The editor will organize a lot of practical knowledge methods and hot news for everyone. Everyone should pay more attention and better content will be presented to you.
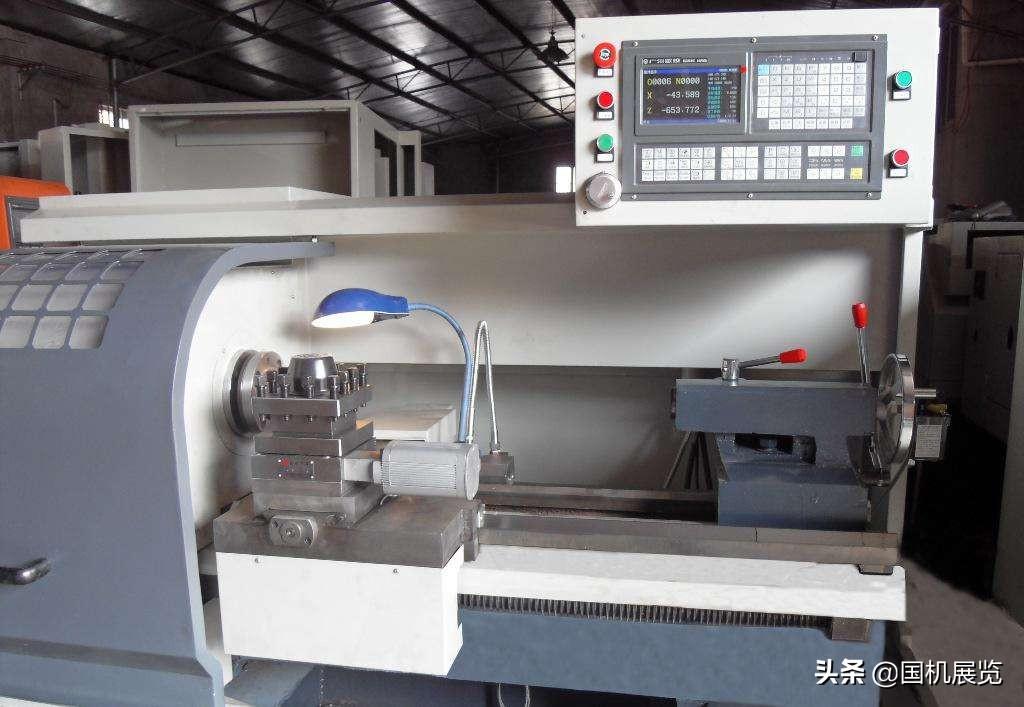
On a CNC lathe, four standard threads can be turned: metric, inch, modulus, and radial control. Regardless of which type of thread is turned, the lathe spindle and tool must maintain a strict motion relationship: that is, for every revolution of the spindle (i.e., every revolution of the workpiece), the tool should move a uniform lead distance of the workpiece. Inter analisi linearum ordinarum, volumus intellegere nostrum linearum ordinarum ut melius procederemus illos.
1 , Dimensional analysis of ordinary threads
The CNC lathe requires a series of dimensions for processing ordinary threads, and the calculation and analysis of the dimensions required for processing ordinary threads mainly include the following two aspects:
1. Diameter of workpiece before thread machining
Considering the expansion of the thread profile during thread processing, the diameter of the workpiece before thread processing is d/d-0.1p, which means the major diameter of the thread is reduced by 0.1 pitch. Generally, based on the small deformation capacity of the material, it is taken as 0.1 to 0.5 smaller than the major diameter of the thread.
2. Thread machining feed amount
Quantitate fertilium fertilium est diameter subter fertilis, quod est novissima positio fertilis fertilis cutoris fertilis.
Minimus diameter virgae est: diameter magnus -2 times altitudo dentis; Altitudo tres=0.54p (p est pitch)
The feed amount for thread machining should be continuously reduced, and the specific feed amount should be selected based on the tool and working material.
2,Installation and alignment of ordinary thread cutting tools
Si installatio instrumenti conversationis nimis alta aut nimis est, quando instrumentum sectationis profunditatem pervenit, superficie retrorsum sectationis instrumenti conversationis contra laborem, crescere frictionem et etiam crescere laborem, causa phenomenum interficionis instrumenti; Si nihil est, cipes non facile discargentur, et fortitudo radicalis instrumenti conversionis ad centrum opus est. In addition, the gap between the horizontal screw and the nut is too large, causing the cutting depth to automatically depth, thereby lifting the workpiece and causing cutting. At this point, the height of the turning tool should be adjusted in a timely manner to ensure that its tip is at the same height as the axis of the workpiece (using the tip of the caulstock to align the tool). During rough and semi precision turning, the tool tip position is about 1% higher than the center of the workpiece (d represents the diameter of the workpiece being processed).
