판금 가공 판금 가공은 금속 박판 (일반적으로 6mm 이하) 을 대상으로 하는 종합 냉가공 공정으로 절단, 재단, 벤드, 용접, 리벳 연결, 금형 성형 및 표면 처리 등을 포함한다.그 뚜렷한 특징은 같은 부품의 두께가 일치한다는 것이다.
판금 가공 방법: 비금형 가공: 수충, 레이저 절단, 오판기, 절곡기, 리벳기 등 설비를 통해 판금에 대한 공정 방식은 일반적으로 샘플 제작 또는 소량 생산에 사용되며 원가가 비교적 높다.가공 주기가 짧고 반응이 빠르다.금형 가공: 고정된 금형을 통해 판금을 가공하는데 일반적으로 원료 모형, 성형 모형이 있는데 주로 대량의 생산에 사용되고 원가가 비교적 낮다.전기 금형은 원가가 높고 부품의 품질이 보장된다.전기 가공 주기가 길고 금형 원가가 높다.판금 가공 절차: 재료: 충격, 레이저 절단, 절단기
형 - 벤드, 밀어내기, 펀치: 배관 절곡 기계, 프레스 등
기타 가공: 리벳 누르기, 공치 등
용접: 판금 연결 방법
표면처리: 분말, 전기도금, 지퍼, 실크인쇄 등
판금 가공 공정-원단 판금의 원단 방식은 주로 수충, 레이저 절단, 절단기, 금형 하부 재료 등이 있으며, 수치 제어는 현재 자주 사용하는 방식이며, 레이저 절단은 주로 샘플링 단계 (스테인리스강 판금 부품도 가공할 수 있음) 에 사용되며, 가공 비용이 높고, 금형 하부 재료는 대부분 대량 가공에 사용된다.
아래에 우리는 주로 수충으로 판금의 재료를 소개한다.
수충은 회전탑 수치 제어 프레스라고도 하는데, 재료, 펀치, 스트레칭 구멍, 롤링 리브, 블라인드 등에 사용할 수 있으며, 그 가공 정밀도는 +/-0.1mm에 달한다.
수치 제어 가공 가능한 판재 두께:
냉간 압연판, 열 압연판 4.0mm
알루미늄판 5.0mm
스테인리스 강판 2.0mm
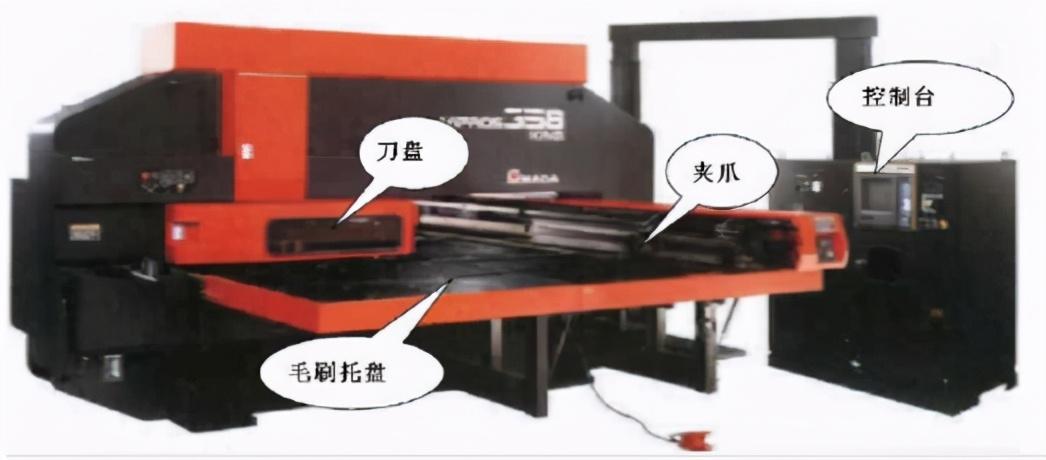
펀치에 최소 크기 요구사항이 있습니다.펀치의 최소 크기는 구멍의 모양, 재료 기계 성능 및 재료 두께와 관련이 있습니다.(아래 그림)
2. 펀치의 구멍 간격과 구멍 여백부품의 펀치 가장자리가 외형에서 가장 작은 거리가 부품 외형 가장자리와 평행하지 않을 경우 이 최소 거리는 재료 두께 t보다 작지 않아야 한다.평행일 때는 1.5t 이상이어야 합니다.(아래 그림)
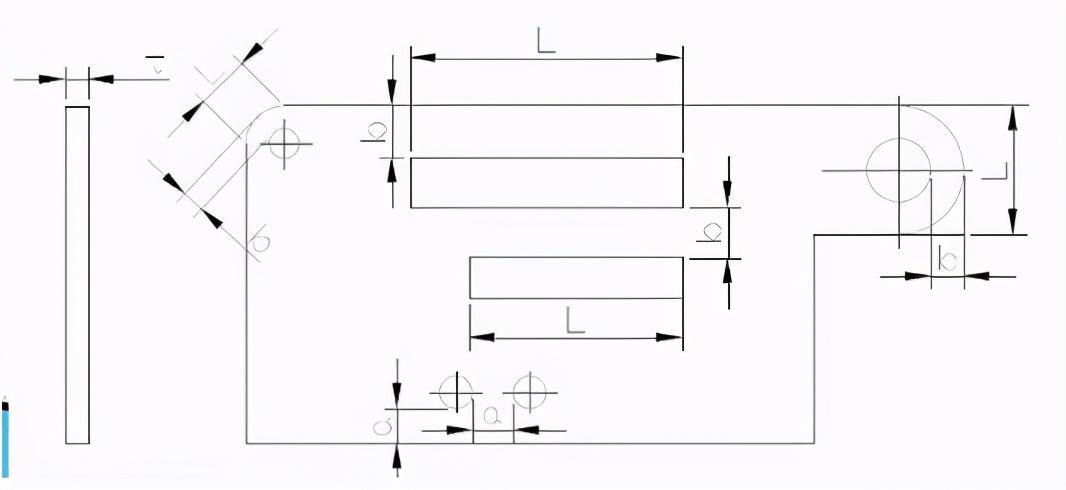
3. 구멍을 밀어낼 때 밀어낸 구멍은 모서리에서 최소 3T, 두 밀어낸 구멍 사이의 최소 거리는 6T, 밀어낸 구멍은 벤드 모서리 (안쪽) 에서 최소 안전거리 3T + R (T는 판금 두께, R은 벤드 필렛)
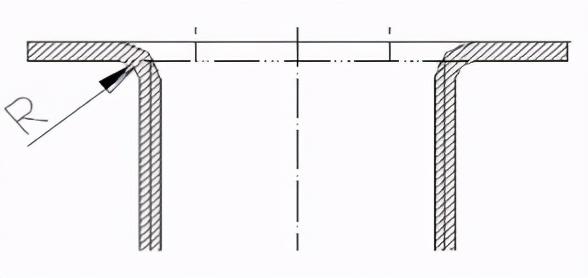
4. 벤드 부품을 밀어내고 펀치를 깊이 있게 할 때 해당 구멍 벽과 직선 벽 사이에 일정한 거리를 두어야 합니다.(아래 그림)
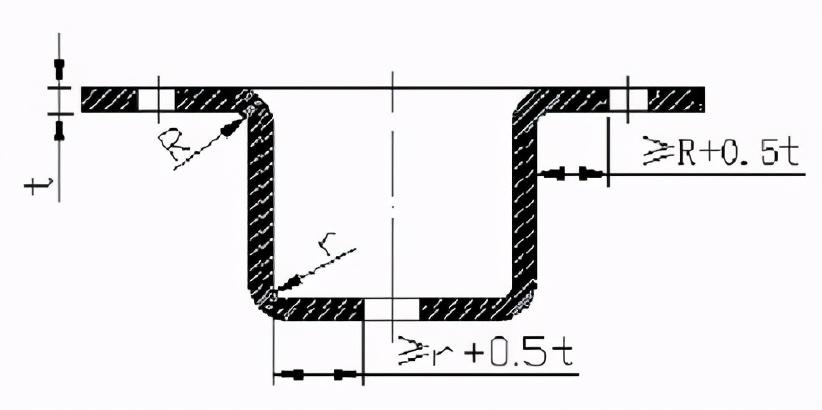
판금 가공 프로세스 - 성형 판금의 성형은 주로 판금의 벤드, 밀어내기입니다.
1. 판금 벤드 1.1 판금의 벤드는 주로 벤드 작업셀을 사용합니다.
