Selection of cutting tools and tools is one of the important contents in CNC Machining technology, which not only affects the machining efficiency of the machine tool, but also directly affects the machining quality. Compared with traditional machining methods, CNC machining has higher requirements for cutting tools and tools. Non solum altum precision, bonum rigiditatem, et durabilitatem opus est, sed etiam magnitudinem stabilem et instaurationem et adjustationem opus est.
CNC machining tool materials 1. High speed steel
Vellum velocem, etiam auriculum aut album. Est steel alloy qui continet elementos, sicut tungsten (W), molybdenum (Mo), chromium (Cr), vanadium (V), cobalt (Co), etc. In duas series major tungsten et molybdenum dividitur et materia tradicionala est. Temperatura temperatura cubiculi eius 62-65HRC est, et temperatura temperatura eius usque ad 500-600 °C crescere potest. Post extinguendum parva est deformatio facile aculare et fraudulentur et succidentur It can't only be used to manufacture drill bits and milling cutters, but also to manufacture complex cutting tools such as gear cutters and forming milling cutters. However, due to its low allowable cutting speed (50m/min), it is mostly used for low-speed machining on CNC machines. Ordinary high-speed steel is represented by W18Cr4V.
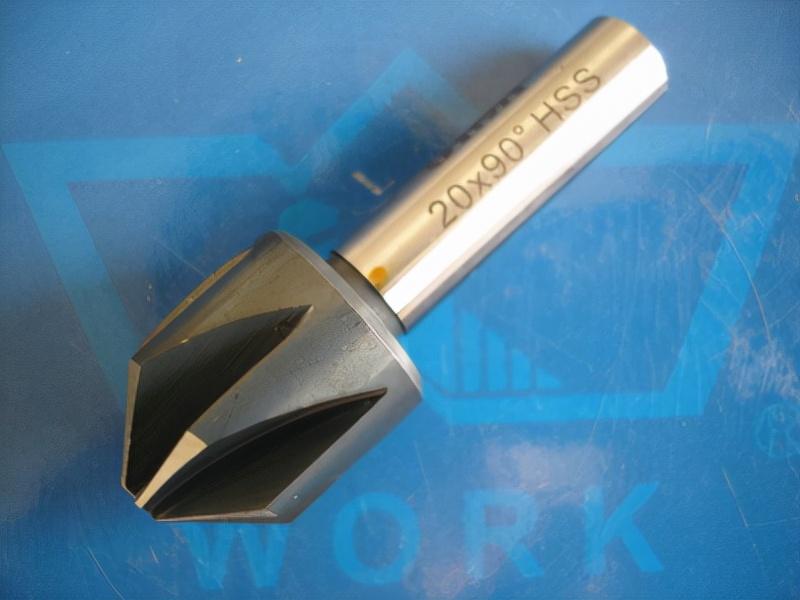
2. Difficile alloy
Hard alloy is a powder metallurgy product made from carbides (WC, TiC, TaC, NbC, etc.) with high hardness and melting point, using Co, Mo, Ni as binders. Oda sıcaklığı 74-82HRC ile yüksek sıcaklığı 800 °C ile 1000 °C ile dayanabilir. Pro minimo productione costa, excellent cutting performance in medium speed (150m/min) et high feed cutting, making it the most widely used tool material in CNC machining. But its impact hard and bending strength are much lower than those of high speed steel, so it is rarely made in integral cutting tools. In exercitu praecepta, blocos difficile secationis in corpore secationis parasti fixentur per conculcationem aut clampionem mecanicam. The commonly used hard alloys include tungsten cobalt (YG) alloys (YG8, YG6, YG3), tungsten titanium (YT) alloys (YT5, YT15, YT30), and tungsten titanium tantalum (niobium) (YW) (YW1, YW2) alloys.
