칼길의 총칙
굵게: 작업셀의 최대 하중에서 대부분의 경우 가능한 한 큰 칼, 가능한 한 큰 칼, 가능한 한 빨리 공급해야 합니다.동일한 칼의 경우 이송과 이송의 양은 반비례합니다.일반적으로 선반의 하중은 문제가 아니며, 칼을 선택하는 원칙은 주로 제품의 2차원 각도와 3차원 호가 너무 작은지에 따라 고려된다.칼을 고른 후, 칼의 길이를 정하는데, 원칙은 칼의 길이가 가공 깊이보다 크고, 큰 공작물은 클램프의 간섭 여부를 고려해야 한다.
광도: 광도의 목적은 가공소재 표면의 광결도를 만족시키고 적당한 여유를 남겨두는 가공 요구를 달성하기 위한 것이다.마찬가지로 광도는 가능한 한 큰 칼, 가능한 한 빠른 시간을 선택한다. 왜냐하면 정밀도는 비교적 긴 시간을 필요로 하기 때문이다. 가장 적합한 칼과 공급으로 한다.동일한 이송 아래의 수평 진입은 클수록 빠르며, 서피스 진입량은 가공 후의 마무리와 관련이 있으며, 이송의 크기는 서피스의 겉모양과 관련이 있으며, 면에 손상을 주지 않고 최소 여유, 최대 칼, 가장 빠른 회전 속도, 적절한 이송을 남긴다.
클립 방법
1. 모든 클립은 가로 길이와 세로 길이가 짧습니다.
2. 펜치 클립: 클립 높이는 10밀리미터 이상이어야 하며, 가공품을 가공할 때 클립 높이와 가공 높이를 반드시 명시해야 한다.가공 높이는 펜치 평면보다 5밀리미터 정도 높아야 하는데, 그 목적은 견고성을 보장하는 동시에 펜치를 다치게 하지 않기 위해서이다.이러한 클립은 가공소재의 크기와 관련이 있는 일반적인 클립으로, 클립 높이가 클수록 클립 높이가 증가합니다.
3. 클립보드 클립: 클립보드는 야드로 작업대에 있고, 공작물은 나사로 클립보드에 잠겨 있다. 이 클립은 클립의 높이가 부족하고 가공력이 비교적 큰 공작물에 적용된다. 일반적으로 중대형 공작물은 효과가 비교적 좋다.
4, 야드 철 클립: 공작물이 비교적 크고, 클립 높이가 부족하며, 또 아래쪽에서 포슬을 잠그지 못할 때, 야드 철 클립을 사용한다.이 클립은 두 번 클립을 설치해야 하는데, 먼저 사각을 잘 치고, 다른 부분을 잘 가공한 다음, 다시 사각을 치고, 사각을 가공해야 한다.두 번째 클립을 조립할 때, 가공소재를 느슨하게 하지 말고, 먼저 부호한 다음에 느슨하게 해라.양쪽 사이즈를 먼저 찍어 다른 양쪽을 가공할 수도 있습니다.
5. 공구의 클립: 직경 10mm 이상, 클립 길이는 30mm 이상이어야 한다;지름 10mm 이하, 클립 길이는 20mm 이상이어야 합니다.공구의 클립은 견고해야 하며, 공구에 부딪히거나 직접 가공소재를 삽입하는 것을 엄격히 방지해야 한다.
공구 분류 및 적용 범위
1. 재료에 따라 나눈다:
● 백강칼: 마모되기 쉬우며 구리 공용 및 작은 강재 개조에 사용된다.
● 텅스텐 나이프: 청각 (특히 강재) 및 광도에 사용됩니다.
● 합금 칼: 텅스텐 강철 칼과 유사하다.
● 자색 칼;고속 절삭에 사용되며 쉽게 마모되지 않습니다.
2. 칼날에 따라 나눈다:
● 플랫 나이프: 평면 및 직체 측면에 사용되며 평면 각도를 맑게 합니다.
● 공구: 다양한 서피스의 라이트, 공구에 사용됩니다.
● 소코칼 (일방, 양자 및 5변 있음): 강재 개조 (R0.8, R0.3, R0.5, R0.4)에 사용된다.
● 트위드 커터: 트위드를 위한 여유 (0.3)
3. 칼대에 따라 나눈다:
● 스트레이트 드라이버: 스트레이트 드라이버는 다양한 장소에 적용됩니다.
● 슬래시 나이프: 그러나 직선 면 및 슬래시가 슬래시보다 작은 면에는 적용되지 않습니다.
