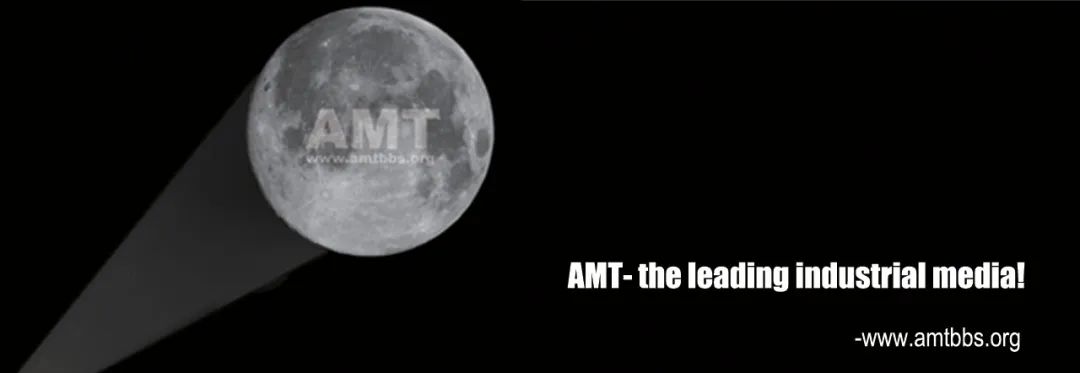
CNCプラグミリング加工により切削効率と工具寿命が大幅に向上
金属切削効率の向上における多くの重要な進展は、工具メーカー、工作機械メーカー、ソフトウェア開発者が共同で努力した結果である。プラグミリング(Z軸ミリング)加工が良い例です。インサートミリング加工時、回転した工具はZ軸方向に沿って直接下にワークに切り込み、Z軸方向に沿って上にリトラクトし、その後X軸またはY軸方向に距離を横に移動し、前回の切削部分と重なる垂直切削を行い、より多くのワーク材料を切削する。プラグミリング加工には多くのメリットがあります。特に、深型キャビティをミリングするなどの長いオーバーハング加工では、従来の平面ミリング方式(すなわちワークの片側から他方側へミリング)は、振動を引き起こす側方力をできるだけ小さくするために、切削速度を低下させなければならなかった。一方、プラグミリング時には、切削力が工作機械の主軸とテーブルに直接伝達されるため、従来のミリング方式よりもはるかに高い金属除去率を得ることができる。AMTソフトウェア社によると、同社が開発したProspector CAMパッケージにはプラグミリング機能が組み込まれており、ボタン型面フライスを用いた従来の平面粗ミリングに比べて、プラグミリング加工の金属除去率は少なくとも50%向上することができる。プラグミリングは、工作機械部品に作用する横荷重を最大限に低減することができるので、剛性が不足している旧式工作機械や軽量工作機械に使用することができ、生産性を向上させることができる。斗山工作機械のJohn Rossマーケティングマネージャーは、低性能工作機械に作用する切削力を減らすことができるという説に賛同したが、構造設計がプラグ加工に有利な新型工作機械では、この技術の優位性を最大限に発揮することができると付け加えた。彼は、プラグミリングの切削力が直接工作機械の主軸とテーブルに伝わるため、ワークのクランプがしっかりしていないことによる様々な問題を最小限に抑えることができると指摘した。インゲソル(Ingersoll)工具会社の金型生産ライン製品マネージャのBill Fiorenza氏によると、プラグミリングは工具やワークに入る切削熱を減らすのに役立つという。「インサートミリング加工の場合、ワークに入る熱はそれほど多くありません。カッターが回転するとワークに切り込みと切り出す速度が速いからです。移動ステップのごく一部のワークだけがカッターに接触しています」と述べた。ステンレス鋼、高温合金、チタン合金などの加工困難な材料を切削する場合、この特徴は特に優位性がある。Fiorenza氏はプラグミリングのデモを行った際、「通常、金属チップの温度は高く、チップの山の中でサンドイッチを焼くこともできます。しかし、プラグミリング加工が終わると、すぐに自分の手をワークに置くことができ、触ってみるとひんやりしています」と説明した。切削熱を減らすことは、工具の寿命を延ばすことができるほか、ワークの変形を最大限に減らすことができる。
【試してみる価値のあるプラグミリング加工】プラグミリングはハイエンド、複雑な部品の生産リズムを大幅に速めることができる。山高(Seco)工具会社ミリング製品マネージャーのGary Meyers氏は、「プラグミリング技術の最も応用されている分野は金型製造と航空工業である。これらの業界の部品タイプはプラグミリング加工に適しているからだ」と述べた。金型製造業者は、金型キャビティを形成するためにワーク全体に様々な複雑な形状をミリングする必要があり、多くの航空部品も全体のブランクで加工されている。彼は、「これらのワークの切削量は驚くほど大きく、場合によっては、ブランクから50%〜60%以上のワーク材料を切削する必要がある」と述べた。ESPRIT CAMソフトウェアの開発者であるDPテクノロジーズ製品マネージャのKenyon Whetsell氏は、複雑な部品メーカーのほかに、汎用型機械加工工場もプラグミリング技術を応用することで利益を得ることができると指摘した。金属加工の微信は、内容がよく、注目に値する。彼は、「一部の職場では2.5軸加工技術を使用しているが、それらの工作機械は型式が古く、剛性が悪く、治具の挟持力も不足しているが、生産性を向上させたいと考えている。これらの職場では2.5軸挿通フライス技術を利用してこの目的を達成することができる」と述べた。ケナー社の転位フライスグローバルプロダクトマネージャーのJuan Seculi氏は、「挿通フライス技術は大サイズと中サイズの部品の複雑な形状とキャビティ加工に広く適用されており、この加工ではフライスの長径比が重要であるが、伝統的なミリング戦略は振動と振動を発生させ、工具寿命を短縮する」と述べた。ユーザーの増加するニーズに対応するプラットフォーム。「Z軸インサートフライスの販売台数が増加し、年間成長率が40%に達していることが時間的に証明された」