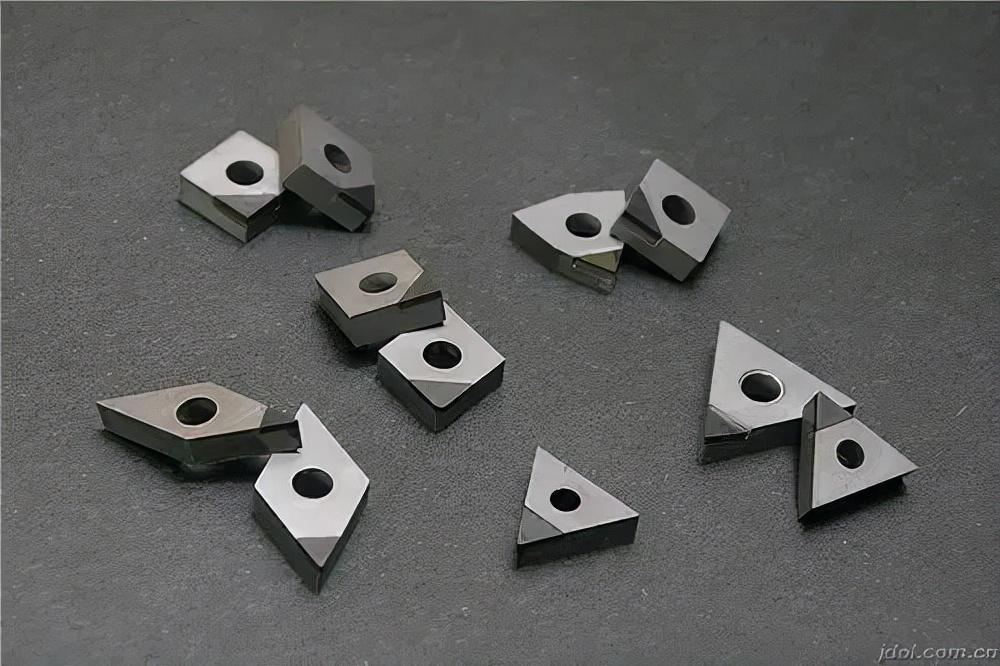
3. Gravitas difficile coated
Coated hard alloy tools are made by coating one or more layers of wear-resistant TiN, TiCN, TiAlN, and Al2O3 on hard alloy tools with good difficulty. The thickness of the coating is ranging from 2 µm to 18 µm. Coatings usually have two functions: a one hand, they have a much lower conductivity coefficient than the tool substrate and workpiece material, weakening the thermal effect of the tool substrate; On the other hand, it can effectively improve the friction and adhesion during the cutting process, reducing the generation of cutting heat. TiN habet humiles characteres frictionis, quae perditionem tissuei coationis reddere potest. TiCN potest reddere vestimentum superficie exterioris sectionis. TiCN vestimentum maiorem difficultatem habet. Al2O3 coating has excellent thermal insulation effect. Comparatus cum vasis difficilis secationis, vasa difficilis secationis, multo meliora sunt in fortitudine, difficile, et resistentia. For cutting works pieces with a hardness of 45-55HRC, low-cost coated hard alloys can achieve high-speed cutting. In recent years, some manufacturers have relied on improving the coating materials and proportions, which has greatly improved the properties of coated cutting tools.
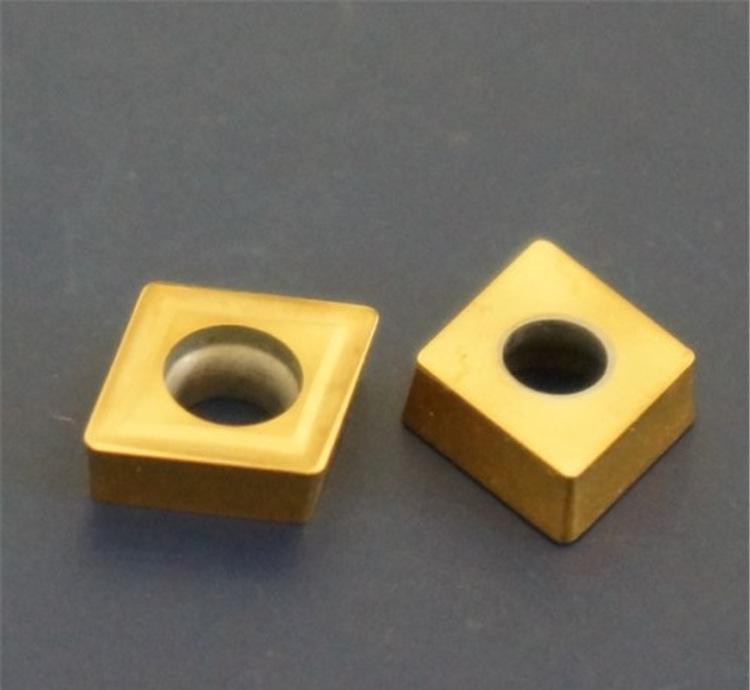
4. Ceramic materiales
Ceramica est unus de instrumentis cutationis quae velociter develoverat et in praeterito 20 annos amplius utilis est. In proximo futuro, ceramica ad tertiam revolutionem potest inducere machinas, secundum altum velocitatem steelam et difficilem.
