1. 가공 공정의 공구 경로 계획 최적화: 고효율 절삭 전략: CNC 알루미늄 합금 부품은 고속 할례(HSM) 또는 나선형 밀링과 같은 고급 공구 경로 전략을 사용하여 가공됩니다. 고속 할례는 높은 절삭 속도를 유지하면서 공구 경로를 더 부드럽게 만들어 갑작스러운 절삭력의 변화를 줄여 가공 효율을 높이고 공구 수명을 연장할 수 있습니다. 나선형 밀링은 공구를 축 방향과 방사상 방향으로 동시에 절단할 수 있습니다. 알루미늄 합금의 비교적 부드러운 소재의 경우 절삭 깊이와 폭을 크게 달성하고 가공 층의 수를 줄이며 가공 시간을 효과적으로 단축할 수 있습니다. 예를 들어 알루미늄 합금 복합 곡선 부품을 가공할 때 000 @ 000 빈 스트로크 감소 : CNC 알루미늄 합금 부품 가공은 공구 경로를 합리적으로 계획하여 공구의 빈 스트로크 시간을 줄입니다. 프로그래밍 시 불필요한 빠른 움직임과 잦은 공구 변경을 방지하기 위해 가공 영역에서 공구를 연속적으로 절단하십시오. 예를 들어 동일한 알루미늄 합금 부품을 여러 개 가공 할 때 가공 순서를 최적화하여 한 부품의 가공을 완료한 후 가장 짧은 경로에서 다음 부품의 가공 시작 위치로 공구가 이동할 수 있도록 하여 비가공 시간을 많이 절약합니다. 절삭 파라미터 최적화 : 절삭 속도 및 공급 개선 : 알루미늄 합금의 경도가 상대적으로 낮고 절삭 성능이 우수하여 절삭 속도와 피드를 적절하게 개선할 일반적으로 절삭 속도는 1000 - 3000m/min에 이를 수 있으며 피드는 0.1 - 0.5mm/z에 이를 수 있습니다. 예를 들어 알루미늄 합금 항공 부품을 가공할 때 절삭 속도를 기존 800m/min에서 2000m/min으로 높이고 공급량을 합리적으로 조절하는 동시에 가공 효율을 50% 이상 높일 수 있습니다. 적절한 절삭 깊이 선택 : CNC 알루미늄 합금 부품의 가공 정확도와 표면 품질을 보장한다는 전제 하에 절삭 깊이를 적절하게 높일 수 있습니다. 거칠기의 경우 큰 절삭 깊이를 사용하여 허용량을 신속하게 제거할 수 있습니다. 마감의 경우 부품의 정확도 및 표면 거칠기 요구 사항에 따라 적절한 절삭 깊이를 결정할 수 있습니다. 예를 들어 알루미늄 합금 금형을 거칠게 할 때 절삭 깊이를 3~5mm로 설정할 수 있으며, 마감 시 절삭 깊이를 0.1~0.3mm로 제어할 수 있습니다. 2. 첨단 가공 장비 및 기술 채택 고속 가공 센터: 고속 및 고속 공급 시스템: 높은 스핀들 속도와 높은 공급 속도를 가진 CNC 가공 센터를 사용하십시오. 고속 스핀들은 더 높은 절삭 속도를 달성하고 재료 제거 속도를 향상시킬 수 있습니다. 고속 공급 속도는 단위 시간에 더 많은 표면을 처리하고 가공 주기를 단축할 수 있습니다. 예를 들어 일부 고급 CNC 가공 센터 스핀들 속도는 40000r/min 이상, 공급 속도는 60m/min 이상, 알루미늄 합금 부품 가공 시 고정밀 및 고강성 구조: 고속 가공 센터의 고정밀 및 고강성 구조는 가공의 정확성과 안정성을 보장할 수 있습니다. 