板金加工板金加工は金属薄板(通常6 mm以下)に対する総合冷間加工技術であり、せん断、打ち抜き、曲げ、溶接、カシメ、金型成形及び表面処理などを含む。その顕著な特徴は、同じ部品の厚さが一致していることです。
板金加工方法:非金型加工:数パンチ、レーザー切断、板切り機、折り曲げ機、リベット機などの設備を通じて板金に対して行う技術方式は、一般的にサンプル製作あるいは小ロット生産に用いられ、コストが高い。加工周期が短く、反応が速い。金型加工:固定された金型を通じて、板金を加工し、一般的には下型、成形型があり、主に大量生産に用いられ、コストが低い。前期の金型はコストが高く、部品の品質が保証されている。前期加工周期が長く、金型コストが高い。板金加工プロセス:材料投入:数ストローク、レーザー切断、切断機
成形-曲げ、引張り、パンチ:曲げ機、パンチなど
その他の加工:リベット押え、歯攻めなど
溶接ようせつ:シートメタルの接続方法しーとめたるのせつぞくほうしき
表面処理:スプレー、めっき、糸引き、シルク印刷など
板金加工技術--材料除去板金の材料除去方法は主に数パンチ、レーザー切断、板金切断機、金型材料除去などがあり、数値制御は現在常用方式であり、レーザー切断はサンプリング段階(ステンレス板金加工も可能)に用いられることが多く、加工費用が高く、金型材料除去は大量加工に用いられることが多い。
次に、主に数沖で板金の下材を紹介します。
数パンチは回転塔NCプレスとも呼ばれ、材料の出し入れ、パンチ、延伸穴、転筋、ルーバーなどに使用でき、その加工精度は+/-0.1 mmに達することができる。
数値制御加工可能な板材の厚さは、
冷間圧延板、熱間圧延板4.0 mm
アルミニウム板5.0 mm
ステンレス板2.0 mm
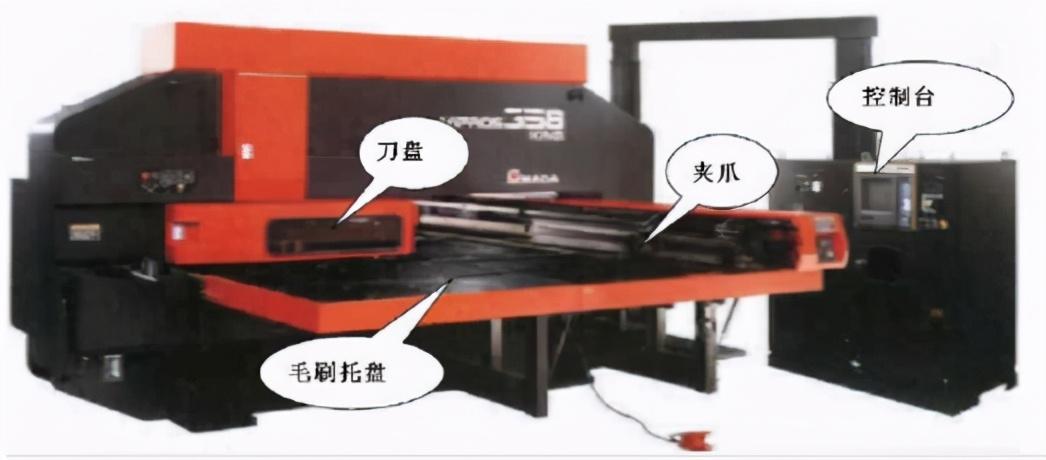
パンチ穴には最小寸法要件があります。パンチ穴の最小寸法は、穴の形状、材料の機械的性質、材料の厚さに関係しています。(下図)
2.パンチの穴間隔と穴マージンを数えます。部品のパンチエッジの外形からの最小距離が部品外形エッジと平行でない場合、この最小距離は材料厚さtより小さくないこと。平行の場合、1.5 t以上でなければならない。(下図)
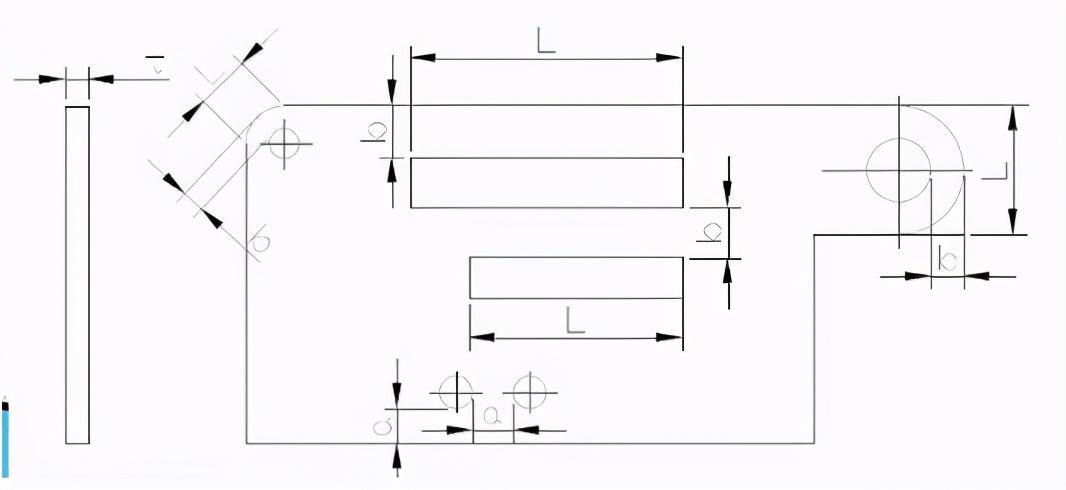
