디지털화 설계 심양 판금 가공 부품의 오차가 비교적 은폐된 문제에 대해 모델링 과정에서 발생하는 오차와 가능한 제거 조치를 분석하고 디지털 제어 측정에서 오차가 축적되는 문제를 분석했다.또 측정점 구름과 부품 표면 Z가 잘 맞물린 결과를 분석해 오차 평정에 관한 새로운 판단 기준을 제시했다.상술한 조치를 통해 부품 가공 오차를 줄이고 부품의 합격률을 높일 수 있다.
1. 등거리면을 만들 때 발생하는 오차 및 해소방법:
CATIA 소프트웨어를 사용하여 다음과 같이 분석하고 있습니다.016mm 두께의 판금을 가공할 때 어떤 곳은 두께가 1.021mm로 0.005mm 차이가 나는데 이는 등거리면 기능을 등거리면으로 할 때 오차가 존재한다는것을 말해준다.오차를 줄이고 공정에서 요구하는 정밀도를 달성하기 위해서는 먼저 오프셋 서피스의 Z 큰 편차가 공정에서 허용하는 오차 범위 내에 있는지 확인해야 하며, 둘째, 여러 번 오프셋이 필요할 때 가능하다면 모든 오프셋에 대해 이전 오프셋 서피스가 아닌 원래 서피스를 사용해야 한다.
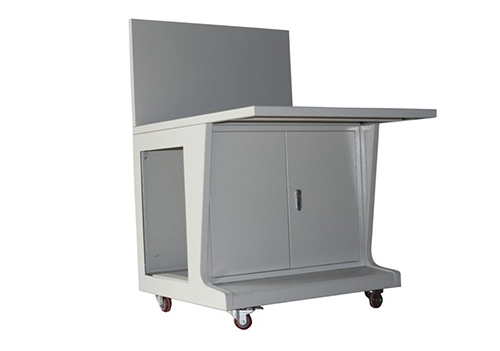
2. 측정기준의 부적절한 선택으로 인한 오차:
수치제어가공의 판금가공부품 타이어의 경우 우에 남겨진 기준은 흔히 설계기준이 아니다. 이런 기준은 수치제어가공과정에서 이미 가공된 특성으로서 타이어설계기준에 대한 오차는 타이어가공오차이다.전체 모델 가공이 완료되면 공차가 축적되어 모델의 가장자리, 외형 등 측정 기준에 비해 오차가 두 배인 설계 공차가 발생한다.부품의 외형 공차가 0이라고 가정합니다.25mm, 모델 타이어 설계 공차 0.08mm, 상술한 원인으로 외형이 측정기준에 비해 0.16mm로 변하여 측정결과가 부품의 초차라는 허상을 쉽게 초래할수 있다.
오차를 줄이기 위해서는 측정 기준이 설계 기준과 일치해야 한다.또한 점 클라우드와 부품 표면의 Z 적합성을 측정할 때 초핸디캡이 가장 적은 변환을 기록하면 판금 가공품의 합격률을 높일 수 있다.
글의 내용은 인터넷에서 유래한 것이니, 문제가 있으면 저에게 연락하여 삭제해 주십시오!