The business process and current situation of the sheet metal industry
According to a definition in a foreign professional journal, sheet metal can be defined as a comprehensive cold working process for metal sheets (usually below 6mm), including cutting, punching/cutting/composite, folding, welding, riveting, splicing, forming (such as automotive body), etc. Pronuntior eius est, quod densitudo eiusdem partem consistentia est. Generally speaking, the basic equipment of a sheet metal factory includes a shear machine, CNC punching machine/laser, plasma, waterjet cutting machine/composite machine, bending machine, and various auxiliary equipment such as an uncoiler, leveling machine, deburring machine, spot welding machine, etc.
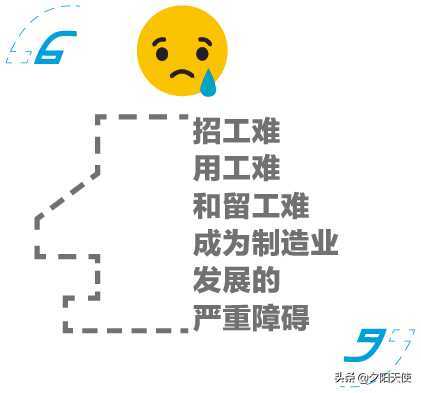
Procedus fabricae metallorum folia: Operatio departamentorum in fabrica metallorum folia non multo diferenta est ab ea generis fabricatorum. Hic, tantum fabricationem produktorum in laboratorio introducamus. Usually, the three most important steps in a sheet metal factory are cutting, punching/cutting, and folding.
1. Prima gradus est procedus fractae materiae (etiam cognoscatus est fracta materiae). Usually, on-site workers will use a shearing machine to cut the appropriate size of parts materials from large plates based on the unfolding diagram provided by the PIE department. Si pulssa pulssa est, terra clampionis considerabitur. Post succidendum, operarii numerum partem in superficie singulorum partem materiae per calamum signum notabuntur.
Note: Some factories don't have this processing step and directly layout on standard sheets, followed by direct stamping/cutting processing.
2. Then the material will be sent to the CNC punching/cutting machine for punching/cutting processes. In hoc processo opus est codificationes NC (Numerical Control) procedentibus. Nowadays, most machine tool manufacturers provide automatic programming software (domestic manufacturers almost always cooperate with foreign software companies for OEM sales, so they do not have their own software development team), which greatly facilitates programming engineers. The factors that stamping/cutting programming engineers need to consider are sheet utilization, cutting tools, efficiency, accuracy, and other issues. Post conpletionem pulsavi/secessi, partes de microconnexiis auferuntur et tunc ad pulsavi machinam mittitur.
3. In processo bending, principes considerationes sunt seleccio instrumentorum, ordine bending, compensatione bending, interference bending, etc. Usually, bending programming software is also sold randomly, but most CNC bending machines in China are still manually programmed, often relying too much on the experience of teachers. On the other hand, the manufacturing process requirements in China still have a certain distance compared to foreign countries, so efficiency has not been improved, and the performance of CNC bending machines has not been maximized.
Finally, depending on the product situation, welding, polishing, painting, assembly, packaging and other processes may be carried out, which will not be described here.
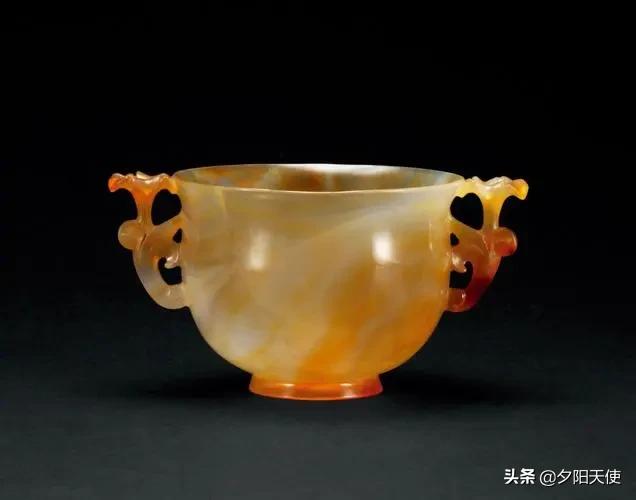
The current situation of the sheet metal industry!