4、칼날에 따라 나눈다:
양날,삼날,사날,날수가 많을수록 효과가 좋지만 일을 많이 할수록 회전속도와 공급에 상응하는 조정으로 날수가 많고 수명이 길다.
5. 공칼과 날도광칼의 차이:
공구: 오목한 면자가 볼보다 작고 평면자가 볼R보다 작을 경우 빛이 나지 않는다 (밑모서리가 보이지 않는다).
비도: 장점은 밑각을 맑게 하는 것이다.기계를 좋아하는 친구들은 직관학 기계 마이크로신호에 관심을 가질 수 있다.같은 매개 변수의 비교: V = R * 회전속도가 훨씬 빠르다 (비도), 힘이 세면 빛이 나는 물건이 밝다. 비도는 비교적 많은 등 높은 외형에 사용되며 때로는 비도를 사용할 때 중광이 필요하지 않다.단점은 오목면 크기와 평면자가 날의 지름보다 작으면 시간이 안 된다는 것이다.
시트 정수 문제
1. 이미 만들어진 가공면이 없는 상황에서 평면의 사면분 중에서 중심은 원점에 대하고 꼭대기는 0에 대하며 꼭대기는 평상시 (동공의 경우) 에 0.1의 여분을 남기지 않는다. 즉 수를 건드렸을 때 실제로는 0 (z) 에 대하고 그림은 0.1보다 낮다.
2. 이미 만들어진 가공면이 있을 때 그림의 기성이 0 (z) 을 마주하고 평면이 중간으로 나눌 수 있으면 중간으로 나눌 수 있다. 그렇지 않으면 이미 만들어진 모서리 수 (한쪽) 로 가공면은 실제 높이, 너비, 길이와 도면의 차이를 교정하고 실제 재료에 따라 프로그래밍해야 한다.일반적으로 먼저 그림의 크기로 가공한 다음 그림의 모양으로 가공합니다.
3. 여러 비트를 가공할 때, 첫 번째 비트 (표준 비트) 는 다른 몇 비트의 기준을 잘 징으로 하고, 길이와 너비를 모두 징으로 하고, 모든 다음 가공 기준은 이전에 이미 가공한 면을 기준으로 한다.
4. 상감부품의 위치: 전체 안에 놓고 아래를 일정한 높이로 받친 다음 도면도 이 높이를 높인다. 평면은 전체에 따라 나누고, 높이는 그림 아래에 따라 노란색 실로 묶는다.네모반듯하면 직분중할 수 있다.대략적으로 최대 외형 분할 가능;클램프를 잘라서 클램프 분할에 따라 상감도와 클램프의 상대적인 위치를 확정한 다음 도면 원점을 클램프 중심점에 놓는다.
트위드 패스 선택
1. 서피스 슬롯
● 관건은 범위의 선택과 면의 선택이다.
가공 영역은 선택한 범위 내에서 선택한 면을 끝 면으로 하고 가장 높은 점에서 가장 낮은 점까지 공구가 내려갈 수 있는 모든 곳을 원칙으로 합니다.선택한 면은 전체 면이 가장 좋고, 경계는 가공할 영역만 될 수 있으며, 면이 없는 곳은 공구 지름의 절반 미만의 거리를 확장하며, 다른 면은 충분한 여유가 있기 때문에 자동으로 보호됩니다.가장 낮은 곳에 R 징이 하나도 없기 때문에 최저선을 연장하는 것이 좋다.
● 공구 선택: 공구가 헬리컬 또는 사선으로 공구를 넣을 수 없거나 가공할 수 없는 영역이 공구에 들어갈 수 없는 영역은 봉하여 두 번 두꺼운 상태로 둡니다.
● 광선 공구 이전에는 반드시 두껍지 않은 영역을 모두 두껍게 해야 한다. 특히 작은 각은 2차원 각, 3차원 각 및 봉인된 영역을 포함한다. 그렇지 않으면 칼이 부러질 수 있다.기계를 좋아하는 친구들은 직관학 기계 마이크로신호에 관심을 가질 수 있다.2차 개조: 일반적으로 3차원 슬롯으로 범위를 선택하고, 평저 칼을 사용하며, 평면 슬롯과 외형 칼길을 사용할 수 있는 것은 사용한다.다른 면에 손상을 주지 않고 공구의 중심에서 선택한 경계까지, 일반적으로 경계를 정교하게 수정하지 않고, 빠른 양방향 각도로 상황에 따라 정한다. 나선형 진입, 각도 1.5도, 높이 1. 슬롯 모양이 막대일 때 나선형 하단이 안 되면 사선으로 진입한다. 일반적으로 여과를 연다. 특히 곡면이 굵어지고, 진입 평면이 낮아서는 안 된다. 칼에 부딪히지 않도록 하고, 안전 높이가 낮아서는 안 된다.