Ceramic cutting tools have advantages such as high hardness (91-95HRA), high strength (bending strength of 750MPa~1000MPa), good wear resistance, good chemical stability, good adhesive resistance, low friction coefficient, and low cost. Non solum hoc, ceramic cutting tools also have high temperature hardness, reaching 80HRA at 1200 °C. Cum usus est ceramic a cuta instrumenta vitae multo longa habent, et velocitas cuta a 2-5 vicibus in comparatione ad instrumenta difficile cuta potest. They are particularly suitable for processing high hardness materials, precision machining, and high-speed machining. They can process various types of quenched steel and hardened cast iron with a hardness of up to 60HRC. Commonly used include alumina based ceramics, silicon nitride based ceramics, and metal ceramics. Alumina based ceramic cutting tools have higher thermal hardening than hard alloys. Under high speed cutting conditions, the cutting edge generally does not undergo plastic deformation, but its strength and difficulty are lower. In addition to high thermal hardness, silicon nitride based ceramics also have good difficulty. Compared with silicon oxide based ceramics, its disadvantage is that it is prone to high-temperature diffusion during steel processing, which intensifies tool wear. Silicon nitride based ceramic tools are mainly used for intermittent turning and milling of gray cast iron. Cermet metal is a tool material based on carbides, similar to hard alloys, but with lower affinity, good friction, and better wear resistance. It can withstand