1. Praecepta productionis maxima est. China is gradually becoming an international manufacturing center, and with the continuous increase of foreign investment, the demand for metal processing capabilities is constantly increasing. In the metal processing industry, electrical control boxes, machine casings, and other components are generally sheet metal parts, so the demand for Sheet Metal Processing capabilities is also constantly increasing.
2. As far as sheet metal processing is concerned, precision within a few threads is quite common, and the complexity of the process is also relatively high, with some parts even reaching dozens of processes. So sheet metal processing enterprises usually need various types of mechanical equipment to meet different process requirements. The precision of sheet metal punching is generally within 177; About 0.1mm, the bending accuracy can generally reach 177; 0.5mm.
3. Magnum profitum: pulchritudo generale circa 30% attingere potest, cum laser cuto 50% aut plus attingere potest.
4. Multae caracteribus principibus industriae metallorum domus in summario sunt: equipatio non est tantum efficabile quam terras disveloppae, accuracio non est tantum accuracta quam alii, et maxime importantia est, quia scientiae artificili R&D et technicis producentium adhuc in principio stagni sunt. Technologia bona est in mentis doctorum, et mechanismus curriciosis adhuc in simplo stagno operation is machinarum. Nullum est standard industriae professionalis et sustinentiae, it a difficile est satisficere necessitates internacionis superfinis, resultante in situatio in qua non possumus facere ordines.
1. Department Manager: Lead the technical team or project team to complete the product development and development on time, with the quality and quantity, as well as the production, release, and change of the process technology. Arrange, inspect, and adjust the project progress to meet production and customer needs, ensuring that the requirements of the process documents can maximize the company's interests (including production cost control, an optimization, and the production, and the development of the technical team, in anianim plana, in anim plana, anim plana, anim plana, anim plana, anim plana, anim plana, anim plana, anim plana, anim plana, anim plana, anim plana, anim plana, anim plana, anim plana, anim plana, anim plana, anim plana Quid?
2. Process technology engineer: responsible for the production and release of BOM material lists, alternative materials, process documents/technical specifications, and engineering changes; Technical support in the production site; Communicate process and technical issues with customers; Optimizatio productionis procedentium;
3. Pricing Engineer: Establish a standard cost accounting system and update it in a timely manner based on material and market changes. Provide accurate and effective cost prices in a timely manner when bidding for new orders or sample orders
Decisiones de "ordine review team" facite et confidentiam pretiosae esse responsabilitatem ut custodiant interesa firmae;
4. Mold Engineer: Review and confirm the rationality of the mold plan, track the progress of the mold, create standardized operation manuals for use, provide on-site guidance for production, and maintain the mold database;
5. CNC programmer: responsible for programming CNC programs, ensuring maximum material utilization through programming, correctly selecting materials, maintaining the database of numerical punching molds, and timely completing 1002 production arrangements.
6. Draftsman: responsible for developing customer drawings, compiling process documents, and developing towards the direction of engineers;
7. Clerk: Responsible for the release management of technical documents, product coding management, document transmission between departments, data statistics, and daily administrative work of the department.
3,IE Business Process
1. New product development (sample development):
Our company is an OEM/ODM processing type. When the sales department discusses new products with customers, they usually provide technical documents. The PIE (Process Integration Department) department arranges a project team to analyze product processes, BOMs, and other issues based on technical documents/samples. At the same time, standard costs are calculated and submitted to the MRB (Order Review Team).