3.穴を延伸する時、延伸穴の縁からの最小距離は3 Tで、2つの延伸穴の間の最小距離は6 Tで、延伸穴の曲げエッジ(内)からの最小安全距離は3 T+R(Tは板金厚さ、Rは曲げフィレット)である
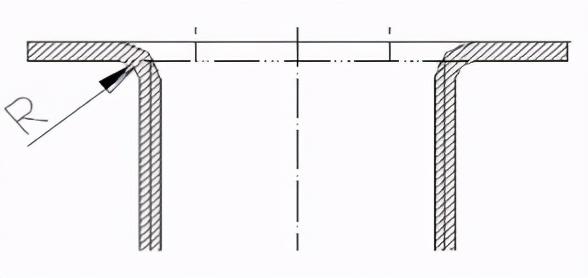
4.曲げ部材及び絞り部材を引張して穴を開ける場合、その穴壁と直壁の間に一定の距離を保持しなければならない。(下図)
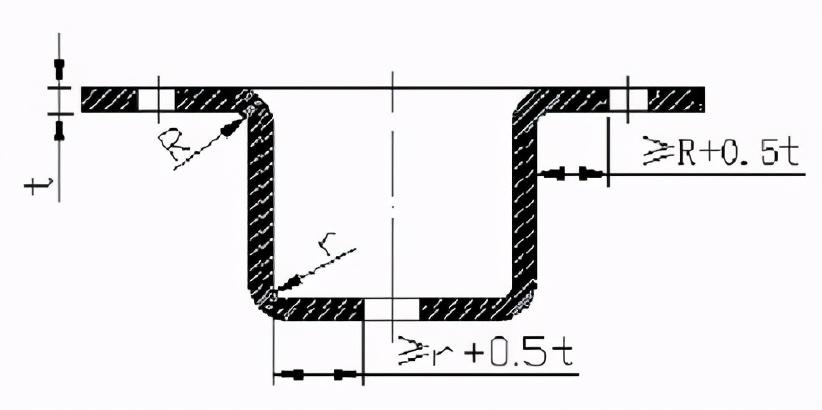
板金加工プロセス--成形板金の成形は主に板金の曲げ、延伸である。
1.板金ベンド1.1板金のベンドは、ベンド加工機を主に使用します。
折り畳み機の加工精度
一折:+/-0.1 mm
二つ折り:+/-0.2 mm
二つ折り以上:+/-0.3 mm
1.2曲げ加工手順の基本原則:内から外へ曲げ、小さいものから大きいものまで曲げ、まず特殊な形状を曲げ、前工程で成形した後、後工程に影響や干渉を与えない。
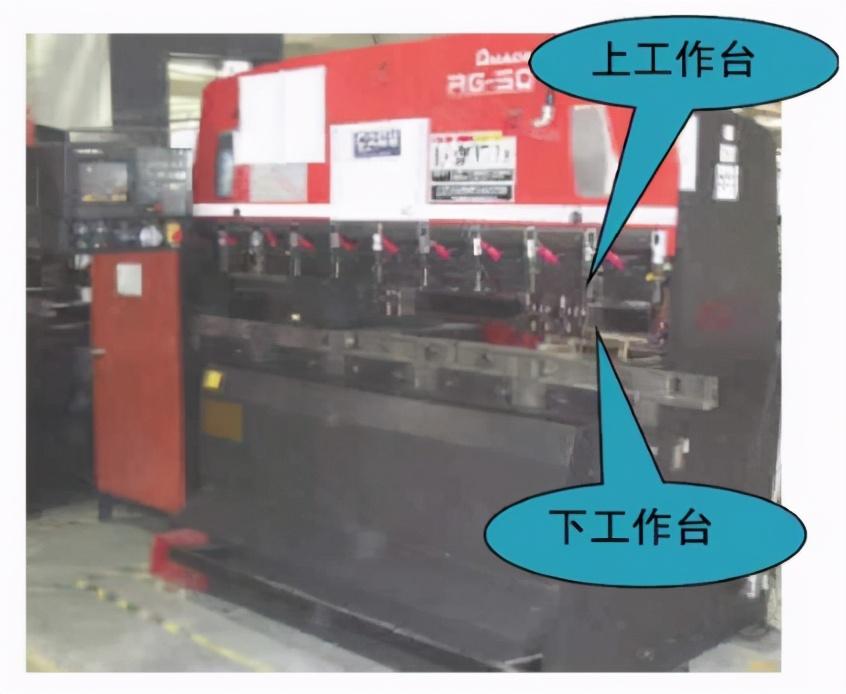
1.3一般的なベンド形状:
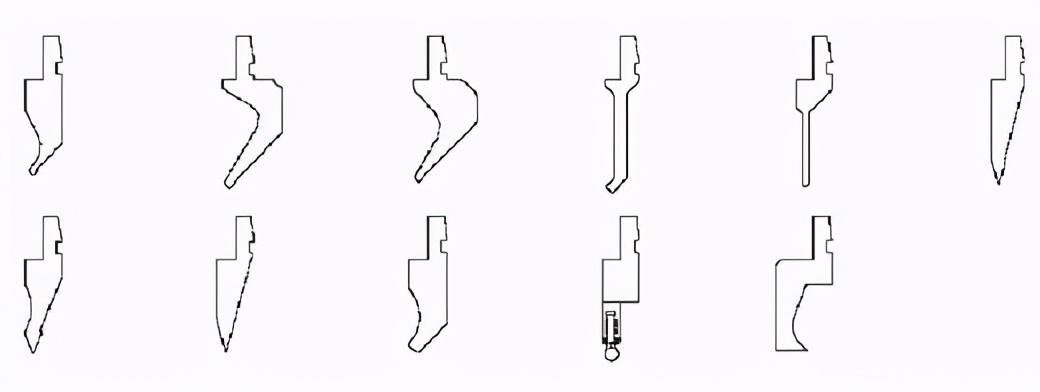
一般的なVスロット形状:
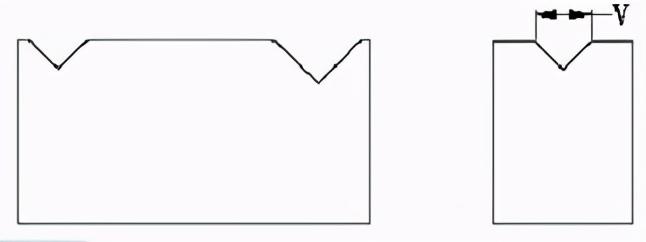
1.4ベンド部品の最小曲げ半径:
材料が湾曲すると、そのフィレット領域上で外層が伸張され、内層が圧縮されます。材料の厚さが一定である場合、内rが小さいほど、材料の延伸と圧縮が深刻になる。外層フィレットの引張応力が材料の限界強度を超えると、亀裂や折れが発生するため、曲げ部品の構造設計は、過度に小さい曲げフィレット半径を避けるべきである。会社で一般的に使用されている材料の最小ベンド半径を次の表に示します。
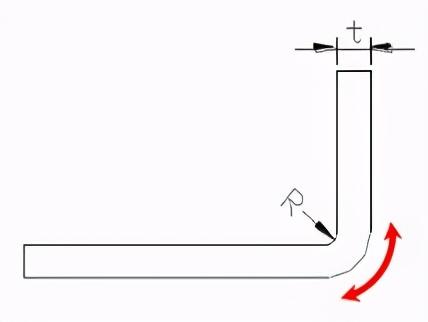
ベンド部品の最小曲げ半径テーブル:
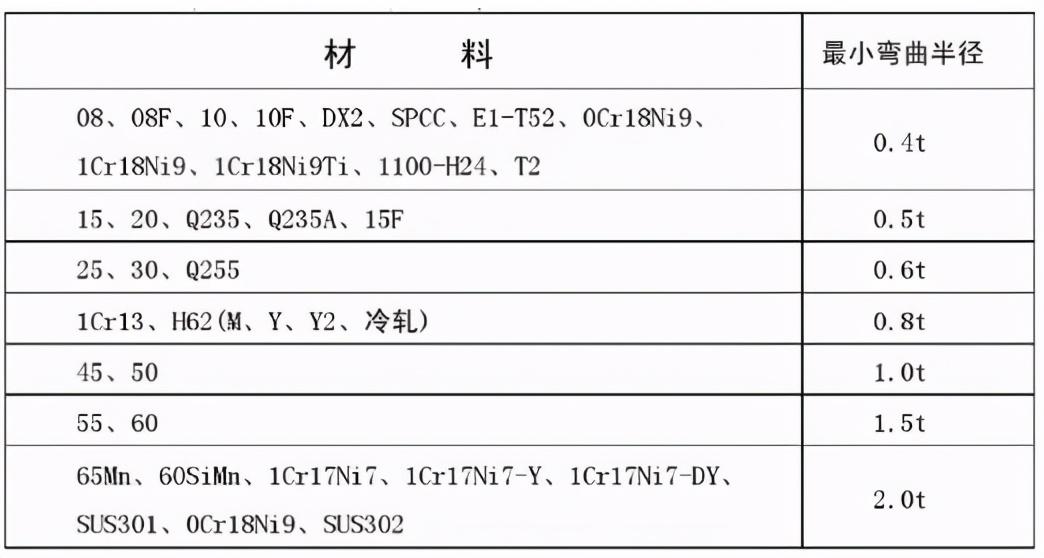
曲げ半径とは、曲げ部材の内側半径であり、tは材料の肉厚である。
1.5ベンドの直線エッジの高さ:
一般的な場合の最小直線エッジ高さは小さすぎるべきではなく、最小高さ要求:h>2 t
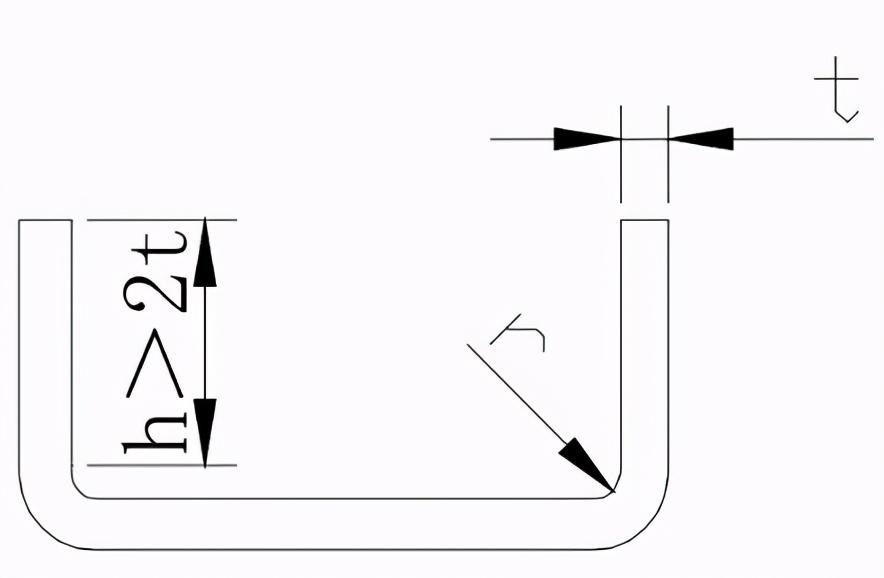
