우리의 많은 알루미늄 형재는 압출하여 생산한 후에 모두 후기에 정밀 가공해야 한다. 왜냐하면 특수한 사용 장소에 조립해야 하기 때문이다. 어떤 조립 정밀도가 매우 높으면 가공 변형량을 줄여야 한다. 알루미늄 합금 형재는 정밀 가공하여 변형된 이유가 많다. 재료, 부품 외형, 생산 제조 표준 등과 모두 관련이 있다.주로 다음과 같은 여러 가지 측면이 있다: 모배열 응력으로 인한 변형, 절삭력, 절삭열로 인한 변형, 협착력으로 인한 변형.
가공 변형을 낮추는 가공 공정 대책
1. 반제품의 열응력 감소
자연 또는 인공 시효 및 진동 해결을 선택하면 모두 일부 반제품의 열 응력을 제거할 수 있다.사전 가공도 실행 가능한 가공 공정 방식이다.크고 굵은 모배는 용량이 크기 때문에 가공 후 변형도 크다.만약에 벽돌의 불필요한 부분을 미리 가공하고 각 부분의 용량을 줄이면 이후 공정 과정의 가공 변형을 낮출 수 있을 뿐만 아니라 미리 가공한 후에 일정 시간을 두면 일부 열응력을 방출할 수 있다.
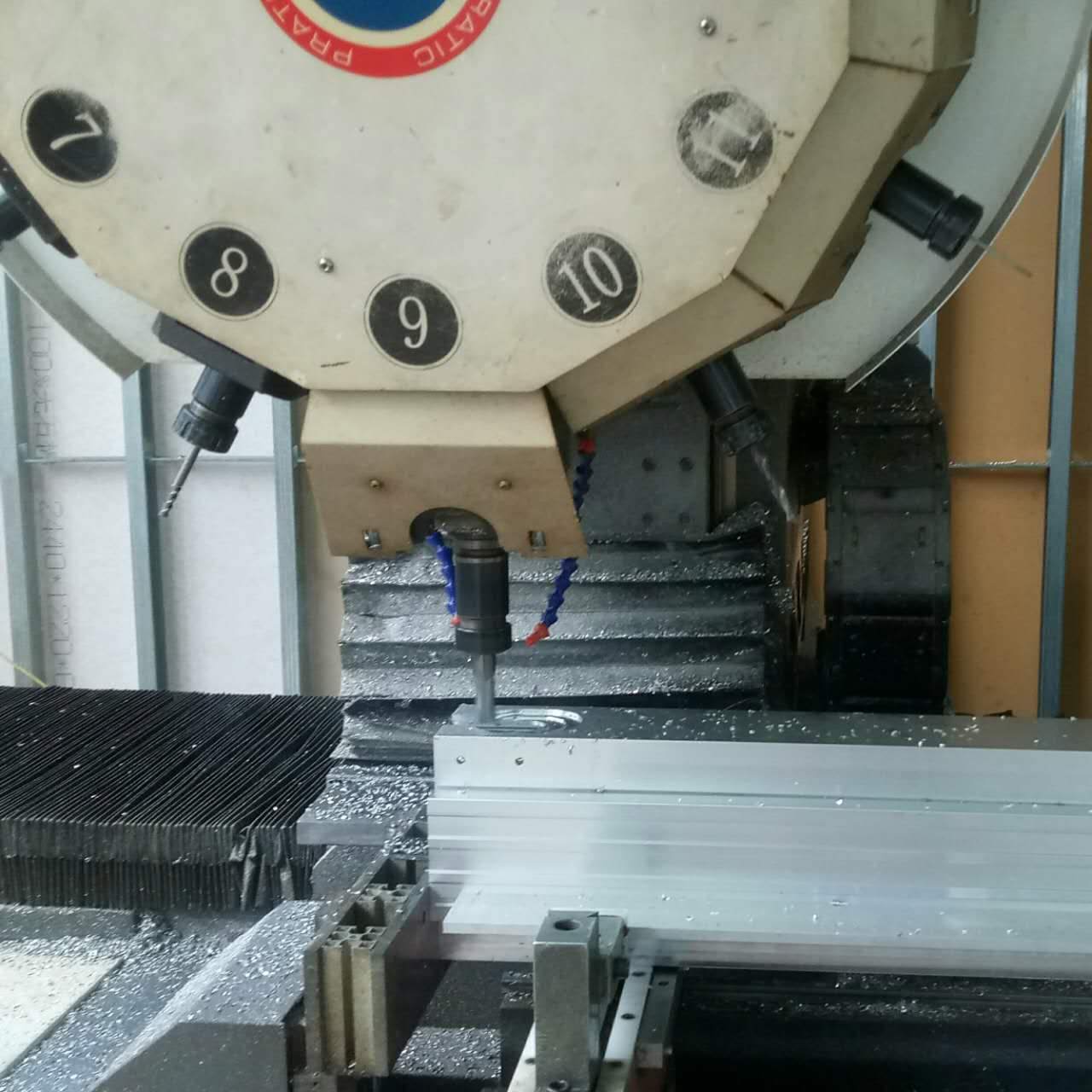
2. 공구의 절삭 작업 능력 개선
공구의 원자재, 기하도형의 주요매개변수는 절삭력, 절삭열에 아주 큰 위해를 끼치므로 공구를 적당히 선택하는것은 알루미니움합금부품의 정밀가공변형을 낮추는데 특히 중요하다.
(1) 공구 형상의 주요 매개변수를 효과적으로 선택합니다.
① 전각: 칼날의 압력 저항 강도를 유지하는 기준에서 전각은 적당히 크게 선택하여 한편으로는 날카로운 칼날을 다듬을 수 있고, 그 밖에 절삭의 변형을 낮출 수 있으며, 밀링면을 원만하게 하여 절삭력과 절삭 온도를 줄일 수 있다.음수 전면 각도 공구를 적용하지 마십시오.
