What are the machined products? What are the machined parts?
Machined workpieces, such as Sheet Metal Processing: shearing, punching, folding, pressing, bending. Or cutting: turning, milling, planing, grinding, drilling, sheet metal processing does not change the thickness of the material, cutting removal of the material changes the thickness of the workpiece. Mainly refers to the processing method that does not have chemical reactions (or the reaction is very small).
What are the main categories of "machined" parts?
Machining There are two main categories of machining: manual machining and numerical control machining. Manual machining refers to the method of machining various materials by manually operating mechanical equipment such as milling machines, lathes, drilling machines and sawing machines by mechanical workers. Manual machining is suitable for small batch and simple part production. Numerical control machining (CNC) refers to the use of numerical control equipment by mechanical workers for machining. These numerical control equipment include machining centers, turning and milling centers, wire EDM equipment, thread cutting machines, etc. The vast majority of machining workshops use numerical control machining technology. Through programming, the position coordinates (X, Y, Z) of the machined workpiece in the Cartesian coordinate system are converted into programming language, and the CNC controller of the numerical control machine tool controls the axis of the numerical control machine tool by recognizing and interpreting the programming language, and automatically removes the material as required, so as to obtain the finishing machine workpiece. Numerical control machining processes workpieces in a continuous manner, suitable for large quantities and complex parts.
Machining is mainly to process the parts we need, such as: the components of bicycles, the components of automobiles, aircraft and other parts we want to get belong to the category of machining, of course, machining is only the process of realizing the final product. Commonly used machining equipment includes digital display milling machine, digital display forming grinder, digital display lathe, electric spark machine, universal grinder, machining center, laser welding, medium wire, fast wire, slow wire, cylindrical grinder, internal grinding machine, precision lathe, etc., can carry out precision parts of the car, milling, planing, grinding and other processing, such machinery is good at precision parts of the car, milling, planing, grinding and other processing, can process all kinds of irregular shape parts, machining accuracy up to 2μm or even ultra-precision precision.
Machining production process
The production process of a machine refers to the entire process of making products from raw materials (or work in progress). For machine production, it includes the transportation and preservation of raw materials, the preparation of production, the manufacture of blanks, the processing and heat treatment of parts, the assembly and commissioning of products, painting and packaging. The content of the production process is very extensive. Modern enterprises use the principles and methods of systems engineering to organize production and guide production, and regard the production process as a production system with input and output. It can make the management of enterprises scientific and make enterprises more adaptable and competitive.
In the production process, the process of changing the shape, size, position and nature of the production object to make it a finished product or work in progress is called the process. It is the main part of the production process. The process can be divided into casting, forging, stamping, welding, machining, assembly and other processes. The mechanical manufacturing process generally refers to the sum of the machining process of parts and the assembly process of machines. Other processes are called auxiliary processes, such as transportation, storage, power supply, equipment maintenance, etc. The process is composed of one or several sequential processes. A process is composed of several working steps, and a working step is composed of several cutting tools.
The process is the basic unit that makes up the machining process. The so-called process refers to the part of the process that a worker (or a group of workers) continuously completes on the same workpiece (or several workpieces at the same time) on a machine tool (or a work site). The main feature of a process is that it does not change the processing object, equipment and operator, and the content of the process is completed continuously. The work step is the part of the process that is completed continuously under the condition that the processing surface remains unchanged, the processing tool remains unchanged, and the cutting amount remains unchanged. Also known as the work stroke, it is the work step completed by the processing tool on the processing surface once.
To develop a machining process, it is necessary to determine how many processes the workpiece will go through and the order in which the processes are carried out. Only a brief process with the name of the main process and its processing sequence is listed, which is called the process route.
The formulation of the process route is to formulate the overall layout of the process. The main task is to select the processing methods of each surface, determine the processing sequence of each surface, and the number of processes in the entire process. The formulation of the process route must follow certain principles.
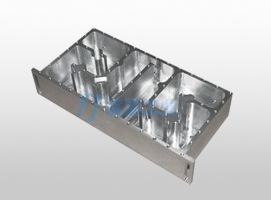