① G32 머시닝 끝 스레드 소개:
개요: 평면 스레드는 대부분 직사각형 스레드를 위주로 하며, 선반의 자정 코어 디스크 (디스크) 는 바로 이런 구조를 사용한다.이런 종류의 스레드는 구체적인 코드 마크업이 없으며 일반적으로 문자 주석이다.
그림 2-8은 끝 스레드의 약도입니다.
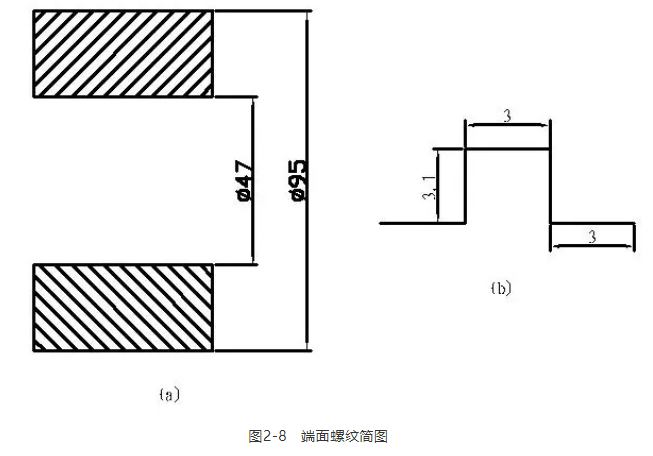
그림 (a) 은 단면 스레드 전체 구조의 약도이고, 그림 (b) 은 단면 스레드의 국부 증폭도이며, 스레드 깊이가 5mm 미만일 때 0.1mm를 추가해야 한다고 규정한다.
끝 스레드 회전 방향에 대한 판단:
주축이 한창 돌아가는 상황에서 밖에서 안쪽으로 차를 몰면 오른쪽 회전 (시계 방향) 에 속하고 반대로 왼쪽 회전 스레드 (반시계 방향) 에 속한다.
명령 형식: G32 X g F g (X는 컷의 끝점 좌표, F는 스레드 가이드)
프로그램 문 (차량 끝 스레드 세그먼트만)
G99 M3 S500 T0202;(슬롯 커터 B = 3mm)
G0 X100. M8;
Z-0.5;
G32 X40. F3.0;
G0 Z3.;
X100.;
Z-0.7;
G32 X40. (칼날 너비 그림 2-9 고려) F3.0;
G0 Z3.;
X100.;
Z-1.0;
G32 X40. F3.0;
G0 Z3.;
X100.;
Z-1.5;
G32 X40. F3.0;
G0 Z3.;
X100.;
Z-2.0;
G32 X40. F3.0;
G0 Z3.;
X100.;
Z-2.5;
G32 X40. F3.0;
G0 Z3.;
X100.;
Z-3.1;
G32 X40. F3.0;
G0 Z90.;
M5;
M30;
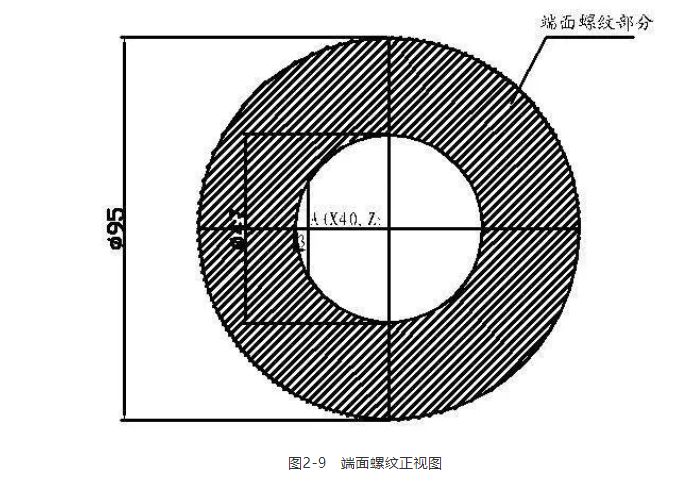
참고: 이 위치는 일치해야 합니다.
