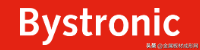
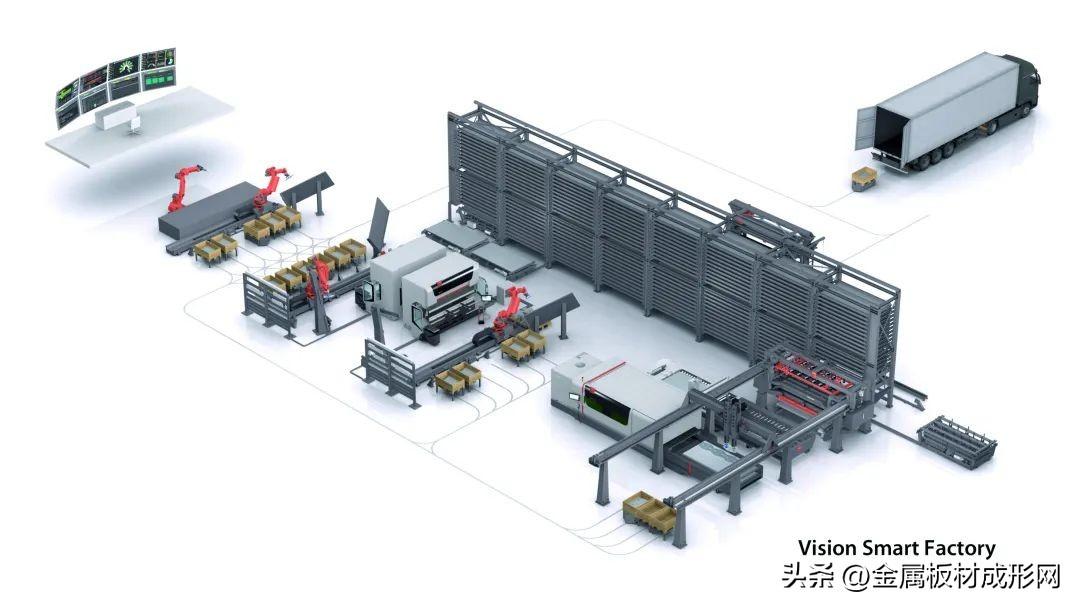
섀시 캐비닛 판금 가공은 여러 가지 다른 제조 방법을 사용하여 금속판을 원하는 모양으로 성형하는 과정으로 절단, 벤드, 용접에서 표면 처리, 조립 등 많은 단계를 포함한다.일반적으로 섀시 캐비닛 판금에서 금속 제품에 이르는 과정은 도면 제작에서 시작되며, 도면이 완성되면 판금 제조 과정을 거쳐 다양한 부품을 만든다.
레이저 절단
레이저 절단은 섀시 캐비닛의 판재를 절단하는 데 가장 선호되며, 이것은 매우 빠르고 정확한 절단 방법이며, 그림 1.5mm의 판재와 같은 금형의 제한을 받지 않고 평평하고 매끄럽고 가시가 없는 절단이다.
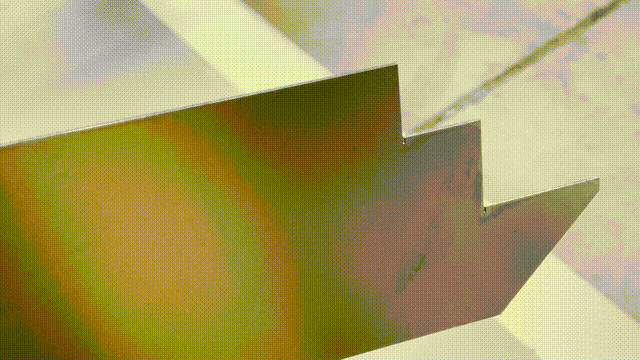
수치 제어 회전탑 프레스
프레스는 판금 업계에서 구멍을 자르는 또 다른 방법으로, 금속 헤드를 이용하여 판재에 구멍을 뚫는 것으로 대규모 생산에 적용되며, 둥근 구멍, 다공 등 규칙적인 모양을 만나면 수치 제어 회전탑 프레스가 금형 프레스를 사용하여 빠르게 실현할 수 있다.
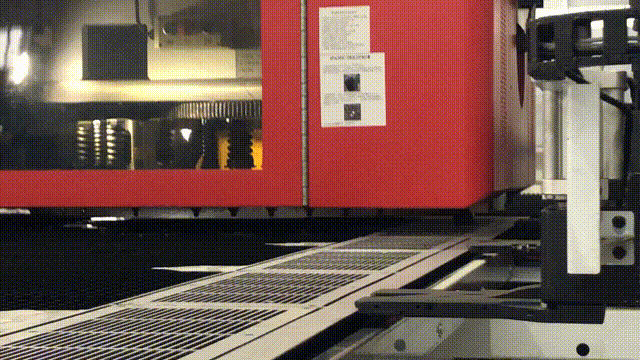
벤드
벤드의 복잡성 때문에 엔지니어가 금속의 벤드 속성에 익숙해야 하는 섀시 캐비닛 판금 가공 금속 제조에서 가장 어려운 단계가 될 수 있습니다.