higher cutting temperatures than conventional hard alloys, but lacks the impact resistance, toughness during heavy machining, and strength at low speeds and high feed rates of hard alloys. In recent years, through extensive research, improvement, and adoption of new manufacturing processes, the bending strength and toughness of ceramic materials have been greatly improved. For example, the new metal ceramic NX2525 developed by Mitsubishi Metal Company in Japan and the CT series of metal ceramic blades and the coated metal ceramic blade series developed by Sandvik Company in Sweden have significantly higher bending strength and wear resistance than ordinary metal ceramics, greatly expanding the application range of ceramic materials.
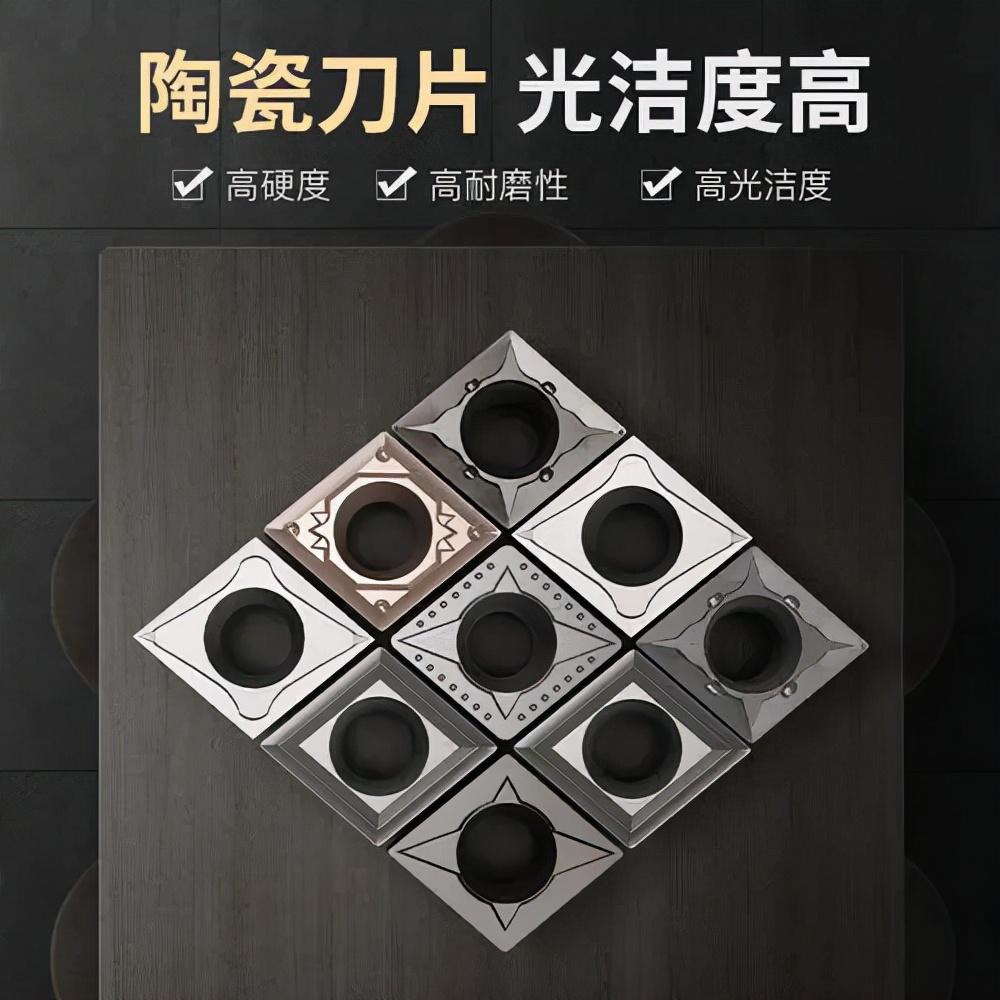
5. Nitridus cubiculus (CBN)
CBN is a artificially synthesized high hardness material, with a hardness of up to 7300-9000HV. Its hardness and wear resistance are second only to diamond, and it has excellent high-temperature hardness. Compared with ceramic cutting tools, its heat resistance and chemical stability are slightly worse, but its impact toughness and anti crushing performance are better.
Ferrum ferrum ferrum ferrum ferrum frigidum et temperatura altissimum sequitur amplius est. Comparatus cum instrumentis dissipationis difficilis, velocitas dissipationis in ordine magnitudinis crescere potest. PCBN (polycrystalline cubic boron nitride) cutting tools with high CBN content have high hardness, good wear resistance, high compressive strength, and good impact toughness. However, their