● 리트랙트: 일반적으로 상대 리트랙트를 사용하지 않고 절대 리트랙트를 사용하며, 섬이 없을 때는 상대 리트랙트를 사용합니다.
2. 평면 슬롯
다양한 평면, 노치 평면을 밀링하고 부분 개방형 평면을 밀링할 때 경계를 정해야 한다. 원칙은 칼을 들어갈 수 있고 (한 칼의 지름보다 크다), 개방된 곳은 반쪽보다 크며 외곽을 폐쇄한다.
3. 외형
선택한 평면이 외형분층에 적합할 경우 외형분층으로 칼을 들고 (평면외형) 칼을 들고 칼을 드는 점과 아래 칼을 드는 점이 한 점일 경우 칼을 들 필요가 없다. z평면은 일반적으로 칼을 들고 가능한 한 상대적인 높이를 사용하지 않는다.보정 방향은 일반적으로 오른쪽으로 보정 (순도) 한다.
4. 기계보정의 칼길 설치
보정 번호는 21이고, 컴퓨터 보정 기계 보정, 진입도는 수직 진입도로, 칼이 지나갈 수 없는 곳은 R을 크게 바꾸어 여분을 남기지 않는다.
5, 등 높은 외형
닫힌 면을 걷기에 적합합니다. 열린 면을 4바퀴 돌면 봉항면, 4바퀴 안 또는 4바퀴 안 돌면 범위와 높이 (일부 호형 외곽진입 굵기) 를 선택하여 굵은 면을 여는 데 사용합니다. 어느 한 평면 내의 가공 거리가 한 지름보다 작고, 한 지름보다 크면 더 큰 칼이나 두 번 같은 높은 외형을 사용해야 합니다.
6. 서피스 흐름선
최고의 균일성과 깔끔성을 가지고 있어 광도가 많은 경우에 대체할 수 있는 등 높은 외형에 적합하다.
7, 방사선 칼 길
중간에 큰 구멍이 있는 경우에 적합합니다 (소용).주의사항: 탄도, 칼이 날카롭지 않고, 칼이 너무 길며, 공작물이 너무 깊을 때 에워싸고 위아래로 걸어서는 안 된다;가공소재의 리각 양쪽의 면은 두 개의 칼로 나뉘어야 하며, 넘을 수 없으며, 광선칼의 가장자리는 연장하는 것이 좋다 (호선으로 진퇴칼을 사용한다).
청각
1. 이곳의 청각은 2차원 사각지대이다. 앞의 공정도 가보지 못한 부분이다. 만약 광도가 가야 할 곳은 먼저 청각을 한 다음 광도를 해야 한다. 너무 작고 큰 깊은 각은 몇 자루의 칼을 나누어 정리할 수 있다. 작은 칼로 너무 많은 곳을 청소하지 말아야 한다.
2. 3차원 각도 정리: 작은 홈을 열고 일부 3차원 모서리 부분.
3. 부러지기 쉬운 칼은 반드시 가는 칼, 너무 길고 가공량이 너무 큰 (주로 z방향, 깊이 방향) 상황을 고려해야 한다.
4. 칼길: 2차원 외형으로 가면 소각 (R0.8) 과 2차원 평면각만 청소할 수 있다;평행 칼로리 사용하기;등고 외형 사용하기;칼이 갈 수 없는 곡면과 외형이 갈 수 없는 사각지대가 있으면 먼저 봉하여 칼을 일으키고, 마지막에 각을 맑게 하고, 큰 면의 작은 구멍은 일반적으로 먼저 봉한다.
중광
1. 중광: 곡면으로서의 강재와 세공재 중광.
2. 원칙: 큰 칼이 굵게 열릴 때 층과 층 사이의 여분이 비교적 많아 광선칼을 사용할 때 더욱 좋은 효과를 얻을 수 있는 공정이다.
3. 특징: 빠른 제거, 큰 칼 날도 가능, 큰 진급, 큰 간격;표면의 질량을 꺼릴 필요가 없다;평면의 가공소재는 미디엄 라이트가 필요하지 않습니다.등고외형의 공작물은 중광을 사용하지 않으며, 등고외형이 굵어질 때 두 공정을 가늘게 함께 놓을 수 있으며, 가늘게 하면 표면의 여분과 층과 층의 거리를 가리킨다;중광이 필요한지, 또 하나의 중요한 요소는 작업하는 재료이다. 재료가 단단할수록 중광을 고려한다.중광의 가공 방향과 광선의 굵기가 가장 좋은 것은 이렇게 가공한 것이 효과가 좋고 균일하다.