접이식 침대의 가공 정밀도;
1절: +/- 0.1mm
20% 할인: +/- 0.2mm
20% 이상: +/- 0.3mm
1.2 벤드 가공 순서의 기본 원칙: 안에서 밖으로 벤드, 작은 것에서 큰 것으로 벤드, 먼저 특수 형태를 벤드, 전 공정이 성형된 후 후계 공정에 영향을 주거나 간섭하지 않는다.
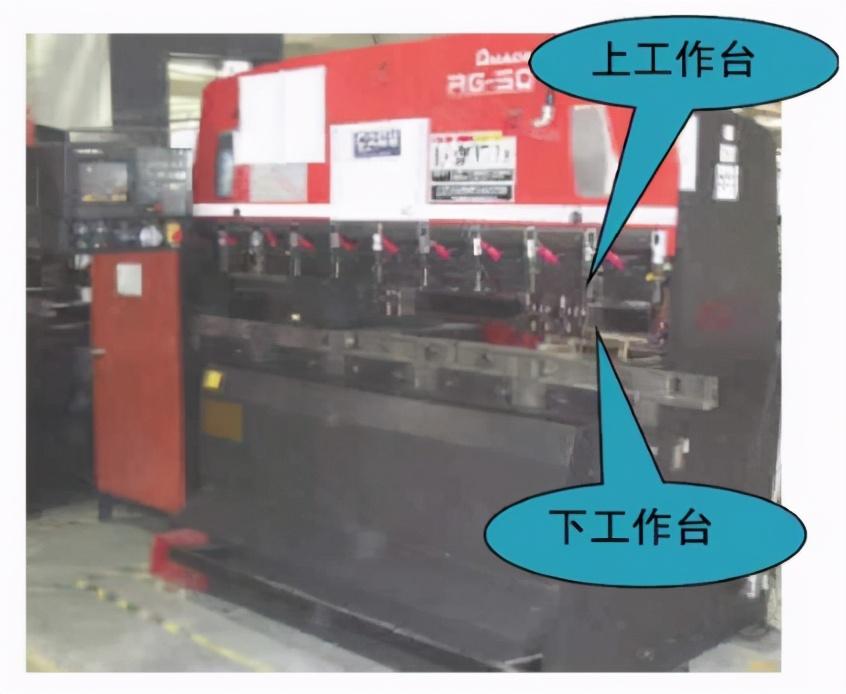
1.3 일반 엘보우 형태:
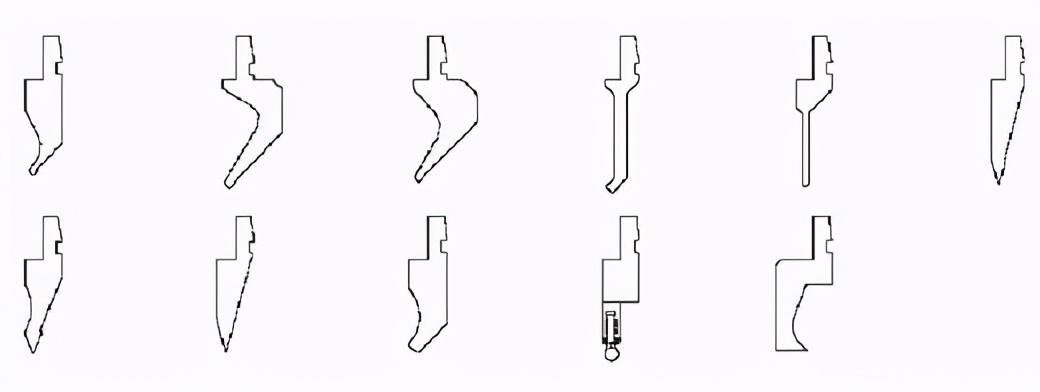
일반적인 V 슬롯 형태:
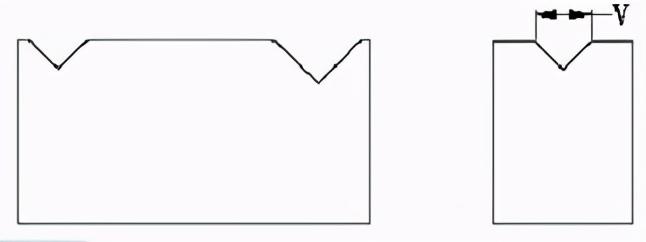
1.4 벤드 부품의 최소 벤드 반지름:
재료가 구부러지면 필렛 영역의 바깥쪽은 신축되고 안쪽은 압축됩니다.재료의 두께가 일정할 때 내부 r가 작을수록 재료의 신축과 압축은 더욱 심각해진다.외부 필렛의 신축 응력이 재료의 극한 강도를 초과하면 균열과 부러짐이 발생하므로 벤드 부품의 구조 설계는 벤드 필렛 반지름을 너무 작게 하지 않도록 해야 한다.회사 공통 재료의 최소 벤드 반지름은 다음 표를 참조하십시오.
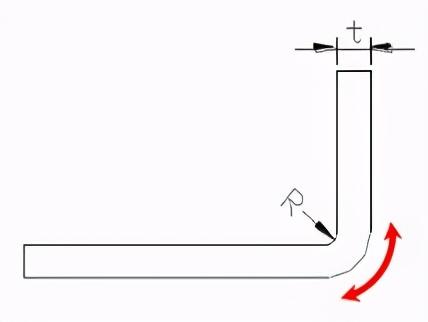
벤드 부품의 최소 벤드 반지름 테이블:
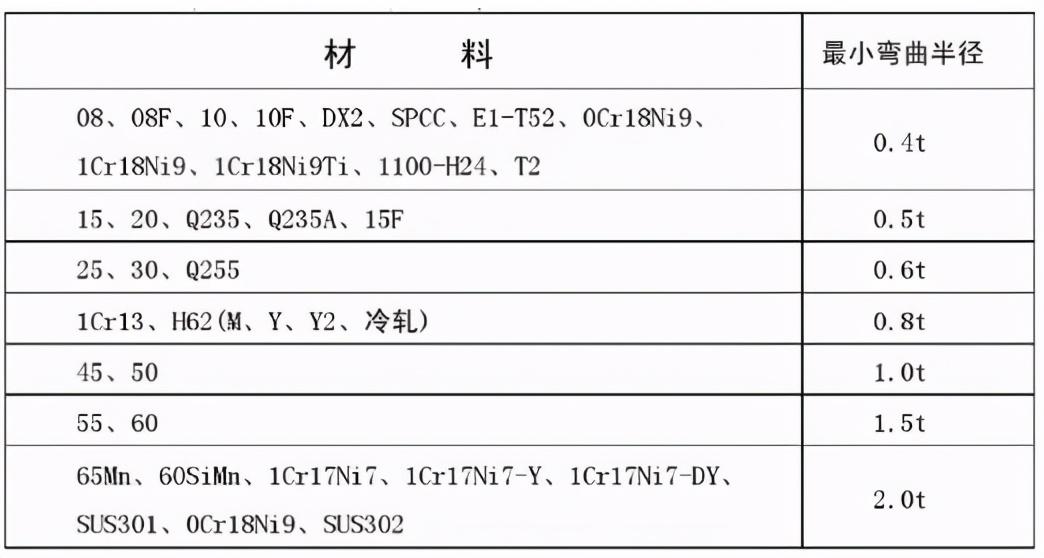
벤드 반지름은 벤드 부품의 내부 반지름을 의미하며 t는 재료의 벽 두께입니다.
1.5 벤드 부품의 직선 모서리 높이:
일반적인 상황에서 최소 직변 높이는 너무 작아서는 안 된다. 최소 높이 요구: h〉2t
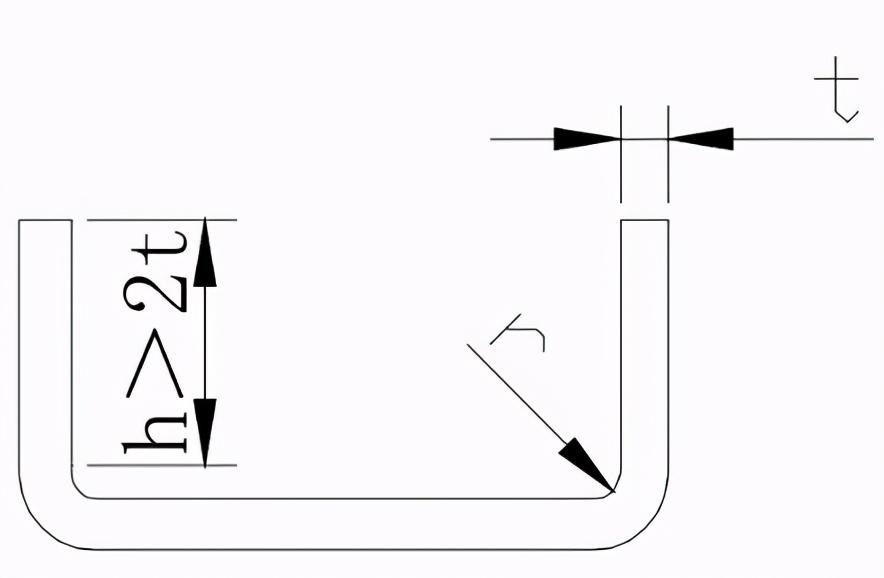
커브 부품의 직변 높이 h2t가 필요하면 먼저 커브 높이를 높이고 구부린 후 필요한 크기로 가공한다.또는 벤드 변형 영역 내에서 얕은 슬롯을 가공한 후 벤드합니다.