【プラグフライスの設計特徴】工具メーカーはプラグフライス技術の優位性を十分に発揮できる各種プラグフライスを開発した。山高工具のMeyers氏によると、このような工具の切削力はほとんどZ軸に直接伝達されるという。プラグフライスの形状は90角肩フライスとよく似ている。異なる点は、プラグミリングブレードの前置角が垂直面から何度もずれていることであり、90ではなく87である可能性があることです。「90フライスで側壁を下に挿入すると、刃の切削刃全体が側壁と摩擦します。刃の前置角が87の場合、切削刃とワーク側壁の間に隙間があります。」切削刃は刃の底部の切削刃で切削し、底面から側面への移行部が刃の最も弱いところであり、刃の側面で加工すると振動を引き起こす半径方向の切削力が発生する可能性があるため、刃の側面で切削する必要があります。Meyers氏によると、刃の側面を用いて切削することはあまり見られないが、「上向き(または下向き)倣いフライス」と呼ばれる加工の中には、フライスは上向きと下向きのストロークの中で複雑な形状に加工することができるという。簡単な例としては、下ルートカット方式を用いて直側壁をミリング加工することが挙げられ、「まず下にミリングして、それから内に移動して、ワークピースの根元をミリングすることができます。」Meyers氏は、ミリング技術の限界は工具の実際の切削直径と工具本体の直径の差にあると考えている。切削刃にできるだけ大きな支持を提供するためには、標準面フライスの刃体を工具の切削直径全体にできるだけ近づけるように大きくする必要があります。インサートの切削直径は、倣いミリングに使用されるプラグミリングカッタのボディ直径を超えています。金属加工の微信は、内容がよく、注目に値する。彼は、「しかし、プラグミリングブレードの突出量はあまり大きくできないため、超過量には一定の制限がある」と述べた。Meyers氏は、プラグミリングは典型的な粗ミリング加工であるが、その技術は工具と同様に半仕上げ加工と仕上げ加工に適していると述べた。彼は、より良い加工表面仕上げを得るためには、ボールエンドミルで3次元仕上げミリングを行う場合に採用される減小ステップ加工方式と同じように、小径方向カッターの走行ステップを減らすべきだと提案した。Meyers氏は、本質的には、カッターステップはブレード幅と切削刃のワーク材料への切り込み量に基づいて決定されると説明している。工具製品サンプルが推奨するステップサイズは、特定のプラグフライスの加工表面粗さを決定する一定の残留高さを生成します。
ケナ金属のSeculi社によると、プラグフライスの設計は改善されつつあるという。例えば、ケナーZ軸挿入フライスの新しい特徴は以下を含む:刃体上に設計されたジグザグ構造は屑形成と屑排出性能を高めることができ、冷却液出口の設計は切削熱の制御と屑排出性能を改善することができる。「これらと刃体と一体化した構造設計は、大正前角を採用した前刃面と結合することで、切削力を低減し、工作機械の電力要求を低減することができ、それによって工具の寿命を延長し、加工信頼性を高めることができる」と述べた。
【CAMプラグミリングのプログラミングに考慮すべき要素】Fiorenza氏によると、プラグミリング技術の応用は少なくとも15年の歴史があるが、近年、加工現場ではプラグミリングがより高い材料除去率を得ることができ、しかもパスのプログラミングと検証が容易になるため、プラグミリング加工の応用も過去より容易になることがますますはっきりと認識されている。プラグミリング加工に特化したアルゴリズムを持つCAMシステムが増えている。また、切削シミュレーションソフトウェアを利用して、加工現場はプラグミリングサイクルプログラムを実行する前に、その信頼性を検証することができる。Fiorenza氏は、「専用カッターは通常中心カッターではないので、カッターの走行経路に沿った動きを検証する必要があります」と話しています。非中心カッターを使用する場合、選択した走行距離が適切でなかったり、ワークの加工マージンが不明だったりすると、打刀になる可能性があります。