NC旋盤は高精度、高効率の自動化工作機械であり、NC旋盤を使用することによって加工効果を高め、より多くの価値を創造することができ、NC旋盤の出現によって企業はその立ち後れた加工技術NC旋盤加工技術から抜け出すことができた。通常の旋盤の加工技術と似ているが、NC旋盤は鉗子であるため、連続自動加工ですべての旋削工程を完成することができる。そのため、次の点に注意しなければなりません。
一、切削用量を合理的に選択する
高効率な金属切削加工には、被加工材料、切削工具、切削条件の3つの要素がある。これらは加工時間、工具寿命、加工品質を決定する。経済的に有効な加工方式は必然的に合理的に切削条件を選択した。
切削条件の3要素:切削速度、送り量、切断深さは直接工具損傷を引き起こす。切削速度の向上に伴い刃先温度が上昇し、機械的、化学的、熱的摩耗が発生する。切削速度が20%上昇すると、工具寿命は1/2減少します。
送り条件と工具後摩耗との関係は非常に小さい範囲で発生する。しかし、送り量が多く、切削温度が上昇し、後面の摩耗が大きい。切削速度は工具の影響より小さい。切断深さが工具に与える影響は、切削速度や送り量は大きくないが、マイクロ切断深さで切削すると、被切削材に硬化層が生じ、同様に工具の寿命に影響を与える。
ユーザーは加工された材料、硬度、切削状態、材料の種類、送り量、切り込みなどに基づいて使用する切削速度を選択する。
適切な加工条件を選択するには、これらの要素に基づいて選択します。規則的に安定した摩耗が寿命に達することが理想的な条件である。
しかし、実際の作業において、工具寿命の選択は工具摩耗、加工寸法の変化、表面品質、切削ノイズ、加工熱などと関係がある。加工条件を決定する際には、実際の状況に応じて検討する必要がある。ステンレスや耐熱合金などの難加工材料には、冷媒や剛性の良い刃を使用することができる。
二、工具を合理的に選択する
1.粗車の場合、強度が高く、耐久性に優れた工具を選択し、粗車の場合、大背刃量、大送り量の要求を満たす。
2.精車を使用する場合、加工精度を保証するためには、精度が高く、耐久性に優れた工具を選択しなければならない。
3.交換時間を短縮し、ナイフを使いやすくするためには、できるだけペンチとペンチを使用しなければならない。
三、治具を合理的に選択する
1.できるだけ汎用治具を選択してワークを挟み、専用治具の採用を避ける。
2.部品の位置決め基準を重ね合わせ、位置決め誤差を減らす。
加工経路の決定
加工経路とは、デジタル制御工作機械の加工過程における工具の部品に対する運動軌跡と方向を指す。
1.加工精度と表面粗さの要求を満たすべきである、
2.加工ルートはできるだけ短くして、工具のアイドルストローク時間を減らすべきである。
加工ルートと加工残量の関連
現在、デジタル制御スピンドルが一般的に使用されていない条件下では、一般的に青色過残留が加えられており、特に鍛造、鋳造ハードコートを含む残量を通常スピンドルに配置するには加工が必要である。デジタルスピンディスクで加工しなければならないのであれば、プログラムを作る柔軟な配合に注意しなければならない。
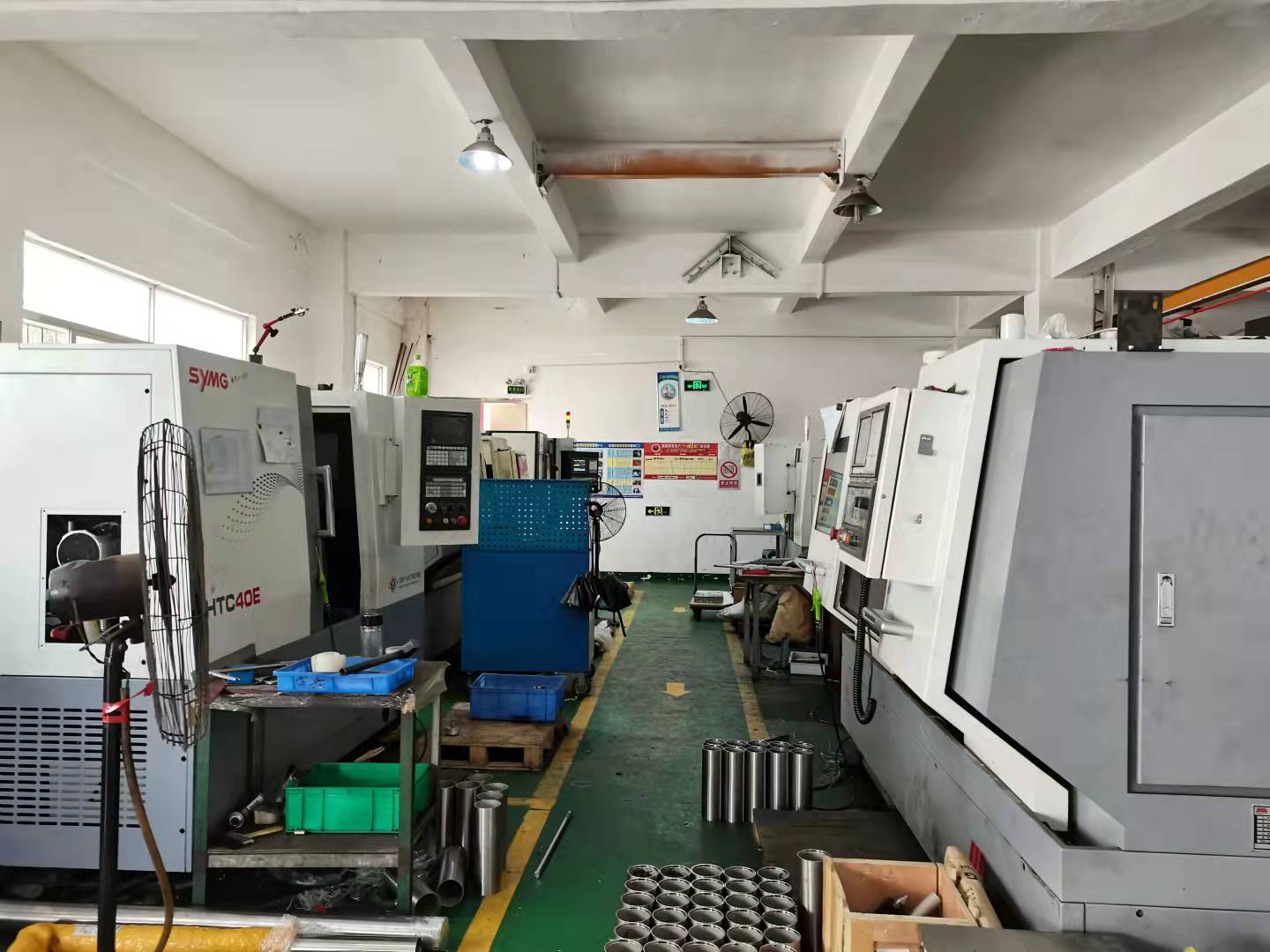