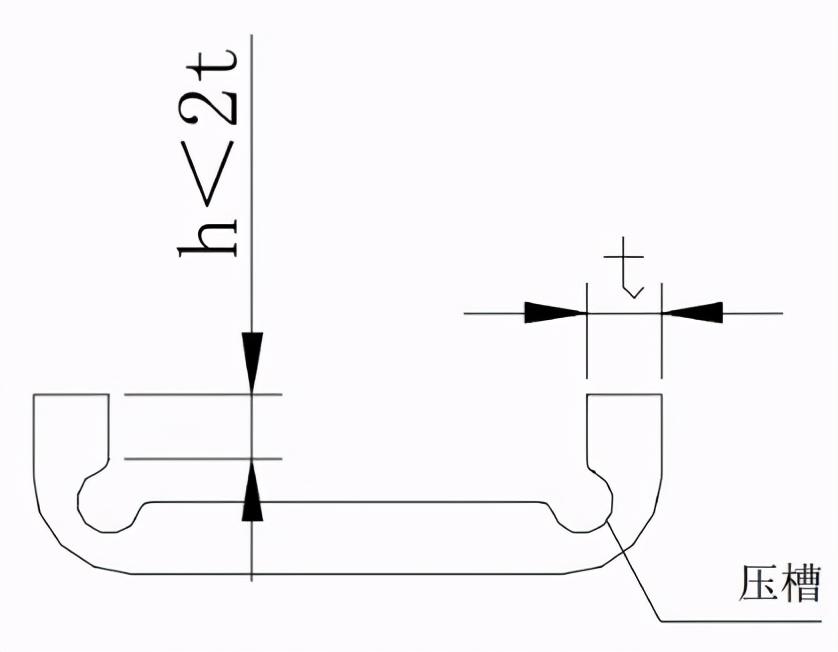
1.6 벤드 모서리 측면 모서리의 경사가 있는 최소 벤드 직선 모서리 높이:
구부러진 측면 모서리에 경사가 있는 구부러진 부품이 있을 때 측면의 최소 높이는 h=(2~4)t>3mm
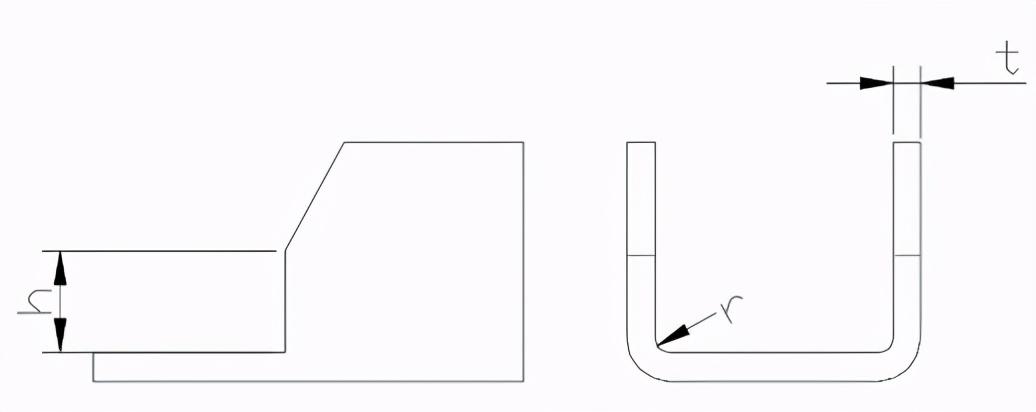
1.7 벤드 부품의 구멍 여백:
구멍 여백: 구멍을 먼저 뚫은 후 벤드해야 하며, 구멍의 위치는 벤드 변형 영역 밖에 있어야 하며, 벤드할 때 구멍이 변형되지 않도록 해야 합니다.구멍 벽에서 커브 모서리까지의 거리는 다음 표를 참조하십시오.
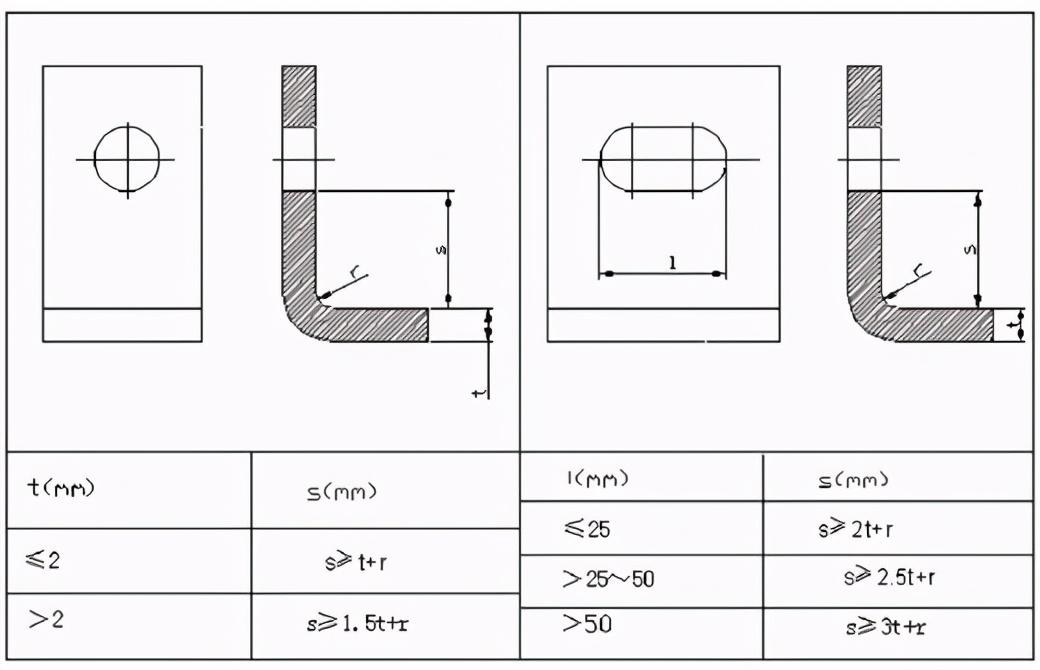
1.8 부분적으로 구부러진 프로세스 컷:
벤드 부품의 커브 선은 치수 돌연변이의 위치를 피해야 합니다.모서리를 부분적으로 구부릴 때 뾰족한 각도의 응력이 집중적으로 구부러지는 것을 방지하기 위해 구부린 선을 일정한 거리로 이동하여 치수가 돌변한 곳 (그림 a) 을 벗어나거나 공정 슬롯 (그림 b) 을 열거나 공정 구멍 (그림 c) 을 뚫을 수 있다.그림의 크기 요구 사항: SR,슬롯 너비kt;슬롯 깊이 Lt+R+k/2.
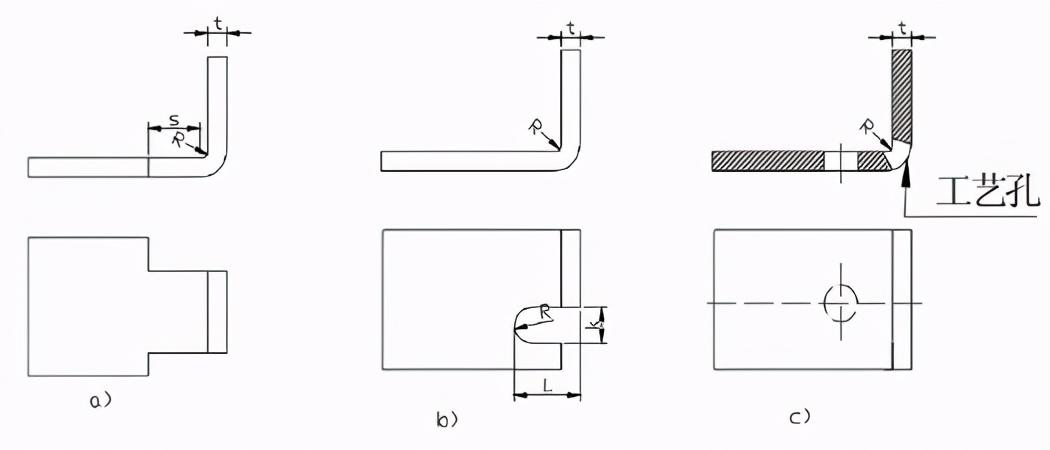
1.9 경사가 있는 벤드 모서리는 변형 영역을 피해야 합니다.