② 후각: 후각 치수는 후면 칼날의 손상 및 가공 공정 성능에 현저한 위해를 가한다.컷의 두께는 후면을 선택하는 데 중요한 기준입니다.굵게 밀링할 때, 절삭 속도가 크고, 절삭 부하가 무겁고, 열값이 크기 때문에, 공구 열관의 열 방출 표준이 좋다고 규정하기 때문에, 후각은 좀 작게 선택해야 한다.밀링을 할 때, 칼날이 예리하도록 규정하고, 뒷날과 가공 표층의 마찰을 완화하며, 연전성 변형을 줄이기 때문에, 뒷각은 좀 더 큰 것을 골라야 한다.
③ 나선각: 절삭을 안정시키고 절삭력을 줄이기 위해 나선각은 최대한 크게 선택해야 한다.
④ 주경각: 주경각을 적당히 줄이면 열관의 열방출기준을 개선하여 알루미늄형재 정밀가공구역의 평균기온을 낮출수 있다.
(2) 공구 구조를 개선합니다.
① 나이프의 이빨 수를 낮추고 부스러기 실내 공간을 늘린다.왜냐하면 압주물 원자재는 가소성 변형이 매우 크고, 가공 중 절삭 변형이 매우 크기 때문에, 반드시 매우 큰 부스러기 실내 공간이 필요하기 때문에, 부스러기 슬롯 밑의 반경이 매우 커야 하고, 나이프의 치수가 적은 것이 좋다.
② 나이프 테크닉 이빨.측면 컷 날이 Ra = 0.4um보다 표면 투박도가 낮습니다.새 칼을 사용하기 전에, 가는 숫돌로 옆날 앞, 뒤쪽을 가볍게 두 번 갈아서, 칼날 숫날 테크닉의 이빨에 남아 있는 모변과 가벼운 톱니 모양의 무늬를 제거해야 한다.이렇게 하면 절삭 열을 줄일 수 있을 뿐만 아니라 절삭 변형도 작아집니다.
