Mengurangi tindakan deformasi selama mesinan bagian adalah proses komprensif yang membutuhkan pertimbangan dari berbagai aspek seperti bahan, metode mesinan, desain fixture, parameter memotong, dll. Berikut adalah beberapa tindakan spesifik: pertama, optimisasi proses produksi kosong untuk mengurangi stres internal: kosong akan menghasilkan stres internal selama proses produksi, yang mungkin menyebabkan deformasi bagian dalam proses berikutnya. Dengan penuaan alami, penuaan artificial, atau perawatan getaran, stres internal kosong dapat secara parsial dihilangkan, dengan itu mengurangi deformasi selama proses. 2. Pilih parameter pemotong yang sesuai dan parameter pemotong alat: kecepatan pemotong, kadar feed, kedalaman pemotong, dan parameter lainnya perlu dipilih secara layak menurut bahan, bentuk, dan keperluan proses bagian. Contohnya, mengurangi jumlah pemotongan belakang dapat mengurangi kekuatan pemotongan, tetapi juga mengurangi efisiensi produksi. Dalam mesin CNC, mungkin untuk mempertahankan efisiensi mesin sementara mengurangi kekuatan memotong dengan meningkatkan kecepatan mesin dan tingkat feed. Seleksi alat: Material dan parameter geometri alat memiliki dampak yang signifikan pada kekuatan memotong dan memotong panas. Seleksi yang masuk akal dari parameter geometri alat, seperti sudut rake, sudut rake, sudut heliks, dan sudut lead, dapat menggali pinggir tajam dan mengurangi deformasi potongan. Selain itu, memperbaiki struktur alat, seperti mengurangi jumlah gigi pemotong pemotong pemotong pemotong, meningkatkan ruang chip, dan memperbaiki gigi pemotong, juga dapat mengurangi pemotong panas dan memotong deformasi. 3[UNK] Seleksi yang masuk akal dari metode tekanan dan desain pemasangan kekuatan tekanan: desain dan seleksi tekanan memiliki dampak yang signifikan pada deformasi bagian selama mesin. Reasonable fixture design can ensure the stability of parts during processing and reduce the impact of clamping force on part deformation. Untuk bagian-bagian dengan dinding tipis dengan ketenangan yang buruk, kompresi wajah akhir aksi atau peralatan seperti cangkir suction vakum dapat digunakan untuk mendapatkan kekuatan pegangan yang disebarkan secara seragam. Kontrol kekuatan memeluk: kekuatan memeluk seharusnya sebanyak mungkin sementara memastikan bahwa bagian kerja tidak hilang. Kekuatan tepat bisa menyebabkan deformasi bagian. Selain itu, kekuatan memeluk harus diaplikasikan sebanyak mungkin pada permukaan dukungan dan dalam arah ketat yang baik bagian kerja. 4[UNK] Secara masuk akal mengatur urutan proses dan parameter memotong: urutan proses yang masuk akal dapat mengurangi stres internal bagian dan mengurangi resiko deformasi. Contohnya, mesin kasar dapat dilakukan pertama, diikuti dengan mesin presisi untuk mengurangi dampak kekuatan memotong dan memotong panas pada bagian. Untuk bagian-bagian dengan pembayaran mesin besar, mesin simetrik harus diadopsi untuk menghindari deformasi disebabkan oleh konsentrasi panas. Parameter pemotong: Selama proses pemotong, kekuatan pemotong dan pemotong panas dikurangi dengan mengubah parameter pemotong. Dalam mesin CNC, tujuan ini dapat dicapai dengan mengurangi jumlah potongan belakang, meningkatkan kadar makan, dan meningkatkan kecepatan mesin. 5[UNK] Monitor dan penyesuaian proses mesinan waktu nyata: Monitor waktu nyata dilakukan selama proses mesinan untuk mendeteksi dan memperbaiki deformasi dalam waktu yang tepat. Dengan parameter pengawasan seperti kekuatan memotong dan suhu memotong, mungkin untuk menentukan apakah bagian-bagian telah mengalami deformasi dan mengambil tindakan yang sesuai untuk penyesuaian. 6[UNK] Ukuran lainnya untuk meningkatkan metode memeluk bagian kerja: Untuk bagian yang tidak ketat seperti bagian kerja dengan dinding tipis, metode memenuhi dapat digunakan untuk meningkatkan proses ketat dan mengurangi deformasi selama proses memeluk dan memotong. Perobatan permukaan: Melalui proses perawatan permukaan seperti anodizi, karakteristik permukaan bagian dapat lebih lanjut diperbaiki atau diubah, meningkatkan ketat dan resistensi mereka terhadap deformasi.
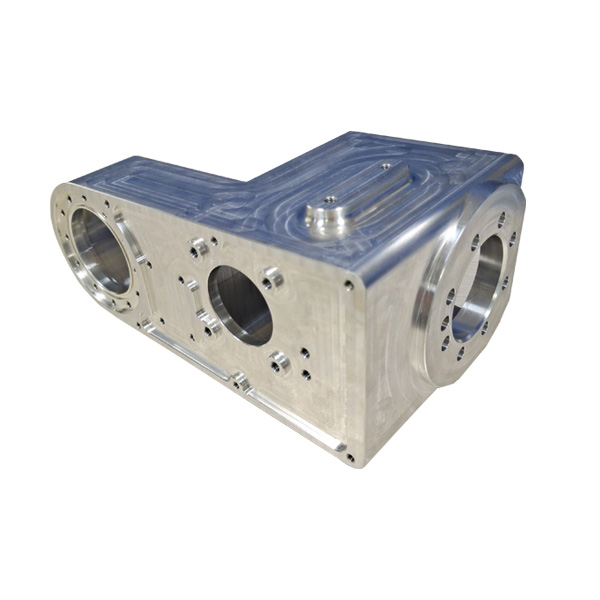