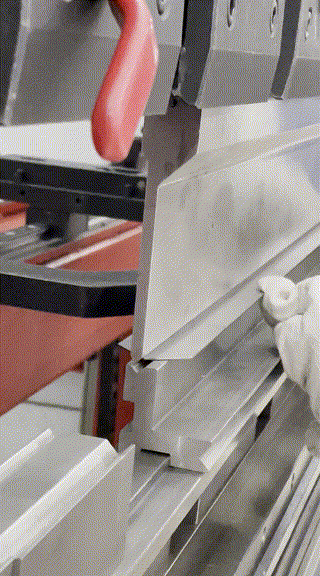
용접
용접 공정은 제품의 생산 성질, 도면 및 기술 요구에 따라 기존 조건과 결합하여 절단, 벤드 후의 판금 부품을 상자로 용접하는 것이다.
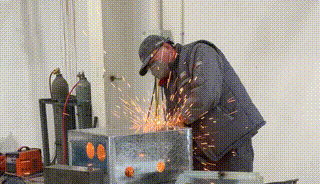
스프레이 (표면 처리)
용접이 성형된 상자는 시험 조립을 한 후 스프레이 작업장으로 순서를 바꾸어 분말 분사를 한다.분말 플라스틱은 정전기 분말 도료를 공작물에 도포하는 것으로, 정전기 작용으로 분말이 공작물 표면에 고르게 흡착된 후 고온으로 구워 최종 코팅을 형성한다.
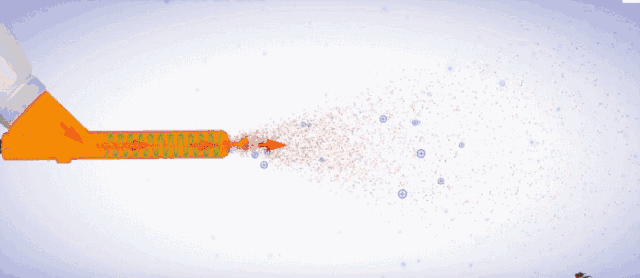
플라스틱 분사 후의 제품 표면은 먼지와 방수를 방지하며, 그 부착력, 부식, 노화 방지 등 방면은 페인트 분사 공예보다 우수하여 야외의 각종 열악한 환경에 적합하다.특별한 요구 사항이 없을 때 가장 선호하는 표면 처리 방법입니다.
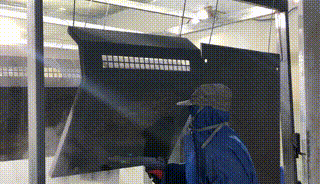
인쇄
일부 섀시 캐비닛은 플라스틱이 완성되면 조립으로 직접 순서를 바꾸어 조립하지만, 일부는 로고나 도안을 인쇄해야 하기 때문에 인쇄실로 순서를 바꾸어 인쇄해야 한다.
UV 태블릿 프린터는 산업 프린터에서 다크호스라고 할 수 있다. 전통적인 실크 인쇄 공예에 비해 그 기능은 매우 강력하다: 조판할 필요가 없고, 서로 다른 크기의 부품 인쇄에 적응할 수 있으며, 한 번에 성형할 수 있고, 도안이 아름답고 선명하며, 자외선 차단과 방수, 가장 중요한 것은 환경 보호에 냄새가 없다.
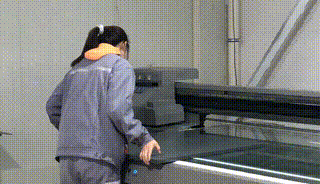
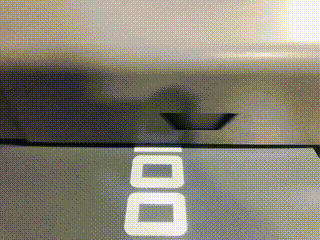
수치 제어점 접착제
수치제어점접착제는 전통적인 인공스티커에 비해 접착이 견고하고 표면이 매끄럽고 아름다우며 한번에 성형하면 이음매가 없고 부착력이 강하며 탄성이 좋고 방수와 방진이 된다.
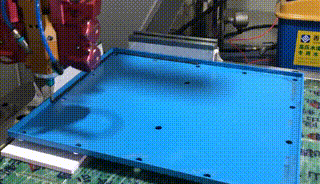
조립
섀시 캐비닛 최종 품목의 마지막 단계는 조립입니다.모든 판금 부품이 준비되었으니 조립하면 됩니다.
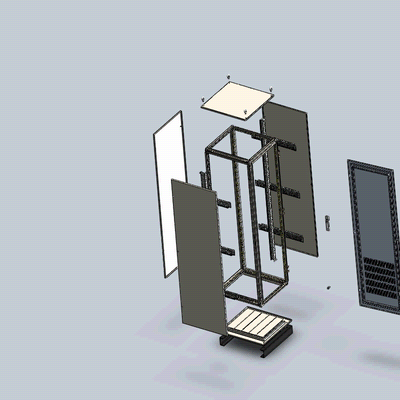