曲げ部材の直線エッジ高さh 2 tが必要な場合は、まず曲げエッジ高さを大きくし、曲げた後に必要な寸法に加工しなければならない。または曲げ変形領域内で浅い溝を加工した後、曲げます。
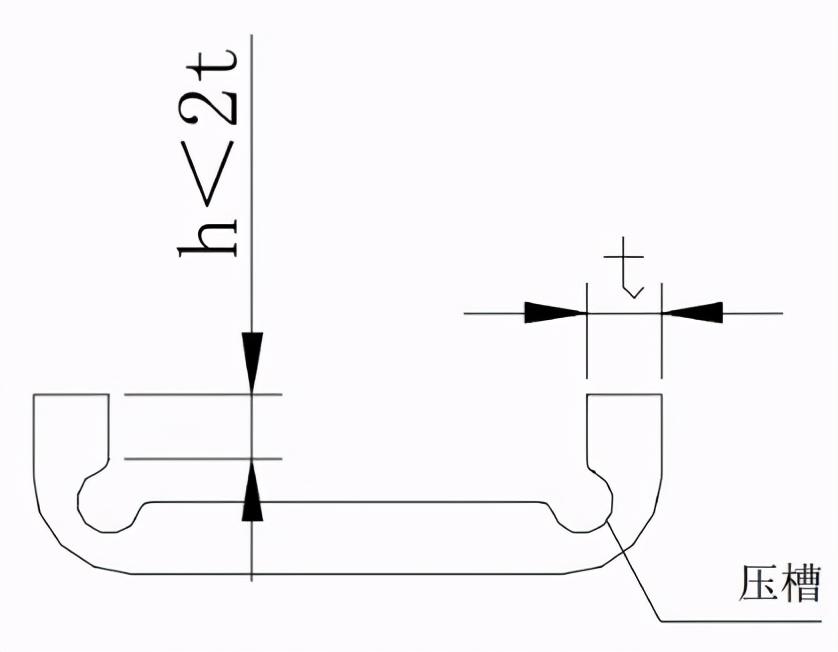
1.6ベンドエッジの側面に面取りを持つ最小ベンド直線エッジ高さ:
フランジ側縁に傾斜角を有する湾曲部材を有する場合、側面の最小高さは、h=(2〜4)t> ;3mm
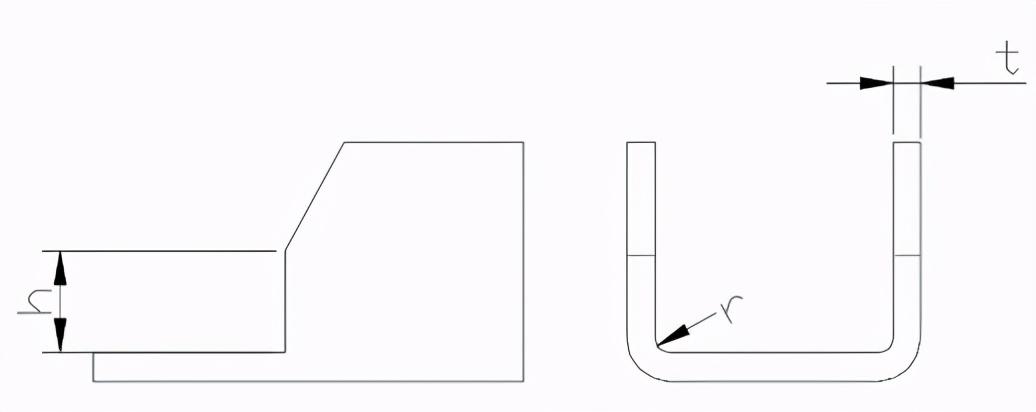
1.7ベンド上の穴マージン:
穴マージン:先に穴を開けてから折り曲げ、穴の位置は曲げ変形領域の外にあるべきで、曲げ時に穴が変形することを避ける。穴壁から曲げエッジまでの距離は次の表を参照してください。
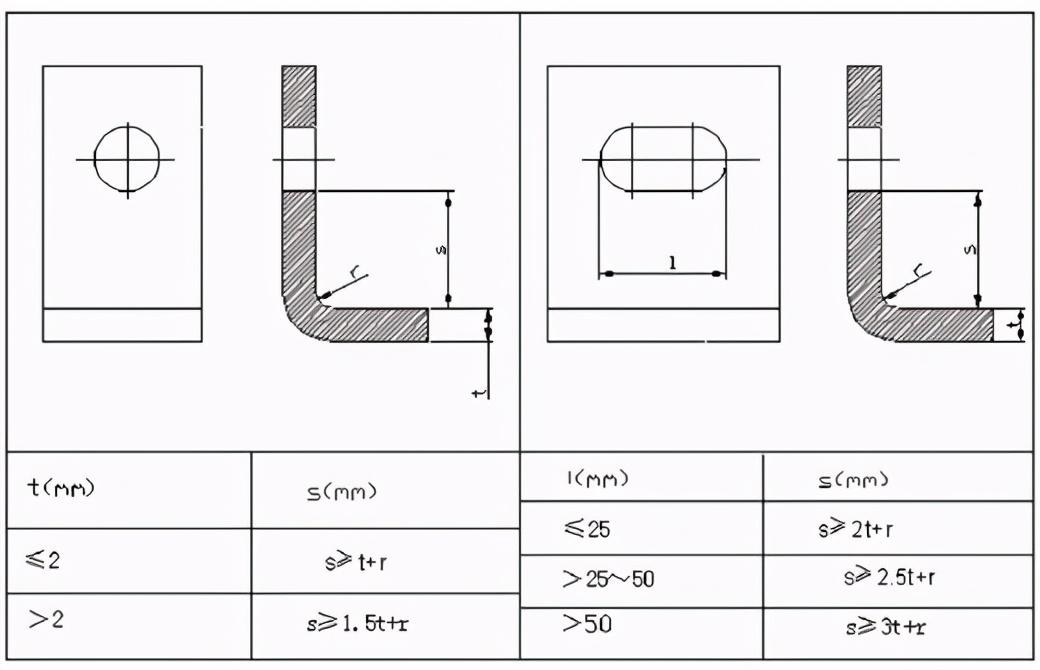
1.8部分的に湾曲したプロセスカット:
曲げ部材の曲げ線は寸法突然変異の位置を避けるべきである。あるエッジを部分的に曲げた場合、尖角出応力集中による亀裂の発生を防止するために、寸法突然変異箇所(図a)から離れたり、溝(図b)を開いたり、穴をあけたりするために、湾曲線を一定距離移動させることができます(図c)。注意図の寸法要件:SR、溝幅kt溝深さLt+R+k/2。
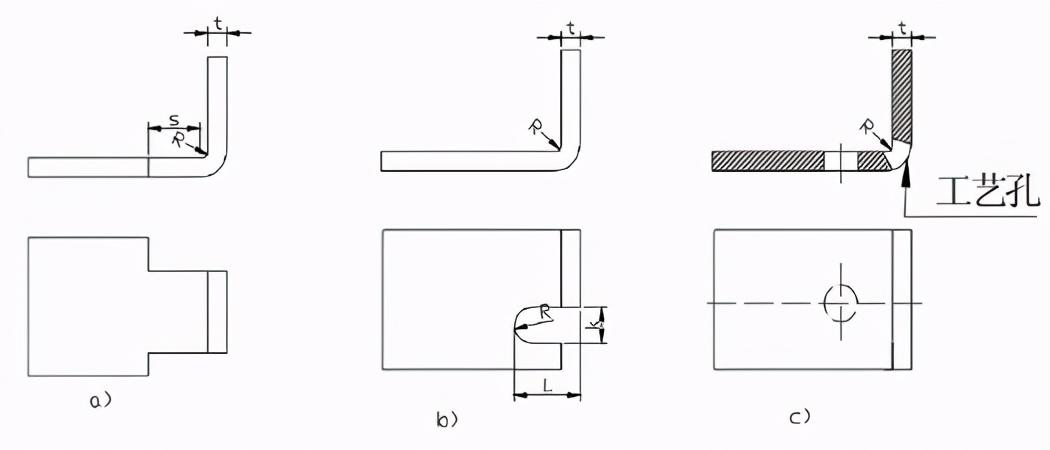
1.9斜辺を持つベンドエッジは変形領域を避けなければならない:
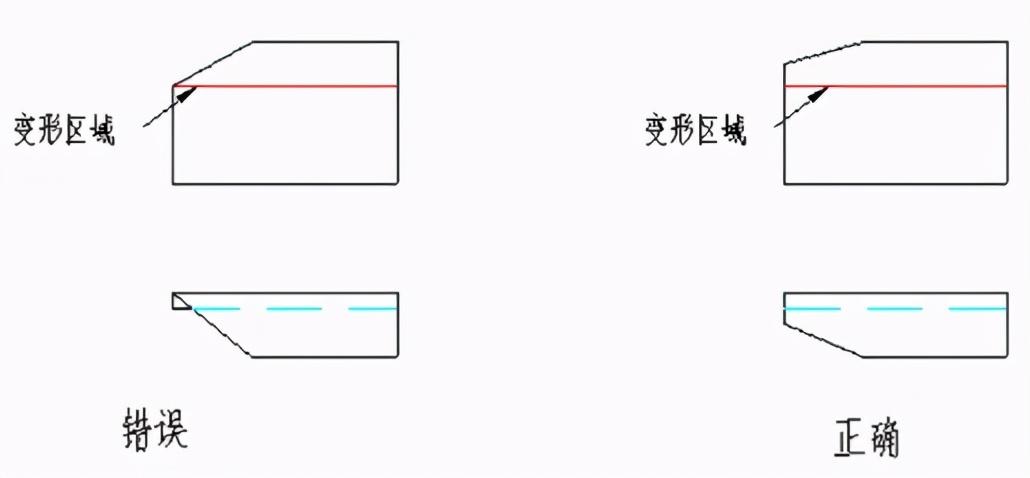
1.10板金フリル(エッジを打ち殺す)の設計要件:
板金フリルのデッドエッジ長さは、材料の厚さに関係しています。下図に示すように、一般的なデッドエッジ最小長L 3.5 t+Rである。
ここで、tは材料の肉厚、Rはエッジを打ち殺す前工程(下図右に示す)の最小内曲げ半径である。

1.11追加されたプロセス位置決め穴:
ブランクが金型中で正確に位置決めされ、曲げ時にブランクがずれて廃棄物が発生するのを防止するために、下図に示すように、予め設計時にプロセス位置決め穴を追加しなければならない。特に複数回曲げ成形した部品は、すべてプロセス穴を位置決め基準として、積算誤差を減少し、製品の品質を保証しなければならない。
