판금 가공 차체 재료도 일반 합금강 재료에서 스테인리스강, 알루미늄합금 형재로 발전하여 재료의 변경은 가공 기술의 개선을 이끌었고, 레이저 절단, 레이저 용접의 선진 기술도 따라서 철도 차량의 제조 생산 라인에 도입되었다.차체 생산의 과정은 다음과 같다: 먼저 구입한 알루미늄 합금 원자재를 사이즈에 따라 레이저, 물 절단 등 공정으로 재료를 사용하고, 그 후 다른 부품으로 가공 용접한다. 이 부품들은 조합되어 최종적으로 하나의 차체로 용접된다.기관차의 강철구조물가운데는 약 20~30% 의 이형부품이 있는데 특히 기관차운전사실, 차체보조장치 등의 부품은 레이자재료를 선택하기에 비교적 적합하다.레이저 절단은 유연한 가공을 실현하고 절단 과정은 제어 자동화를 실현하기 쉬우며 생산 주기를 크게 단축하고 제조 원가를 낮추며 제품의 품질을 향상시킬 수 있다.그러므로 레이자절단은 이미 전통적인 가공방식을 대체하여 국내외 궤도차량제조업에서 금속판재를 원료로 하는 주요수단으로 되였다.
아웃도어의 전자 설비는 갈수록 많아지고 있다. 많은 것이 목적성이 상대적으로 강한 전문 기능 제품이다. 또한 전자 제품 설비의 마이크로 구조화, 제품 품질 경형화, 제품 벽 두께와 얇은 형화 및 계기 하우징 미니화도 대중의 미래 수요이다.그러나 이러한 전자 장비 계기는 계기 케이스의 표면 보호에 의존한다. 현재 날로 고급스러워지는 전자 기계 제품의 경우 케이스의 부피가 작을수록 케이스의 무게가 가벼워진다. 그렇다면 이러한 계기 케이스의 휴대 측면성도 강할수록 현대 생활에서의 적용성도 보편화된다.그리고 점점 더 소형화되고 있는 이 케이스들은 소비성 휴대가 편리하고 여유롭고 수리가 용이합니다.
스테인리스강 섀시 캐비닛 섀시 케이스 제조업체 광택은 유연한 광택 공구와 연마재 입자 또는 기타 광택 매체를 이용하여 스테인리스강 섀시 캐비닛 표면을 수식 가공한다.광택은 스테인리스 섀시 캐비닛의 크기 정밀도나 기하학적 정밀도를 높이는 것이 아니라 매끄러운 표면이나 거울의 광택을 얻기 위해 사용되며, 때로는 광택(소광)을 없애는 데도 사용된다.일반적으로 광택 휠을 광택 도구로 사용합니다.광택 바퀴는 일반적으로 여러 겹의 캔버스, 펠트 또는 가죽을 겹쳐서 만들고, 양쪽은 금속 원판으로 끼우며, 그 바퀴 가장자리는 마이크로 파우더 연마재와 기름 등이 고르게 혼합된 광택제를 도포한다.
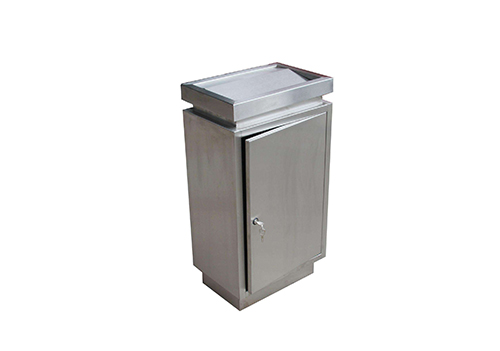