegye a forgácseltávolítást, és alacsonyabb vágási ellenállást és hőt. Ne használjon negatív első szögű szerszámokat.
Hátsó sarok: A hátsó sarok mérete közvetlenül befolyásolja a hátsó sarok felületének kopását és a megmunkált felület minőségét. A vágási vastagság fontos kritérium a hátsó szög kiválasztásához. Durva megmunkálás esetén az előtolási sebesség nagy, a vágási terhelés magas, és a hőtermelés nagy, ezért szükséges, hogy a szerszám jó hőelvezetési körülményekkel rendelkezzen. Ezért kisebb hátsó szöget kell választani. Marógéppel történő precíziós megmunkálás esetén a forgácsolóélet csiszolása szükséges, hogy csökkentse a súrlódást a hátsó forgácsolófelület és a megmunkáló felület között, és minimalizálja a rugalmas deformációt. Ezért nagyobb hátsó szöget kell választani.
Spirálszög: A spirálszöget a lehető legnagyobb mértékben kell kiválasztani, hogy a marógép sima legyen és csökkentse a marógép terhelését.
Megközelítési szög: A megközelítési szög megfelelő csökkentése hatékonyan javíthatja a hőelvezetési körülményeket és csökkentheti a kezelési terület átlagos hőmérsékletét.
Csökkentse a marófogak számát, és növelje a forgácseltávolítás helyét.
Az alumíniumötvözet anyagainak nagy plaszticitása miatt a feldolgozás során jelentős vágási deformáció tapasztalható, ami nagy forgácsterületet eredményez. A forgácshorny alsó sugarának nagynak kell lennie, és a maró fogainak számának kicsinek kell lennie. Például a 20 mm-nél kisebb átmérőjű marómarók 2 fogat használnak, de a 30 ~ 60 mm átmérőjű marómarók a legjobban 3 foggal vannak felszerelve, hogy megakadályozzák a vékony alumíniumötvözet alkatrészek forgácselzáródás miatti deformációját.
Finomkörű fogak: A fogszél érdességének értéke Ra=0,4um. Az új kés használata előtt az elülső és hátsó részét finom olajkővel finoman kell polírozni, hogy eltávolítsa a csiszolás során hátrahagyott kopásokat vagy enyhe fogásokat. Ily módon nemcsak a vágási hő csökkenthető, hanem a vágási deformáció is viszonylag kicsi.
Szigorúan ellenőrizzük a szerszámok kopási normáit. Ahogy a szerszám kimerül, a munkadarab felületi érdességértéke nő, a vágási hőmérséklet emelkedik, és a munkadarab deformációja nő. Ezért a jó kopásállóságú szerszámanyagok kiválasztása mellett a kopási szabvány nem haladhatja meg a 0,2 mm-t. Ellenkező esetben könnyű törmelék tumorok kialakulása. A vágás során a munkadarab hőmérséklete általában nem haladhatja meg a 100 ℃-ot a deformáció megakadályozása érdekében.
5. Válasszon egy ésszerű berendezést.
Az alkatrészeknek teljes mértékben meg kell felelniük a gép igényeinek a szükségtelen pozicionálási hibák csökkentése érdekében, és speciális rögzítőszerszámokat kell kiválasztani.
(6) Meghatározza az ésszerű feldolgozási módot.
A gép kopásának csökkentése érdekében próbálja meg a lehető legrövidebben tartani a feldolgozási útvonalat.
Nagy sebességű vágásnál a megmunkálási engedély nagy, és a vágás időszakos, így a marás során rezgés keletkezik, ami befolyásolja a megmunkálási pontosságot és a felületi érdességet. Ezért a CNC nagy sebességű vágás általában durva megmunkálásra, félprecíziós megmunkálásra, saroktisztításra, precíziós megmunkálásra és egyéb folyamatokra osztható.
A nagy pontosságot igénylő alkatrészek esetében a precíziós megmunkálás előtt másodlagos félmegmunkálásra lehet szükség. Durva megmunkálás után az alkatrészeket természetesen hűtik, hogy kiküszöböljék a durva megmunkálás által generált belső feszültséget és csökkentsék a deformációt. A durva megmunkálás után fennmaradó mennyiségnek nagyobbnak kell lennie, mint a deformáció mennyisége (általában 1-2mm). A precíziós megmunkálási folyamat során az alkatrész precíziós megmunkálási felületének egységes megmunkálási tűréseket kell tartania. 0,2-0,5 mm általában jó. Ez stabil marad a szerszám a megmunkálási folyamat során, és jelentősen csökkenti a vágási deformációt. A termék pontosságának biztosítása érdekében jó felületi feldolgozási minőséget érhet el.