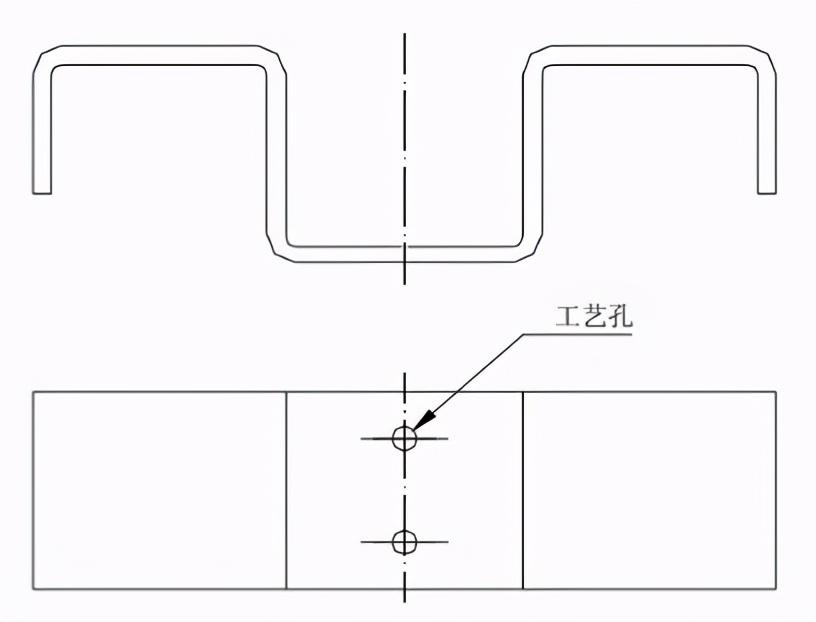
1.12曲げ部品に関する寸法を表示する時、技術性を考慮する:
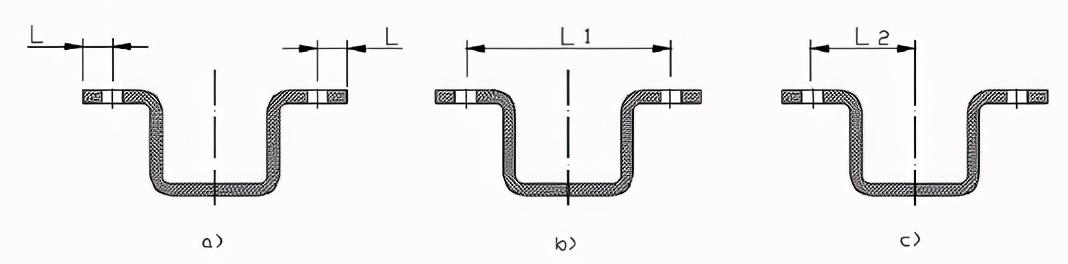
上図のように、a)先に穴を開けてから折り曲げて、L寸法精度が保証しやすく、加工が便利である。b)とc)寸法L精度の要求が高い場合、先に曲げてから穴を加工する必要があり、加工が面倒である。
1.13曲げ部材のスプリングバックはスプリングバックに影響する要素が多く、材料の機械的性質、肉厚、曲げ半径及び曲げ時の正圧力などが含まれる。曲げ部材の内角半径と板厚の比が大きいほど、スプリングバックが大きくなります。設計上の反発を抑制する方法としては、ベンドの反発を例示し、現在は主にメーカーが金型設計時に一定の措置を取って回避している。同時に、設計面からいくつかの構造を改善することで、反発角の簡略化を下図のように促す:湾曲領域で補強リブをプレスすることは、ワークの剛性を高めることができるだけでなく、反発を抑制することにも有利である。
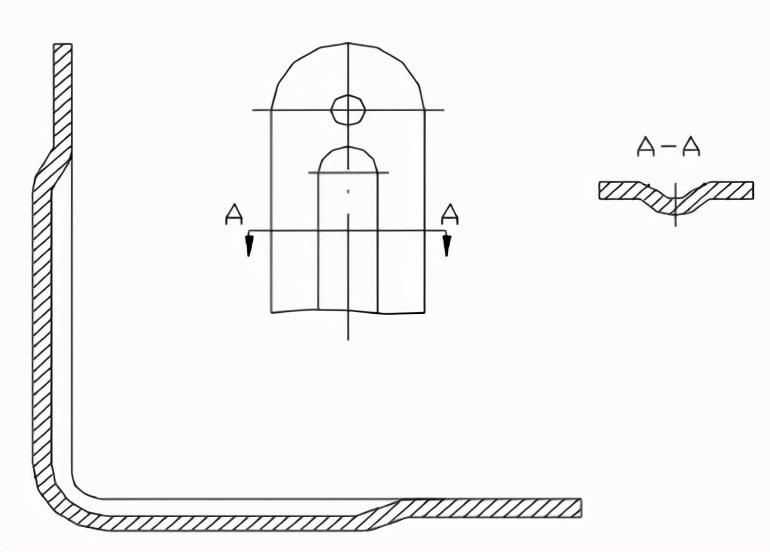
2.板金延伸板金の延伸は主に数値制御または普通パンチによって行われ、各種の延伸パンチまたは金型が必要である。
延伸材の形状はできるだけ簡単で対称的で、できるだけ一回延伸成形しなければならない。
複数回延伸する必要がある部品は、延伸中に表面に発生する可能性がある痕跡を許容する必要があります。
組立要求を保証する前提で、延伸側壁に一定の傾斜を持たせなければならない。
2.1ストレッチャーの底部と直壁の間のフィレット半径の大きさの要件:
下図に示すように、延伸材の底部と直壁との間のフィレット半径は板厚、すなわちr 1 tより大きくなければならない。延伸をより円滑に行うためには、一般にr 1=(3〜5)tをとり、最大フィレット半径は板厚の8倍以下、すなわちr 18 tでなければならない。
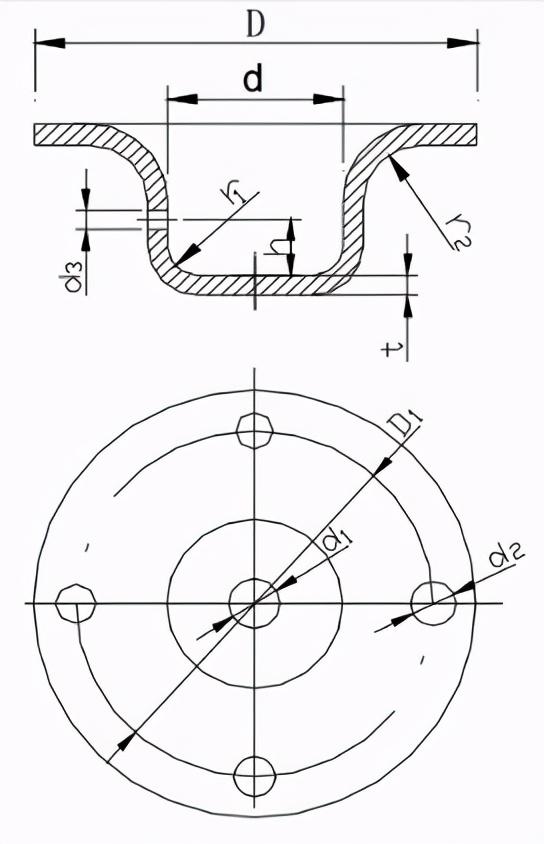
2.2延伸フランジと壁の間のフィレット半径
延伸材のフランジと壁との間のフィレット半径は板厚の2倍、すなわちr 22 tより大きくなければならず、延伸をより円滑に行うためには、一般にr 2=(5 ~ 10)tをとり、最大フランジ半径は板厚の8倍、すなわちr 28 t以下でなければならない。(上図参照)