Meyersによると、一部の作業場ではNC加工におけるG 81ドリルサイクルプログラムを用いてプラグミリング加工を実行している。しかし、このような加工では、フライスが下から挿入されて戻ってくると、そのブレードがワークの側壁と擦れてしまう可能性があります。この問題を解決するために、専用に作成されたCAMプラグミリングサイクルプログラムは、工具が下挿底部に到達し、リトラクトがストローク頂点に戻る準備をする前に、X軸またはY軸方向に0.025-0.050 mm移動します。工具の後方移動により、リトラクト時に刃が加工された表面と擦れないようにすることができます。Meyers氏は、「手動でプラグミリングサイクルプログラムを作成することもできます。場合によっては、同じ深さの単純なプラグミリングであれば、X軸またはY軸での工具の動きを特定するためのサブプログラムだけを作成することができます。しかし、手動プログラミングの作業量は大きく、加工コードを作成する必要がある場合と作成する必要がない場合にのみ使用することができます」と述べた。DP技術会社のWhetsell氏は、「プラグミリング加工サイクルを最適化して、各切削におけるプラグミリング工具の最大の潜在力を十分に発揮させ、できるだけ多くの工具材料を切除することができます。プログラミングパラメータを決定するには、工具に対してワークの軸に切り込む必要があります切削走行毎に刃の切削能力を最大限に利用するために、切削量を動的に計算する。これには、ワーク素材と加工後の完成品部品のサイズを知る必要があります。」部品の最終寸法さえ分かれば、フライスのプラグミリング深さを決定することができ、ワークブランクの寸法が分かれば、どこからプラグミリングを開始するかを決定することができる。金属加工の微信は、内容がよく、注目に値する。Whetsell氏は、「これは基本的に今の段階で、以前プラグミリング加工が行われていたワーク素材のプログラミング情報です。DP社のESPRIT CAMソフトウェアでは、これを『ブランク自動プログラミング』と呼んでいます」と述べた。Whetsell氏は、「X軸またはY軸方向の切削後退刃のプログラミングは、工具をその後ろのワーク素材にちょうど後退させることができないため、工具を先ほどの切削によって発生した残留材料に後退させることも望んでいない」と述べた。CAMソフトウェアは、さまざまな方法でプラグミリング加工プログラムを作成することができる。Whetsell氏は、「例えば、送りピッチや半径方向の切断幅を定義せずに、残留高さ(例えば0.25 mm)を定義することができ、CAMソフトウェアはその残留高さを実現するプラグミリング回数を計算することができる」と述べた。DPテクノロジー社はESPRITソフトウェアのために専用のプラグミリング加工サイクルを開発しており、一部のユーザーはこのパッケージの先進的なプログラミングインタフェースを通じてプラグミリング加工プログラムを作成している。ケナー社のSeculiによると、プラグミリング加工に採用される切削パラメータと専門用語は他のミリング方法とは異なるという。例えば、ウォブリングを防止するために、プラグフライスのオーバーハングが長い場合には、より低い切削速度を採用する必要があります。プラグミリング加工を説明する際に、平面ミリングにおける軸方向の切削深さを表すために使用されるApの意味も変化しています。これは、垂直軸方向ではなくプラグミリングカッタの半径方向に位置しているためです。Z軸挿通ミリング加工では、軸方向の切削深さ寸法はなく、径方向の切削深さ(すなわち、パスステップ)と径方向の切削寸法しかありません。切削深さは通常、ブレードサイズに関係しています。ケナー社は、プラグミリング加工時には、刃の切削長さの15%よりも切削深さを常に維持することを提案している。切削深さがブレードの刃先円弧半径値に近づくか小さくなると、径方向切削力が増大し、プラグミリング技術の利点が失われます。
