섀시 가공 과정에서 쉘의 개구부와 간격을 줄이는 것은 섀시의 전반적인 성능과 미학을 개선하는 중요한 단계입니다. 다음은 몇 가지 구체적인 조치와 제안입니다. 개구부 요건을 최소화하기 위한 설계 단계의 최적화: 설계 단계에서 각 개구부의 필요성을 신중하게 평가하고 내부 레이아웃 최적화를 통해 불필요한 개구부를 최대한 줄여야 합니다. 예를 들어, 합리적인 케이블 라우팅 설계를 통해 외부 인터페이스의 필요성을 줄일 수 있습니다. 개구부 크기 및 위치 최적화: 필요한 개구부의 경우 크기와 위치를 정확하게 계산하고 최적화하여 섀시의 차폐 성능에 미치는 영향을 최소화하면서 기능 요구 사항을 충족해야 합니다. 개구부의 크기는 전자파 누출을 방지하기 위해 zui에서 가장 높은 간섭 주파수에 해당하는 파장의 1/20 미만이어야 합니다. 통합 설계 채택: 섀시 가공은 통합도가 높은 부품과 모듈을 최대한 사용하여 별도로 설치 및 배선해야 하는 부품의 수를 줄임으로써 개구부와 간격을 줄입니다. 둘째, 가공 및 제조 공정의 제어 고정밀 가공: 섀시 쉘의 가공 정확도와 표면 품질을 보장하기 위해 고정밀 가공 장비 및 기술을 채택합니다. 고정밀 가공은 가공 오류로 인한 갭 및 불일치 문제를 줄일 수 있습니다. 합리적인 심 설계: 섀시 가공은 접기, EMI 파편 또는 EMI 터치 포인트 구성, 조임 등과 같은 합리적인 설계를 채택하여 동시에 솔기의 부드러움과 청결을 보장하고 불균일하거나 불순물로 인한 틈을 피하십시오. 전자기 밀봉 개스킷 사용: 솔기와 개구부에 전자기 밀봉 개스킷을 설치하여 틈새를 메우고 전도성 불연속 지점을 제거합니다. 전자기 밀봉 개스킷은 전도성 표면이 있는 탄성 물질로 섀시의 차폐 성능을 크게 향상시킬 수 있습니다. III. 후처리 및 테스트 엄격한 품질 검사 : 섀시 처리 후 개구부 및 틈새의 밀봉, 전체 구조물의 안정성 등 섀시 쉘에 대한 종합적인 품질 검사를 실시합니다. 품질 검사를 통해 기존 문제를 제때 찾아 수리할 수 있습니다. 합리적인 설치 및 디버깅 : 섀시 설치 및 디버깅 중에 불필요한 쉘 손상을 동시에 모든 구성 요소와 모듈이 설계 요구 사항에 따라 올바르게 설치되고 연결되었는지 확인하십시오. IV. 적합한 재료를 선택하기 위한 기타 제안: 섀시 쉘은 알루미늄-마그네슘 합금 등과 같이 차폐 특성과 기계적 강도가 우수한 재료로 제작되어야 합니다. 이러한 재료는 전자기파의 누출을 효과적으로 차단할 수 있을 뿐만 아니라 특정 충격과 진동을 견딜 수 있습니다. 인력 교육 강화: 섀시 가공, 제조 및 설치 및 시운전 인력에 대한 전문 교육을 실시하여 전문 기술과 품질 인식을 개선합니다. 교육을 통해 프로세스 요구 사항에 따라 엄격하게 작동하고 인적 요인으로 인한 품질 문제를 줄일 수 있습니다.
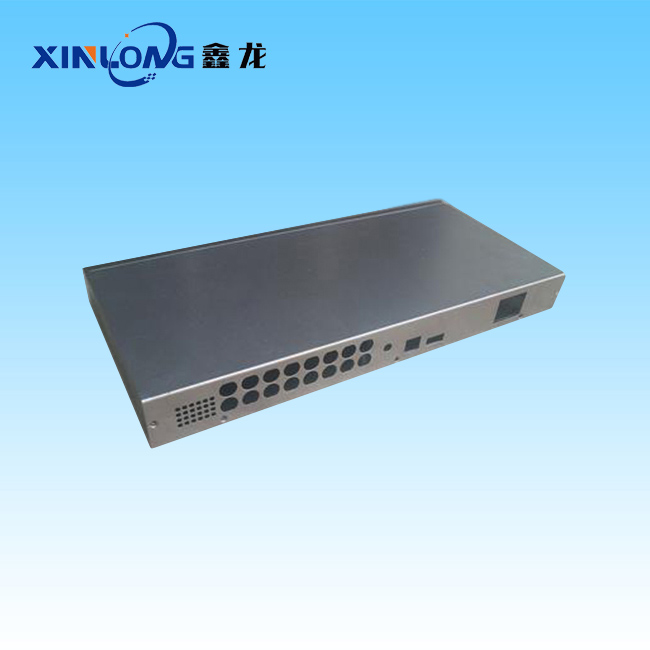