2.3円形延伸材の内腔直径
円形延伸材の内腔直径は、延伸時に押え板がしわにならないように、Dd+10 tをとるべきである。(上図参照)
2.4矩形延伸材の隣接する2つの壁間のフィレット半径
矩形延伸材の隣接する2つの壁間のフィレット半径はr 3 3 tをとり、延伸回数を減らすためにできるだけr 3 H/5をとり、一度に引き出す必要があります。
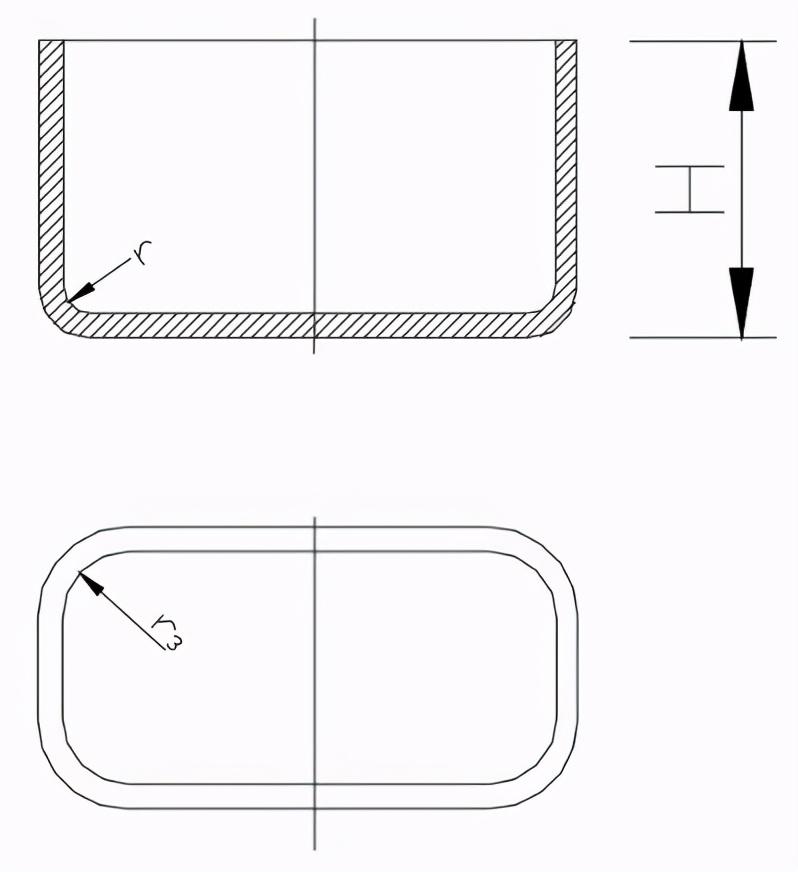
2.5円形フランジレス延伸材を一次成形する際の高さと直径の寸法関係の要求
円形フランジなし延伸材を一次成形する場合、高さHと直径dの比は下図に示すように0.4以下、すなわちH/d 0.4になるべきである。
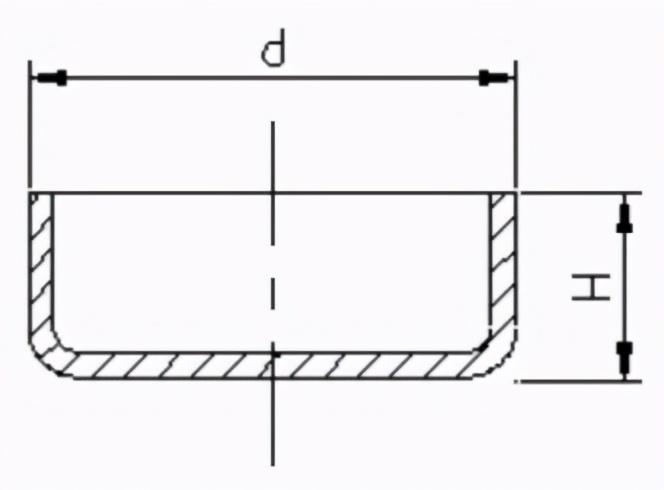
2.6延伸材材料の厚さ変化:
延伸材は各所で応力の大きさが異なるため、延伸後の材料の厚さが変化する。一般的に、底部中央は元の厚さを維持し、底部の角の材料は薄くなり、頂部のフランジに近い材料は厚くなり、矩形延伸材の周囲の角の材料は厚くなる。
2.7延伸材の製品寸法の表示方法
延伸製品を設計する際、製品図の寸法に対して外部寸法または内部寸法を保証しなければならず、同時に内外寸法を表示することはできないことを明確に明記しなければならない。
2.8延伸材の寸法公差の表示方法
延伸材凹凸円弧の内半径及び一次成形円筒形延伸材の高さ寸法公差は両面対称偏差であり、その偏差値は国標(GB)16級精度公差絶対値の半分であり、番号を冠する。
3.板金のその他の成形:補強リブ--板状金属部品にリブを押し、構造剛性を高めるのに役立つ。
ルーバー--ルーバーは通常、さまざまなカバーまたはキャビネット上で通気放熱の役割を果たすために使用されます。
「穴フランジ」(押し出し穴)-ねじを加工したり、穴の剛性を高めたりするために使用します。
3.1リブ:
リブ構造とその寸法選択
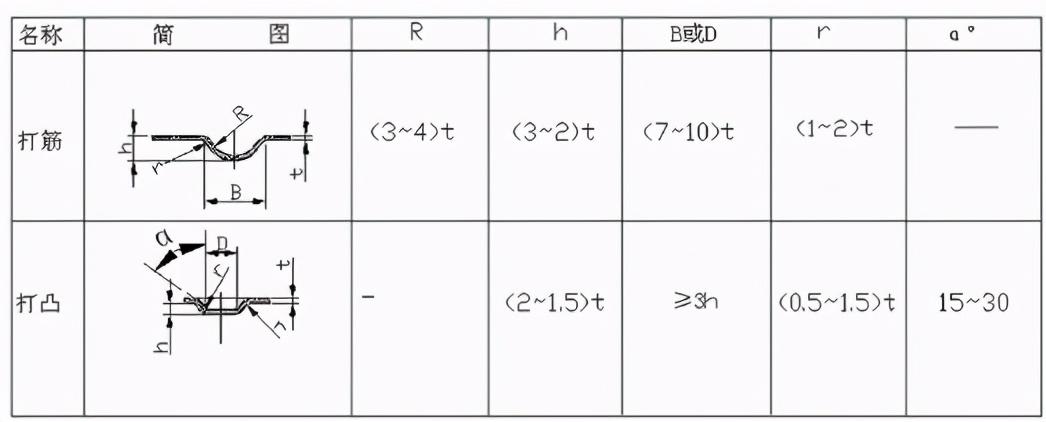
凸ピッチと凸マージンの限界寸法を表に示します。
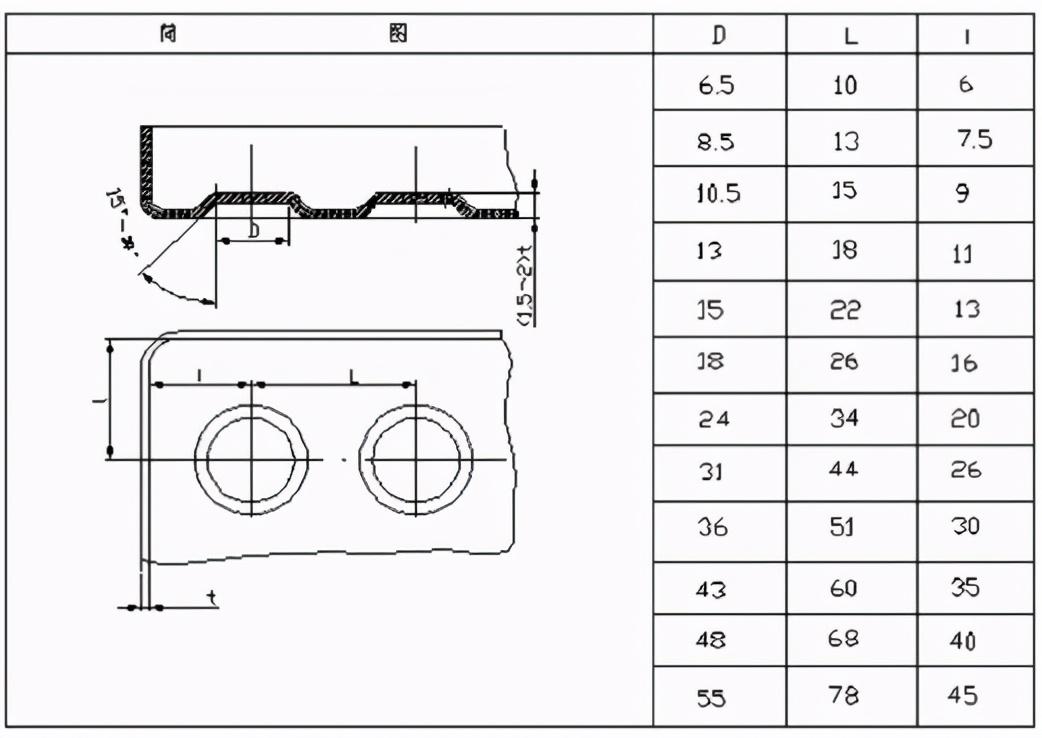
3.2ブラインド