② 피치 스레드 가공 소개
광저우 수치제어(GSK) 등 일부 국내 수치제어 시스템은 변거 스레드를 가공할 때 G32 지령을 사용한다.그림 2-10과 같이
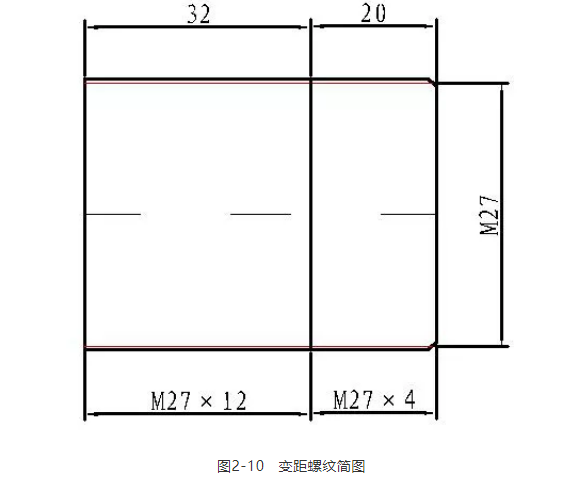
그림 2-10 피치 스레드 약도
수치 계산:
274의 치아 높이(지름값) = 1.34 = 5.2mm;
2712의 치아 높이(지름값) = 1.312=15.6mm;
치고는 최소 치고를 근거로 한다.
그래서 오솔길 = 27-5.2 = 21.8mm.
차가 스레드에서 멀어지면 최대 스레드의 스레드(P=12)로 스핀들 회전 속도가 결정됩니다.
프로그램 문 (차량 스레드 세그먼트만)
G99 M3 S200 T0202;
G0 X30.;
Z3.;
X26.;
G32 Z-20 F4.0;
G32 Z-56 F12.;
G0 X30.;
Z3.;
X25.6;
G32 Z-20. F4.0;
G32 Z-56. F12.;
…;
G32 X30.;
Z3.;
X21.8;
G32 Z-20. F4.;
G32 Z-56. F12.;
G0 X30.;
Z90.;
M5;
M30;
피치 스레드란 스레드 플런지로 데이텀 피치 값 F를 지정한 다음 피치마다 피치 차이 K (부가가치나 감액) 를 생성하는 것을 말합니다.
FANUC (파나코) 등 일부 수입된 수치제어시스템에는 변거리나사를 가공하는 특정지령 G34가 있다.
명령 형식: G34 X~6 Z ~ F~6 Kg;
여기서 X, Z는 스레드의 끝점 위치이고 F는 긴 축 방향이 시작점에 있는 도정이며 K는 주축의 각 도정의 증가량과 감소량이다. K 값의 지령 범위는 0.0001-500.0000mm이다. 아래 그림과 같다.
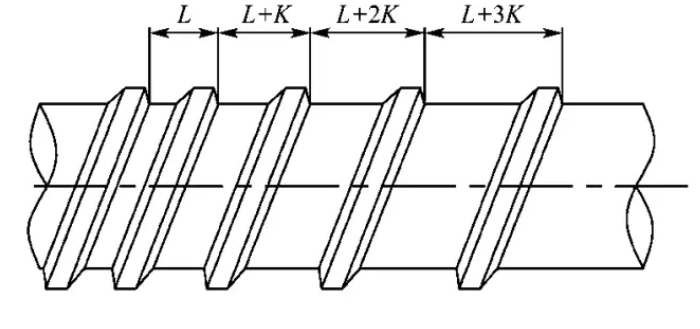
예를 들어, 시작점은 5mm, 증가는 1mm, 스레드 길이는 50mm, 프로그램은 G34 Z-50.F5. K1。
③ 폴리선 스레드 가공
다선나사는 일반적으로 전동에 사용되는데 모두 직나사이다. 수치제어는 다선나사를 가공한다. G92를 사용하여 서브루틴을 호출하는 방법을 사용할수 있다. 수입선반은 또 G32지령을 지원하여 다선나사를 가공할수 있으며 G76지령도 다선나사를 가공할수 있다 (뒤의 설명).
G92는 그림 2-11과 같이 서브루틴을 호출하여 폴리선 스레드 머시닝을 처리합니다.