고정밀 좌표 축 위치 지정 시스템은 마이크론 수준의 가공 정확도를 달성하여 정확도 오류로 인한 반복적인 가공 또는 보정 시간을 줄일 수 있습니다. 고강성 침대와 테이블은 큰 절삭력을 견딜 수 있으며 고속 절삭 시 진동을 발생시키지 않아 가공 품질과 효율성을 보장합니다. 예를 들어 고정밀 알루미늄 합금 전자 부품을 가공할 때 가공 센터의 고정밀 위치 지정 시스템은 효율적인 가공 속도를 보장하면서 0.01mm 이내의 부품의 치수 정확도를 제어할 수 있습니다. 다축 연결 가공 기술: 가공의 자유도를 높입니다. 다축 연결(4축 및 5축 연결 등) 가공 기술을 사용하면 클램핑 횟수를 줄이고 한 번의 클램핑으로 여러 면의 가공을 완료할 수 있습니다. 여러 베벨과 곡면이 있는 항공기 엔진 블레이드 또는 자동차 부품과 같은 복잡한 알루미늄 합금 부품의 경우 다축 연결 가공은 더 복잡한 공구 경로를 달성하여 여러 클램핑으로 인한 위치 오류와 반복적인 가공 시간을 피할 수 있습니다. 예를 들어 5축 연결에서 알루미늄 합금 임펠러를 가공할 때 블레이드의 프로필, 허브, 블레이드 루트 등 여러 부품의 가공을 한 번의 클램핑으로 완료할 수 있으며 가공 효율은 기존 3축 가공의 2 공구 자세 및 절삭각 최적화 : 다축 연결 가공은 또한 부품의 모양 및 가공 요구 사항에 따라 공구 자세 및 절삭각을 실시간으로 조정하여 공구가 항상 최상의 절삭 상태에 있도록 할 수 있습니다. 이를 통해 공구의 절삭 효율을 개선하고 공구 마모를 줄일 수 있습니다. 예를 들어 알루미늄 합금 자유형 표면을 가공할 때 5축 연결을 통해 공구의 축 방향을 제어하여 곡면의 정상적인 방향과 일치하도록 함으로써 보다 균일한 절삭력 분포를 달성할 수 있으며 가공 품질과 효율성을 향상시킬 수 있습니다. 3. 공구 재료 및 기하학의 합리적인 선택 및 관리 : 적절한 공구 재료 선택 : 알루미늄 합금의 가공 카바이드 공구는 높은 경도, 높은 강도 및 우수한 내마모성을 가지고 있으며 일반적으로 알루미늄 합금 가공에 사용되는 공구 재료입니다. 고속 가공의 경우 코팅된 카바이드 공구는 공구의 절삭 성능을 더욱 향상시킬 수 있습니다. 예를 들어 TiAlN 코팅이 적용된 카바이드 밀링 커터는 알루미늄 합금을 가공할 때 공구 수명을 30%~50% 늘리는 동시에 더 높은 절삭 속도를 견딜 수 있습니다. 공구 기하학 최적화: 알루미늄 합금 부품의 가공 요구 사항에 따라 적절한 공구 기하학을 선택하십시오. 거칠기의 경우 나선 각도가 크고 전면 각도가 큰 공구를 선택하면 최첨단의 선명도를 높이고 절삭력을 줄이며 재료 제거 속도를 향상시킬 수 예를 들어, 알루미늄 합금 블록 부품을 거칠게 가공할 때 나선 각도가 40-45인 밀링 커터를 사용하면 허용량을 효과적으로 제거할 수 있습니다. 곡면을 마감할 때 0.01-0 0.02mm의 가장자리 반경을 가진 볼 밀링 커터를 사용하면 부품의 표면 거칠기가 Ra0.8 - Ra0.4m에 이를 수 있습니다. 