③ 공구의 손상 규범을 엄격히 제어한다.공구가 손상되면 가공소재의 거친도 값이 높아지고 절삭 온도가 높아지며 가공소재의 변형이 향상됩니다.따라서 내마모성이 좋은 칼의 원자재를 사용하는 것 외에 칼의 손상 규범은 0.3mm를 초과해서는 안 된다. 그렇지 않으면 부스러기 종양을 일으키기 쉽다.가공소재의 온도는 일반적으로 변형을 방지하기 위해 100℃를 초과하지 않아도 됩니다.
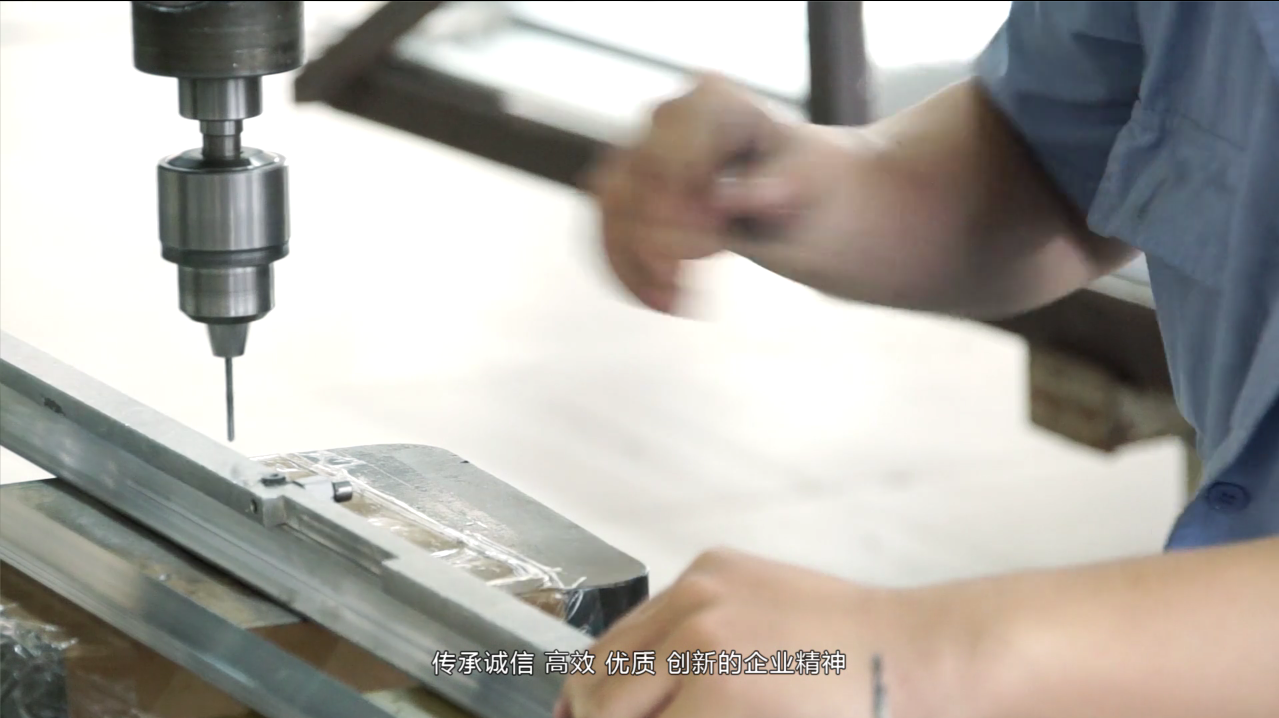
3. 가공소재의 끼워 넣는 방식을 개선한다
강도가 약한 두꺼운 벽 캐스트 가공소재의 경우 다음과 같은 클립 방법을 선택하여 변형을 줄일 수 있습니다.
① 두꺼운 벽 축 세트류 부품에 대하여 만약 세 발로 스스로 안심하는 유압 카드판이나 탄성 클램프로 축에서 끼워 넣는다면, 가공 후 일단 느슨해지면 알루미늄 형재 부품은 반드시 변형이 발생한다.이때 강도가 좋은 레이디얼 안쪽 구멍을 조이는 방식을 사용해야 한다.부품 내부 나사로 정확하게 위치를 정하고, 스스로 외부 나사가 있는 샤프트 목을 만들고, 부품의 내부 나사를 끼우고, 그 위에 후면 덮개로 내부 구멍을 조이고, 다시 나사로 등을 조인다.외부 원을 가공할 때 그립의 변형을 방지하여 만족스러운 가공 정밀도를 얻을 수 있습니다.