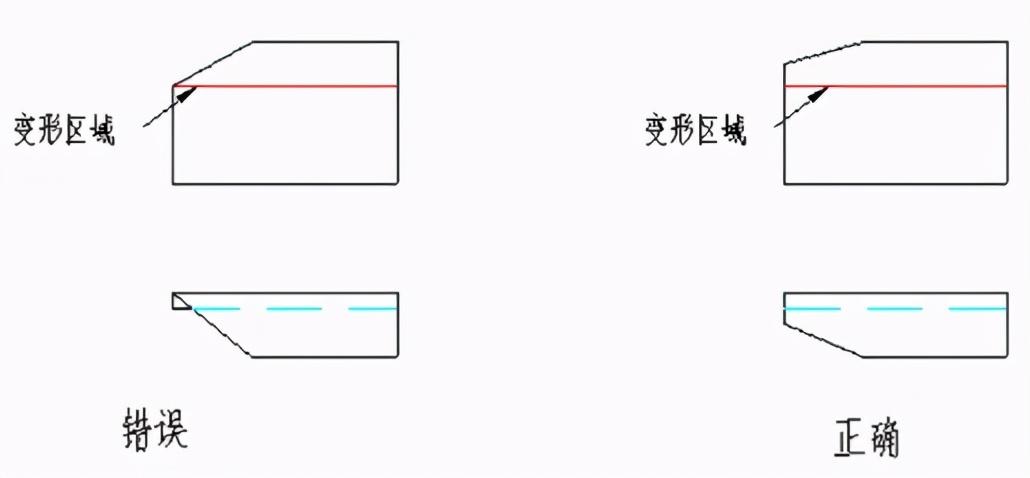
1.10 판금 플리츠 (패치 모서리) 설계 요구 사항:
판금 플리츠의 죽은 모서리 길이는 재료의 두께와 관련이 있습니다.다음 그림과 같이 일반적으로 데드 모서리의 최소 길이는 L3.5t+R입니다.
여기서 t는 재료 벽 두께이고 R은 다음 그림 오른쪽에 표시된 것처럼 모서리를 때려 죽이기 전 공정의 최소 내부 벤드 반지름입니다.

1.11 추가된 프로세스 배치 구멍:
다음 그림과 같이 몰드에서 스톡을 정확하게 배치하고 구부릴 때 스톡이 오프셋되어 폐품이 발생하는 것을 방지하기 위해 미리 설계할 때 공정 위치 구멍을 추가해야 합니다.특히 여러 번 구부러져 성형된 부품은 모두 반드시 공정구멍을 위치확정기준으로 하여 루계 오차를 줄이고 제품의 품질을 보장해야 한다.
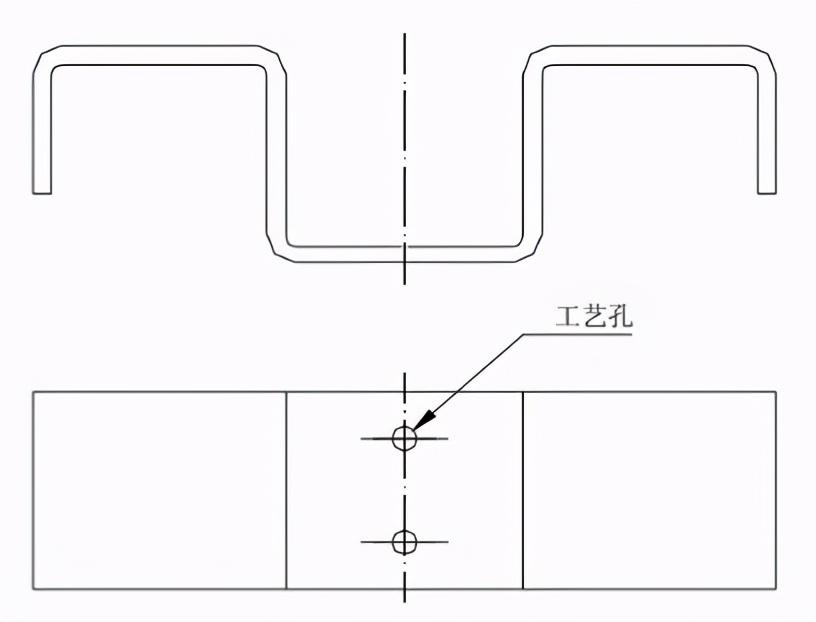
1.12 커브 관련 치수를 지정할 때 공정성을 고려해야 합니다.
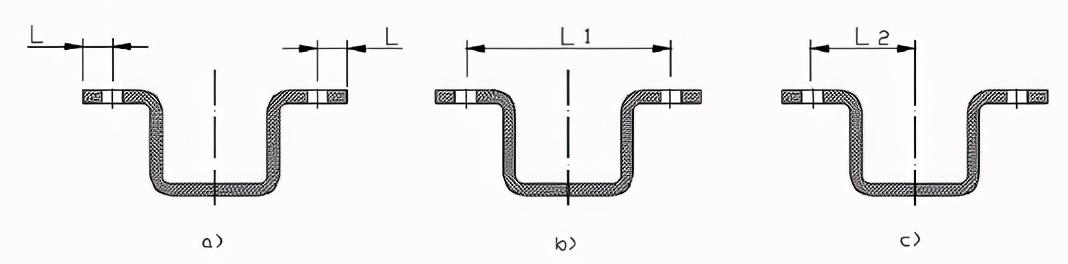
위 그림에서 볼 수 있듯이 a) 먼저 펀칭한 후 벤드하면 L 치수의 정밀도가 쉽게 보장되고 가공이 편리합니다.b) 및 c) 치수 L 정밀도가 높은 경우 먼저 벤드한 후 구멍을 가공해야 하므로 가공이 번거롭습니다.
1.13 커브 부품의 리턴은 재료의 기계적 성능, 벽 두께, 구부러진 반경 및 구부러졌을 때의 정압력 등 리턴에 영향을 주는 요소가 많다.벤드 부품의 내부 필렛 반지름이 보드 두께에 비해 클수록 리턴이 커집니다.설계에서 리턴을 억제하는 방법의 예로는 구부러진 부품의 리턴이 있는데, 현재 주로 생산 업체가 금형을 설계할 때 일정한 조치를 취하여 회피하고 있다.이와 동시에 설계면에서 일부 구조를 개진하여 회탄각을 다음과 같이 간소화하도록 해야 한다. 구부러진 구역에서 강화근을 압제하면 공작물의 강도를 높일수 있을뿐만아니라 회탄을 억제하는데도 유리하다.
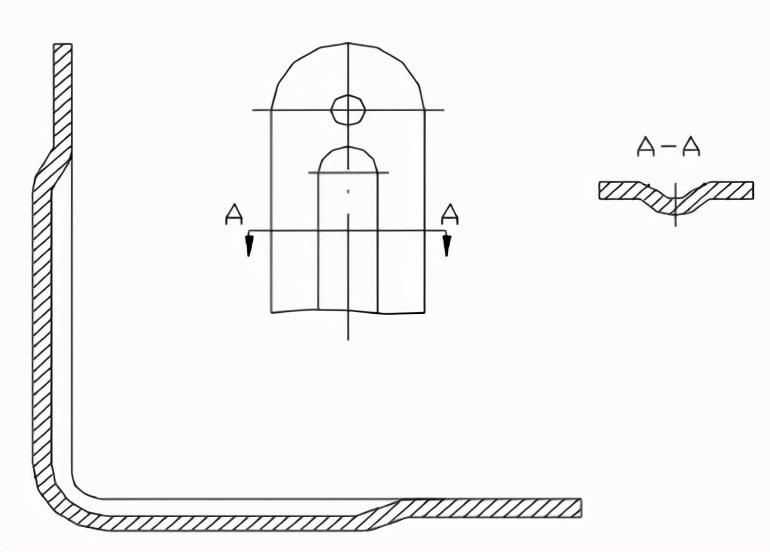
2. 판금 스트레칭 판금의 스트레칭은 주로 수치 제어 또는 일반 펀치로 이루어지며 다양한 스트레칭 헤드나 몰드가 필요합니다.
밀어낸 부품의 형태는 가능한 한 간단하고 대칭적이어야 하며, 가능한 한 한 번에 밀어내어 모양을 만들어야 한다.