광도
광도는 각종 제품과 금형의 조립 요구에 도달해야 하기 때문에 매우 신중해야 하며, 서로 다른 요구에 따라 서로 다른 칼 길 설정과 파라미터 설정을 해야 한다.
1. 광선의 언더 공차 높이와 마지막 높이가 모두 0으로 변경되고 공차는 1사 이내로 설계되며 여과할 필요가 없다(공부가 작을수록 공차가 작아지고 공차는 외형에 영향을 미친다).
2. 전면 모델과 파팅 면은 가장 좋은 광결도에 도달해야 하며, 후면 모델은 차수 가능하며, 기타 비협조 및 피빈 공간은 거칠게 할 수 있다.
3. 칼날 설계는 다음과 같은 요소에 의해 결정된다.
● 평면과 다른 면과 같은 구체적인 외형, 가파른 면과 평평한 곡면.
● 양면 사이의 이각 여부(이각은 분리).
● 두 부분의 요구가 다른지 여부(여분을 남길지, 여분의 양은 얼마인지, 광결도의 요구는 다르다).
● 광도에서 면을 보호하는 문제는 큰 문제이다. 이미 가공된 면에 대해서는 반드시 가공 중의 오차로 미리 보호하고 보호면의 요구에 따라 보호해야 한다.범위 보호, 오차를 따지지 않는 0 보호, 높이 범위와 평면 범위;보호면 보호.
● 칼길의 연장 문제, 광도에서 칼길을 가장자리까지 가공할 때는 호 진퇴 칼을 만드는 것이 좋다. 그렇지 않으면 미리 면을 약간 연장한다.
● 광도 중의 칼 문제.칼을 드는 것은 시간을 낭비하기 때문에 가능한 한 칼을 드는 것을 피해야 한다.
방법 1: 리프팅 클리어런스 설정 (작은 구멍)
방법 2: 표지, 칼을 드는 곳을 봉인(작은 구멍)
방법 3: 간격 (큰 구멍) 을 피합니다.
방법 4: 동일 높이에서 동일 높이로 확장
● 광도 중의 진입 문제, 첫 번째 칼의 진입은 반드시 공작물 밖으로 들어가야 하며, 진동 및 부딪쳐 공작물을 다치게 하는 것을 피해야 하며, 모든 광도는 반드시 진입도를 설치해야 한다.
● 공구의 마모 문제: 가공소재가 비교적 크면 여러 개의 칼이 같은 가공소재를 다 광내야 한다.
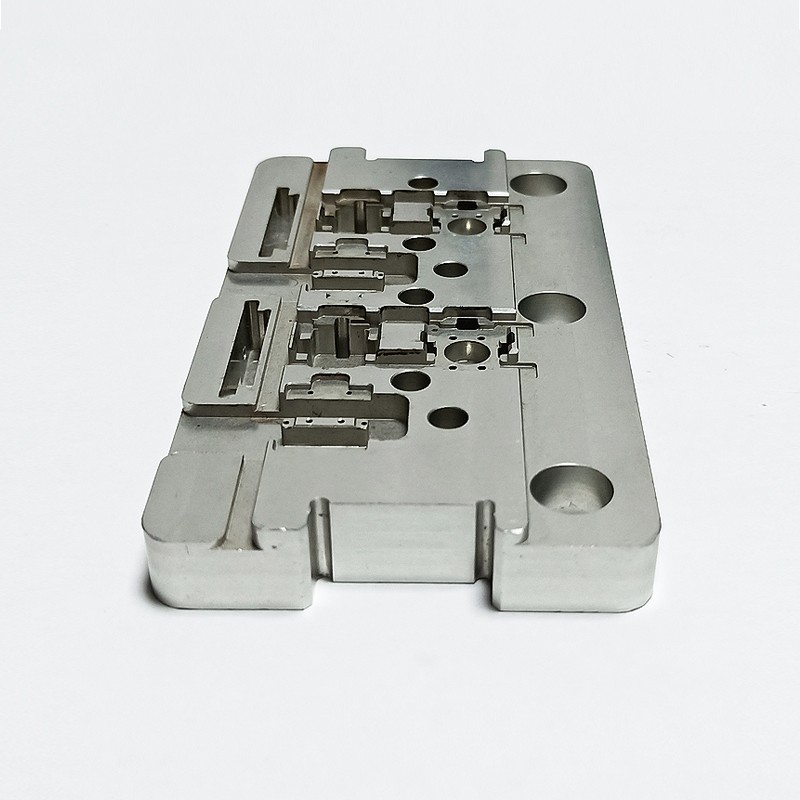