지금까지 판금 캐비닛 가공은 비교적 복잡한 가공 공정에 속했지만, 응용 업계 및 제품의 차이로 인해 판금 캐비닛 가공이 사용하는 공정도 다를 수 있지만, 전체적으로 볼 때 큰 차이가 없다.판금 캐비닛 머시닝에 사용되는 일반적인 프로세스 중 몇 가지를 알고 계십니까?다음은 엠마과학기술유한회사 편집장이 당신에게 소개하겠습니다.
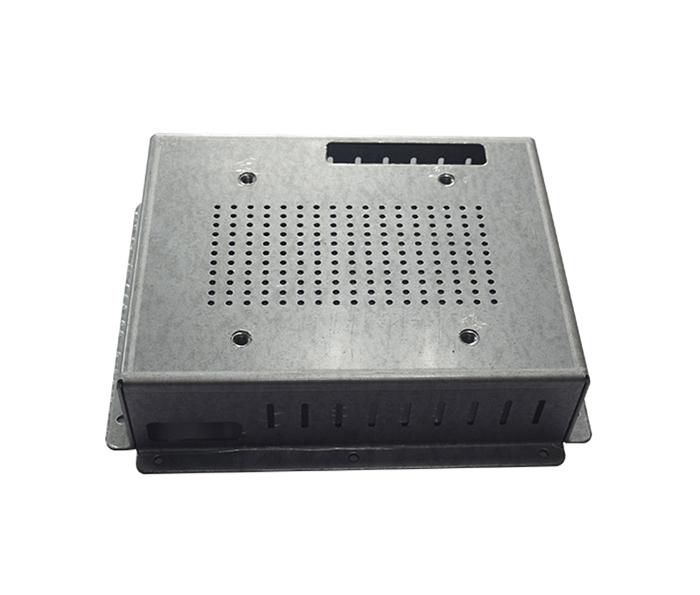
판금 캐비닛 머시닝에 사용되는 일반적인 프로세스는 다음과 같습니다.
1. 조립 공정
판금 캐비닛을 가공하는 과정에서 자주 사용하는 조립 방법으로는 지형 조립법, 모형 조립법, 수평식, 입식 및 역조립 조립법이 있다.
2. 원료 공급 공정
바로 모재에서 이미 로프트를 완성한 도안에 따라 재료를 내리는데 일반적으로 사용하는 방법으로는 수공절단, 기계절단, 재단가공, 화염절단, 플라스마가스절단과 레이자절단 등이 있다.판금 캐비닛 머시닝은 다양한 기술 요구 사항, 벌크의 크기 및 비용에 따라 재료를 드롭할 때 선택할 수 있습니다.재료를 넣는 방법에 따라 도안에 따라 나머지 재료를 가공하는 등 요소에 따라 다른 선택이 있을 수 있다.
3. 벤드 프로세스
벤드의 복잡성 때문에 이것은 판금 캐비닛이 금속을 가공하는 데 비교적 어려운 단계일 수 있으며, 엔지니어는 금속의 벤드 속성에 대해 잘 알아야 한다.대부분의 배관 절곡 장치는 벤드에 대해 일정한 제한이 있는데, 일반적으로 한쪽 높이는 배관 절곡 장치의 크기와 상단 칼의 높이이며, 해결 방법은 다각도의 큰 각도로 벤드할 수 있다.쌍방의 높이는 한쪽의 최대 높이보다 크지 않아야 하며, 한쪽 높이의 모든 제한을 받는 것 외에 밑변의 제한도 받는다: 벤드 높이 <;밑변.
4. 성형공예
성형 공정은 판금 캐비닛 가공에서 가장 중요한 부분인 설계 요구사항으로 가공 효율과 제품 품질을 향상시키고 원가를 낮추는 데 중요한 역할을 한다.성형공예에는 인공성형, 기계성형, 정압성형, 폭발로 붉은색이 되는 등이 포함된다.그 중 인공척형은 전통 판금공이 반드시 습득해야 할 기본 기능이다;기계 성형은 현재 가장 자주 사용되는 공정으로, 롤링 설비, 롤링 설비 및 금형, 압연 설비 및 금형, 엘보우 설비 및 금형을 통해 판금 부품의 성형을 실현한다.
판금 캐비닛 가공은 성형 방식에 따라 도안에 따라 재료 길이가 다르기 때문에 모두 생산 가공 과정에서 주도면밀하게 고려해야 한다.그렇지 않으면 원료의 크기가 너무 커서 재료를 낭비하여 원가를 높이고 때로는 가공에 어려움을 초래한다.재료가 부족하면 가공소재의 폐품을 초래할 수 있다.그리고 가공 성형의 공예 기술은 제품의 품질을 보장하고 작업 효율을 높이는 관건이다.
상술한 바를 종합하면, 우리는 판금 캐비닛 가공의 상용 공예에는 주로 조립, 하재, 성형 등이 포함된다는 것을 알 수 있다.그러나 이러한 일반적인 프로세스 외에도 다듬기, 절단, 벤드, 스프레이, 표면 처리......등등 프로세스가 포함되어 있으며, 여러분은 선택할 때 자신의 요구에 따라 적합한 판금 캐비닛 가공 프로세스를 선택하여 품질이 좋은 판금 캐비닛 가공 부품을 얻을 수 있습니다.