여러 번 밀어내야 하는 부품은 밀어내는 동안 표면에 발생할 수 있는 흔적을 허용해야 합니다.
어셈블리 요구사항을 보장하기 위해 밀어낸 측면 벽의 기울기를 허용해야 합니다.
2.1 밀어낸 부품의 아래쪽과 직벽 사이의 필렛 반지름 크기 요구사항:
다음 그림과 같이 밀어낸 부품의 아래쪽과 직벽 사이의 필렛 반지름은 두께(r1t)보다 커야 합니다.스트레칭을 더 원활하게 하기 위해서는 일반적으로 r1=(3~5)t를 취하고 최대 원각 반경은 판두께의 8배, 즉 r18t보다 작거나 같아야 한다.
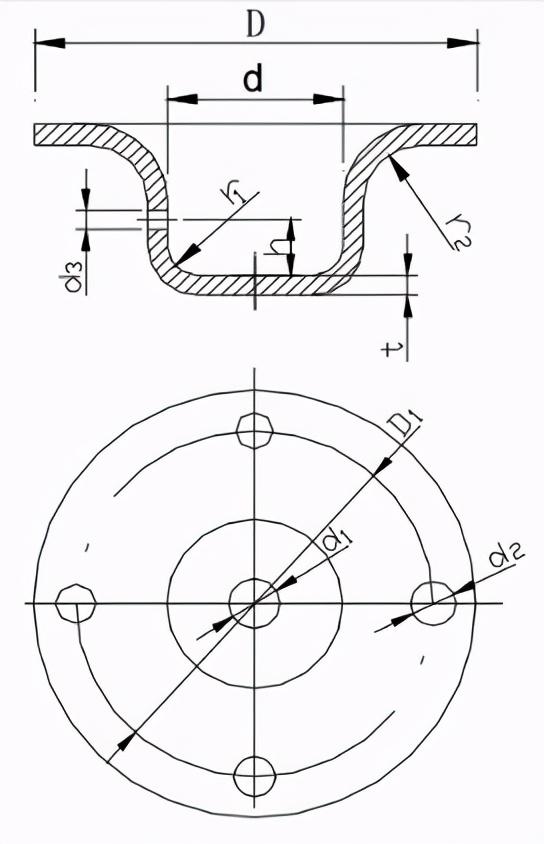
2.2 밀어낸 부분 플랜지와 벽 사이의 필렛 반지름
스트레치 부품 플랜지와 벽 사이의 필렛 반지름은 판 두께의 2배, 즉 r22t보다 커야 하며, 스트레치를 더 원활하게 하기 위해서는 일반적으로 r2=(5~10)t, 최대 플랜지 반지름은 판 두께의 8배, 즉 r28t보다 작거나 같아야 한다.(위 그림 참조)
2.3 원형 밀어내기의 캐비티 지름
원형 스트레치 부품의 내장 지름은 D d+10t를 취하여 스트레치할 때 압판이 눌려 구김이 생기지 않도록 해야 한다.(위 그림 참조)
2.4 직사각형 밀어내기 부품이 인접한 두 벽 사이의 필렛 반지름
직사각형 밀어내기 부품은 인접한 두 벽 사이의 필렛 반지름에서 r3 3t를 가져와야 하며, 한 번에 끌어낼 수 있도록 가능한 한 r3 H/5를 가져와야 합니다.
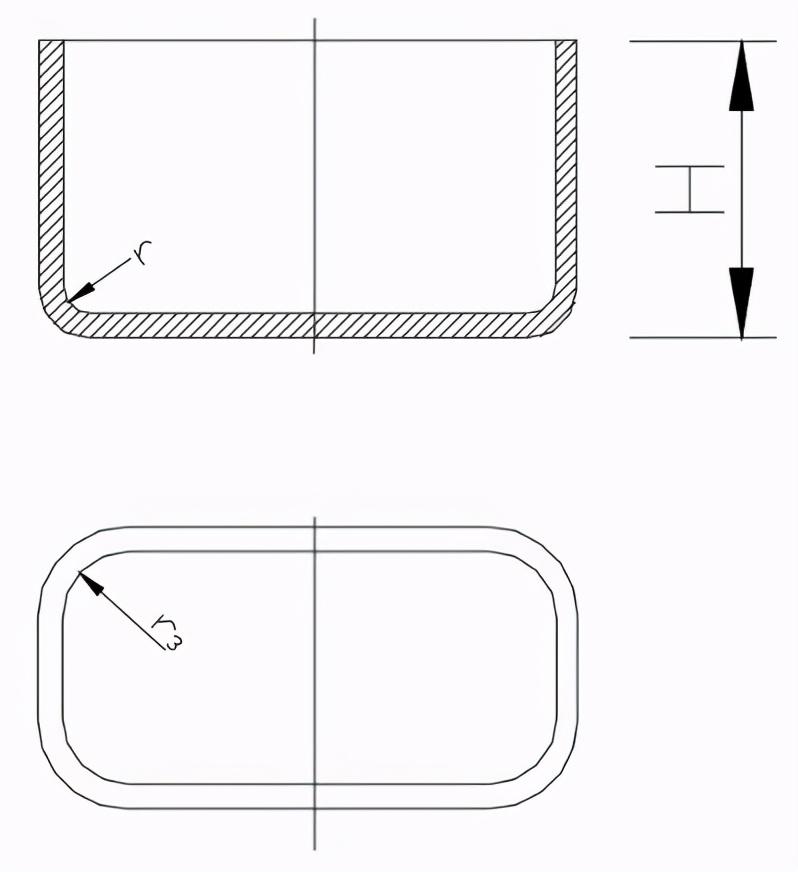
2.5 원형 비플랜지 밀어내기 부품이 한 번에 형성될 때 높이와 지름의 치수 관계 요구 사항
원형의 플랜지 없는 밀어낸 부품이 한 번에 형성될 때 다음 그림과 같이 높이 H와 지름 d의 비율은 0.4, 즉 H/d 0.4보다 작거나 같아야 합니다.
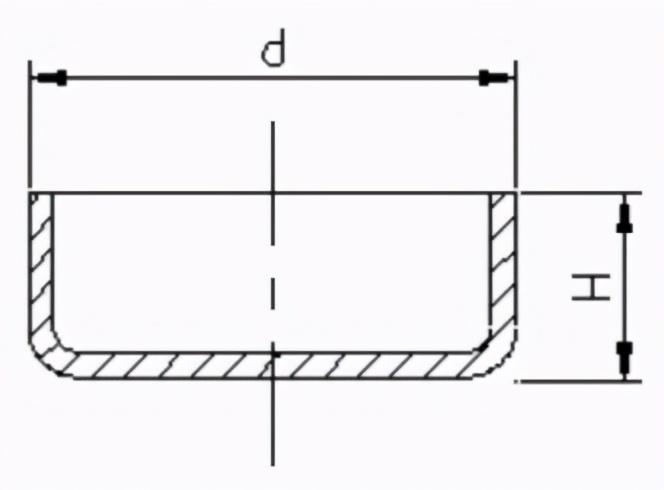
2.6 스트레치 재료의 두께 변화:
스트레치 부품은 각 곳에서 받는 응력의 크기가 다르기 때문에 스트레치된 재료의 두께가 변경됩니다.일반적으로 밑부분의 중앙은 원래의 두께를 유지하고 밑부분의 원각부분의 재료는 얇아지며 위쪽의 볼록가장자리에 가까운 재료는 두꺼워지고 직사각형의 신축부품 사방의 원각부분의 재료는 두꺼워진다.
2.7 스트레치 제품 치수 지정 방법
밀어낸 제품을 설계할 때는 외부 치수나 내부 치수를 보장해야 하며 내외부 치수를 동시에 표시할 수 없다는 점을 제품 다이어그램의 치수에 명시해야 합니다.
2.8 밀어낸 부품 치수 공차의 치수화 방법
스트레치 부품 범프 호의 내부 반지름 및 한 번에 형성된 원통형 스트레치 부품의 높이 치수 공차는 국가 표준 (GB) 16 레벨 정밀도 공차 절대값의 절반인 양면 대칭 편차입니다.
3. 판금 기타 성형: 리브 강화 - 판상 금속 부품에 리브를 눌러 구조의 강성을 높이는 데 도움이 된다.
블라인드 – 블라인드는 일반적으로 다양한 커버 또는 케이스에서 공기 흐름 및 냉각 기능을 수행하는 데 사용됩니다.
구멍 플립 모서리 (구멍 밀어내기) - 스레드를 가공하거나 구멍의 강성을 높이는 데 사용합니다.