도구 관리 시스템: 도구 수명 관리: 도구 절단 시간, 절단 거리 또는 가공 부품 수와 같은 매개 변수의 모니터링을 통해 도구 수명 관리 시스템을 구축하여 도구를 제때 교체할 수 있습니다. 이를 통해 과도한 공구 마모로 인한 처리 품질 및 처리 효율성 저하를 방지할 수 있습니다. 예를 들어, 가공 공정 중에 공구 공구 사전 조정 및 빠른 공구 변경: 공구 사전 조정 장치는 공구 길이, 반지름 및 기타 파라미터가 정확한지 확인하기 위해 공구가 공작기계에 설치되기 전에 사전 조정을 하는 데 사용됩니다. 동시에 공작기계의 공구 변경 시스템은 빠른 공구 변경을 실현하도록 최적화됩니다. 빠른 공구 변경 시스템은 몇 초 안에 공구 변경을 완료하여 가공 프로세스 중 다운타임을 줄일 수 있습니다. 예를 들어 일부 고급 CNC 가공 센터에서는 자동 공구 변경 장치를 사용하며 공구 변경 시간을 3-5초 이내에 제어할 수 있어 가공의 연속성과 효율성이 향상됩니다. 4. 생산 공정의 구성 및 관리 대량 생산 최적화: 그룹 기술 적용 : 알루미늄 합금 부품 부품의 모양, 크기, 가공 기술 및 기타 특성에 따라 그룹화한 다음 유사한 가공 기술과 고정장치를 사용하여 가공합니다. 이를 통해 공구 고정장치의 설계 및 제조 시간을 단축하고 생산 효율성을 향상시킬 수 있습니다. 예를 들어, 알루미늄 합금 자동차 부품을 다른 모델로 나누고 모양과 가공 기술이 비슷하지만 그룹으로 나누고 일반적인 고정장치와 공구 경로 템플릿을 사용하여 처리하면 많은 프로그래밍 및 디버깅 시간을 절약할 수 있습니다. 병렬 가공 배치 : 여러 가공 단계가 있는 알루미늄 합금 부품의 경우 병렬 가공이 이루어집니다. 가공 장비와 인력의 합리적인 할당을 통해 여러 공정을 동시에 수행할 수 있습니다. 예를 들어 알루미늄 합금의 복잡한 부분을 가공할 때 품질관리 및 효율성 균형 : 온라인 검출 및 피드백 : 가공 공정에서 레이저 측정, 접촉 프로브 검출 등 온라인 검출 기술을 사용하여 부품의 가공 크기와 형상 정확도를 실시간으로 모니터링합니다. 가공 오류가 발견되면 공작기계 제어 시스템으로 다시 공급되어 제때 조정됩니다. 이를 통해 가공 품질 문제로 인한 재작업 및 스크랩을 줄이고 생산 효율성을 향상시킬 수 있습니다. 예를 들어 알루미늄 합금 항공 부품을 가공할 때 온라인 검사 시스템을 통해 정기적으로 핵심 치수를 감지합니다. 치수 편차가 공차 범위를 초과하면 공작기계가 자동으로 공구 보상량을 조정하여 부품의 가공 정확도와 생산 효율을 보장합니다. 품질 관리 프로세스 최적화 : 부품의 품질 보장을 전 지나치게 번거로운 검사 링크를 피하고 통계 공정 제어(SPC) 및 기타 방법을 사용하여 주요 품질 특성에 초점을 맞춰 부품의 품질에 대한 통계 분석을 수행합니다. 예를 들어 알루미늄 합금 일반 기계 부품의 경우 불필요한 풀사이즈 검사를 줄이고 샘플링 검사 및 SPC 제어를 통해 비정상적인 품질 추세를 제때 감지하여 생산 효율을 높이는 동시에 품질을 보장합니다.
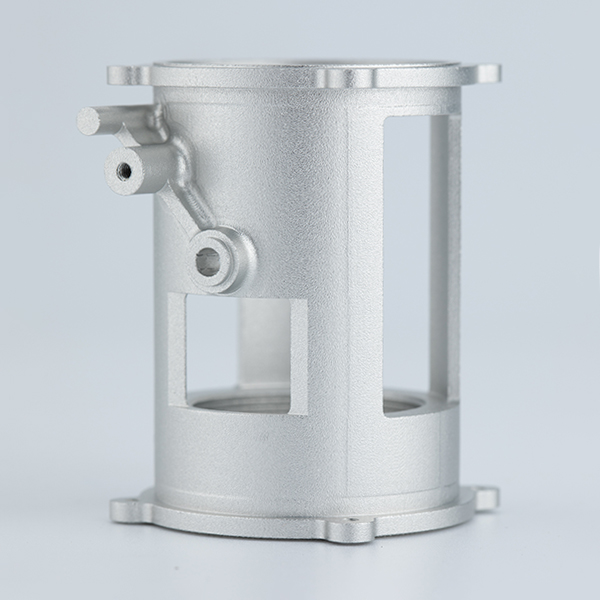