【プラグミリングと大送りミリング】プラグミリングは生産性の高い金属切削戦略である。この技術を採用するか、他のミリング戦略を採用するかを選択するかは、さまざまな要因に依存します。プラグミリングの利点を最大限に引き出すためには、専用プラグミリングカッターを使用してCAMプログラミングを入念に行う必要があります。多くの場合、大送りフライスはより簡便で容易な挿通フライスの代替案となり、大送りフライスは基本的に大前進角を持つ直刃フライスである。先端角を大きくして切り屑を薄くし、十分な切り屑厚を保つためには送り率を高める必要がある。大送りフライスは、大送り率、小切込み量で金属材料を迅速に切除するとともに、工作機械や工具に作用する横荷重を最小にすることができます。インゲソル工具会社のMAXline製品マネージャTom Noble氏は、部品の特徴的な寸法と構造は、加工現場がプラグミリングを採用すべきか、大送りミリングを採用すべきかを決定するのに役立つと考えている。彼は、「小さな凹部を加工する必要がある場合は、プラグミリングを使用するのが適切かもしれない。径方向移動距離が短いため、径方向ミリングに多くの材料を使用する必要はない。しかし、ミリングが必要な面積がかなり大きい場合は、大送りミリングを使用した方が効率的かもしれない」と述べた。大送りミリングには横方向の負荷が存在することは確かだが、小切深、早送り、複数回送りを使用することで、最小にすることができる。同社のFiorenza氏は、直径50 mm以上のプラグフライスを用いたロングサスペンションプラグフライスは非常に有効である可能性があると指摘している。一方、大送りミリングは、小径ミリングカッターのロングオーバーハングミリングに適している可能性があります。彼は、「工具のオーバーハング長さが直径の4倍または6倍に増大すると、いくつかのタイプのウォブリングが発生し始めます。大送りフライスと0.38-0.50 mmの小切込み深さを採用してこれらの加工に対応することができます。全体的な硬質合金のシャンクやモジュラーカッターヘッドなどの耐振工具構造を採用する必要があるかもしれません」と述べた。ノーブルは、フライス方法を選択するための重要な考慮要素の1つとして、作業場の日常的な加工任務を考えている。キャビティミリング、直壁ミリング、溝ミリング、大量加工の場合は、専用プラグミリングを購入する投資をする必要があります。」
【適切なプラグミルの選択】汎用型工作機械は「1機で多用途」という利点があるが、生産性を最大限に高める(および変形を小さくする)ためには、専用工作機械を採用することがより良い選択であることが多い。縦型マシニングセンター(VMC)、横型ボーリングフライスなどを生産する斗山工作機械は、軽量タップセンターから金型重荷切削用の高速5軸マシニングセンターまでの各種工作機械を提供することができる。金属加工の微信は、内容がよく、注目に値する。マーケティングマネージャのJohn Ross氏によると、同社は異なる加工(さらには異なる地域)のために工作機械をカスタマイズすることができるという。例えば、直線ガイドを採用している機械もあれば、より丈夫な硬いレールを採用している機械もあります。「米国カリフォルニア州のいくつかの地域で主に軽量材料を切削する市場に参入したとき、直線レール工作機械はちょうど道に合っていた。しかし、中西部地域の航空材料と高温合金を加工する市場に参入したとき、ユーザーは大きな切削力に耐え、より強固で耐久性のある硬レール工作機械を必要とした。」直線レールを採用した高速金型加工工作機械は少量の工作物材料を迅速に切削する際に性能が優れ、プラグミリング技術を採用することで粗加工能力をさらに高めることができる。しかし、この工作機械の切粉荷重に耐える能力は、ハードレール工作機械には及ばない。Ross氏によると、斗山のマイナックスシリーズ縦型加工センターはプラグミリングの優位性を最大限に発揮できる加工プラットフォームであり、その剛性は斗山VMCの中で最も高いという。この工作機械のベースは全体鋳造を採用し、1500 mm 750 mmテーブルは大型金型や航空鋳物を加工することができる。斗山会社の応用エンジニアSteve Sigg氏は、「工作機械の主軸が太ければ大きいほど、ミリング能力が高くなる」と指摘した。重負荷切削の際、インコーネル合金やステンレス鋼などの難加工材料に対して効率的に粗ミリング加工を行うことができ、面フライスでこれらの材料に対して径方向加工効率が低い。工具のオーバーハング量が大きい場合、横方向ミリング力は過度の振動を引き起こし、プラグミリング加工もこの難題をうまく解決することができる。ちなみに、メーカーがプラグミリング加工に興味を持ち始めたもう一つの理由は、米国の製造業の復興に伴い、一部の金型加工任務が中国から米国に還流しつつあることだと述べた。
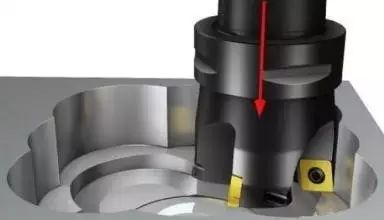