3.1 강화 리브:
리브 구조 및 치수 선택 강화
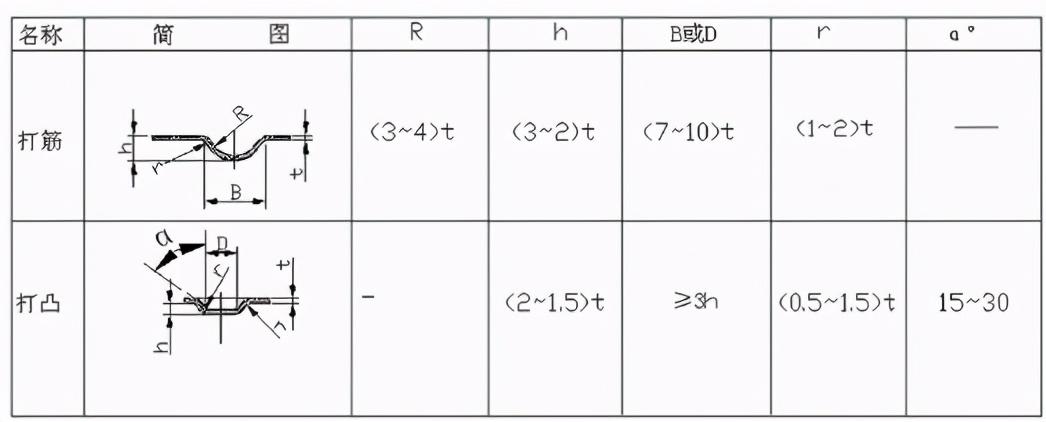
볼록 간격 및 볼록 여백의 한계 치수는 테이블을 눌러 선택합니다.
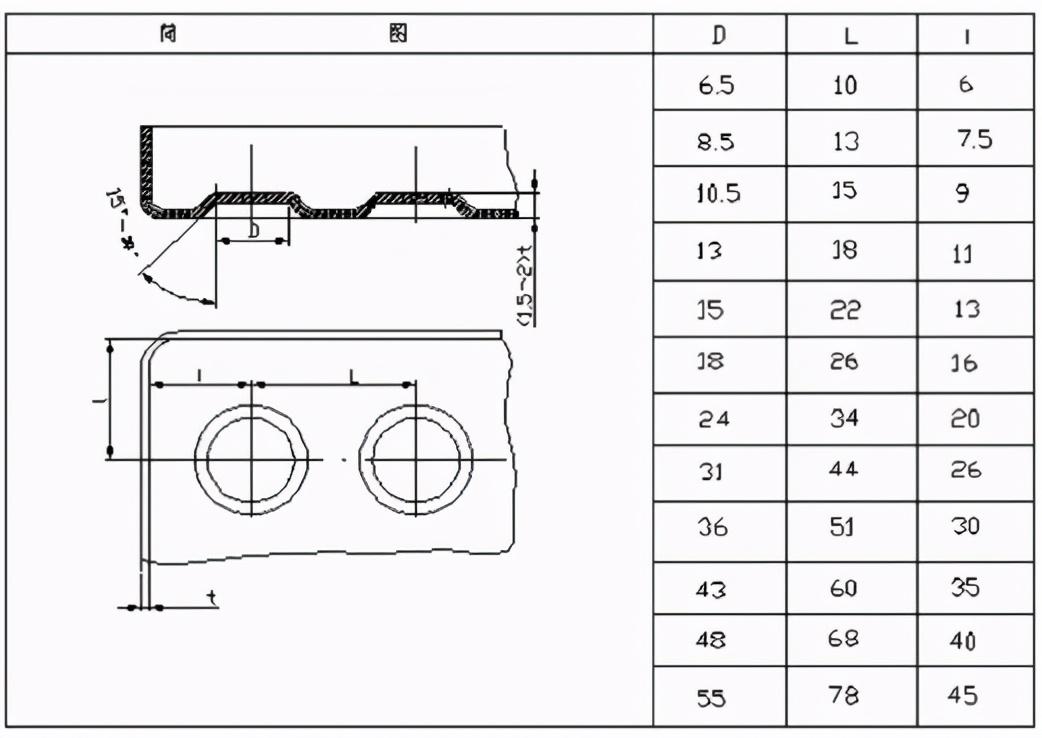
3.2 블라인드
블라인드 성형 방법은 펀치 형의 한쪽 칼날을 빌려 재료를 절개하고 펀치 형의 나머지 부분은 재료를 동시에 스트레칭하여 변형시켜 한쪽 입구의 기복 모양을 형성하는 것이다.
블라인드의 일반적인 구조는 다음 그림을 참조하십시오.
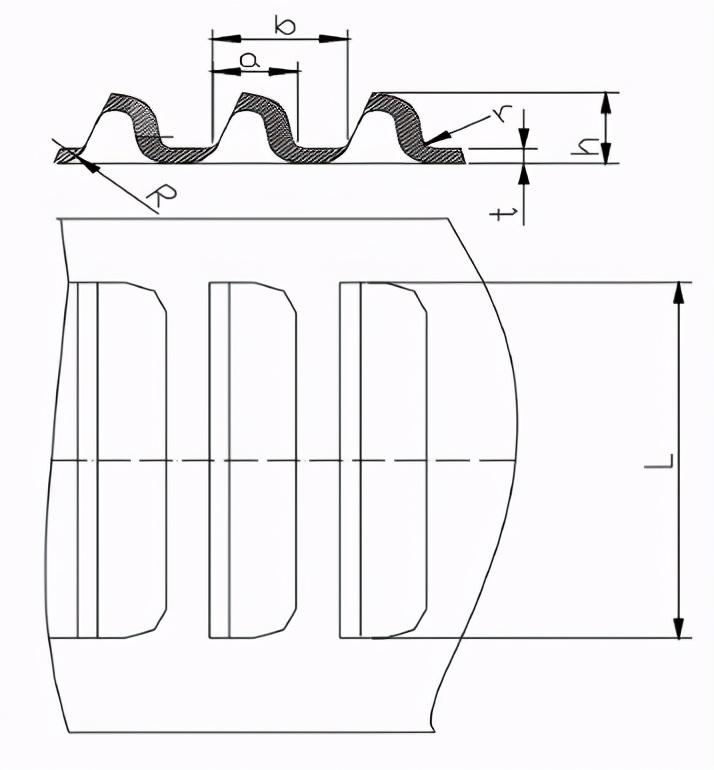
블라인드 크기 요구사항: a4t;b6t;h5t;L24t;r0.5t。
3.3 구멍 뒤집기 (밀어내기)
구멍 플립 형태가 비교적 많은데, 흔히 스레드를 가공할 내부 구멍 플립입니다.
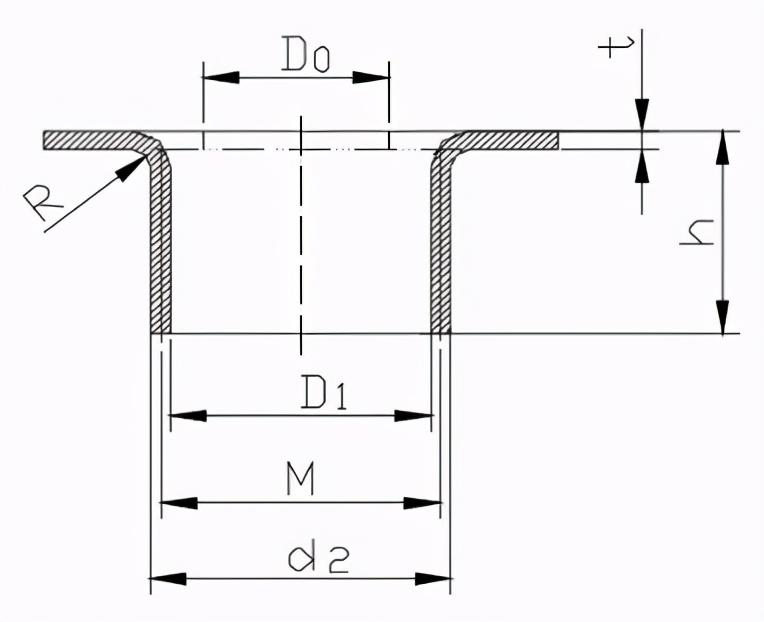
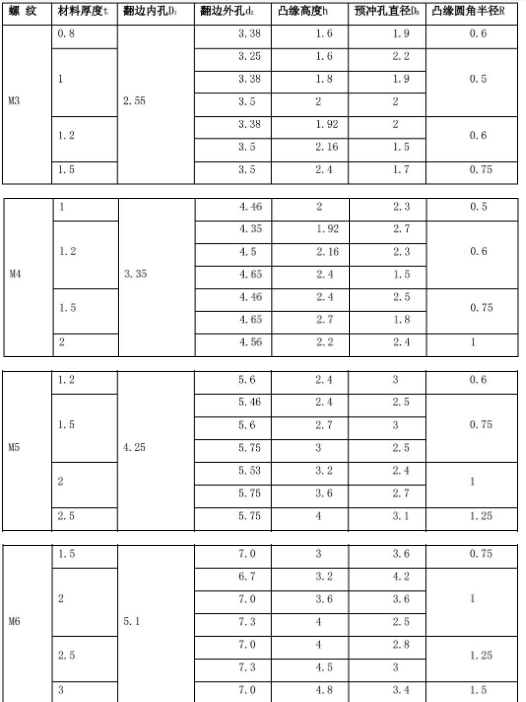
판금 가공 프로세스 - 리벳 너트, 리벳 나사, 리벳 가이드 기둥 등 다른 가공 판금 부품의 리벳 조인트.