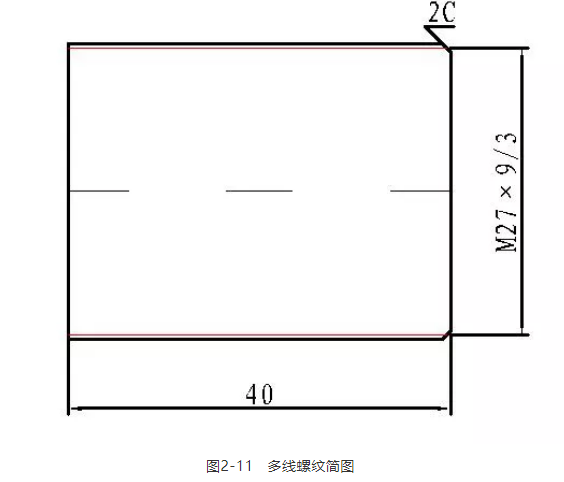
그림에 표시된 의미: M279/3
여기서 M27은 명목상 지름, 9는 스레드 가이드, 3은 피치입니다.
가이드 = 피치 선 수 때문에 이 스레드는 3선 스레드입니다.
수치 계산:
대경 = 27-0.133 = 26.61mm;
오솔길 = 27-1.33 = 23.1mm;
프로그램 문 (차량 스레드 세그먼트만)
서브루틴 (O0046)
G92 X26. Z-40. F9.;
X25.7;
X25.4;
X25.2;
X25.0;
…;
X23.1;
M99;
마스터 프로그램
G99 M3 S700 T0202;
G0 X30. M8;
Z3.;
M98 P0046;
G0 X30.;
Z6.;
M98 P0046;
G0 X30.;
Z9.;
M98 P0046;
G0 Z90.;
M5;
M30;
Z3.Z6.Z9.포지셔닝당 피치 증가 (P=3)
G32 머시닝 피치 스레드를 지원하는 시스템도 있습니다.
명령 형식: G32 X~6 Z ~ F~6 Qg;
여기서 X, Z는 스레드의 끝 위치이고 F는 스레드 트랙이며 Q는 스레드의 시작 각도입니다.증분은 0.001이며 소수점을 지정할 수 없습니다.이중 스레드를 가공하고 해당 변위가 180이면 Q180000을 지정합니다.
시작 각도 Q는 모드 값이 아니므로 매번 지정해야 합니다. 그렇지 않으면 시스템은 0으로 간주됩니다.
다선 스레드 가공은 G32, G34, G92, G76 명령어에 모두 유효합니다.
④ 사다리꼴 스레드 가공
수치제어선반에서는 G76 나사산절삭순환지령을 사용할수 있으며 사진법, 교차절삭 등 방법으로 사다리꼴나사를 가공할수 있지만 일정한 기술난이도가 있다.그러므로 장기적인 실천경험에 근거하여 일련의 경험공식이 프로그래밍데이터에 대한 정밀계산을 기초로 나사못절삭지령 G32를 사용하고 서브루틴을 호출하며 서브루틴에 가공방법을 교묘하게 설정하여 사다리꼴나사를 가공함으로써 안전하고 믿음직하게 합격된 사다리꼴나사를 가공할수 있다.
프로그래밍 및 가공 기술 분석:
(1) 칼날을 갈 때 칼의 칼끝 각도가 이빨 모양의 각도와 일치하도록 주의해야 하며, 칼끝 너비는 슬롯 밑의 너비보다 작아야 한다.
(2) 가능한 한 선반가공 과정의 치조 간극이 충분히 커서 바이트의 단일 날 절삭과 부스러기 배출이 순조로울 수 있도록 보장한다.예를 들어 나사 거리가 5mm인 사다리꼴 스레드 슬롯의 바닥 너비는 1.7mm이고 칼날의 끝은 1.2-1.4mm가 적당하다.칼끝이 너무 크면 칼끝과 치측의 간격이 너무 작아 부스러기가 잘 배출되지 않고 칼을 찌르기 쉽다.칼끝이 너무 작으면 칼끝의 강성이 나빠져 진동을 일으키기 쉬워 가공 표면의 거칠음이 비교적 떨어지고 정밀도를 제어하기 어렵다.
(3) 차 나사 앞에서의 바이트의 위치를 주의한다. 칼끝에서 치정까지의 거리는 치고h보다 크다. 치고h보다 작으면 칼끝이 나사 가공 후 단계와 나사 치정 사이에서 마찰하여 폐품이 발생한다.
(4) 서브루틴을 작성하고 호출한다. 1중 서브루틴을 사용할 수도 있고 다중 서브루틴을 호출할 수도 있다.