② 두꺼운 벽 금속 박판 부품을 가공할 때는 진공 흡판을 사용하여 균일한 협착력을 얻은 다음 작은 절삭 사용량으로 가공하면 부품의 변형을 매우 잘 피할 수 있다.
이 밖에 봉쇄법도 적용할 수 있다.두꺼운 벽 알루미늄 형재 부품의 가공 공정 강도를 높이기 위해 부품 내부에 물질을 충전하여 클램핑과 절삭 전 과정에서 부품이 변형되는 것을 줄일 수 있다.예를 들어, 질산칼륨의 3~6% 를 함유한 요소 용액 용해물을 공작물 안에 주입하고, 가공 후 알루미늄 형재 공작물을 물이나 에탄올에 스며들면 이 충전재를 용해하여 쏟아낼 수 있다.
4. 공정 절차를 과학적으로 안배한다
髙속 절삭 시, 가공 용량이 크고 그 단속 절삭 때문에 절삭 전 과정은 일반적으로 진동을 초래하여 알루미늄 형재 가공 정밀도와 거칠음을 해친다.따라서 수치 제어 작업셀의 빠른 절삭 가공 가공 공정의 전 과정은 일반적으로 황삭-반정밀-밀링 가공-정밀 가공과 같은 공정으로 나눌 수 있다.정밀도 규정이 높은 부품에 대하여 때로는 반드시 2차 반정밀 가공을 전개한 후 다시 정밀 가공을 전개해야 한다.황삭 후 부품은 당연히 냉각되어 황삭으로 인한 열 응력을 제거하고 변형을 줄일 수 있다.조가공 후 남겨진 용량은 변형량을 초과해야 하며, 일반적으로 1~3mm이다.알루미늄형 재료를 정밀 가공할 때, 정밀 가공 표층은 균형 잡힌 가공 용량을 유지해야 하는데, 일반적으로 0.2~0.5mm를 적당히 하여 칼이 가공 전 과정에서 안정된 상황에 처하게 하면 절삭 변형을 크게 줄일 수 있고, 우수한 표층 가공 품질을 얻을 수 있으며, 상품의 정밀도를 확보할 수 있다.
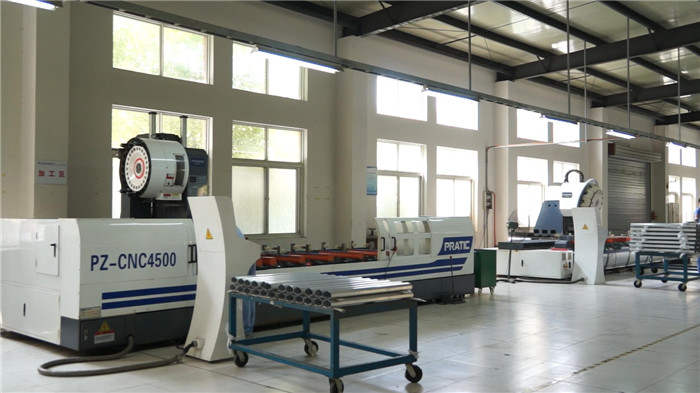
가공 변형을 낮추는 실제 조작 방법
알루미늄합금 원자재의 부품은 가공 전 과정에서 변형되는데, 상술한 연고를 제외하고, 조작 과정에서 조작 절차도 매우 관건적이다.
1. 가공 용량이 큰 부품에 대하여 가공 전 과정에서 비교적 좋은 열관 방열 표준을 가지고 발열량의 집중화를 방지하기 위하여 가공할 때 대칭성 가공을 선택하는 것이 좋다.90mm 두께의 두꺼운 판자가 있으면 60mm까지 가공해야 하며, 한 면을 밀링한 후 바로 다른 면을 절삭하여 한 번에 최종 규격까지 가공하면 평평도가 5mm에 달한다;연속적인 언더핸드 대칭성 가공을 선택하여 각 면을 최종 사양에 2회에 걸쳐 가공하면 플랫도가 0.2mm가 되도록 보장할 수 있습니다.