Laboratorium firme clamabitur non potest, et robustum opus ipsius non potest resistere fortem cutationis durante conversationis, resultat in excessive deflectione et cambiare altitudinem centri inter instrumentum conversationis et opus (opus elevatur), ut subito cresceret profunditatem et instrumentum gnantiam. In hoc tempore, opus clamabitur firme, et tipes caulstacki utili potest ut cresceret rigiditatem opus.
The tool alignment methods for ordinary threads include trial cutting method and automatic tool alignment instrument. The tool can be directly used for trial cutting, or the workpiece zero point can be set with G50, and the workpiece zero point can be set with workpiece movement for tool alignment. Praecepta ad alignationem instrumentorum in machinationibus fertilibus non sunt altissima, sublime non sunt limitationes strictae ad alignationem instrumentorum in z-direction, quae iuxta praecepta programationis.
3,Programming and machining of ordinary threads
In current CNC lathes, there are generally three processing methods for thread cutting: g32 straight cutting method, g92 straight cutting method, and g76 oblique cutting method. Due different cutting methods and programming methods, machining errors also vary. Operium et utilium diligenter analizare debemus, et partibus altis precisiis procedere debemus.
1. Metodo recto secendi G32 propter simultanem operationem utraque angulorum secendi est fortitudo excelsa et difficile est secere. Pro hoc, dum secendi, utraque angulorum secendi proni sunt indure. Cum mittat tres in maxima hydribus propter maximum profunditatem secessionis, calamo celerior est, resultit errores in diametro triturae. However, its processed tooth shape accuracia is relatively high, so it generally used for small pitch thread processing. Pro factum quod movementum instrumentorum et cutationem omnes per programmationem completa sunt, programma machinationis est relative longa; Pro facile gesto finis, mensura frequentia necessa est in processione.
2. The G92 straight cutting method simplifies programming and improves efficiency compared to the G32 instruction.
3. G76 oblique cutting method, a causa universae radici machinae, is prona to damage and wear of the cutting edge, resulting in an uneven threaded surface and changes in the tool tip angle, resulting in poor dent shape accuracy. However, due to its single edge operation, the tool load is small, the removal of chip is easy, and the cutting depth is decreasing. Hoc ergo methodo machinationis generale utilis est ad machinationem magnis tonnas. Pro facile removione chipa et bonis conditionibus cutationis, hoc methodo machinationis convenientior est quando praecepta sunt precisa thread non alta. When processing high-precision threads, two tools machining can be used, which involves rough turning using the G76 machining method first and then precision turning using the G32 machining method. But it is important to ensure that the starting point of the tool is accurate, otherwise it is easy to buckle randomly and cause parts to be scrapped.
4. After the thread processing is completed, the quality of the thread can be judged and measures can be taken in a timely manner by observing the thread profile. When the top of the thread is not pointed, increasing the cutting amount of the tool will actually increase the major diameter of the thread, which depends on the plasticity of the material. When the top of the thread is pointed, increasing the cutting amount of the tool will proportionally reduce the major diameter. Based on this characteristic, the cutting amount of the thread should be treated correctly to prevent scrapping.
4,Testing of ordinary threads
For general threads, thread ring gauges or plug gauges are used for measurement. Quando mensura sunt ligna externe si ligna est In fini; Gaudium anuli conclusit, dum quota; End stop; Si gaudium anuli rotaturum non potest, indicat quoniam virga processata complicit requisiis, alioquin non qualificata est. Metientibus fertilibus interioris, gauge fertilibus utilis et eiusdem methodo metientibus utilis. In addition to measuring with a thread ring or plug gauge, other measuring tools can also be used for measurement. The thread diameter can be measured with a thread micrometer, and the thickness of tooth can be measured with a dent thickness vernier caliper for trapezoidal thread diameter and worm pitch diameter. The measuring needle can be used to measure the thread diameter using the three needle measurement method.
The 15th China International Machine Tool Exhibition (CIMES2020) will be held from May 18-22, 2020 at the new building of the China International Exhibition Center (Shunyi) in Beijing. We welcome you to come and guide us.