ブラインド成形方法は、パンチの片側刃口を用いて材料を切開するが、パンチの残りの部分は材料を同時に引張変形し、片側開口の起伏形状を形成する。
ブラインドの典型的な構造は下図を参照
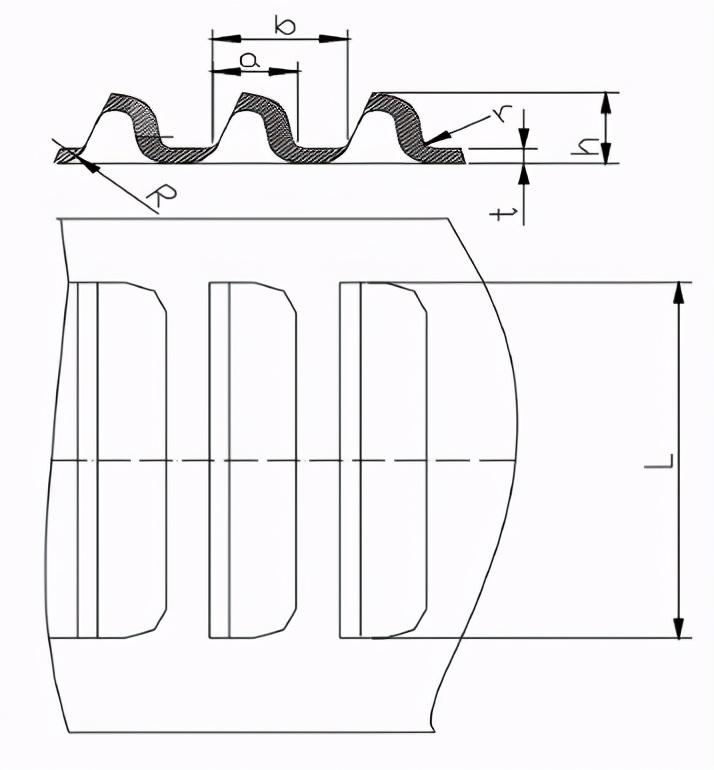
ブラインドサイズ要件:a 4 t、b6t;h5t;L24t;r0.5t。
3.3穴フランジ(押し出し穴)
穴フランジの形が多く、ねじを加工する穴フランジがよく見られます。
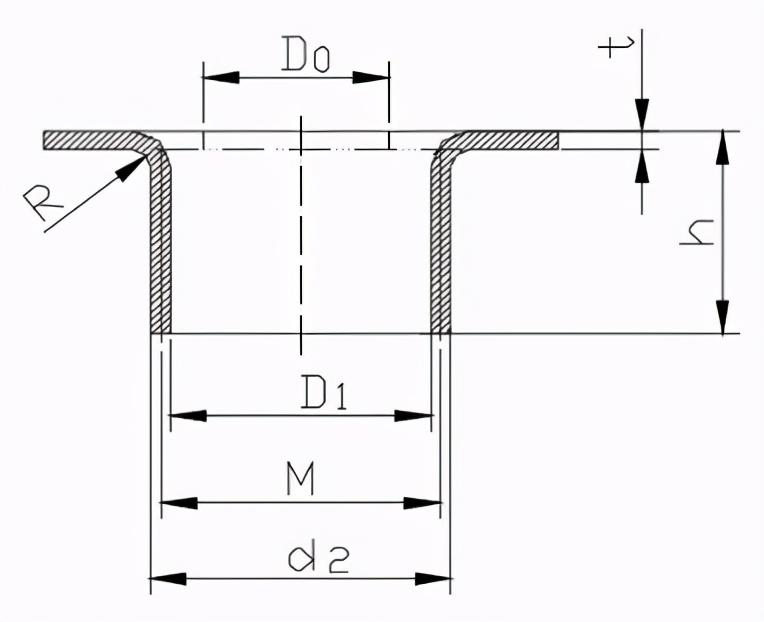
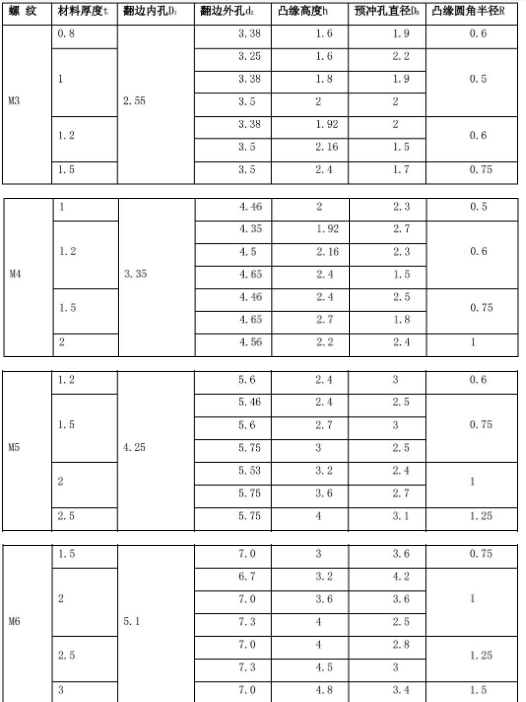
板金加工技術:リベットナット、リベットスタッド、リベットガイドスタッドなどの他の加工板金上の補助部品のリベット接合。
2.板金のねじ穴のタップ。
板金板厚t< ;1.5の場合、反りを用いて歯を攻める。板金厚t 1.5の場合は、直接パンチ歯を採用することができる。
板金加工技術--溶接板金溶接構造設計時には、「溶接ビード、溶接点を対称に配置し、交差、集積、重複を回避し、副次的な溶接ビード、溶接点は中断でき、主要な溶接ビード、溶接点は接続すべき」を貫徹すべきである。
板金にはアーク溶接、抵抗溶接などがよく使われている。
アーク溶接板金間には十分な溶接空間が必要であり、溶接隙間は最大で0.5~0.8 mmであり、溶接ビードは均一に平らでなければならない。
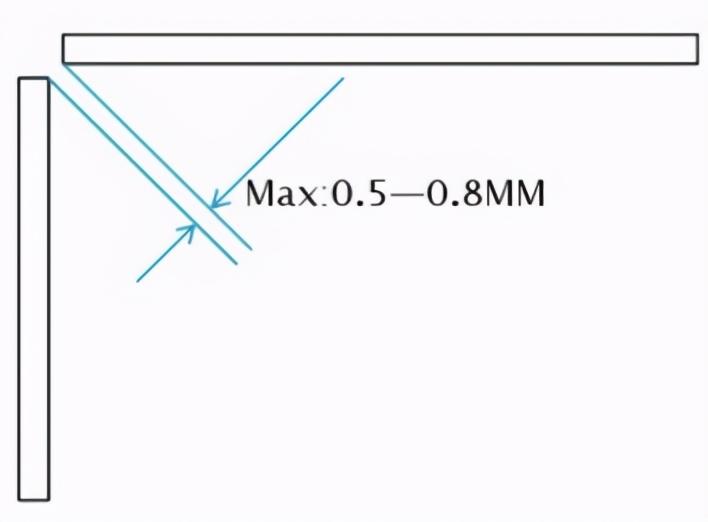
2.抵抗溶接面は平らで、皺、反発などがないことを要求する。
抵抗溶接の寸法は次の表の通りである:
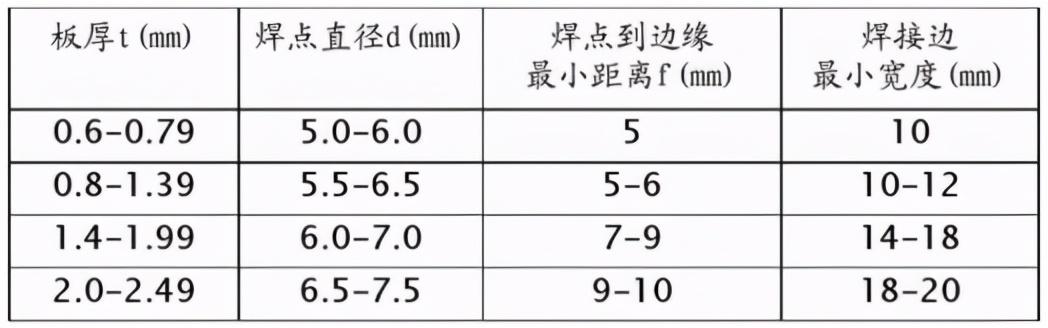
抵抗溶接点間隔
実際の用途では、小さな部品を溶接する際に、次の表のデータを参照することができます。
大型部品を溶接する場合、スポット間距離は適切に大きくすることができ、一般的には40-50 mm以上、非受力部位ではなく、溶接スポット間距離は70-80 mmに拡大することができる。
板厚t、溶接点直径d、最小溶接点直径dmin、溶接点間の最小距離eは、板材が異なる厚さの組み合わせであれば、最も薄い板で選択する。
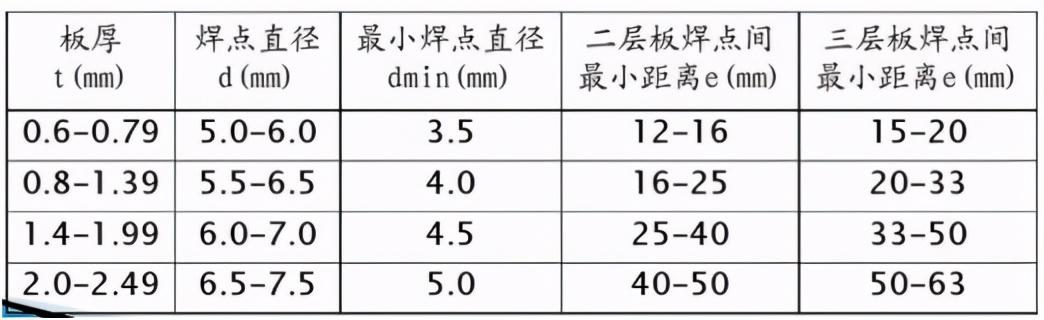
抵抗溶接板材の層数及び肉厚比