2. 만약 알루미늄합금 형재에 오목모형이 여러 개 있다면, 가공할 때 오목모형과 오목모형의 순서가공방식을 선택하기에 적합하지 않으며, 그렇게 하면 부품의 지지가 고르지 않아 변형을 초래하기 쉽다.여러 차례 계층을 선택하여 가공하고, 각 계층은 가능한 한 모든 다이 블록에 별도로 가공한 다음 다음 계층을 가공하여 부품을 균등하게 지지하고 변형을 줄인다.
3. 절삭 사용량을 변경하여 절삭력, 절삭열을 낮춘다.절삭 사용량의 세 가지 요소 중 칼을 등지고 가는 양은 절삭력에 큰 해를 끼친다.만약 가공 용량이 매우 크다면, 한 번에 칼을 들어가는 절삭력이 매우 커서, 부품을 변형시킬 뿐만 아니라, 선반 주축의 강도를 계속 해치고, 공구의 내마모성을 감소시킬 것이다.만약 뒷짐지고 칼을 가는 양을 줄인다면, 또 생산성에 매우 큰 영향을 받게 될 것이다.그러나 수치제어선반가공에서 모두 髙속절삭으로서 이 난점을 벗어날수 있다.등을 지고 칼을 먹는 양을 낮추는 동시에 상대적으로 칼을 확대하고 수치제어선반의 회전속도비를 높이면 절삭력을 줄일수 있으며 또 가공의 고효률을 확보할수 있다.
4. 칼을 넣는 순서도 중시해야 한다.조가공은 가공의 고효율을 높이고 완벽한 단위 시간 내의 절제율을 추구하는 것을 중시하며, 일반적으로 역밀링을 선택할 수 있다.털배아 표층의 불필요한 원자재를 가장 짧은 시간, 가장 적은 시간에 제거하여 정밀가공에 규정된 기하학적 도형의 윤곽을 기초로 한다.정밀 가공은 고정밀 고품질을 중시하므로 밀링면을 선택하는 것이 좋다.밀링을 할 때 나이프의 절삭 두께가 비교적 큰 것에서 서서히 0으로 떨어지기 때문에 가공 경저화 수준이 대폭 완화되고 부품의 변형 수준도 완화된다.
5. 두꺼운 벽 가공소재는 가공할 때 클립으로 인해 변형되기 때문에 정밀가공도 불가피하다.공작물의 변형을 최소한으로 줄이기 위하여 알루미늄형재 정밀가공은 최종규격에 도달하기 전에 조임부품을 느슨하게 하여 공작물을 마음대로 원형으로 복원한 후 다시 가볍게 조임으로써 공작물을 겨우 잡을 수 있는 것을 기준으로 (철저히 촉감에 의해) 이상적인 가공실제효과를 얻을 수 있다.한마디로 말하면 협착력의 작용점은 지지판 표면에 있는것이 가장 좋으며 협착력의 응효능은 공작물의 강도가 좋은 방위에 있으며 공작물이 느슨하지 않도록 확보하는 전제조건에서 협착력이 낮을수록 좋다.
6. 오목모형 알루미늄합금 부품을 가공할 때, 오목모형을 가공할 때 가능한 한 바이트가 꽈배기 드릴처럼 즉시 아래로 부품을 삽입할 필요가 없어 바이트의 부스러기 실내 공간이 부족하고 밀링면이 원활하지 않아 부품의 초온, 팽창 및 그 붕괴 칼, 칼이 부러지는 등 좋지 않은 상황을 초래한다.먼저 바이트와 같은 규격 또는 큰 1호의 꽈배기 드릴을 추가하여 칼구멍을 뚫은 다음 다시 칼로 절삭해야 한다.또는 CAM 소프트웨어를 사용하여 헬리컬 언더레이 프로세스를 제조할 수 있습니다.