disadvantages are poor thermal stability and low chemical inertness, making them suitable for cutting heat-resistant alloys, cast iron, and iron based sintered metals. In agro application of cutting gray cast iron and quenched steel, ceramic cutting tools and CBN cutting tools are available for simultaneous selection. When dry cutting hardened steel, the cost of using Al2O3 ceramics is lower than that of PCBN materials, because ceramic cutting tools have good thermal and chemical stability, but they are not as hard and hard as PCBN cutting tools. Ceramic a instrumenta sectionis optima sunt quando operibus cum difficile sub 60HRC et parva fertilibus procentibus secant. Instrumentos PCBN cutationis ad situationes in qua labor parietem maior est quam 60HRC, subito ad automatissimum et altum precision machinam.
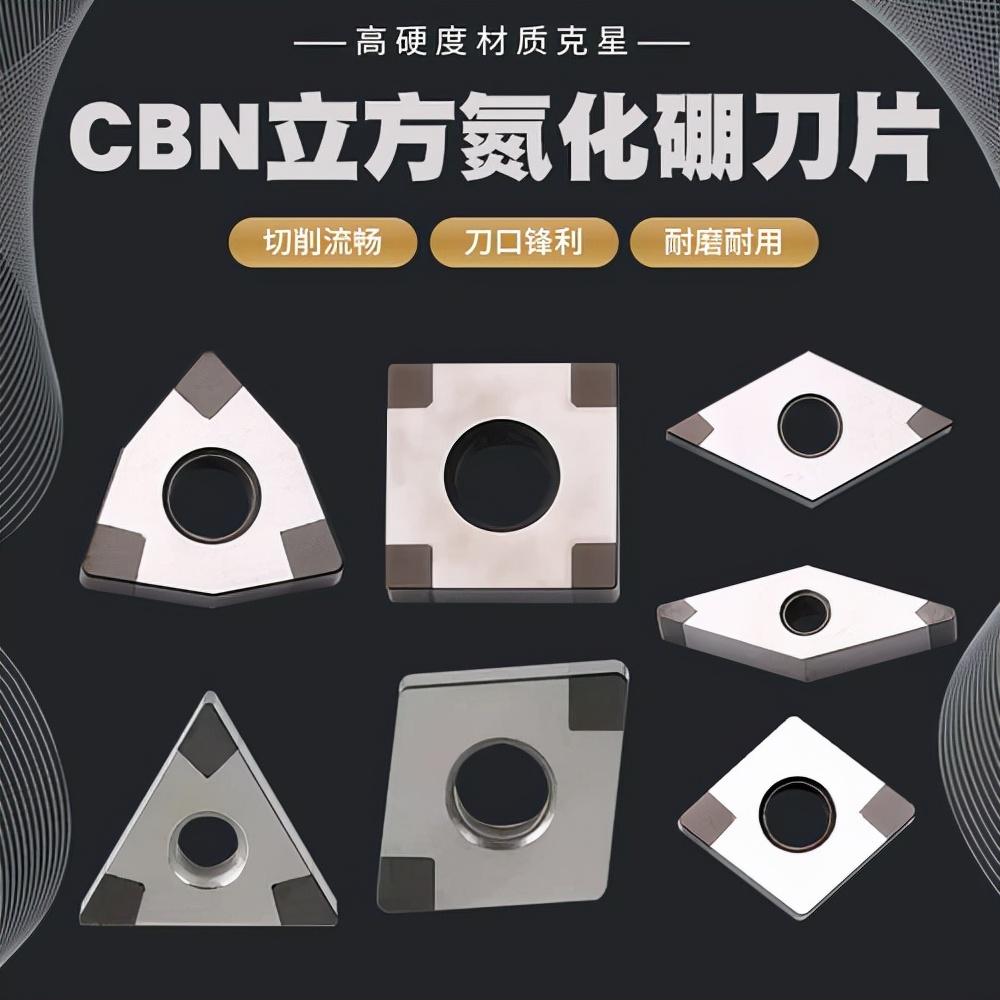
6. Polycrystalline Diamond (PCD)
As the hardest cutting tool material, the PCD has a hardness of up to 10000HV and the best wear resistance. It can process soft non-ferrous metal materials with a high speed (1000m/min) and a high speed (1000m/min) and precision. However, it is sensitive to impact, easy to break, and has a strong affinity for iron in ferrous metals, which can easily trigger chemical reactions. Generally, it can only be used to process non-ferrous parts, such as non-ferrous metals and their alloys, a non-ferrous metals and their alloys, a single fibers, engineering ceramics, and a hard alloys, which are extremely hard materials.Exactly!
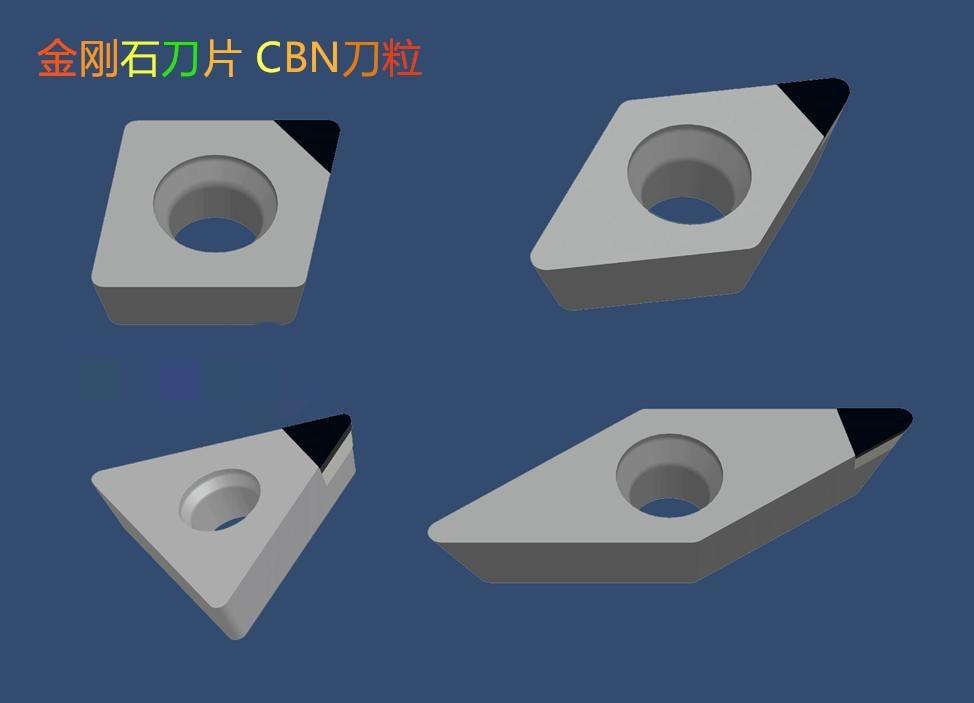