抵抗点溶接の板材は一般的に2層、最大3層であり、溶接ヘッド各層の板材厚さ比は1/3〜3の間にあるべきである。
3層板の溶接が必要であれば、まず材料厚比を検査しなければならない。もし合理的に溶接できるならば、もし合理的でなければ、開プロセス穴またはプロセス切欠き、2層溶接、溶接点をずらすことを考慮しなければならない。
板金加工技術--接続方法ここでは主に板金の加工過程における接続方法を紹介し、主にリベットリベット、溶接(上述)、パンチリベット、TOXリベットがある。
リベットリベットリベット:このリベットはよくリベットと呼ばれ、2枚の板材をリベットリベットによって一緒にリベットと呼ばれ、よく見られるリベット形状は図のように:
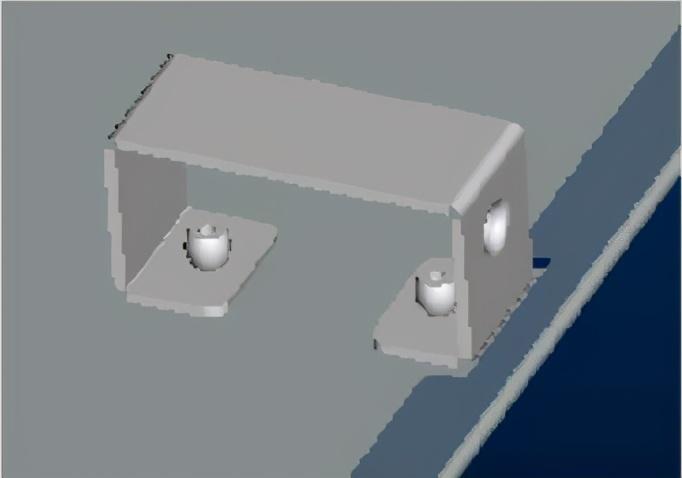
2.溶接(前に述べた)3.引抜きリベット:そのうちの1つは引抜き穴であり、もう1つは沈み穴であり、リベットタッチにより取り外し不可能な接続体にする。
優位性:パンチ穴とそれに合わせた沈み穴の自身は位置決め機能を持っている。かしめ強度が高く、金型によるかしめ効率も比較的高い。
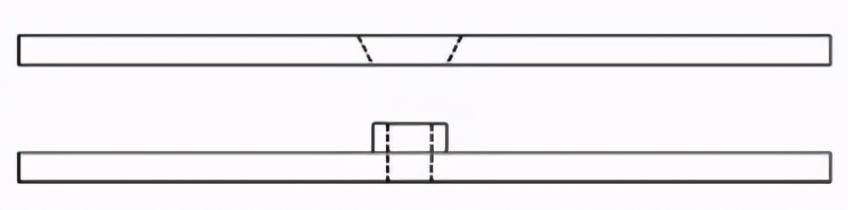
4.TOXリベット:簡単なポンチで被接続体をダイに押し込む。さらなる圧力作用の下で、ダイ内の材料が外へ「流動」する。その結果、角もなく、バリもない円接続点が生成され、しかもその耐食性に影響を与えず、表面にめっき層や塗装層がある板材でも同様に元の防錆防錆特性を保持することができ、めっき層と塗料層と板材も同様に元の防錆防錆特性を保持することができ、めっき層と塗料層もそれに伴って変形流動するためである。材料は両側に押し出され、ダイ側のプレートに押し込まれ、TOX接続点を形成する。次の図に示します。
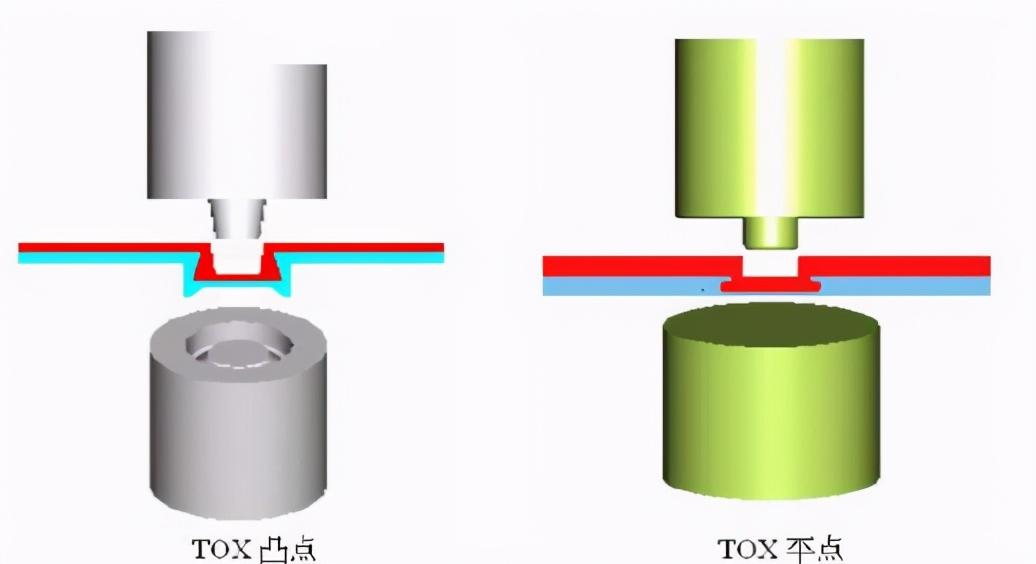
板金加工プロセス:表面処理は板金表面を処理することで防腐保護と装飾の役割を果たすことができる。板金によく見られる表面処理には、粉末溶射、電気亜鉛めっき、熱浸亜鉛、表面酸化、表面糸引き、シルク印刷などがある。
板金を表面処理する前に板金表面の油汚れ、さび、溶接スラグなどを除去しなければならない。
