일반적인 상황에서, 우리가 평소에 말하는 판금 가공은 모두 두께가 균일한 판재를 가공하는 기술을 가리키며, 금형을 통해 성형할 필요가 없고, 생산 속도가 느리며, 하재, 벤드, 스트레칭, 용접, 분사, 조립 등을 포함하며, 주로 잘라서 접고 용접하는 등 가공 절차이다.그러므로 판금가공은 판금기술직원이 파악해야 할 중추기술이며 판금제품의 성형의 중요한 공정이기도 하다.그러면 판금 가공 과정이 어떤지 아세요?다음은 엠마과학기술유한회사 편집장이 당신에게 소개하겠습니다.
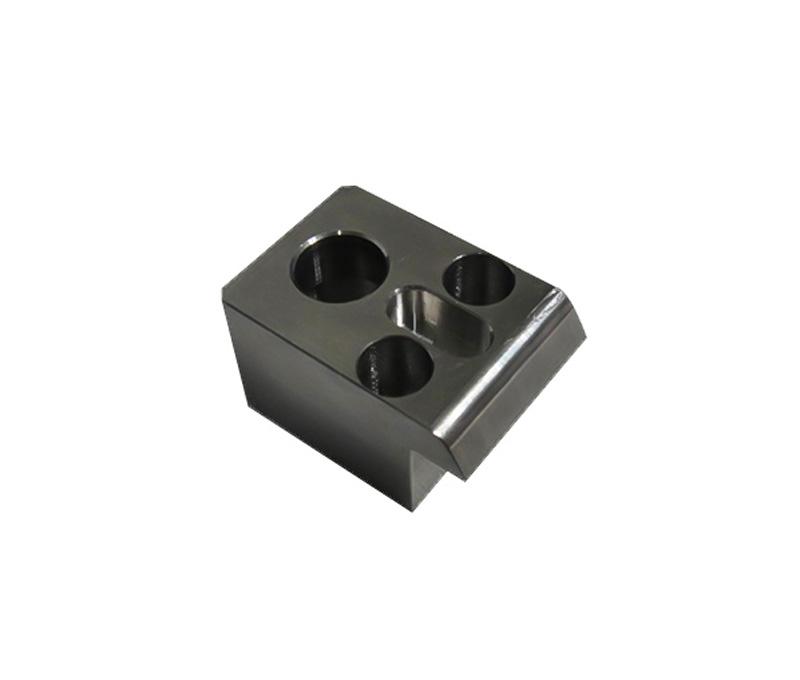
판금 가공의 제작 공정은 다음과 같습니다.
1. 재료:
주로 수충과 레이저 절단이다.수충이란 수치제어프레스로 가공하는데 판재의 두께범위는 랭간압연판과 열압연판 3mm, 알루미니움판 4mm, 스테인리스강 2mm이다.펀치에는 구멍의 모양, 재료의 성능 및 두께와 관련된 작은 크기 요구사항이 있습니다.레이저 절단은 레이저 비행 절단 가공으로 판재 두께 가공 범위는 냉간 압연판과 열 압연판 20mm, 스테인리스강 10mm이다.가공 판재의 두께가 크고 가공 부품의 외형 속도가 빠르며 가공이 유연하다는 장점이 있다.
2. 벤드:
벤드 부품에는 최소 벤드 반지름이 있으며 재료가 벤드되면 모서리 영역에서 바깥쪽은 신축되고 안쪽은 압축됩니다.재료의 두께가 일정할 때 내부 벤드 반지름이 작을수록 재료의 스트레칭과 압축이 심해집니다.바깥쪽의 신축력이 재료의 한계를 초과하면 끊어지고 부러집니다.
3. 밀어내기:
스트레치 부품의 아래쪽과 직벽 사이의 필렛 반지름은 판의 두께보다 커야 하며, 스트레치 후의 재료 두께는 일정한 변화가 있을 수 있으며, 아래쪽 중앙은 일반적으로 원래의 두께를 유지하고, 아래쪽 필렛의 재료는 얇아지며, 위쪽은 플랜지에 가까운 재료는 두꺼워지고, 직사각형 스트레치 부품의 사방 필렛의 재료는 두꺼워진다.
4. 용접:
주로 아크 용접, 가스 용접인데, 그 중 아크 용접은 유연하고 기동적이며 적용성이 광범위하여 전 위치 용접을 할 수 있다;사용 설비가 간단하고 내구성이 좋으며 유지 보수 비용이 적게 드는 등 장점이 있다.그러나 노동 강도가 높고 품질이 안정적이지 못한 것은 조작자의 수준에 달려 있다.판금 가공은 3mm 이상의 탄소강, 저합금강, 구리, 알루미늄 등 비철합금을 용접하는 데 적용된다.에어 용접 화염의 온도와 성질은 조절할 수 있다. 아크 용접에 비해 열원은 열영향구역보다 넓고 열량은 아크 집중보다 못하며 생산성이 낮다. 얇은 벽 구조와 작은 부품의 용접에 응용된다. 강철, 주철, 알루미늄, 구리 및 그 합금, 경질 합금 등을 용접할 수 있다.
5. 분사:
오븐 등 기계를 통해 철물의 표면에 자동적으로 기름을 뿌리고 가루를 분사하는 등 처리를 진행하여 제품의 외관을 밝고 아름답게 하여 포장출하의 수요에 도달시켰다.
6. 검사:
판금가공제품의 생산과정은 품질검사부문에서 실시간으로 통제하여 생산손실과 불량품률을 낮추고 생산품질을 보장한다.
7. 입고:
판금 가공이 위의 절차를 거친 제품은 이미 입고되어 출하를 준비하는 요구에 도달하여 포장하여 입고할 수 있다.
요약하면 판금 가공의 제작 공정입니다.판금 가공은 간단한 클램프만 있으면 금형이 필요 없이 복잡한 금형을 잘라내는 가공 방법을 잘 대체하여 생산 주기를 크게 단축하고 생산 원가를 낮출 수 있기 때문에 판금 가공은 우리의 일상생활에서 매우 널리 응용된다.