1. 프로그래밍 데이터의 계산
(1) 반제품의 위치점 X값 = 공칭 지름 + (0.5P+ac) 2 + 1, 식중 P는 피치, ac는 치정 간격, 0.5P+ac는 치형 높이.피치의 크기에 따라 이빨 위 클리어런스의 값을 선택하려면 다음 표를 참조하십시오.

(2) 첫 번째 공구 밑 공구 점 X 값, X = 명목상 지름 - 상하 편차 평균 -0.2
(3) 오솔길 = 명목상 지름 - (0.5P+ac)2
(4) 가공 더하기 = (첫 번째 공구 밑 공구 점 X 값 - 오솔길) / X 방향 엔트리 (지름 값) + 1
(5) U = 스톡 위치 점 X 값 - 첫 번째 공구 아래 공구 점 X 값.
2.패스 코스: 사다리꼴 나사를 가공하는 것은 일반적으로 좌우 절삭법을 사용하며, 나사 거리가 작은 것은 조차, 반정차, 정차로 나눌 수 있다;나사 거리가 큰 것은 조차, 반조차, 반정차, 정차로 나눌 수 있다.좌우 절삭법을 사용하여 서브루틴을 한 번 호출할 때 바이트가 한 절삭 깊이를 왼쪽 차에 한 번 넣은 후 오른쪽으로 한 간격을 이동하여 한 칼을 더 차고, 한 번 더 서브루틴을 호출할 때 바이트가 또 한 절삭 깊이를 왼쪽 차에 한 칼 넣은 후 오른쪽으로 한 간격을 이동하여 한 칼을 더 차면 완료될 때까지 한다.
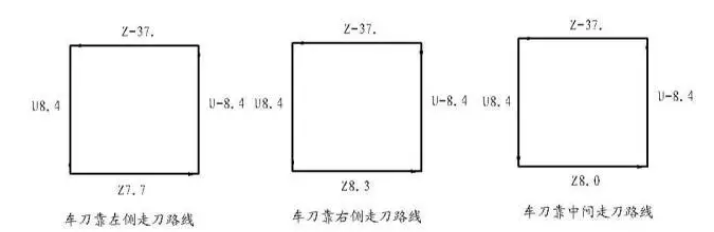
[사다리꼴 스레드 머시닝의 예] 다음 그림과 같이 사다리꼴 스레드 머시닝 부품입니다.
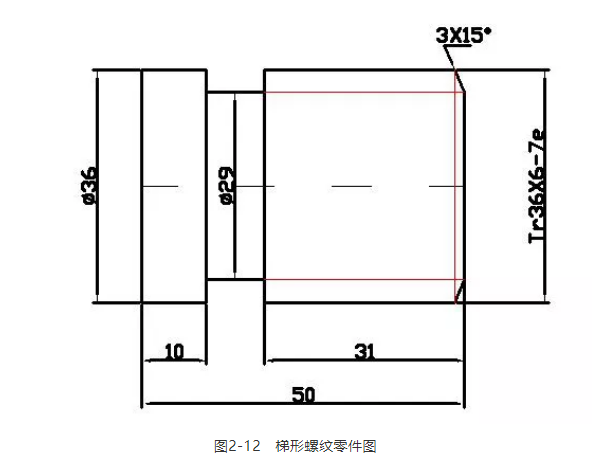
3. 사다리꼴 스레드 데이터 계산 가공
(1) 스톡 위치 X값
X = 공칭 지름 + (0.5P+ac) 2 + 1 = 36 + (0.56+0.5) 2 + 1 = 44
(2) 차트에서 공칭 지름의 상하 편차 값을 확정한다: 상하 편차는 0, 하 편차는 -0.375, 그 평균치는 -0.2, 첫 번째 칼 아래 칼점 X 값 = 36-0.2-0.2 = 35.6.
(3) 오솔길 = 공칭 지름-(0.5P+ac)2 = 36-(0.56+0.5)2 = 29.
(4) 가공 덧셈 = (첫 번째 공구 점 X 값 - 오솔길) / X 방향 엔트리 (지름 값) + 1 = (35.9-29) / 0.1 + 1 = 67.
(5) U = 스톡 위치 점 X 값 - 첫 번째 공구 점 X 값 = 44-35.6 = 8.4.
4. 사다리꼴 스레드 치수를 계산하고 테이블을 검토하여 공차를 결정합니다.