粉末塗装:板金の表面には液体と粉末塗料の2種類が塗装されており、私たちがよく使用するのは粉末塗料である。粉体噴射、静電吸着、高温焼成などの方式を通じて、板金の表面に様々な色の塗料を吹き付け、外観を美化し、材料の防食性エネルギーを高めることができる。は、一般的な表面処理方法です。
注:異なるメーカーがスプレーした色には多少の色差があるので、同じ設備の同じ色の板金はできるだけ同じメーカーでスプレーしなければならない。
2.電気亜鉛めっき、熱浸漬亜鉛板金の表面亜鉛めっきは常用の表面防食処理方法であり、一定の美化外観作用を果たすことができる。亜鉛めっきは電気亜鉛めっきと熱浸漬亜鉛に分けることができる。
電気亜鉛めっきの外観は比較的明るく平らで、亜鉛めっき層は薄く、比較的によく使われている。
熱浸漬亜鉛の亜鉛めっき層は厚く、鉄亜鉛合金層を生成することができ、耐食性は電気亜鉛めっきより優れている。
3.表面酸化:ここでは主にアルミニウムとアルミニウム合金の表面陽極酸化について紹介する。
アルミニウムとアルミニウム合金の表面陽極酸化は様々な色に酸化することができ、防護作用を果たし、また優れた装飾作用を果たすことができる。同時に材料の表面に陽極酸化膜を生成することができ、陽極酸化膜は比較的に高い硬度と耐摩耗性があり、また良好な電気絶縁性と断熱性がある。
4.表面糸引き:材料を糸引き機の上下ローラの間に置き、ローラにベルトが付着し、モータによって駆動され、材料を上下ベルトに通して、材料表面に一筋の痕跡を引き出し、ベルトによって痕跡の太さが異なり、主な役割は外観を美化することである。一般的にはアルミニウム材が糸を引く表面処理方式を考えている。
5.材料表面のシルク印刷に各種の標識を印刷する方法は、一般的には平板シルク印刷と転写の2つの方法があり、平板シルク印刷は主に一般平面上に用いられるが、深い凹みがある場所に遭遇すると、転写に用いる必要がある。
シルク印刷にはシルク印刷型が必要です。
板金加工精度参照付属品:
GBT 13914-2002プレス部品寸法公差
GBT 13915-2002-Tパンチ角度公差
GB-T 15005-2007プレス部品に公差限界偏差を付していない
GB-T 13916-2002パンチの形状と位置に公差がない
一般的な板金加工装置の能力一般的な板金加工装置の範囲
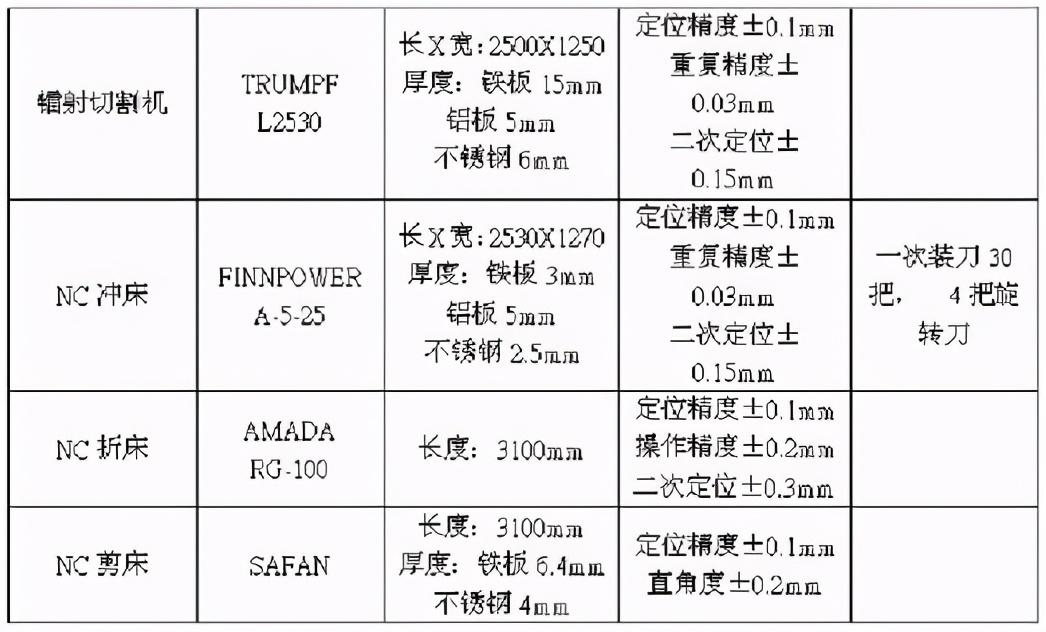