2. 판금 위의 스레드 구멍의 공치.
판금 두께 t <;1.5시에는 가장자리를 뒤집고 이를 공격한다.판금 두께 t1.5의 경우 직접 공치를 사용할 수 있습니다.
판금 가공 프로세스 - 용접은 판금 용접 구조를 설계할 때 "대칭적으로 용접, 용접점을 배치하고 교차, 집결, 중첩을 피하며 부차적인 용접, 용접점은 중단할 수 있고 주요 용접, 용접점은 연결해야 한다."
판금에서 자주 사용하는 용접은 아크 용접, 저항 용접 등이 있다.
아크 용접 판금 사이에는 충분한 용접 공간이 있어야 하며, 용접 간격은 최대 0.5~0.8mm여야 하며, 용접봉은 균일하고 평평해야 한다.
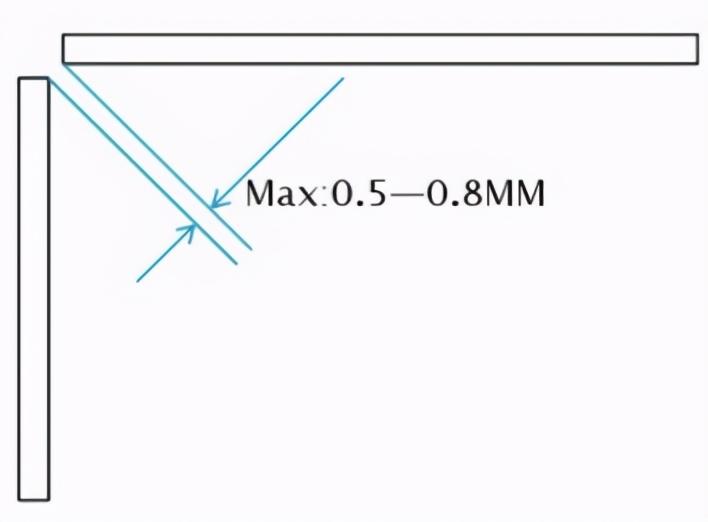
2. 저항용접면은 플랫하고 구김, 리턴 등이 없어야 한다.
저항 용접의 크기는 다음과 같습니다.
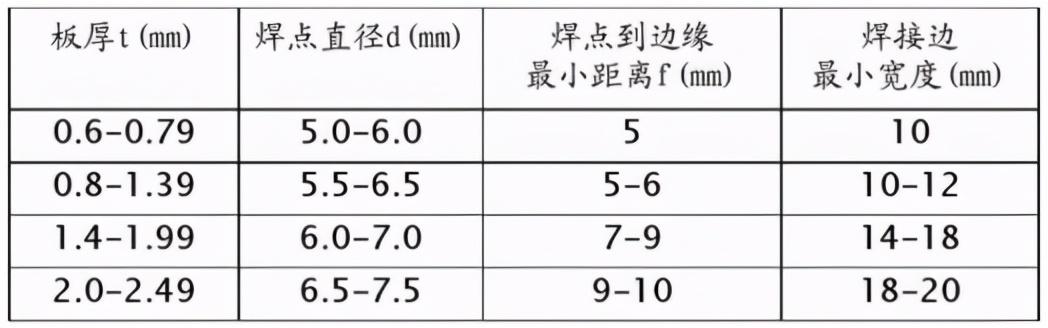
저항 용접점 간격
실제 응용 프로그램에서는 작은 부품을 용접할 때 다음 표 데이터를 참조할 수 있습니다.
큰 크기의 부품을 용접할 때 점거리는 적당히 커질수 있는데 일반적으로 40~50mm 이상이고 힘을 받지 않는 부위이며 용접점의 간격은 70~80mm로 확대될수 있다.
판두께 t, 용접점 지름 d, 최소 용접점 지름 dmin, 용접점 간의 최소 거리 e, 판재가 서로 다른 두께로 조합된 경우 가장 얇은 판으로 선택합니다.
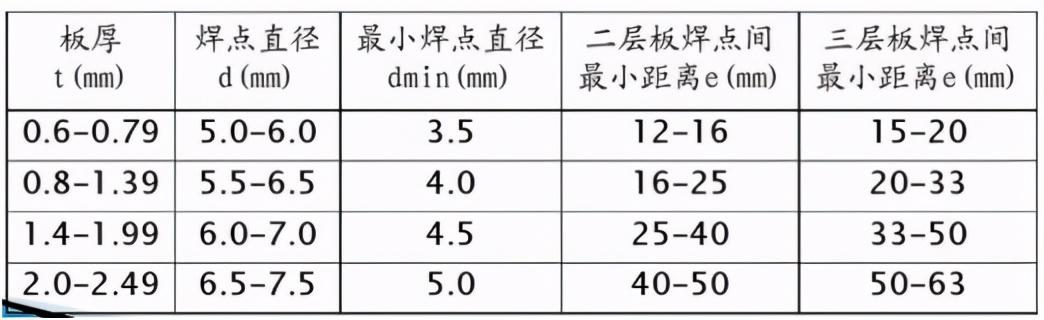
저항 용접판 재료 층수 및 재료 두께비
저항점 용접의 판재는 일반적으로 2층, 최대 3층이며, 용접 헤드 각 층의 판재 두께비는 1/3~3 사이여야 한다.
만약 3층판 용접이 확실히 필요하다면, 먼저 재료 두께비를 검사해야 한다. 만약 합리적으로 용접할 수 있다면, 만약 합리적이지 않다면, 공예 구멍을 열거나 공예 구멍을 열고, 2층 용접을 고려하고, 용접점을 어긋나게 열어야 한다.
판금 가공 공정-연결 방식 여기서 주로 판금이 가공 과정에서 연결되는 방식을 소개하는데 주로 리벳 리벳, 용접(위에서 설명한 바), 펀치 리벳, TOX 리벳이 있다.
리벳 리벳: 이런 리벳은 흔히 라못이라고 하는데 두 판재를 라못을 통해 리벳을 합친다고 하는데 흔히 리벳의 모양은 그림과 같다.
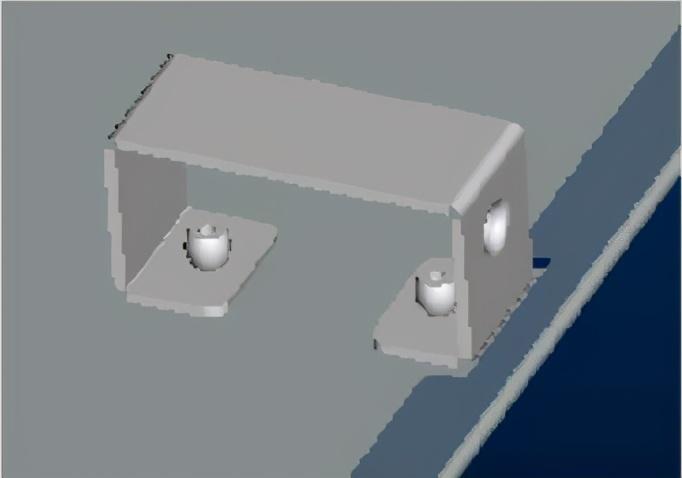
2.용접 (앞에서 설명한 바) 3.피팅 리벳: 그 중 하나는 피팅이고 다른 하나는 가라앉은 구멍입니다. 리벳을 통해 제거할 수 없는 연결체로 만듭니다.
우수성: 펀치와 그에 부합하는 카운터보어 자체는 포지셔닝 기능을 가지고 있다.리벳의 강도가 높고 금형을 통한 리벳의 효율도 비교적 높다.