After MRB decides to take on the order, the technical team begins to produce and convert customer technical documents, purchase trial materials, arrange sample development and trial production, and the process engineer follow s up on the entire process from the production of the process technical documents to on-site technical guidance for sample development and trial production. The project leader must participate in and follow up on the project progress, and feedback problems and progress to the PIE manager at any time. When there are a process or equipment problems, timely communication and improvement should be made with the customer's technical department, and the sales department should be informed at the same time.Exactly!
After passing the initial inspection of the trial production, before small-scale production, the process engineer must complete the production of all required process technical documents (BOM/process technical requirements/substitute material list/standard working hours/standard cost/standard process route/ERP data...) and release them to the controlled DCC.
During the first batch of mass production, process engineers supervise and guide frontline production personnel and supervisors on site to operate correctly. If there are deviations in the "operation process" and "standard working hours", technical documents must be corrected in a timely manner. If batch materials are found to be defective during mass production, solutions should be negotiated with the supplier. If it involves replacing materials to meet customer requirements, customer confirmation must be obtained in advance. Special material technical requirements documents should be developed for these special materials to avoid duplicate problems in future procurement and affect OTD.
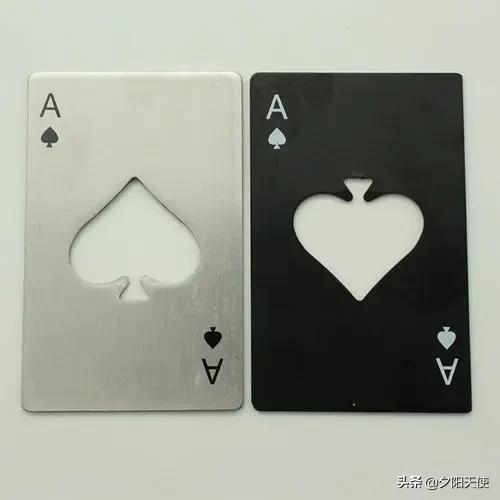
After the first batch of mass production, the standard cost and standard working hours have been basically determined. These materials are provided to the finance department for cost accounting and ǁas a planning and scheduling tool, completing the process from sample opening to mass production. It is emphasized here that the responsible engineer must participate in the entire process, ensuring that frontline personnel can produce efficiently and accurately, and controlling the quality defects of the product process before the second batch of mass production.
2. Produkti iam in mass production:
Due to the fact that the process and technical documents have already been prepared in small batches in the early stage, there is basically not much to do. However, it is important to note the confirmation and release of ECO/ECN design changes, supervise relevant departments to ensure the production of qualified products, and work with production engineers to optimize production processes and design fixtures to improve production efficiency and reduce production costs.
4,PIE Information Management:
1. Security and confidentiality of technical documents:
Departatio MIS utilizat modos technicos ut prohibere COPY illegal, prohibere disclosionem informationum technicam per uploasionem/downloadem online, e-postam, et prohibere hackers de invasione illegally et furare informationes technicam per gestionem securitatis retis; Fix accessum et modificationem permissionibus ad documentos tecnicos, et pone passordes ad introitum retis;
2. Copyright of design and drawing software:
In increasing emphasis on global software copyright/intellectual property, the company uses all genuine design software;
3. Data backup:
Data sempiternorum reservationis a remo conservata; Data reservationis cotidie in securitate custodietur; Develop emergency response plans for data disasters.
5,The role of PIE in Sakaki Province
The importance of PIE in enterprise s is unquestionable. All production and manufacturing, planning, ERP systems, procurement, outsourcing, inventory, and quality work must be based on PIE's technical documents. Therefore, the accuracy and seriousness of PIE's documents are not just a joke. Once a business trip is wrong, causing batch defects or scrapping of products, the losses to the enterprise are difficult to estimate. If this affects customers
The delivery time of customers OTD has led to a decrease in customer satisfaction, and the increase or decrease in subsequent orders has caused great trouble for GM and the sales department.
Only by forming good work habits from a fundamental sense of work responsibility and attitude, and persistently improving the technical document system, can enterprises move towards success!