대경 D = 36
중경 d중 = d-0.5p = 36-3 = 33 차트에서 그 공차를 확정하기 때문에 d= 33
치아 높이 h = 0.5p + ac = 3.5
오솔길 d=d에서 -2h=29
치정 폭 f = 0.336p = 2.196
치저폭 w = 0.366p0.536a = 2.196-0.268 = 1.928
경험에 의하면 사다리꼴 스레드 팁의 너비 f=1.5mm를 사용하는 것이 비교적 합리적이다.
3.1mm의 측정봉으로 중경을 측정하면 그 측정치수는 M = d 중 + 4.864d-1.866p = 36.88이고 중경 공차대에 따라 그 공차(0-0.355)를 확정하면 M = 36.525-36.88이다.
5. 수치 제어 프로그램 작성
G99 M3 S300 T0101;
G0 X44. Z8.;(44는 스톡 위치 X값)
M8;
M98 P470002;(47은 황삭 나이프 수)
M98 P200003;(20은 마무리 공구 수)
M9;
G0 X100. Z100.;
M30.
황삭 서브루틴 작성
G0 U-8.4;(8.4는 U 값)
G32 Z-37. F6.;
G0 U8.4;
Z7.7;
U-8.4;
G32 Z-37. F6.;
G0 U8.4;
Z8.3;
U-8.4;
G32 U0. Z-37. F6.;
G0 U8.3;
Z8.;
M99;
마무리 절차 작성
O0003;
G0 U-8.4;
G32 Z-37. F6.;
G0 U8.4;
Z7.9;
U-8.4;
G32 U0. Z-37. F6.;
G0 U8.4;
Z8.1;
U-8.4;
G32 U0. Z-37. F6.;
G0 U8.3;
Z8.;
M99;
상술한 공작물도 G92로 하위 절차를 작성할 수 있다.
마스터 프로그램
…
G00 X44. Z6.;(탭이 지름에 빠르게 도달함Φ44mm 단면 외 3mm)
M98 P60002;(굵은 차는 O0002 서브루틴 6회 호출)
M98 P80003;(반조차는 O0003 서브루틴을 8회 호출)
M98 P80004;(반정차 호출 주 프로그램 O0004 하위 프로그램 8회)
M98 P80005;(정차 호출 O0005 서브루틴 8회)
G0 X100. Z100.;(탭이 프로그램 시작 지점으로 빠르게 복귀함)
…
O0002(황삭 서브루틴)
G00 U-0.5;(황차당 이송 깊이)
M98 P0006;(기본 서브루틴 O0006 호출)
M99;서브루틴이 종료되면 마스터로 돌아갑니다.
O0003;(반조차 서브루틴)
G00 U-0.3;(하프 황삭차의 이송당 깊이)
M98 P0006;(기본 서브루틴 O0006 호출)
M99;서브루틴이 종료되면 마스터로 돌아갑니다.
O0004;(반정밀 서브루틴)
G0 U-0.15;(반정차 이송당 깊이)
M98 P0006;(기본 서브루틴 O0006 호출)
M99;서브루틴이 종료되면 마스터로 돌아갑니다.
O0005(정차 서브루틴)
G0 U-0.05;(정차 이송당 깊이)
M98 P0006;(기본 서브루틴 O0006 호출)
M99;서브루틴이 종료되면 마스터로 돌아갑니다.
O0006(기본 서브루틴)
G92 U-8. Z-37. F6.;(선반가공 스레드 왼쪽 이빨 측면)
G00 W0.43;(스레드 나이프는 0.43mm를 빠르게 이동하여 오른쪽 치아 측면에 도달합니다.)
G92 U-8. Z-37. F6.;(선반가공 스레드 오른쪽 이빨 측면)
G0 W-0.43;(-0.43mm 이동하여 스레드 왼쪽 이빨 측면 축 위치 복귀)
M99;서브루틴이 종료되면 마스터로 돌아갑니다.
관심 좀 주고 가면 안 돼요?매일 UG 프로그래밍 비디오를 업데이트합니다.
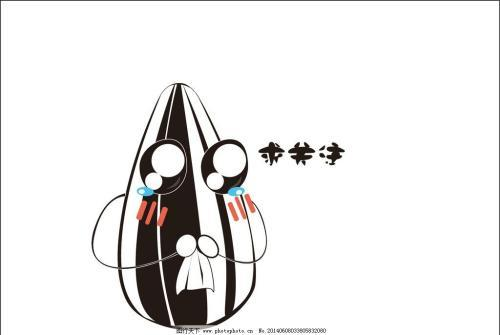