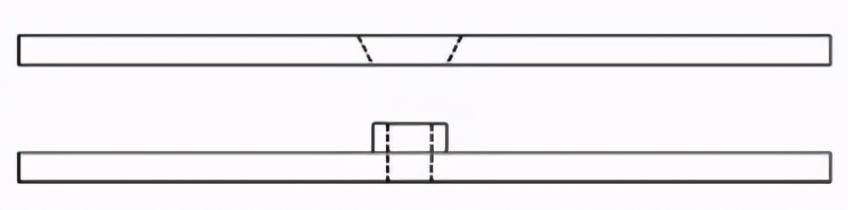
4. TOX 리벳: 간단한 펀치 형을 통해 연결 부품을 다이 형에 눌러 넣습니다.진일보한 압력작용하에서 오목모형내의 재료는 바깥쪽으로"유동"한다.그 결과 모서리도 없고 가시도 없는 둥근 연결점이 생겨나 부식성에 영향을 주지 않는다. 표면에 도금층이나 페인트층이 있는 판재도 마찬가지로 원래의 녹 방지 방부 특성을 보존할 수 있다. 도금층과 페인트층과 판재도 마찬가지로 원래의 녹 방지 방부 특성을 보존할 수 있기 때문이다. 도금층과 페인트층도 따라서 변형되어 흐르기 때문이다.재료가 양쪽으로 밀리면서 다이 면에 있는 판재에 밀어 넣어 TOX 연결 점이 형성됩니다.다음 그림과 같습니다.
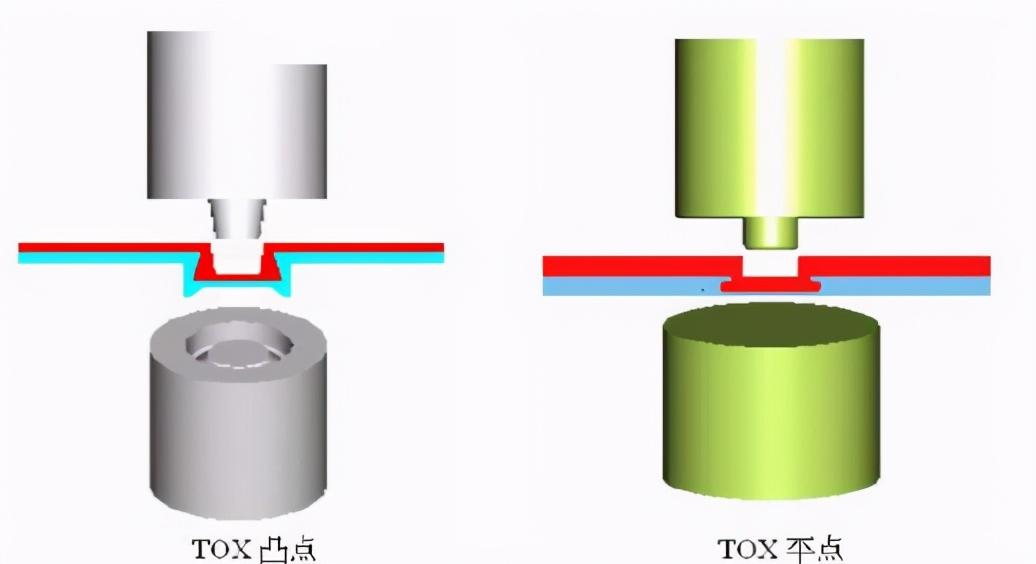
판금 가공 공정 - 판금 표면을 처리하면 방부 보호 및 장식 역할을 할 수 있습니다.판금에서 흔히 볼수 있는 표면처리에는 분말스프레이, 전기아연도금, 열침아연, 표면산화, 표면실크, 실크인쇄 등이 있다.
판금을 표면 처리하기 전에 판금 표면의 기름때, 녹, 용접 찌꺼기 등을 제거해야 한다.
분말 도료: 판금의 표면 도료는 액체와 분말 도료 두 가지가 있는데, 우리가 자주 사용하는 것은 분말 도료이다. 분말, 정전기 흡착, 고온 구이 등의 방식을 통해 판금 표면에 각종 색깔의 도료를 한 층 뿌려 외관을 미화하고 재료의 방부식 성능을 증가시킬 수 있다.일반적인 표면 처리 방식입니다.
주: 서로 다른 공장에서 도포한 색깔은 다소 일정한 색차가 존재하기 때문에 같은 설비의 같은 색깔의 판금은 가능한 한 같은 공장에서 도포해야 한다.
2. 전기도금, 열침아연판금의 표면도금은 흔히 사용하는 표면방부처리방법으로서 일정한 외관미화역할을 할수 있다.아연도금은 전기도금과 열침아연으로 나눌 수 있다.
전기아연도금의 외관은 비교적 밝고 평평하며 아연도금층이 비교적 얇아 비교적 자주 사용한다.
열침아연의 아연도금층은 비교적 두껍고 철아연합금층을 산생할수 있으며 부식방지능력이 전기아연도금보다 강하다.
3. 표면산화: 여기서 주로 알루미늄과 알루미늄합금의 표면양극산화를 소개한다.
알루미늄과 알루미늄합금의 표면 양극 산화는 여러 가지 색깔로 산화되어 보호 작용을 하고 좋은 장식 작용을 한다.동시에 재료의 표면에 양극산화막을 생성할 수 있으며, 양극산화막은 비교적 높은 경도와 내마모성을 가지고 있으며, 또한 양호한 전기절연성과 단열성을 가지고 있다.
4. 표면 지퍼: 재료를 지퍼의 상하 롤러 바퀴 사이에 놓고 롤러 바퀴에 모래띠가 부착되어 전기기계를 통해 움직이며 재료를 상하 모래띠를 통과하게 하고 재료 표면에 흔적을 하나 낸다. 모래띠에 따라 흔적의 굵기도 다르다. 주요 역할은 외관을 미화하는 것이다.일반적으로 모두 알루미늄 소재이기 때문에 실을 당기는 표면 처리 방식을 고려한다.
5. 견직물은 재료 표면의 견직물에 각종 표지를 찍는 공예이다. 일반적으로 평판 견직물과 이쇄 두 가지 방식이 있다. 평판 견직물은 주로 일반 평면에 사용되지만 비교적 깊은 움푹 패인 곳을 만나면 이쇄를 해야 한다.
실크 프린트에는 반드시 실크 프린트가 있어야 한다.
판금 가공 정밀도 참조 첨부:
GBT13914-2002 프레스 부품 크기 공차
GBT13915-2002-T 프레스 각도 공차
GB-T15005-2007 프레스 부재 공차 한계 편차
GB-T 13916-2002 펀치 형상 및 위치 공차
일반 판금 가공 설비의 능력 일반 판금 설비 가공 범위
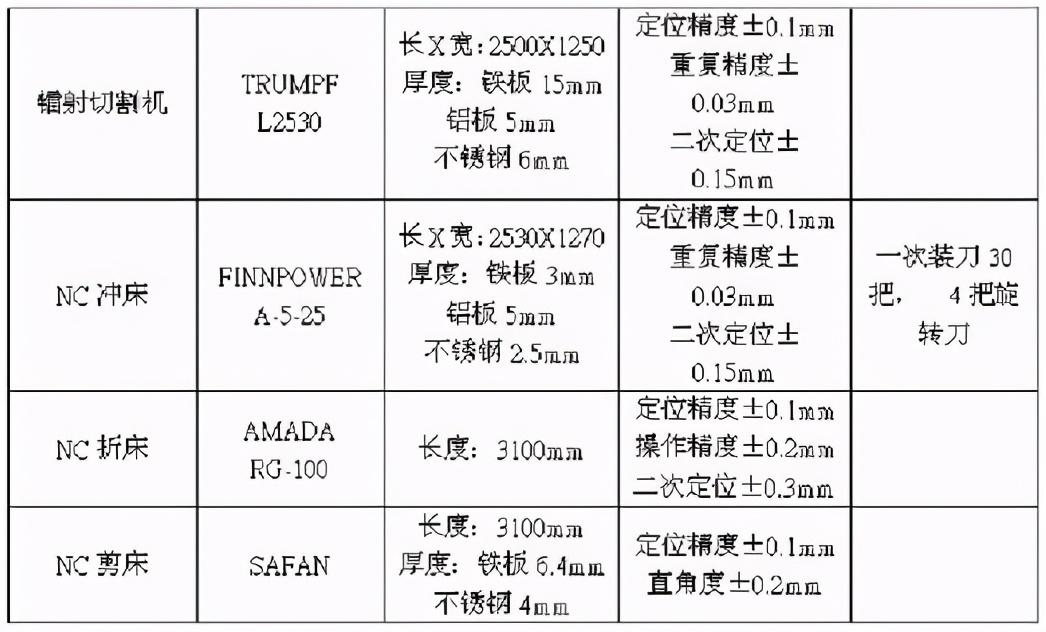